Are you a candy manufacturer looking to create fun shapes that will set your gummy products apart? The solution lies in custom gummy molds. These are the unsung heroes behind these delightful, perfectly shaped, chewy treats. With the global gummy market projected to reach a staggering $5.9 billion by 2026, the right gummy mold can make all the difference. This guide shares tips and recommendations for custom gummy molds. Let’s dive in for more.
What Are Gummy Molds?
Gummy molds are specialized trays or forms designed to hold the liquid gummy mixture as it sets and solidifies. They are available in various materials, sizes, and configurations to give the final gummy treat its distinct shape. You can use customized molds to create visually appealing treats, from classic gummy bears to intricate designs.
Custom gummy molds, in particular, offer a distinctive advantage for manufacturers seeking to stand out in this competitive market.
The unique gummy shapes can be used to establish and reflect a brand's identity. Candy workshops can also incorporate licensed characters or design seasonal treats to add a personalized touch that resonates with consumers.
What’s more, custom gummy molds optimize production processes and improve gummy quality through consistency. They are catalysts for innovation, enabling manufacturers to respond swiftly to gummy trends. Ultimately, custom molds can drive profitability through premium pricing and market expansion in the ever-evolving confectionery landscape.
.
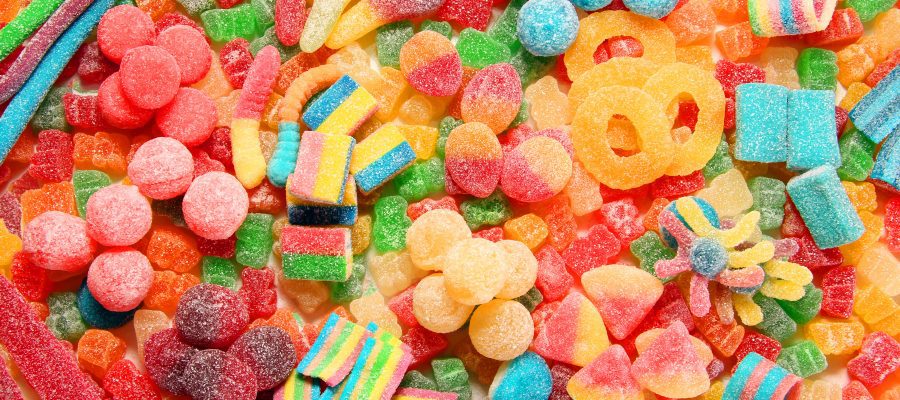
.
How Custom Gummy Molds Can Elevate Your Brand: Small vs. Large-Scale Gummy Production Use-Case Scenarios
Custom gummy molds play a vital role in optimizing gummy production, whether you're running a small startup or a large-scale industrial operation. Below are examples of how custom molds affect different scales of production:
1. Small-Scale Gummy Production
For small businesses or startups, flexibility and creativity are key. Custom gummy molds offer the ability to experiment with unique shapes and designs, allowing smaller producers to stand out in niche markets.
- Example: A local candy startup specializing in CBD-infused gummies may use silicone custom molds to create limited-edition seasonal shapes like pumpkins for Halloween or hearts for Valentine’s Day. These molds allow for quick and easy modifications to fit small-batch production runs, while the flexible silicone material ensures that gummies are easy to demold without any waste or damage.
.
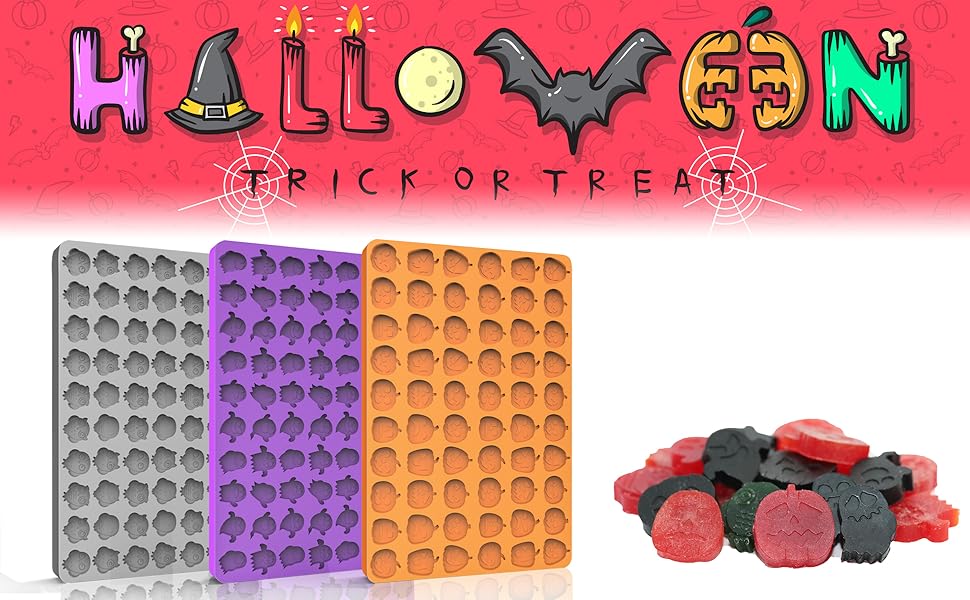
.
- Benefit: For small-scale operations, silicone molds are cost-effective, as they are reusable, easy to clean, and don’t require heavy machinery. They allow businesses to offer a wide variety of products without needing to invest in expensive equipment. This flexibility lets small producers quickly respond to customer trends or special requests.
.
2. Large-Scale Gummy Production
In large-scale, industrial gummy production, the focus shifts towards maximizing efficiency, consistency, and output. Custom gummy molds for large-scale manufacturers are designed to work seamlessly with automated equipment to ensure speed and quality.
- Example: A large nutraceutical company producing thousands of vitamin gummies daily relies on Teflon-coated aluminum molds integrated with fully automated gummy depositors and cooling systems. These molds ensure that the gummy cavities are filled quickly and consistently, while the Teflon coating allows for efficient, damage-free demolding. The high thermal conductivity of aluminum enables faster cooling, shortening production time.
.
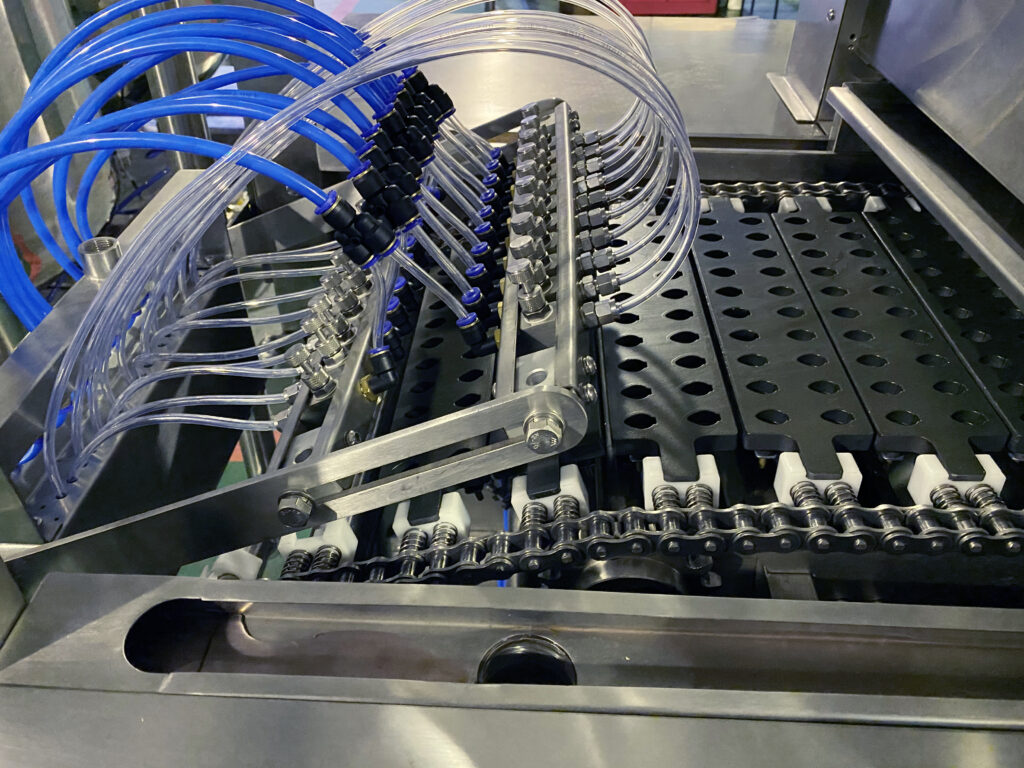
.
- Benefit: For large-scale manufacturers, custom Teflon-coated aluminum molds enhance production speed by minimizing downtime for cleaning and mold preparation. Their durability (up to 5,000 production cycles) ensures long-term cost savings, and their compatibility with automated lines significantly reduces labor costs and human error.
.
3. Mid-Sized Production
For mid-sized operations transitioning from small to large-scale production, polycarbonate molds offer an ideal middle ground between durability and flexibility. They provide detailed shaping capabilities for intricate designs, while their rigidity supports higher output without the risk of warping or cracking.
- Example: A growing gummy brand expanding its product line may use polycarbonate molds to create intricate 3D gummy shapes for specialized products, such as multi-vitamin gummies. The transparency of the molds allows operators to monitor the gummy setting process, ensuring precision for more complex shapes.
- Benefit: Polycarbonate molds are suited for mid-sized producers who need precision but aren’t fully automated yet. They allow for an efficient yet controlled process, helping companies scale their production without compromising on quality.
.
Additional Niche Use-Case Scenarios for Custom Gummy Molds
While custom gummy molds are a staple for businesses of all sizes, they also open doors to niche markets that can help differentiate your brand and target specific consumer needs. Below are examples of how specialized gummy molds can create new opportunities in the luxury, educational, and therapeutic sectors.
1. Luxury Gummy Production
For brands looking to enter the high-end confectionery market, custom gummy molds can elevate their products to a luxury level. These molds allow manufacturers to create intricate, bespoke shapes that align with premium branding and offer a sense of exclusivity.
- Example: A luxury candy brand may use custom gold-plated silicone molds to create gummies shaped like jewelry pieces, gemstones, or other high-end items. These gummies can be sold in boutique stores or used as personalized gifts for exclusive events such as weddings or corporate galas.
- Benefit: Luxury gummies can command premium pricing and attract a wealthy clientele willing to pay more for unique, aesthetically pleasing products. Custom molds in this market are an essential part of branding and product differentiation, allowing companies to produce visually stunning gummies that match their high-end image.
.
2. Educational Gummies for Children
In the educational market, custom gummy molds can be an exciting way to engage children and make learning more fun. These molds are commonly used in the creation of alphabet- or number-shaped gummies, helping brands cater to parents and educators who want to combine learning with snacking.
- Example: A brand specializing in educational snacks may use custom molds in the shapes of letters, numbers, or animals to create gummies that are both nutritious and interactive. These gummies can be used as teaching tools in classrooms or sold as fun, educational snacks for parents to use at home.
- Benefit: Educational gummies not only appeal to children but also to parents and teachers who prioritize both health and learning. Custom molds allow businesses to stand out in a niche market by combining entertainment, education, and nutrition into a single product.
.
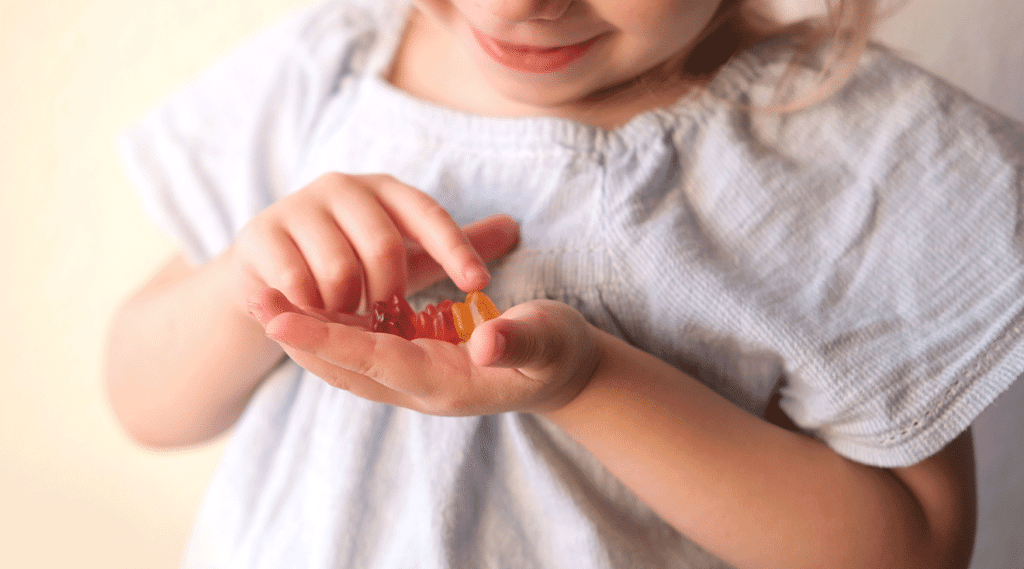
.
3. Therapeutic Gummies (CBD/THC and Nutraceuticals)
As the demand for therapeutic gummies continues to rise—particularly in the CBD/THC and nutraceutical sectors—custom molds play a vital role in helping manufacturers meet strict dosing requirements and ensure regulatory compliance. These industries often demand high levels of precision to ensure the safety and effectiveness of the product, which is critical for maintaining legal and industry standards.
.
(1)Industry-Specific Compliance and Customization
In both the nutraceutical and cannabis industries, manufacturers must comply with a wide array of regulatory requirements, including FDA, GMP (Good Manufacturing Practices), and state-level cannabis laws. This is where GummyGenix’s custom molds stand out by offering solutions that address these industry-specific needs.
- Precise Dosing: GummyGenix custom molds are designed to produce gummies with exact portion sizes to ensure accurate dosage, which is critical for products like CBD/THC gummies or vitamin supplements. Whether you're manufacturing 10mg CBD gummies or 25mg THC gummies, our molds guarantee consistency in every batch.
- Regulatory Compliance: The nutraceutical and cannabis industries are heavily regulated, and meeting these legal requirements is non-negotiable. GummyGenix molds are built with food-grade materials (FDA and ISO-certified), ensuring your gummies are produced in compliance with industry standards for safety and quality. Additionally, our molds can be customized to help traceability and batch control, essential for regulatory audits.
- Custom Branding: With custom molds, you can include unique logos, symbols, or trademarks that help distinguish your product in the competitive marketplace. For example, CBD/THC gummy molds normally are shaped like leaves, cannabis symbols, or even the company logo, creating brand recognition and adding a level of professionalism to the packaging.
.
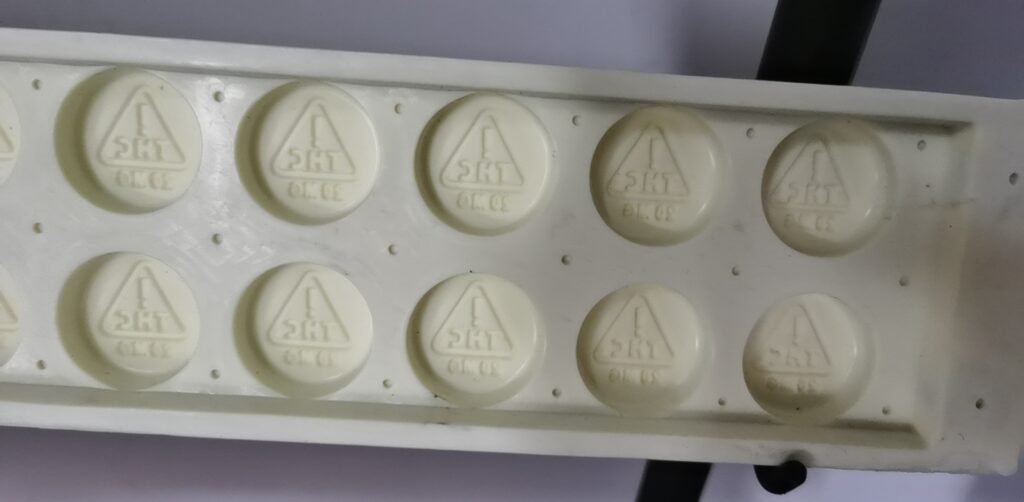
.
(2)Examples of Custom Solutions for Nutraceuticals and CBD/THC Gummies
- CBD Gummies for Health and Wellness: A manufacturer producing CBD-infused gummies may require molds designed for precise dosages, such as 10mg or 25mg per gummy, to comply with product labeling laws and maintain customer trust. GummyGenix molds can also be customized to produce sugar-free, vegan, or gluten-free gummies for health-conscious consumers.
- THC Gummies for Legal Markets: In states where cannabis products are legalized, manufacturers are bound by strict dosage limits (often 10mg of THC per gummy). Using custom molds from GummyGenix ensures each piece meets legal dosage requirements while offering a distinct brand identity through unique shapes and logos.
- Nutraceutical Gummies for Supplement Brands: For vitamin and supplement brands, consistency is key. GummyGenix offers custom molds for multivitamin, fiber, or protein gummies that require precise formulations. Whether you’re manufacturing gummies with added minerals or producing fortified health products, our molds provide high precision to ensure correct nutrient content in each piece.
.
(3)The Role of Custom Molds in Product Differentiation
In these competitive sectors, having a visually appealing and well-branded gummy is as important as meeting regulatory guidelines. GummyGenix allows you to create high-quality molds that not only ensure compliance but also enhance consumer appeal. Custom shapes and designs tailored to CBD/THC products or nutraceutical gummies help your brand stand out in a crowded marketplace.
.
By incorporating GummyGenix molds into your production line, you can confidently meet dosage accuracy and regulatory requirements while producing gummies that reflect your brand’s identity and commitment to quality.
.
Types of Gummy Molds by Material
When choosing gummy molds for your business, you must consider their unique properties to get the most suitable products. Let’s take a closer look:
1. Silicone Molds for Gummies
Most gummy makers prefer silicone because it is flexible and easily takes any shape. FDA food grade silicone gummy molds can withstand different temperatures, are non-stick and tough for repeated use. Moreover, these molds are common in depositing systems for their easy gummy removal, ensuring perfectly shaped gummies with no damage.
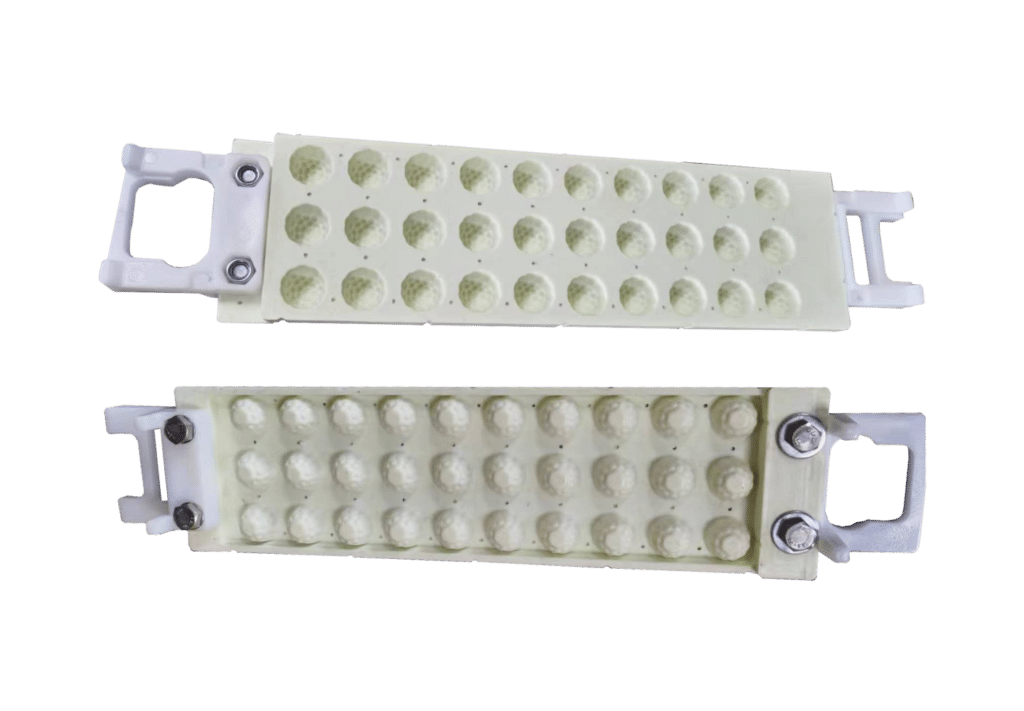
- Temperature Resistance: Food-grade silicone molds are known for their ability to withstand temperatures ranging from -40°C to 260°C (-40°F to 500°F), making them suitable for both high-heat cooking and low-temperature cooling processes.
- Durability: Silicone molds offer long-lasting durability, capable of enduring over 1,000 production cycles without degrading. Their flexibility allows for easy demolding, which prevents damage to the gummies and the molds themselves.
- Efficiency: The non-stick nature of silicone reduces the need for mold preparation and cleaning between batches, enhancing production efficiency by minimizing downtime.
- Technical Specifications:
- Cavity Size: Typical silicone molds for gummies can have cavity sizes ranging from 20mm to 50mm in length, and the depth can vary from 5mm to 10mm, depending on the gummy design.
- Weight Capacity: Each cavity typically holds 2g to 5g of gummy mixture, perfect for standard gummy sizes like gummy bears or fruit shapes.
- Production Yield: With a standard mold tray of 50 cavities, you can expect a production yield of 100 to 250 grams of gummies per tray, depending on cavity size. For small-scale operations, this yields approximately 10 to 20 trays per hour, translating to 1,000 to 5,000 gummies per hour in small batch runs.
Interested in learning how silicone molds can improve your small-scale gummy production? Discover our range of silicone molds at GummyGenix, designed to fit flexible production needs.
.
2. Teflon-Coated Aluminum Molds
These molds are commonly crafted from stainless steel or aluminum. They offer exceptional durability and heat conduction, suitable for high-volume production. However, they can be more expensive and require careful handling to prevent warping or scratching. The metal used may also react with acidic gummy mixtures, potentially affecting flavor or causing discoloration.
Teflon-Coated Aluminum Molds are the go-to for automatic gummy depositors for large-scale gummy production. The Teflon coating applied on these aluminum gummy molds offers non-stick properties, making demolding a breeze. Thus, the Teflon aluminum molds boost efficiency in gummy-making processes and allow for easy cleaning after use.
.
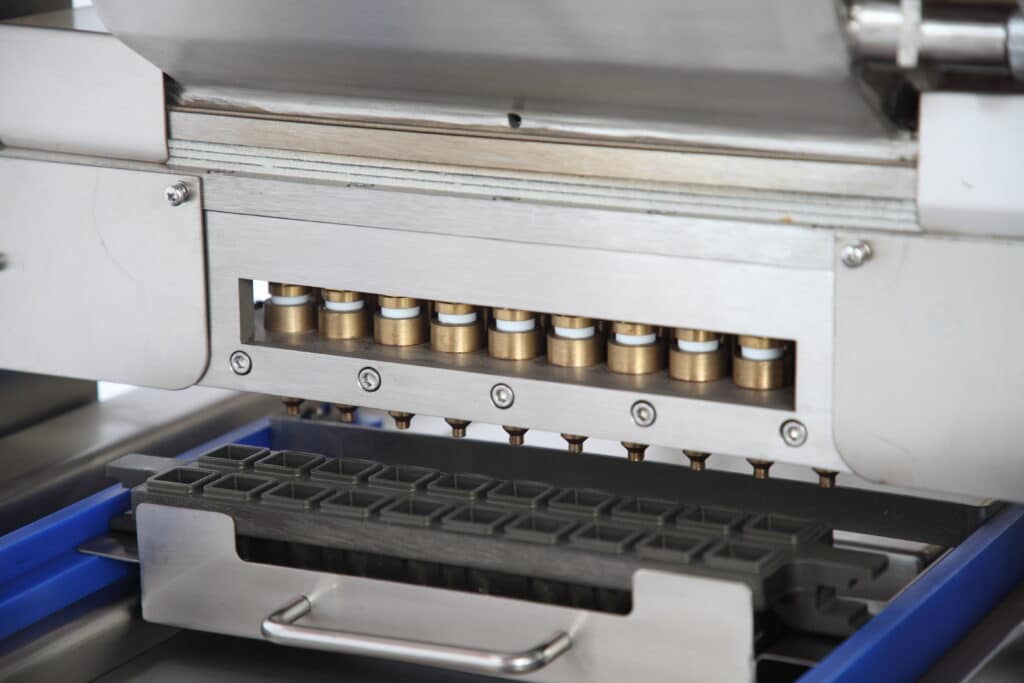
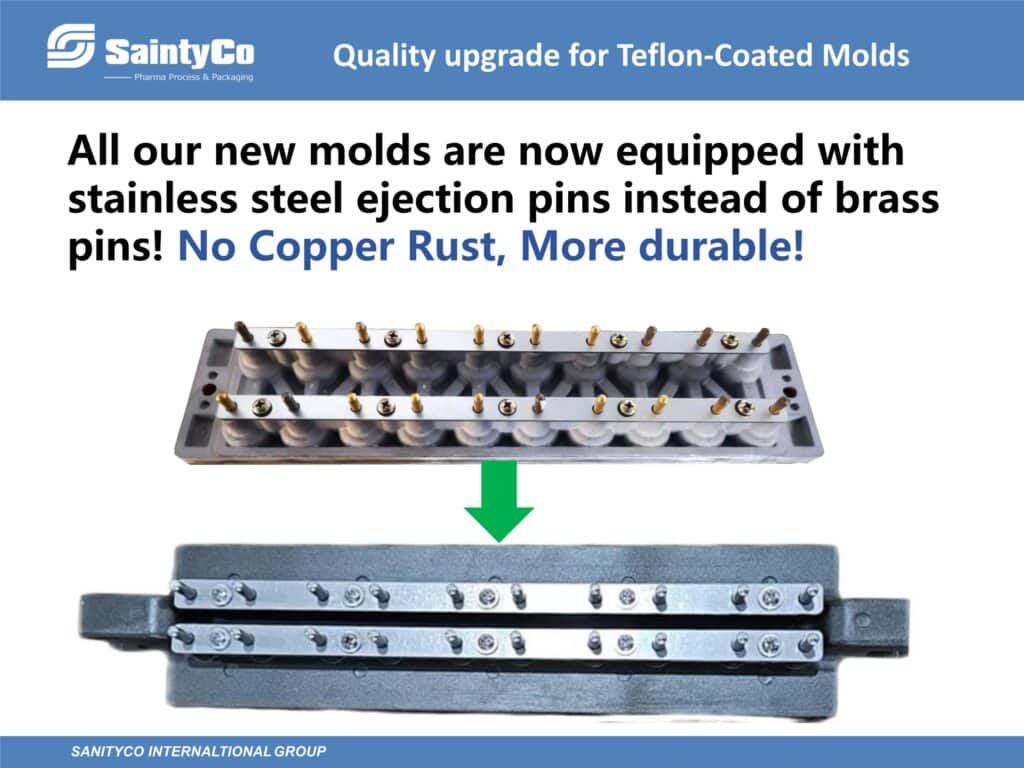
.
- Temperature Resistance: Molds made from Teflon-coated aluminum are highly resistant to high temperatures, withstanding up to 300°C (572°F). This makes them ideal for high-heat production lines where consistent performance under intense conditions is required.
- Durability: The aluminum core provides strength and thermal conductivity, while the Teflon coating ensures non-stick properties for 3,000–5,000 production cycles without losing efficiency. This combination is highly durable, suitable for long-term, high-volume manufacturing.
- Efficiency: Aluminum’s excellent thermal conductivity allows for faster heating and cooling, ensuring gummies set more quickly and consistently, which boosts overall production speeds.
- Technical Specifications:
- Cavity Size: Teflon-coated aluminum molds generally have 20mm to 40mm cavities, with depths of 8mm to 15mm, depending on the specific gummy design and size requirements.
- Weight Capacity: Each cavity can hold 3g to 7g of gummy mixture, making them ideal for larger gummies like vitamin supplements or custom-shaped gummies.
- Production Yield: A typical aluminum mold tray has 100 to 200 cavities, producing between 300g to 1,400g of gummies per tray. Automated lines using these molds can produce 10,000 to 30,000 gummies per hour, depending on the depositor speed and cooling efficiency.
.
Looking to streamline large-scale production with durable molds? Explore Teflon-coated molds that boost efficiency and consistency.
.
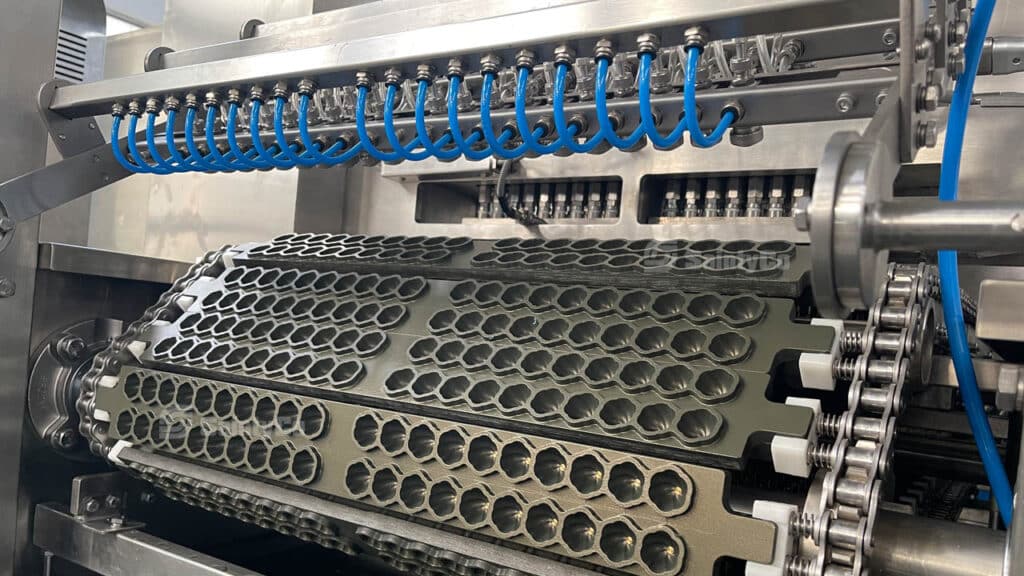
.
3. Plastic Mold
Clear plastic gummy molds give a clear view of the gummy mixture. Candy makers can easily gauge the consistency and thickness of the gummy syrup during depositing and setting. These molds are flexible and it is easy to remove softer gummies with no damage on them. Plus, they boast impressive heat resistance of up to 350°C.
.
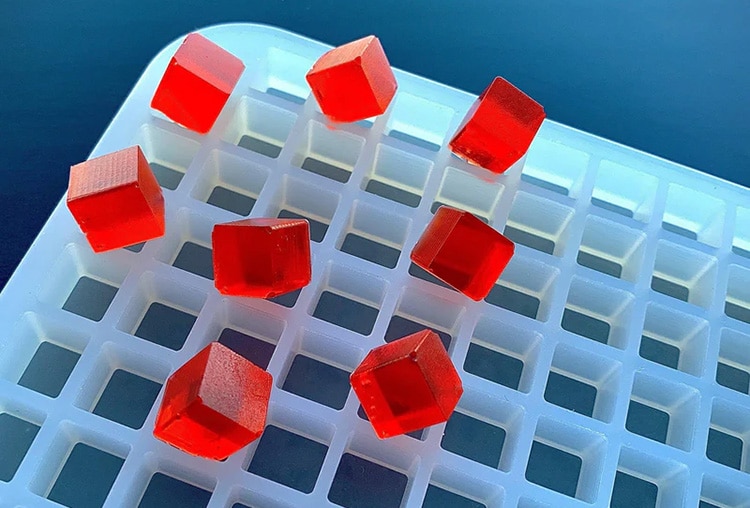
.
4. Polycarbonate Gummy Molds
These gummy molds are tough and transparent. Their transparency allows for easy monitoring of the gummy setting process. Also, their durability ensures resistance to high temperatures and repeated use without warping or cracking. On the flip side, polycarbonate molds tend to be more expensive than other options and may scratch if handled poorly.
- Temperature Resistance: Polycarbonate molds typically withstand temperatures up to 140°C (284°F), making them ideal for processes where visual monitoring of the gummies during setting and cooling is important.
- Durability: With a rigid structure, polycarbonate molds can be used for 2,000+ cycles with proper care, providing sharp, detailed gummy shapes over repeated production runs.
- Efficiency: The transparent nature of polycarbonate allows operators to visually inspect the gummies as they cool and solidify, ensuring consistent quality control throughout the production process.
- Technical Specifications:
- Cavity Size: Polycarbonate molds offer more intricate shapes with cavity sizes ranging from 15mm to 30mm in diameter, with depths of 5mm to 12mm for more complex designs like 3D gummies or multi-vitamin gummies.
- Weight Capacity: Each cavity holds 1.5g to 4g of gummy mixture, allowing for detailed, small-sized gummies suitable for specialized markets like nutraceuticals or luxury gummies.
- Production Yield: A typical polycarbonate mold tray contains 50 to 100 cavities, resulting in a production yield of 100g to 400g per tray. These molds are often used in mid-sized production lines, producing 5,000 to 15,000 gummies per hour, depending on equipment and mold capacity.
.
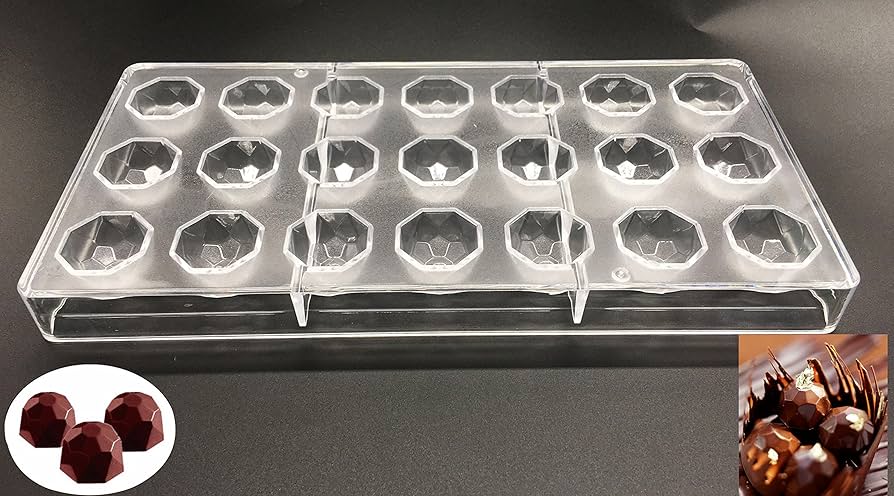
.
For industrial gummy manufacturers, having precise technical specifications helps optimize production lines and reduce errors. By understanding the exact cavity dimensions, weight capacities, and expected production yields for each type of mold, businesses can choose the best mold materials for their production needs, ensure consistent quality, and accurately calculate costs and output. At GummyGenix, our custom molds are designed with these critical factors in mind, ensuring that your production runs smoothly from start to finish.
.
Detailed Technical Specifications
Mold Type | Cavity Size (mm) | Weight Capacity per Cavity (g) | Typical Tray Capacity | Production Yield (g per tray) | Gummies per Hour |
Silicone Molds | 20mm to 50mm | 2g to 5g | 50 cavities | 100g to 250g | 1,000 to 5,000 |
Teflon-Coated Aluminum | 20mm to 40mm | 3g to 7g | 100-200 cavities | 300g to 1,400g | 10,000 to 30,000 |
Polycarbonate Molds | 15mm to 30mm | 1.5g to 4g | 50-100 cavities | 100g to 400g | 5,000 to 15,000 |
Types of Gummy Molds by Use
1. Industrial gummy mold
These are gummy molds designed for large-scale production to be integrated into automated depositing and cooling machines. The gummy depositor accurately fills each mold cavity with the gummy mixture, ensuring consistency and efficiency. The cooling machine then solidifies the gummies, maintaining their shape and texture. Industrial gummy molds are typically made from durable materials like Teflon-coated aluminum or polycarbonate to withstand continuous and rigorous use.
.
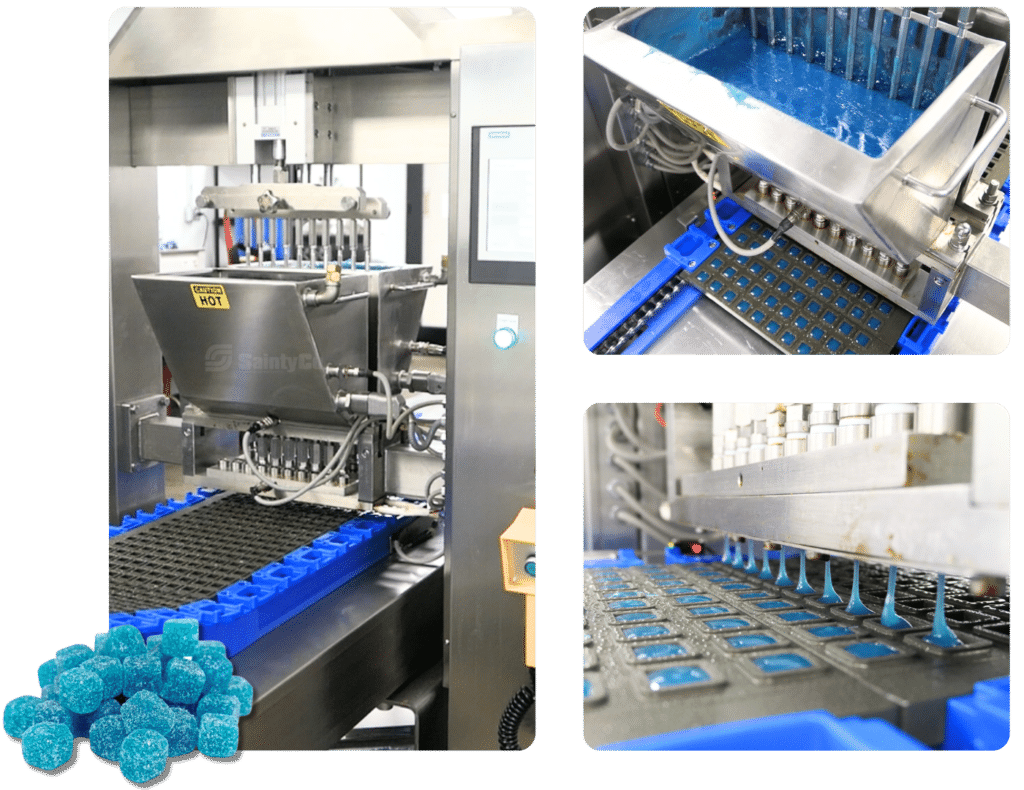
.
Take your industrial gummy production to new heights with custom molds designed for automation. Explore our industrial gummy molds for large-scale manufacturing.
.
2. Home-based gummy molds
These are smaller molds designed for individual or small-batch gummy making. They are often made from silicone or plastic materials and can be filled manually using droppers, spoons, or piping bags. Startups and small-scale gummy makers can experiment with various shapes and flavors for personalized gummy treats for their loved ones or potential customers.
.
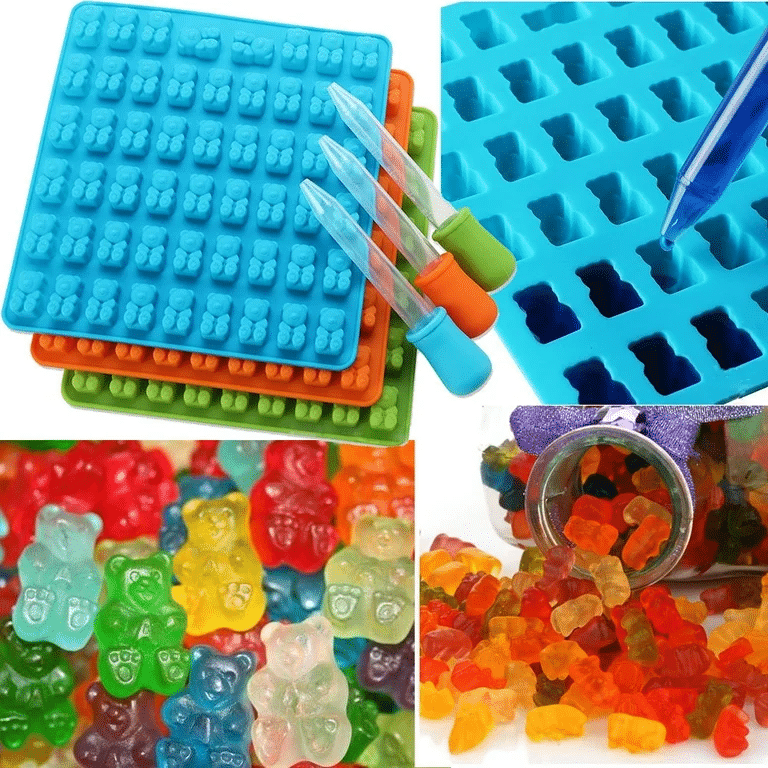
.
Common Custom Gummy Mold Designs
Customized gummy molds present a wide assortment of interesting cavity shapes in 2D and 3D designs. They include:
Gummy bears mold
Gummy berries mold
Dome shaped molds
Orange slices mold
Heart-shaped mold
Leaf-shaped mold
Square shape mold
Geometrical patterns
Fruit-shaped molds and more
.
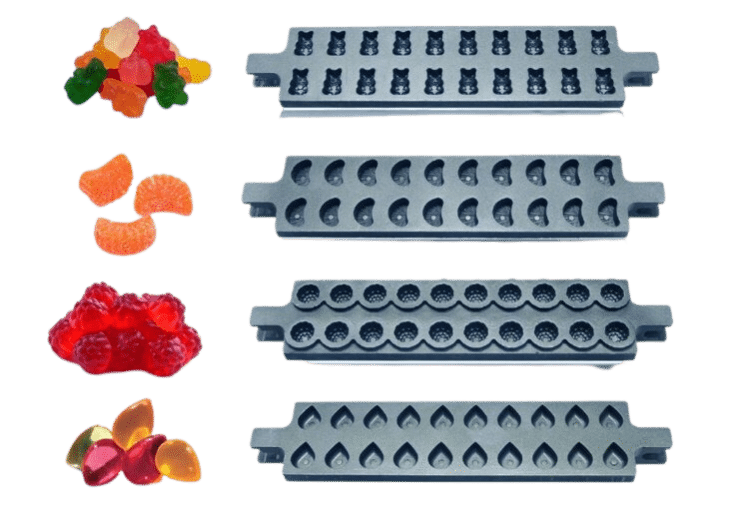
.
How Custom Gummy Molds Fit Seamlessly into Automated Production Lines
At GummyGenix we offer a full gummy-making production line with beautiful built-in gummy mold designs. The seamless integration makes mass production easy, and you can order now to enjoy exclusive offers.
GummyGenix molds are specifically engineered to integrate effortlessly with automated gummy production lines, ensuring consistency, efficiency, and high-quality results. Our molds are compatible with a wide range of automated systems, including gummy depositors, demolding machines, and cooling tunnels, making them ideal for both small-scale and industrial-scale manufacturers.
.
1. Seamless Integration with Automated Gummy Depositors
GummyGenix molds are designed to work hand-in-hand with advanced gummy depositors. The precise cavity alignment ensures that each gummy mold is filled accurately and consistently, with minimal waste and overflow. This reduces production downtime caused by manual adjustments and ensures uniform gummy size and weight, key factors in maintaining production standards.
- Optimized Filling Efficiency: Our molds are optimized for automated depositors that ensure each cavity is filled at high speeds without causing air pockets or uneven fillings, which can occur with inferior molds. This results in smoother, more precise gummy shapes.
- Compatibility with High-Speed Depositors: Whether you’re using a high-speed rotary depositor or a linear depositor, GummyGenix molds are built to withstand the speed and pressure of industrial depositors, ensuring flawless performance even under the most demanding conditions.
.
![[Gummy Machine] G150 Gummy Production Line - SaintyCo](https://gummygenix.com/wp-content/cache/flying-press/TXs20euXnkY-hqdefault.jpg)
.
2. Improved Demolding Efficiency
The seamless demolding process is critical for high-volume gummy production. GummyGenix offers molds with non-stick coatings like Teflon, which allow gummies to be easily removed from the molds without damaging their shape or surface.
- Non-Stick Technology: Our custom metal molds, especially those coated with Teflon, ensure that each gummy releases effortlessly, minimizing downtime and improving production speed. This non-stick feature reduces the need for manual intervention, preventing mold damage and wear.
- Automated Demolding Machines: GummyGenix molds are built for compatibility with fully automated demolding systems. These systems can demold hundreds of gummies in seconds, significantly speeding up the production process while maintaining the integrity of each piece. By integrating our molds with these machines, gummy manufacturers can achieve consistent, rapid, and damage-free demolding in every batch.
.
3. Enhanced Cooling and Setting Performance
Once gummies are deposited into the molds, the cooling process is essential to achieving the desired texture and firmness. GummyGenix molds are designed with materials that enhance thermal conductivity, ensuring that gummies cool evenly and consistently throughout the entire production line.
- Even Heat Distribution: Our metal molds, particularly those made from aluminum with a Teflon coating, offer superior heat transfer, allowing gummies to set faster and more consistently. This reduces production time and ensures that each gummy solidifies with uniform texture and appearance.
- Cooling Tunnel Compatibility: GummyGenix molds are also built to integrate with automated cooling tunnels. The precise dimensions and material properties of our molds ensure that they fit seamlessly into conveyor systems, allowing for uniform cooling as gummies travel through the tunnel, preventing overcooling or hot spots.
.
4. Durability for Continuous Production Cycles
Durability is key in high-volume production environments. GummyGenix molds are constructed from high-quality materials like food-grade silicone and Teflon-coated aluminum, which are designed to withstand continuous use without warping or degrading.
- High Cycle Rates: These molds can withstand thousands of production cycles, maintaining their shape and non-stick properties even under the stress of continuous high-speed production. This reduces the need for frequent mold replacements, lowering long-term operational costs.
- Resistance to Harsh Production Environments: Whether exposed to high temperatures during the cooking phase or cold temperatures in the cooling tunnels, GummyGenix molds retain their integrity, ensuring uninterrupted production without quality loss.
.
5. Scalability for Industrial Production
As gummy manufacturers grow their operations, scalability becomes critical. GummyGenix molds are designed to be scalable and compatible with different production line configurations, allowing manufacturers to increase their output without changing molds or investing in new equipment.
- Custom Sizing for Production Lines: GummyGenix offers molds in various sizes and configurations to match your specific production needs. Whether you require molds for small-batch production or high-output industrial lines, our molds can be tailored to meet the requirements of any scale.
- Modular Design for Flexibility: Our molds feature a modular design that allows for easy switching between different shapes and sizes, giving manufacturers the flexibility to respond to market trends and customer demands without costly equipment overhauls.
.
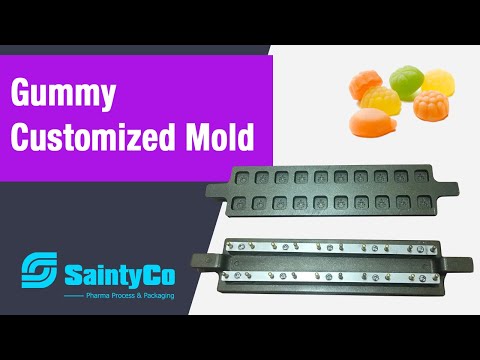
.
Looking for custom molds that integrate effortlessly into your production line? See our full range of gummy production equipment and molds today.
.
Troubleshooting Common Gummies Molds Problems
Even with high-quality gummy molds, production issues can arise. Here are some of the most common problems gummy manufacturers face and practical solutions to ensure smooth, efficient gummy production.
1. Preventing Gummies from Sticking to Molds
Sticking issues are one of the most common problems in gummy production, especially when using molds made from materials like plastic or aluminum without proper coatings.
Solutions:
- Use Non-Stick Coatings: Molds made from materials like silicone or Teflon-coated aluminum have natural non-stick properties that prevent gummies from adhering to the mold. If you're using metal molds without Teflon, apply a food-grade non-stick spray or a thin coat of oil before pouring the gummy mixture.
- Ensure Proper Demolding Time: Allow the gummies to fully set and cool before attempting to demold them. Rushing the process can cause gummies to stick or tear apart. Use a cooling tunnel or chilled environment to speed up the setting time and ensure the gummies harden uniformly.
- Monitor Temperature: Improper heating or cooling can cause gummy mixtures to stick to molds. Ensure the gummy syrup reaches the correct temperature before pouring, and avoid cooling the molds too quickly, which can cause uneven texture and sticking.
.
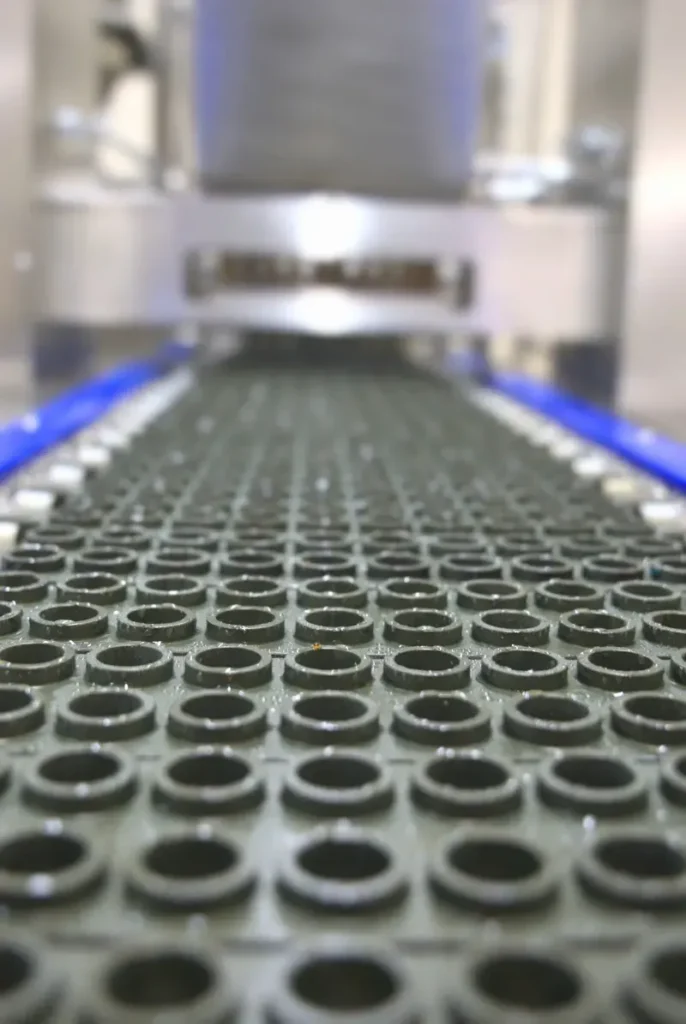
.
2. Solving Demolding Problems
Demolding gummies without damaging their shape can be a challenge, especially when using intricate mold designs or working with less flexible materials.
.
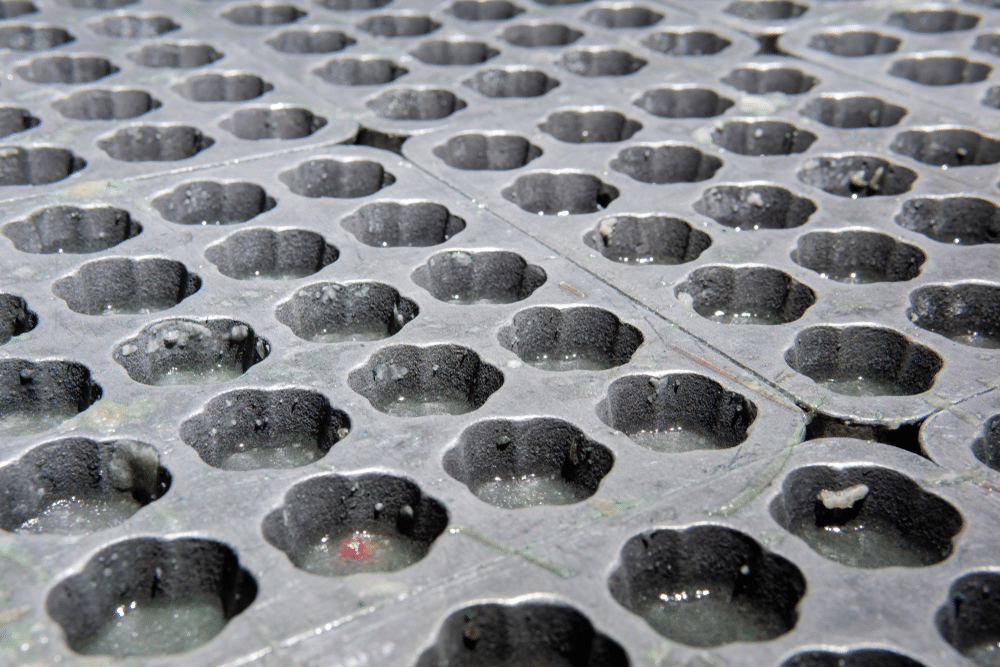
.
Solutions:
- Choose Flexible Materials: Silicone molds are ideal for easy demolding since they can flex and bend, allowing the gummies to pop out without damage. For large-scale production, ensure that your Teflon-coated aluminum molds have a smooth, even coating to aid in demolding.
- Use Automated Demolding Machines: If you're working in a high-volume production environment, consider using automated demolding equipment. These machines apply gentle pressure to release the gummies from the molds without manual labor, reducing the risk of damage and speeding up production.
- Ensure Gummies are Fully Set: Trying to demold gummies before they are fully cooled can result in tearing or misshapen pieces. To prevent this, ensure that the cooling process is complete. Aluminum molds, for example, offer faster cooling due to their excellent thermal conductivity, reducing the likelihood of premature demolding.
- Avoid Overfilling the Molds: Overfilled molds can lead to difficulty during demolding as excess gummy material may spill over the edges and harden. Make sure the molds are filled to the correct level using precise depositors that can control the flow of the gummy syrup.
.
3. Ensuring Even Filling of Gummy Molds
Uneven filling can result in inconsistent gummy shapes and sizes, which affects both product quality and production efficiency.
Solutions:
- Use Precision Depositors: Automated gummy depositors are essential for ensuring consistent and even filling of each mold cavity. These machines allow you to control the exact amount of gummy mixture being deposited into each mold, preventing over- or under-filling.
- Check Syrup Viscosity: The viscosity (thickness) of the gummy syrup plays a critical role in even mold filling. If the syrup is too thick, it may not fill the mold cavities evenly. Conversely, if it's too thin, it may overflow and cause uneven shapes. Adjust your gummy recipe or syrup temperature to achieve the ideal consistency for your molds.
- Maintain Proper Mold Alignment: In automated production lines, ensure that the molds are properly aligned with the depositors. Misaligned molds can result in cavities being overfilled or missed entirely. Regularly check your equipment to make sure the depositor nozzles are aligned with the mold cavities.
.
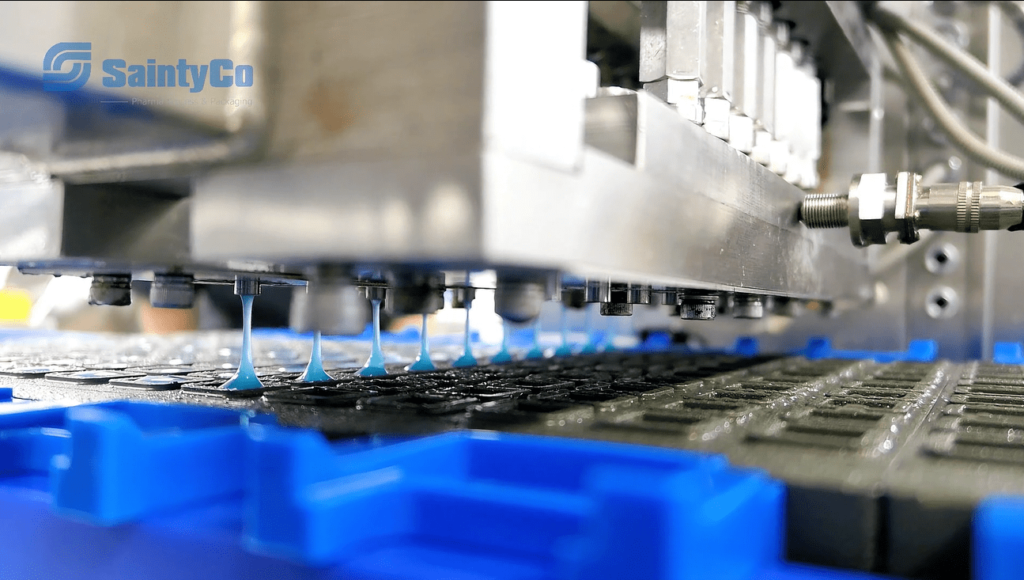
.
4. Handling Air Bubbles in Gummies
Air bubbles can form during the gummy-making process, leading to imperfections in the final product. These bubbles often occur when the gummy mixture is poured too quickly or without proper degassing.
Solutions:
- Degas the Mixture: Before pouring the gummy mixture into the molds, make sure to degass the syrup to remove any trapped air. This can be done by allowing the syrup to sit for a few minutes after cooking or by using vacuum equipment to extract air bubbles.
- Pour Slowly and Evenly: When manually filling molds, pour the mixture slowly and steadily to avoid introducing air bubbles. In automated production, make sure the depositor is set to an appropriate speed to ensure a smooth, bubble-free filling.
- Tap the Molds: After filling the molds, gently tap them on the work surface to encourage any trapped air bubbles to rise to the top and escape. For automated production lines, vibrating platforms can be integrated to remove air bubbles from the filled molds before they move to the cooling tunnel.
.
Optimizing Gummy Production with GummyGenix Molds
At GummyGenix, our custom-designed molds are engineered to address these common issues, ensuring smooth, consistent gummy production every time. Whether you're working with small batches or running a high-volume production line, our molds—crafted from food-grade silicone, Teflon-coated aluminum, and polycarbonate—are built to provide easy demolding, even filling, and seamless integration with automated systems. Our team is here to assist with troubleshooting any production challenges you encounter, ensuring your success in the gummy industry.
.
Pricing for Molds for Gummy Bears
The prices of candy gummy molds depend on your needs and budget. For instance, you can purchase a heart-shaped candy mold for under $4 at Michael's or for as little as $2 on Amazon (in a pack of four). These are mostly plastic, perfect for small batches and are available in different shapes and sizes. Their price range is usually around $3 to $10.
If you run a candy business, it’s best to purchase an entire gummy production line, including gummy-making, molding, coating, and packaging solutions. For industrial-scale production, gummy molds are generally more durable and designed for high-volume use. These molds can range from $100 to $300 or higher for a single industrial gummy mold! (e.g., Teflon-coated aluminum molds)
As a gummy manufacturer, you should consider the following to find an optimal price for the most suitable gummy mold:
- Compatibility with production machines: To streamline the manufacturing process, ensure that the molds are compatible with your chosen gummy-making and demolding machines.
- Quality and durability: You should prioritize gummy molds made from high-quality materials. A good example is metal coated with a Teflon that can withstand continuous use.
- Customization options: Look for manufacturers and suppliers like GummyGenix that offer custom gummy molds tailored to your product design and branding needs.
.
With all these factors considered, you should purchase from GummyGenix. We have a range of high-quality gummy molds designed for industrial use with complete production lines. By choosing GummyGenix, you can access a full suite of gummy-making equipment with molds optimized for your specific production requirements.
.
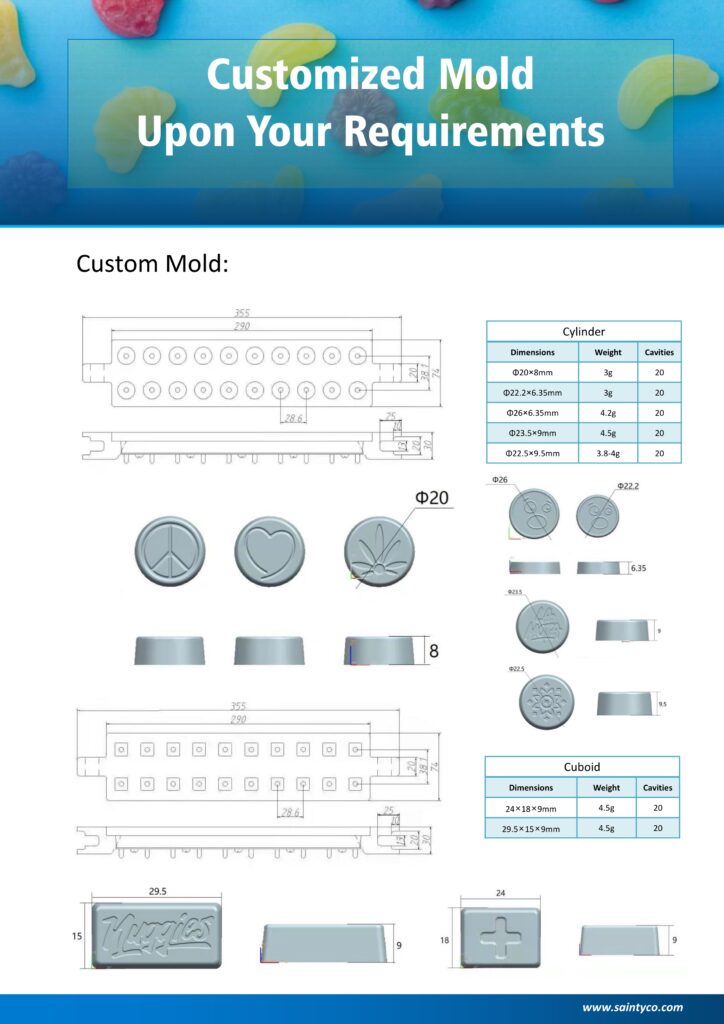
.
GummyGenix Silicone Gummy Candy Molds and Metal Molds
GummyGenix, a sub-brand of SaintyCo, provides innovative automated gummy production and packaging solutions. We have the semi-automated gummy depositor and demolder, as well as the fully automated gummy production line. All our gummy production machines are designed to work seamlessly with our custom gummy molds for efficiency and consistency.
Our custom gummy molds come in two premium materials, each offering distinct advantages to fit your production needs:
1. GummyGenix FDA Compliant Silicone Molds
These molds are crafted from food-grade, flexible silicone for easy demolding with minimal waste to reduce production downtime. Their non-stick surface ensures smooth and flawless gummy treats every time. Silicone is a highly durable material that withstands high heat for longevity and consistent performance. Moreover, silicone molds offer versatility and precision in every batch, making them ideal for producing complex shapes and intricate designs.
.
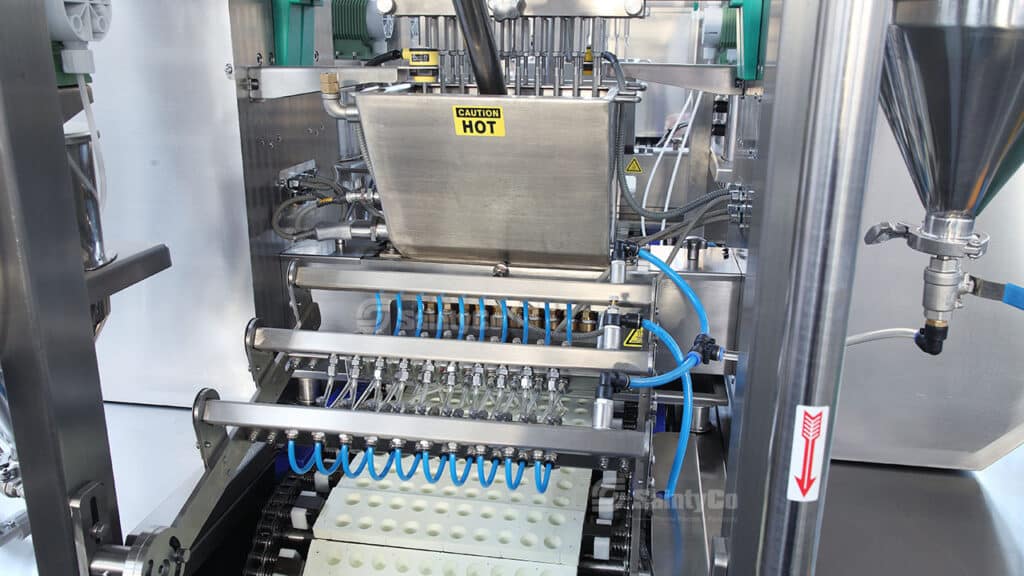
.
2. GummyGenix Metal Molds
These metal molds are precision-engineered from robust, corrosion-resistant stainless steel for heavy-duty, high-volume production. They offer exceptional durability and uniform heat distribution, ensuring consistent cooking, cooling, and texture of every gummy. Metal molds are perfect for large-scale operations. They are built to handle repeated use with minimal maintenance, providing long-term reliability and cost-effectiveness.
.
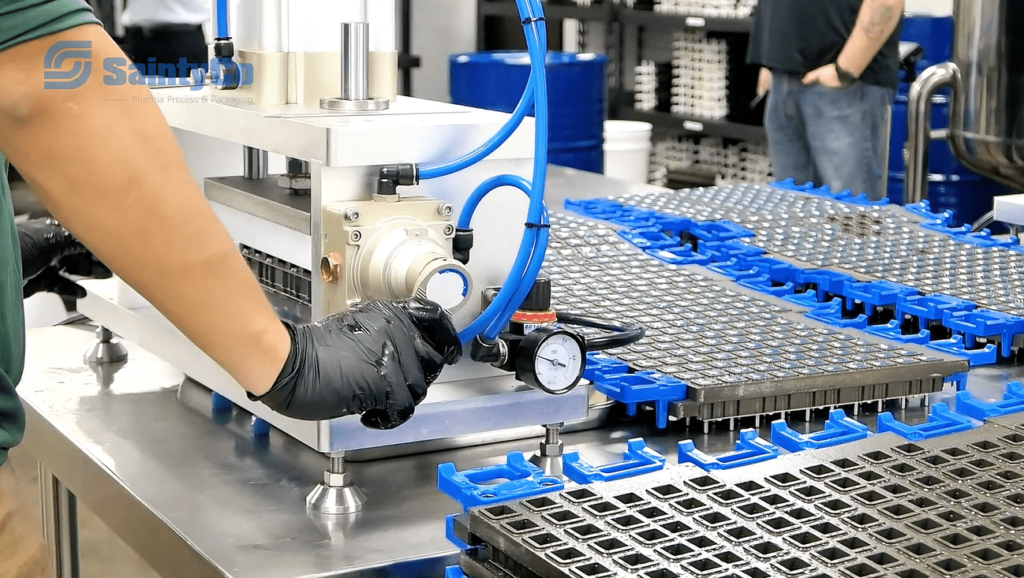
.
Why Choose Gummy Candy Molds from GummyGenix?
- Precision and efficiency: GummyGenix gummy molds are precisely engineered to integrate seamlessly with our depositors and demolders. This ensures consistent gummy shapes and sizes with no waste and maximized production efficiency.
- Streamlined production: GummyGenix provides a comprehensive solution from cooking and depositing to cooling and packaging. The fully integrated production line simplifies the entire gummy-making process. Say goodbye to complex workflows and fragmented processes.
- Tailored to your brand: At GummyGenix, we understand that your gummies are an extension of your brand identity. That's why we offer customizable silicone molds for gummies for flexibility and intricate shapes or metal for durability and high-volume production.
- Your success is our priority: GummyGenix is committed to helping candy makers succeed in the competitive gummy market.
.
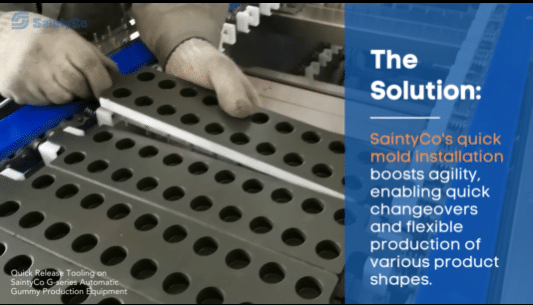
.
A good example is Martin’s gummy business success story in CBD/THC gummies.
.
FAQs about Gummy Molds
1. How should I clean my gummy molds for proper sanitation?
Cleaning gummy molds requires a gentle approach to prevent damage and preserve the non-stick surface, especially on Teflon-coated molds. Prompt cleaning after each use is essential to prevent residue buildup.
Do's:
- Use mild detergents: Opt for cleaners specifically designed for Teflon or delicate surfaces.
- Employ gentle cleaning methods: Hand wash with warm water and a soft brush, or use a steamer or dishwasher for deeper cleaning.
- Dry thoroughly: Wipe with a clean cloth or use an air gun to remove moisture and prevent rust on metal components.
- Store properly: Place molds separately in a dry, ventilated area to prevent stacking damage and moisture buildup.
Don'ts:
- Avoid harsh chemicals: Strong acids or alkaline cleaners can damage the Teflon coating.
- Don't use abrasive tools: Stiff brushes or hard objects can scratch the mold surface.
- Don't stack molds: Stacking can cause wear on the Teflon coating.
- Don't store in damp environments: Humidity can lead to Teflon coating failure or rust on metal parts.
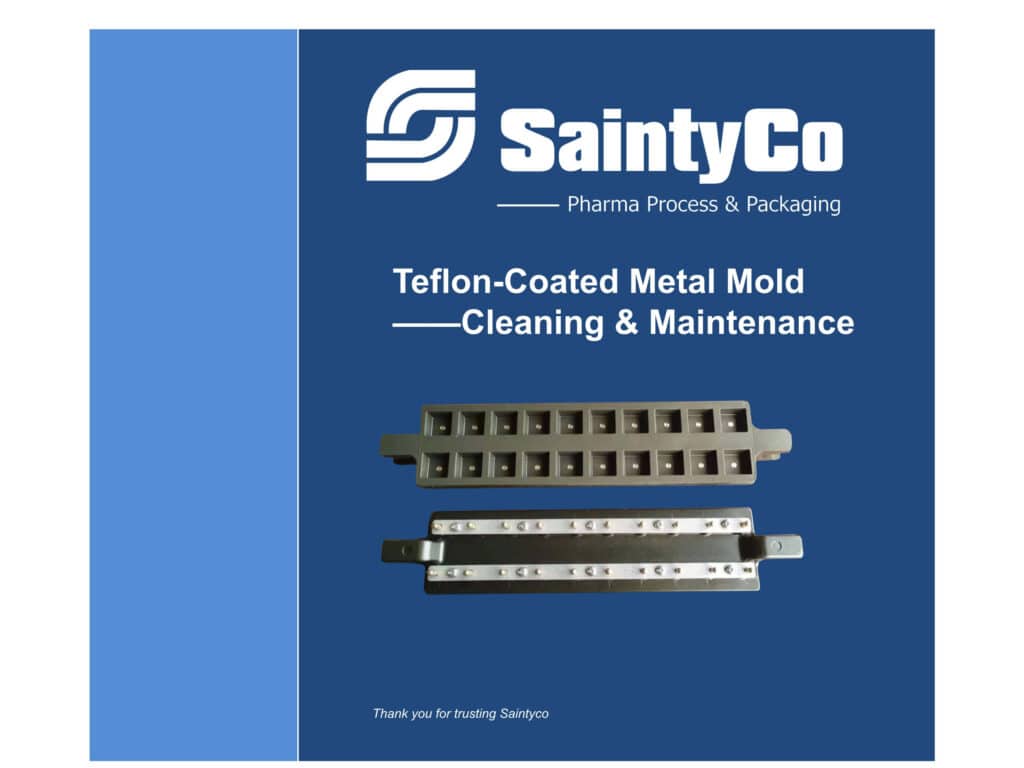
.
2. What’s the best way to prevent candies from sticking to the mold?
The best way to prevent gummy candies from sticking to the mold is to ensure a clean and completely dry mold before use. For intricate designs or if using a material other than silicone, lightly grease the mold with a food-grade oil spray or a thin layer of coconut oil. Allow the gummies to set completely before attempting to remove them, and if needed, gently flex or tap the mold to release the candies. Using high-quality molds with non-stick properties like silicone or Teflon also significantly reduces the risk of sticking.
.
3. Can I get custom gummy molds for multi-colored gummy designs?
Yes, you can get custom gummy molds from GummyGenix to accommodate multi-colored gummy designs. This often involves creating separate cavities for each color, allowing you to pour different colors into designated sections of the mold. You should consult with our sales and support team to discuss your specific design needs. This will ensure the mold is crafted to facilitate your multi-colored gummy production needs.
.
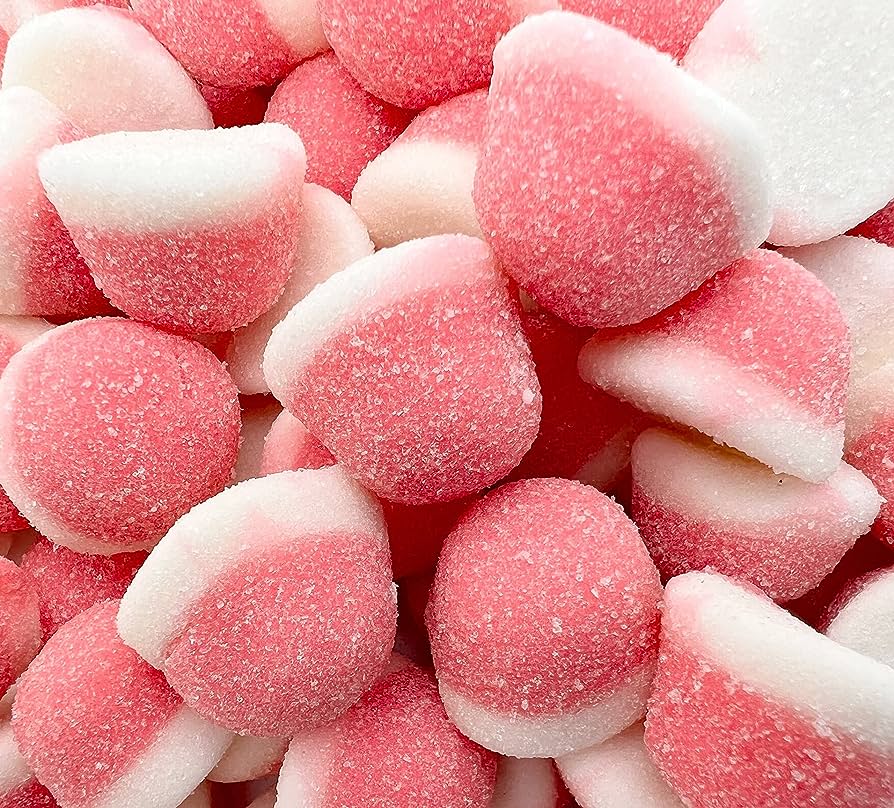
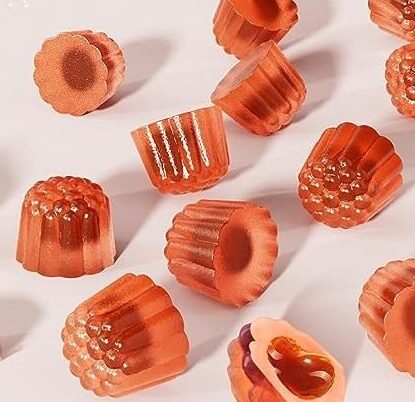
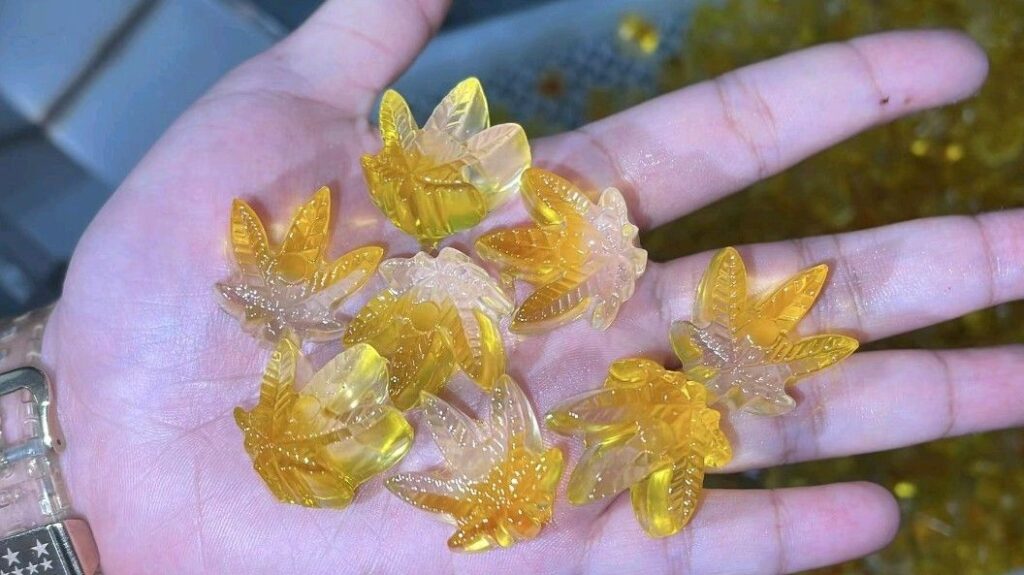
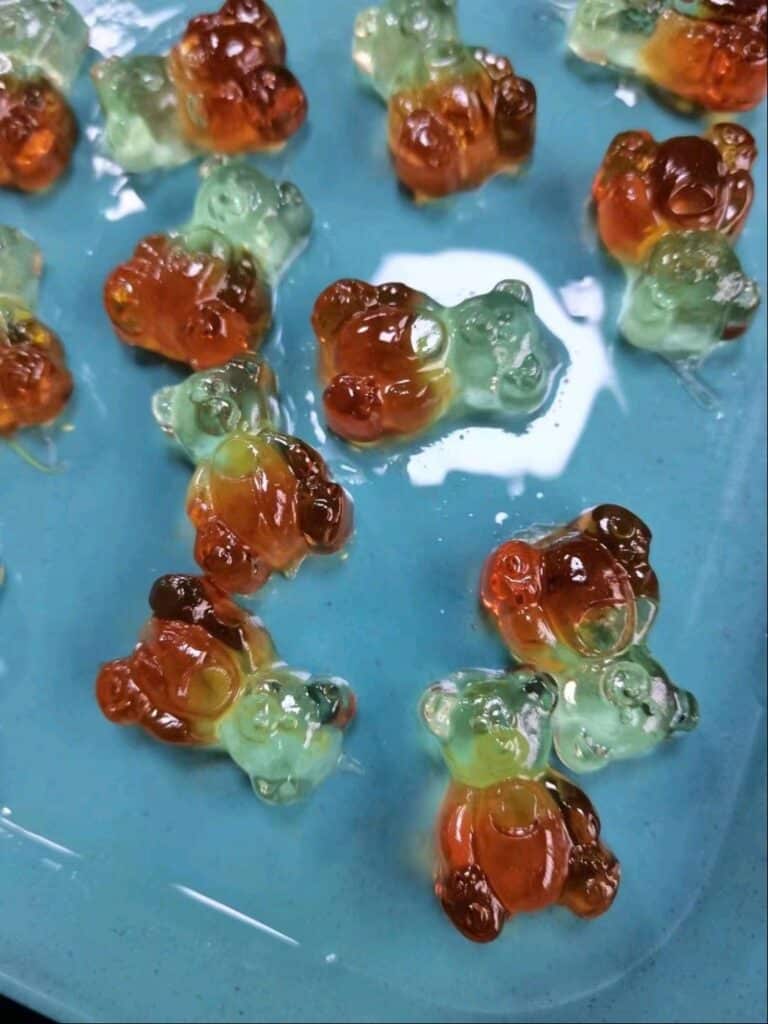
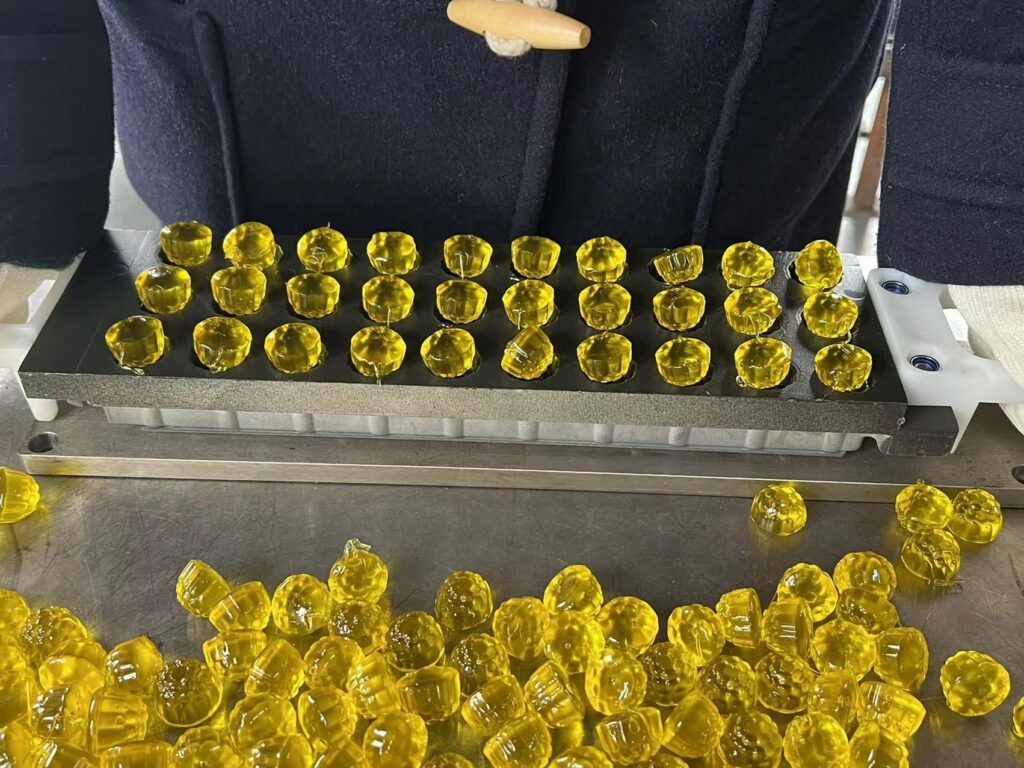
.
4. What affects gummies getting into a perfectly molded shape?
There are several interconnected factors that can influence how well gummies take on the shape of the mold. They include:
- Mold quality: A high-quality mold with precise details will produce sharper and more defined gummies.
- Gummy recipe: The consistency of the gummy mixture is crucial. Too thick, and it may not fill all the mold details; too thin, and it may spread and lose shape.
- Filling technique: Avoid overfilling the mold, as this can lead to overflow and misshapen gummies.
- Setting time and temperature: Allow the gummies to set fully at the correct temperature to ensure they solidify properly and retain their shape.
- Demolding: Be gentle when removing gummies from the mold to prevent tearing or distortion.
.
Need help choosing the right mold or learning more about our products? Contact our expert team at GummyGenix for personalized advice on custom molds.
.
Conclusion
As we've explored, gummy molds are the cornerstone of creating unique candies. Customized gummy molds offer unparalleled advantages in efficiency, quality, and brand differentiation. By partnering with GummyGenix, you gain access to high-quality, tailor-made molds along with a whole production line and expert support.
Our gummy molds are specifically designed to work seamlessly with our equipment, ensuring seamless integration and optimal performance. Due to differences in cavity numbers and mold lengths, they are not suited for machines from other brands. In most cases, our clients first choose our machines and then recognize the benefits of using our custom molds.
Order from GummyGenix to enhance gummy production efficiency with added confidence in your investment!