From Market Entry to Strategic Upscaling
A Fast-Growing Pharma and Wellness Manufacturer’s Transition to SaintyCo’s Medium-Scale Automatic Production Line
Upscaling to the G150 gummy production line from GummyGenix was more than just an upgrade for Mr. Martin’s business; it efficiently accommodated larger orders, fostered broader client collaborations, and paved the way for sustained growth.
In North Carolina, Mr. Martin’s startup began its journey with our DM-20S Gummy Semi-Auto Depositor, quickly establishing a reputation for high quality CBD/THC gummies. With the surge in white-labeling demand, scaling up became imperative.
Recognizing the reliability of SaityCo’s machinery and the consistent support from GummyGenix by SaintyCo, Martin deepened his partnership with us. Our established reputation in the local gummy manufacturing sector, with our extensive knowledge in machinery and automation across pharmaceutical, nutraceutical, and confectionary industries, strengthened Martin’s confidence.
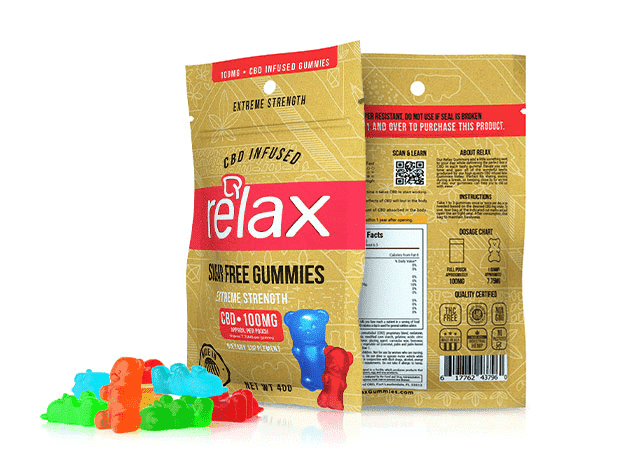
SOLUTIONS PROVIDED
- Customized Equipment Solutions
- Optimized Production Layout
- Seamless Installation & Commissioning
- Comprehensive Staff Training
- Timely Technical Assistance
GUMMY MANUFACTURING EQUIPMENT PROCURED
Initial Phase:
- DM-20S Gummy Semi-Auto Depositor
- De-molding Device
- Molds
- 100L Dissolving Tank
- Sugar Polishing Pan with Inverter
Scale-Up Phase:
- G150 Auto Gummy Production Line: a whole setup including cooking, CFA dosing, depositing, cooling, demolding, coating, and packaging processes
- Sugar Sanding Drum and Conveyer
- Custom Gummy Molds
- GummyCount 40 Bulk Counter
- Ultra-8 Premade Pouch Filling Machine with Code Printing
- Z Type Bucket Chain Gummy Loader
KEY WINS
- Production boost to 50,000 gummies/hour.
- Successfully fulfilled a 2 million gummy order for a global retailer.
- Achieved a 15% gain in operational efficiency.
- Launched 5 new product lines within a year.
- Collaborated with over ten major domestic wholesalers and retailers.
- Perfect scores in FDA and cGMP audits.
Client Profile: Mr Martin's Journey from Startup to Strategic Upscale
Name: Mr. Martin
Position: Vice President (VP)
Company: Founded in 2018 by a team of pharmaceutical scientists and industry veterans.
Location: 10,000 sq.ft. facility in North Carolina, USA.
Industry Focus: Pharmaceuticals, CBD products, wellness supplements, and white label production services.
Challenge Faced: Fragmented Processes & Manual Over-reliance Limiting Efficiency and Output
Within the competitive gummy supplement industry, while the DM-20S semi-auto gummy depositor served its purpose, the fragmented processes and manual dependencies became evident as the business grew.
Key demands as Mr. Martin sought to upscale included:
- End-to-End Production: From cooking to final packaging, ensuring steps like CFA dosing, depositing, demolding, cooling, and coating are seamlessly integrated.
- Consistent Operations: Achieve stable output, particularly with the latest gummy-making technologies.
- Smooth Transition: Move from standalone setups to a fully automated line, optimizing layout and workforce.
- Team Empowerment: Providing comprehensive training to adapt to increased automation.
- Quality First: Guaranteeing premium gummies across all production scales.
- Prompt Support: Ensuring machinery uptime and rapid troubleshooting.
Our Solution: Tailored Machinery Suite and Support for Upscaling Gummy Production
1. In-depth Client Consultation
We sat down with Mr. Martin to understand his operational goals, timelines, budget constraints, and future aspirations. This dialogue allowed us to tailor our expertise to his unique requirements.
Highlight:
- Guided Product Selection: Using insights from our varied client base, we highlighted the G150 Gummy Production Line’s potential, producing 50,000 gummies per hour. Given a 6-hour shift across 22 days, that’s up to 6.6 million gummies a month, though actual output may differ dependent of tank size, cleaning time and depositor speed. Enlightened by this data, Mr. Martin opted for the G150 model.
- Tailored Machinery: Understanding that Mr. Martin’s production goals matched (50 pouches/minute) with our gummy pouch filling machine’s capacity, we observed his specialized packaging — 80mm wide pouches with an unconventional zipper position. To cater to this specificity, we suggested modifications to certain parts, notably the clamp, ensuring seamless packaging operations.
2. Customized Machinery Solutions for Upscaling Gummy Production
1. G150 Automatic Gummy Production Equipment:
- Function: The G150 unit is a comprehensive solution designed for starchless gelatin or pectin gummy candy and medicated gummy production, available in one or two colors.
- Key Features:
- Efficiency:
- Depositor speeds: Up to 60,000 gummies or 150kgs/hr
- Ideal for small to medium-scale production
- Specifications:
- Dimensions: 45’ 11” x 7’ 7”
- Weight: 17,637 lbs
- Build & Design:
- Constructed from SS316 pharmaceutical-grade stainless steel
- Plug-and-pull design for ease of operation
- Operation:
- Recommended operators: 2 – 4
- Controlled via a 10′ Siemens Touch Screen PLC
- Additional Features:
- Certifications: FDA, GMP & CE
- Efficiency:
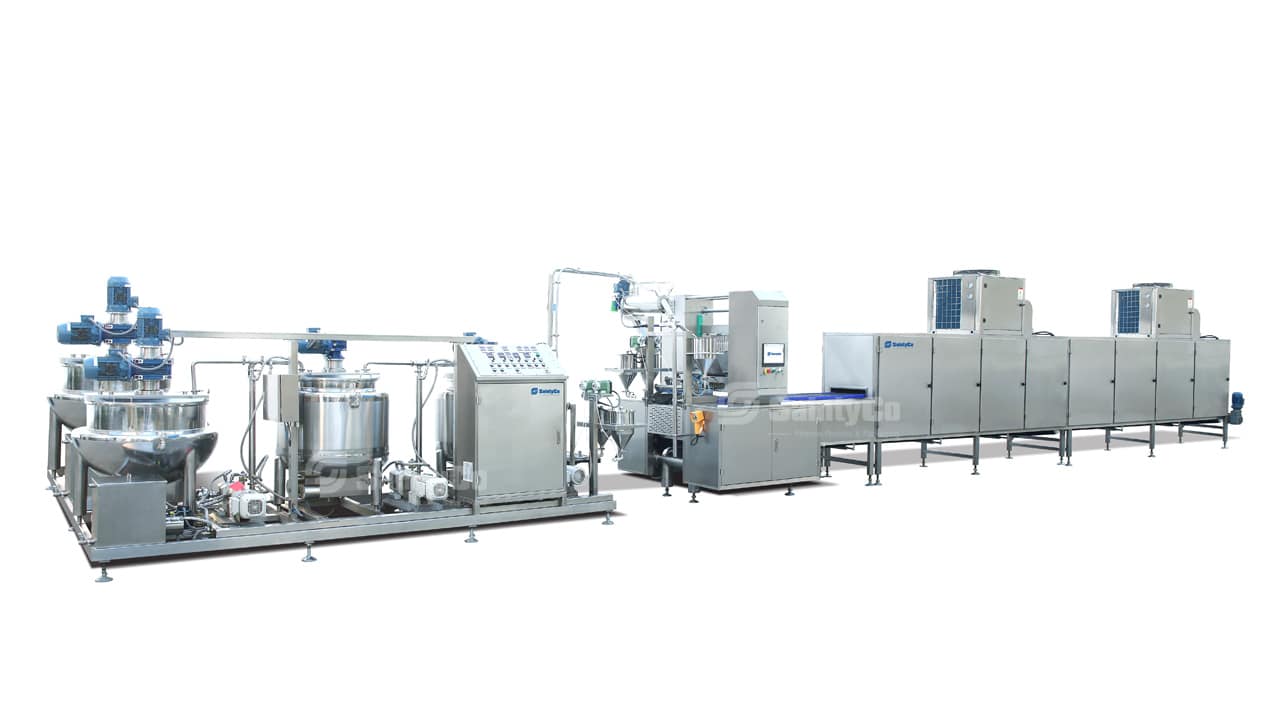
- Included Systems in the G150 Line:
a. Semi-Continuous Cooking System (Pectin/Gelatin):
- Dissolving Tanks: Two 200L jacket-heated tanks for efficient pectin and sugar dissolution, each with a high-shear mixer and variable speed drive.
- Gelatin Processing Tank: 200L capacity with dual heating and cooling functions, integrated with a high-shear mixer, scraper-assisted sweep mixing, and variable speed.
- Heated Transfer Pump: Designed for consistent flow, featuring adjustable speed control.
- Hot Water Recirculation: Comprehensive system with jacketed pipes, heated water tank, and a recirculation pump to maintain optimal temperatures.
- Storage Tank: 300L jacket-heated unit with scraper-assisted sweep mixing and adjustable speed drive.
- Integrated Electrical Cabinet:Manages power for each cooking unit, oversees the Variable Frequency Drive (VFD), and temperature monitoring.
- Optional: Load cell weighing sensors for enhanced accuracy.
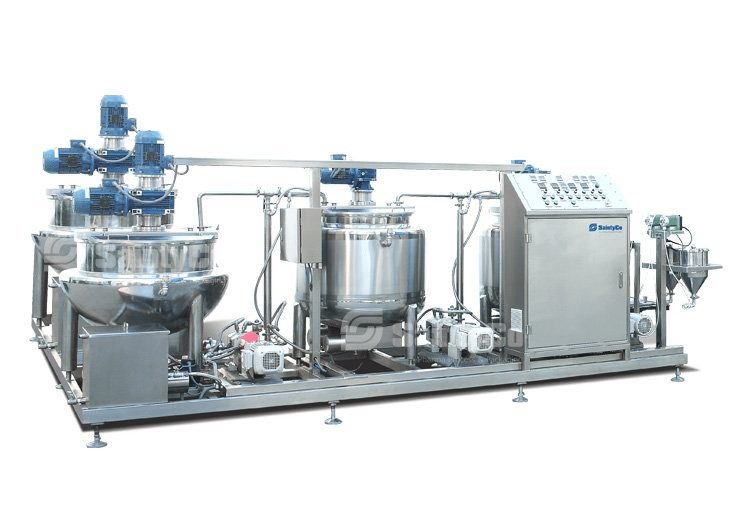
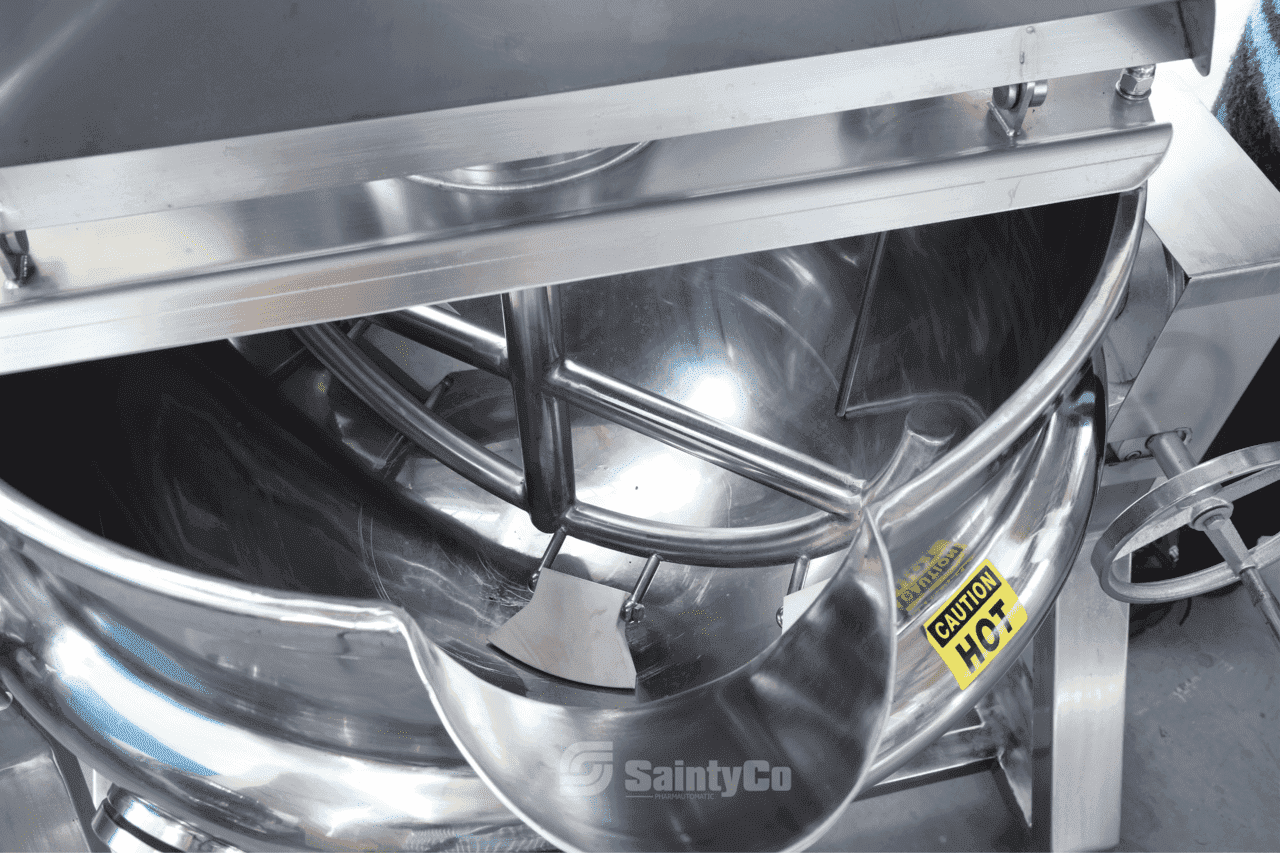
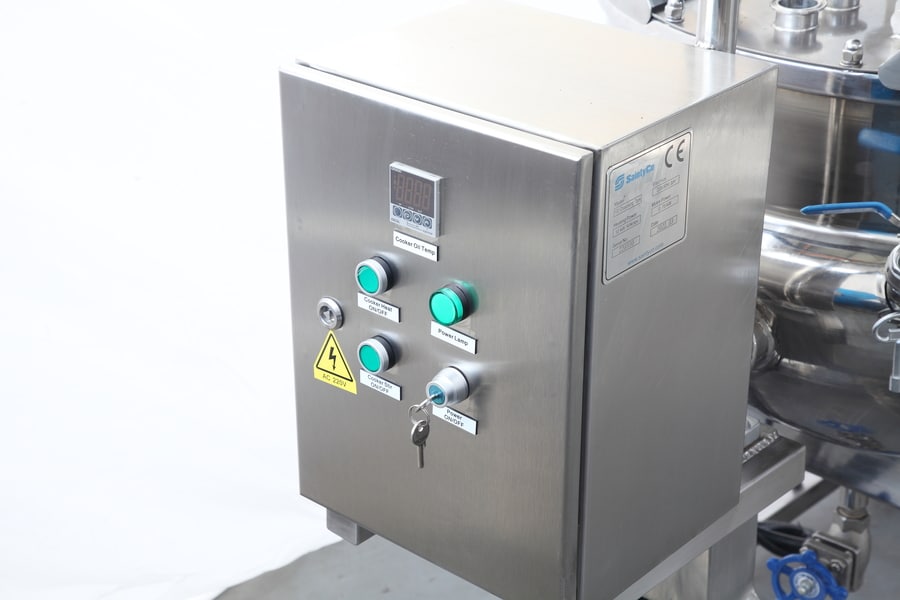
b. Auto CFA Dosing System:
- Mixers for CBD/Vitamin, colors, flavors, and acid.
- Four 20L tanks equipped with MicroDose Metering Pumps.
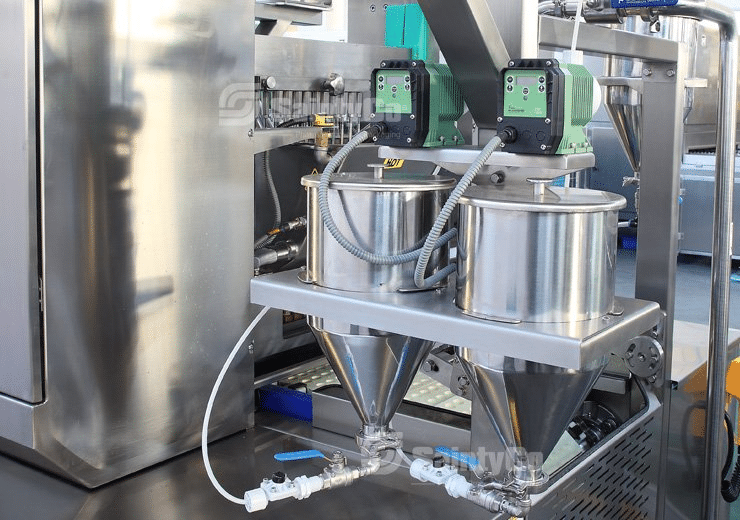
c. Depositing and Demolding System:
- Siemens PLC-controlled and servo-driven system.
- Hopper heating, auto fill volume adjustment, and dual hopper optional for dual color and central filled gummy.
- Efficient demolding with auto oil spraying system, dual brushes, air blowing
- Quick-release mold design.
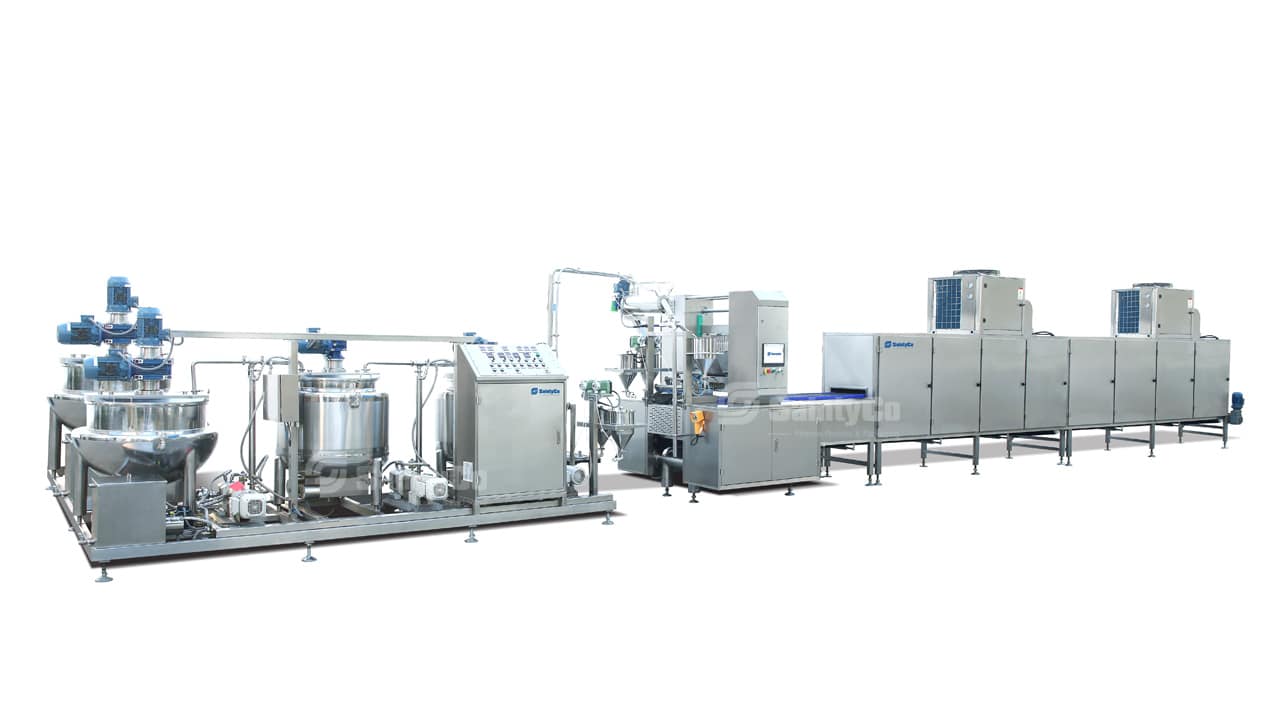
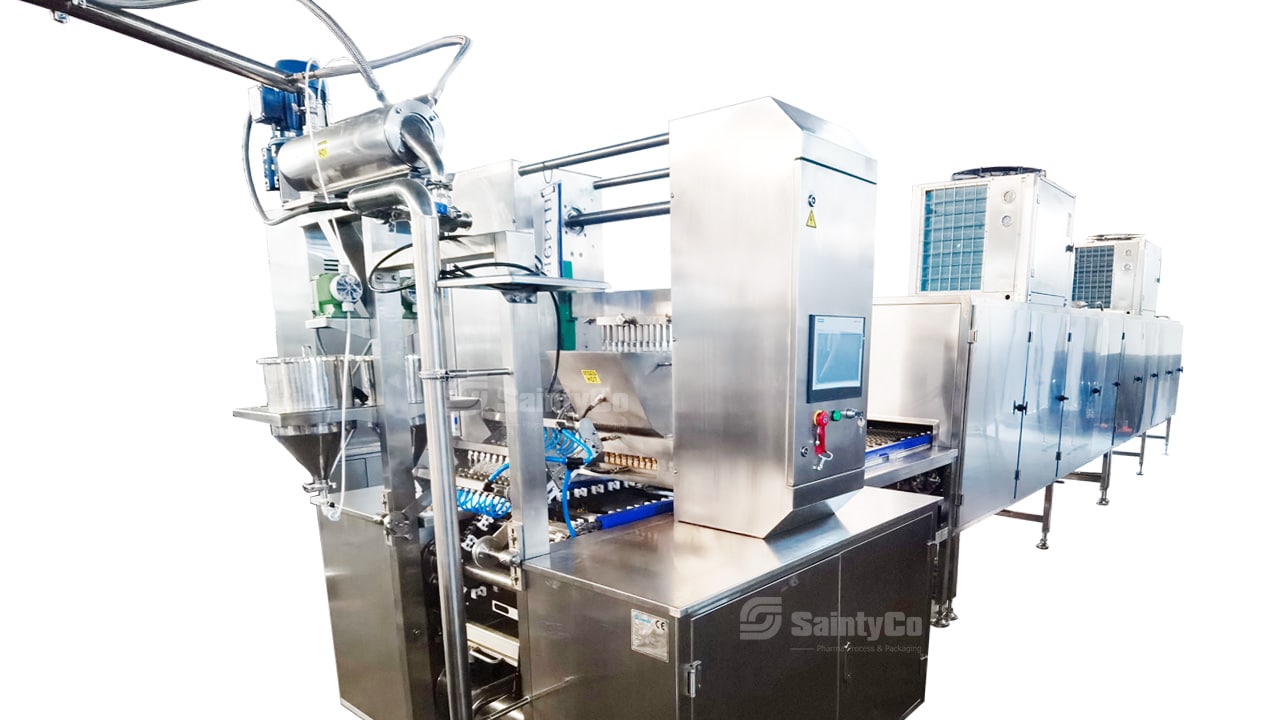
d. Cooling System:
- FDA-approved non-stick cooling belt
- 10HP air cooling within an enclosed tunnel
- Electrical cabinet for temperature and humidity control between 0-20⁰C
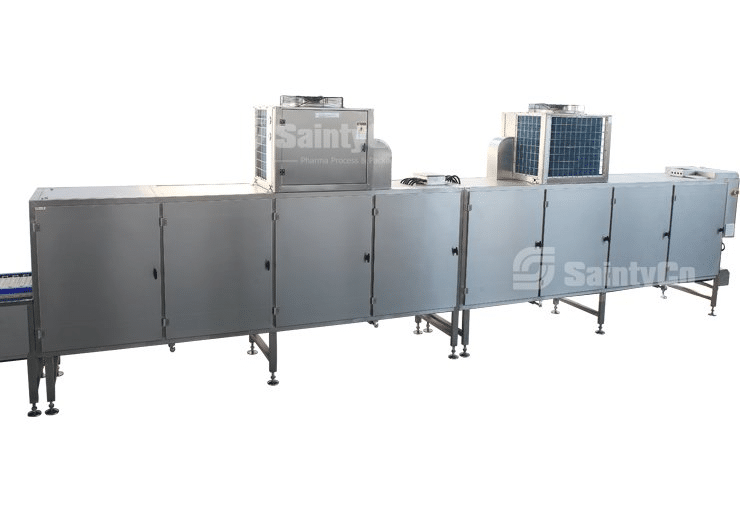
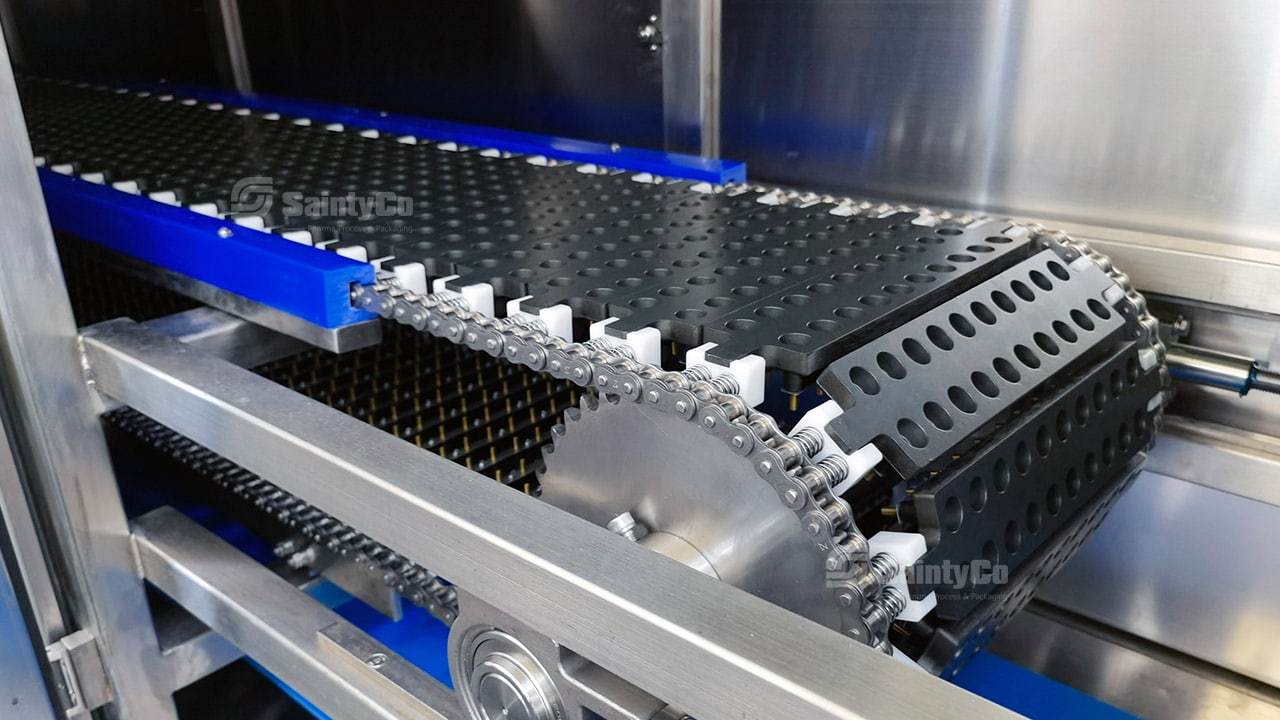
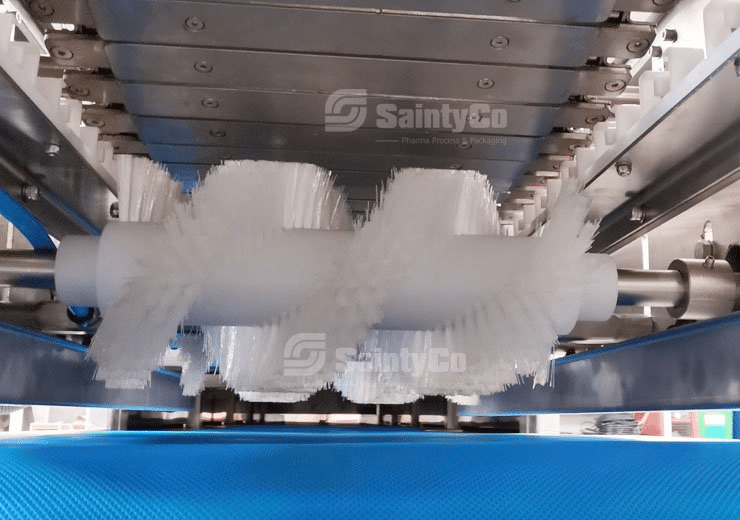
2. Sugar Sanding Drum and Z Type Conveyor:
- Purpose: Facilitates a smooth transition of gummies from the cooling tunnel, guaranteeing a uniformly sugared finish.
- Key Features:
- Adaptable Sugar Application: Tailor the sugar quantity precisely for gummies.
- Optimal Throughput: Achieves up to 600 kg/hr, assuring consistent sugar coating and reliable gummy movement.
- User-Focused Design: Features an intuitive control panel and is easy to clean, reducing downtime.
- Durable Construction: Built entirely from stainless steel 304, meeting the stringent hygiene requirements of gummy manufacturing.
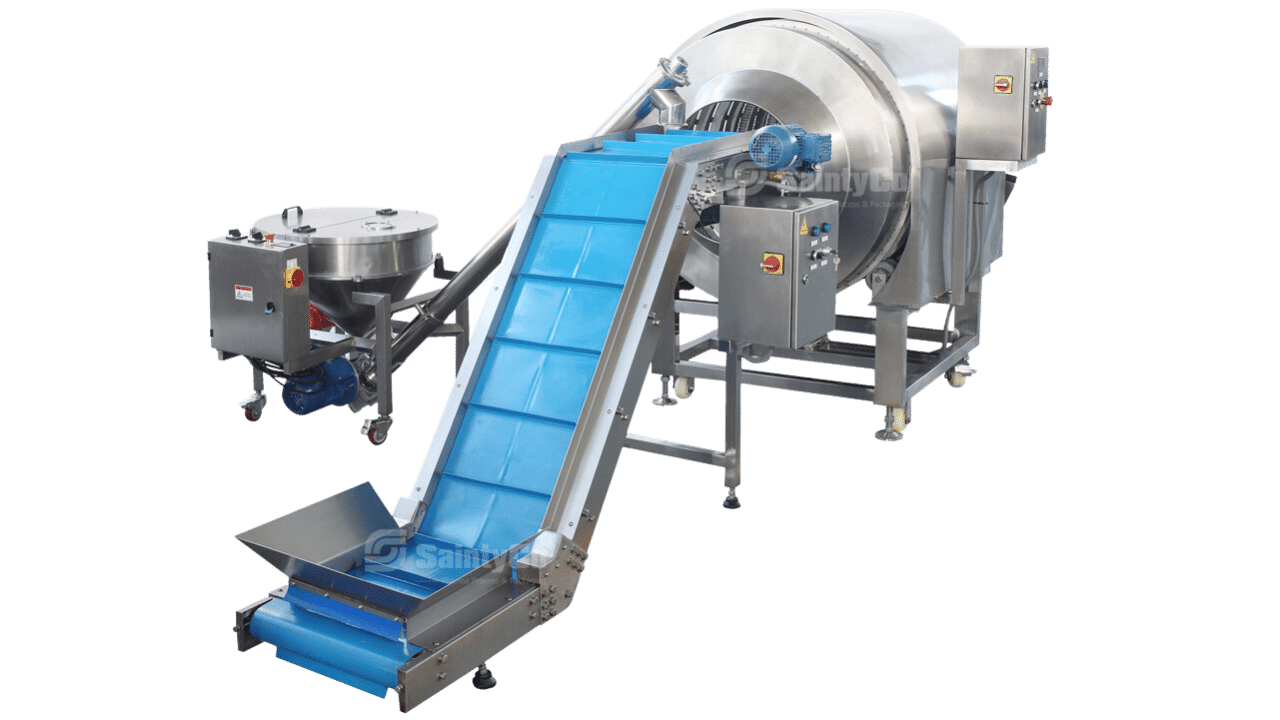
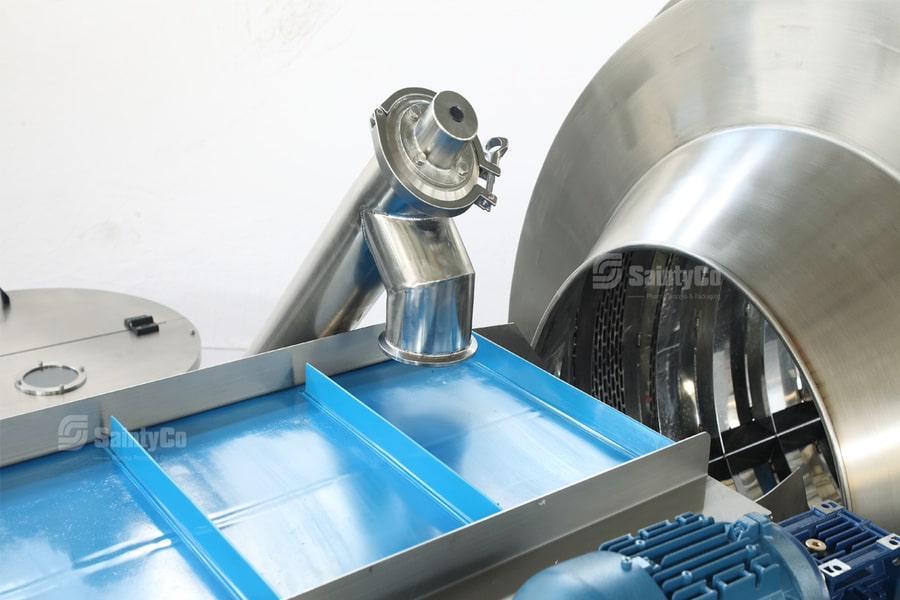
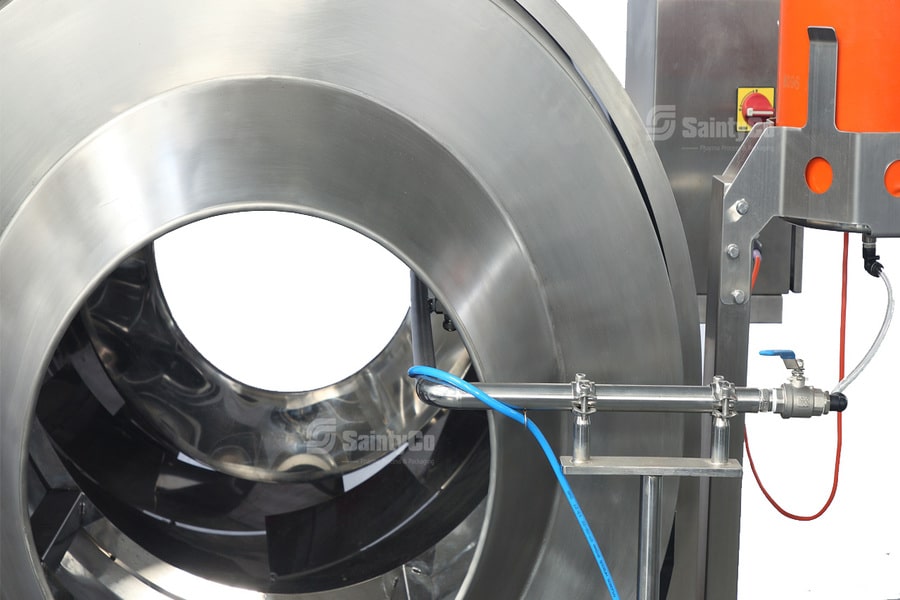
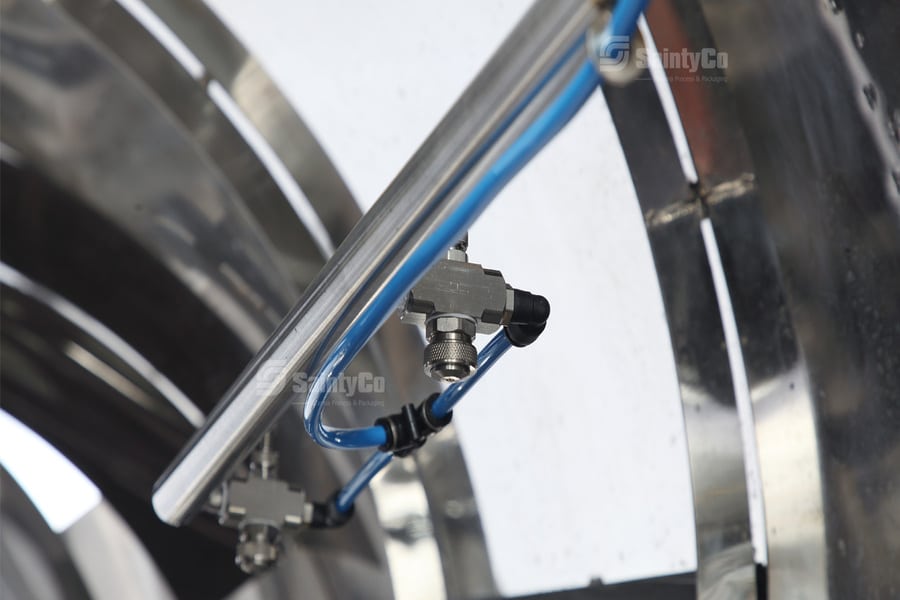
3. Gummy Metal Molds (260 pieces):
- Purpose: Precision molding for gummies.
- Key Features:
- Hygiene: Teflon-coated with stainless-steel ejection.
- Branding: Detailed logo imprinting capability.
- Consistency: 20 cavities per mold ensure uniform output.
- Versatility: Variety of shapes, from standard to custom.
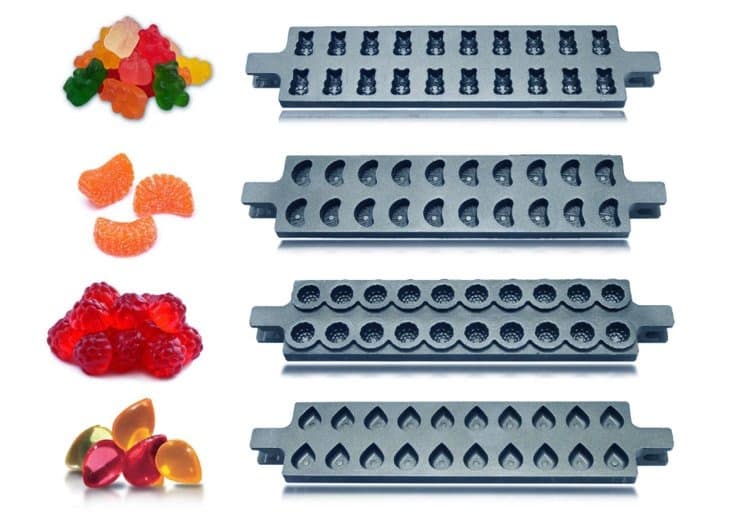
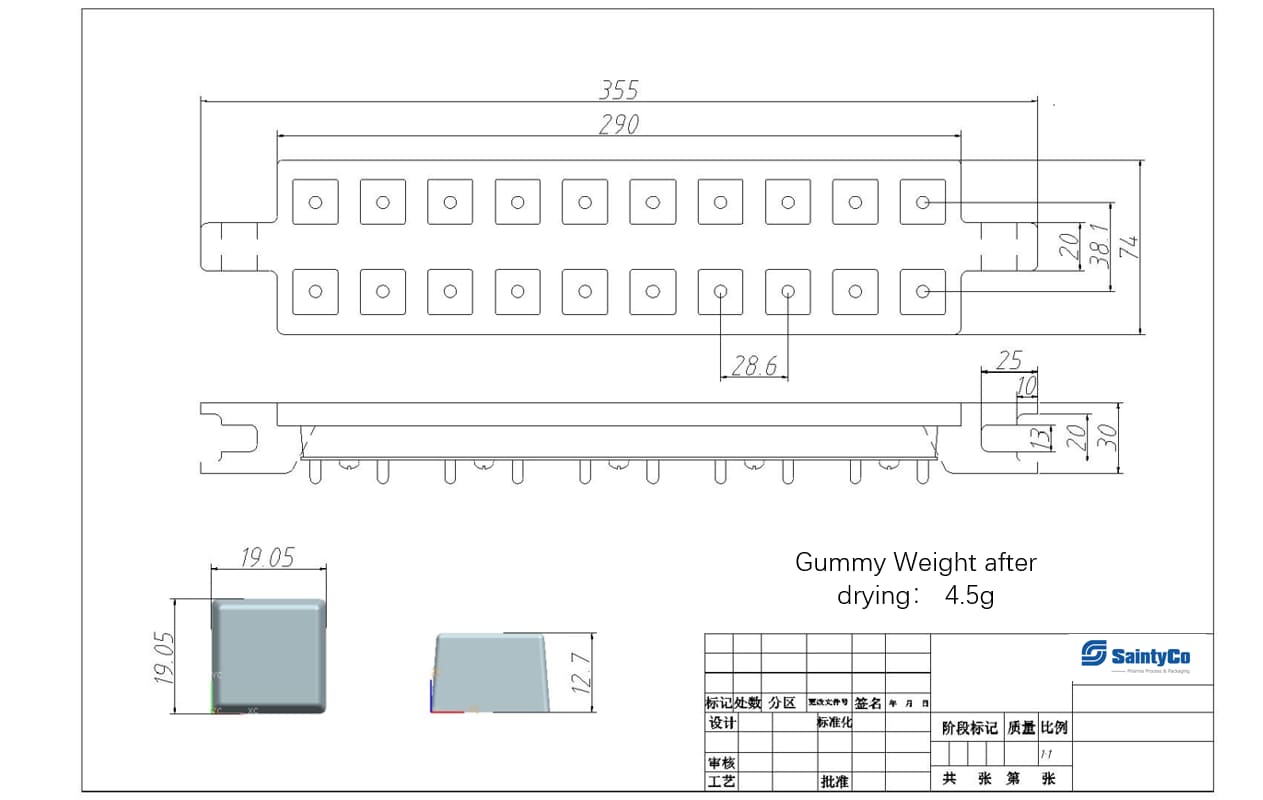
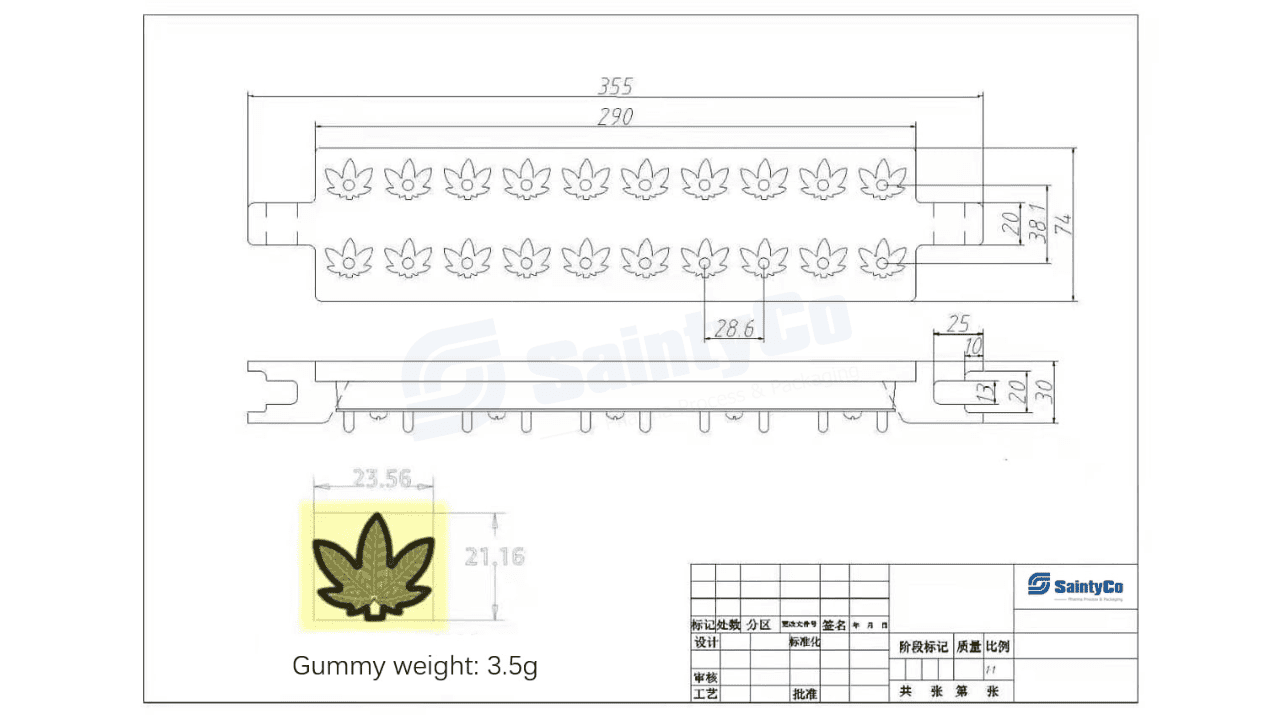
4. Z Type Bucket Chain Gummy Loader:
- Purpose: Efficiently and consistently transports gummies throughout production.
- Key Features:
- Consistent Flow: Utilizes clog-free stainless steel mesh for smooth gummy transport.
- Hygienic Design: Removable structure for easy and thorough cleaning.
- Durability: Constructed with premium materials for prolonged service life.
- Overflow Prevention: Integrated level sensor for optimal production management.
- Simple Set-Up: External machine screws allow for quick assembly and disassembly.
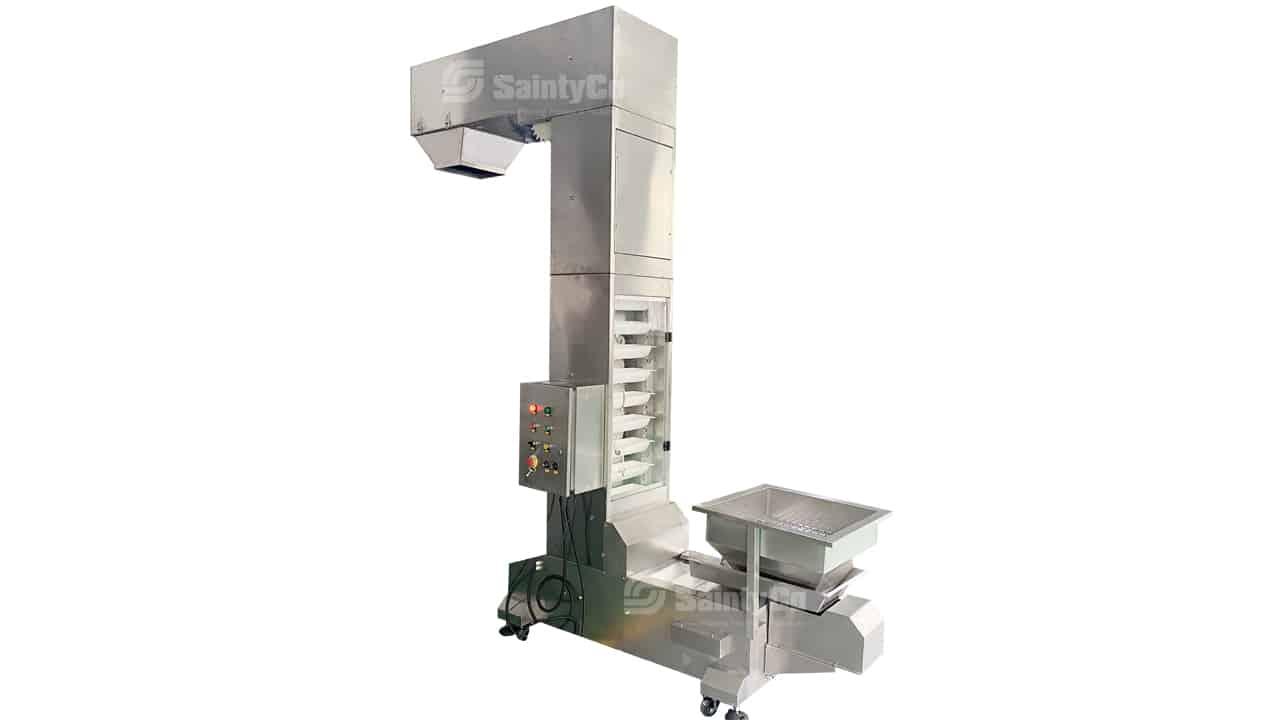
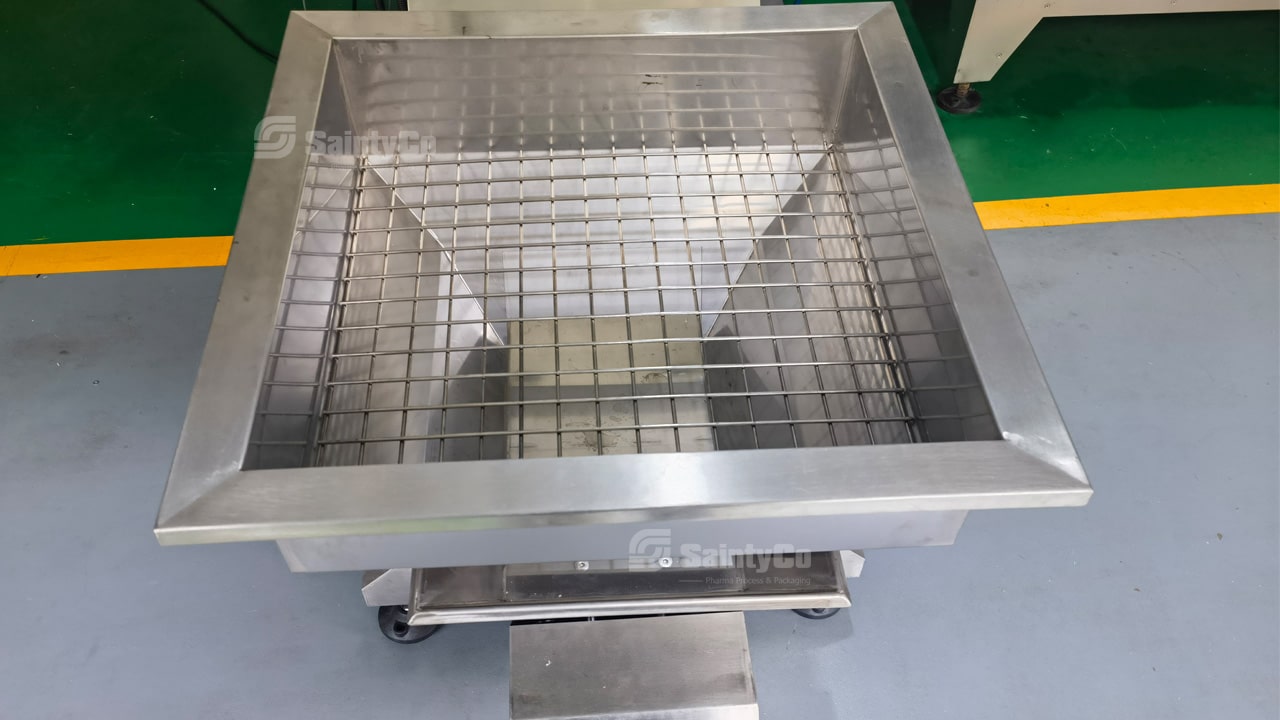
5. GummyCount 40 Bulk Counter:
- Purpose: Elevate gummy counting by overcoming the inherent challenges of their sticky nature, ensuring precise and efficient packaging.
- Key Features:
- Superior Material: Crafted from Stainless steel 316L for contact parts, ensuring durability and hygiene.
- Smart Control: User-friendly PLC & Touch Screen Control Panel for effortless operation.
- Multi-Functional: Not limited to gummies; also counts softgels, capsules, tablets, and candies.
- Precision Counting: Advanced three-stage vibration system guarantees accurate counts every time.
- User-Centric Design: Features like product memory and error message display enhance user experience.
- Safety Assured: The “No bottle, no fill” mechanism prevents wastage and potential mess.
- Maintenance-Friendly: Tool-free dismantling and anti-stick Teflon coated channels ensure easy cleaning and upkeep.
- High Throughput: A robust feeding hopper and an output rate of 40-50 pouches/min cater to high-volume needs.
- Counting Precision: Emphasizes counting gummies instead of weighing them, guaranteeing the correct number in each serving.
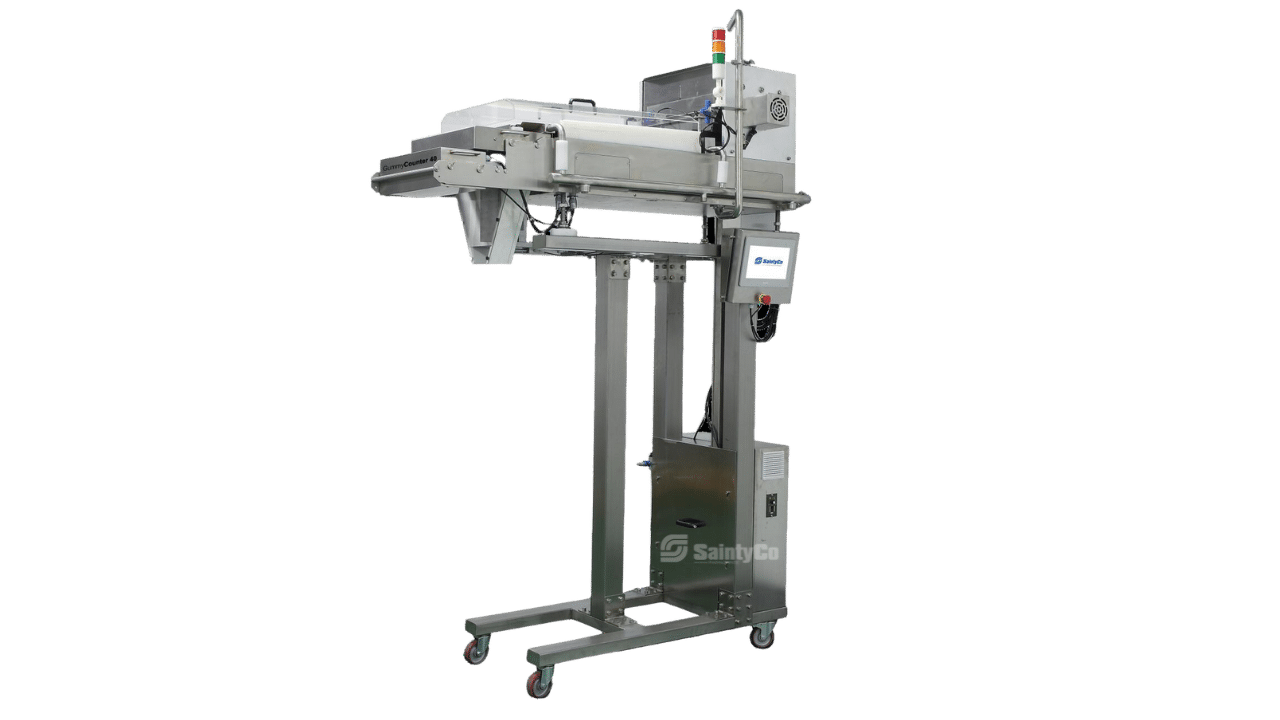

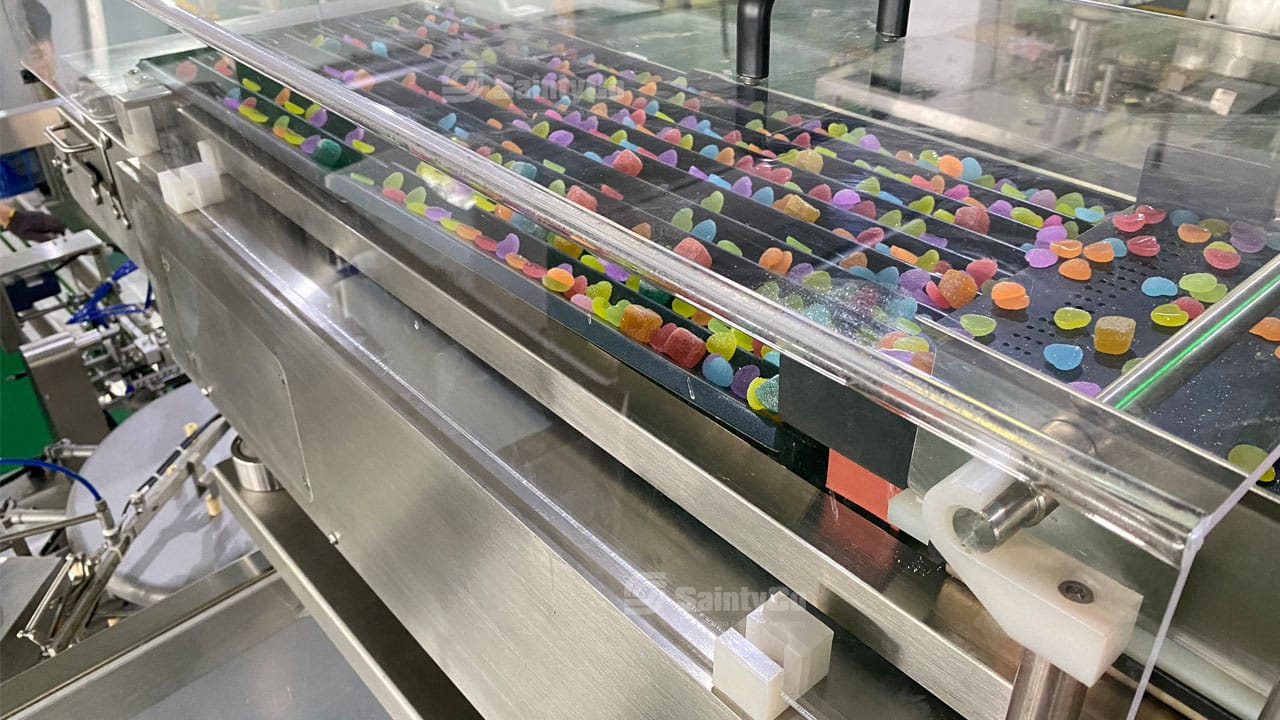

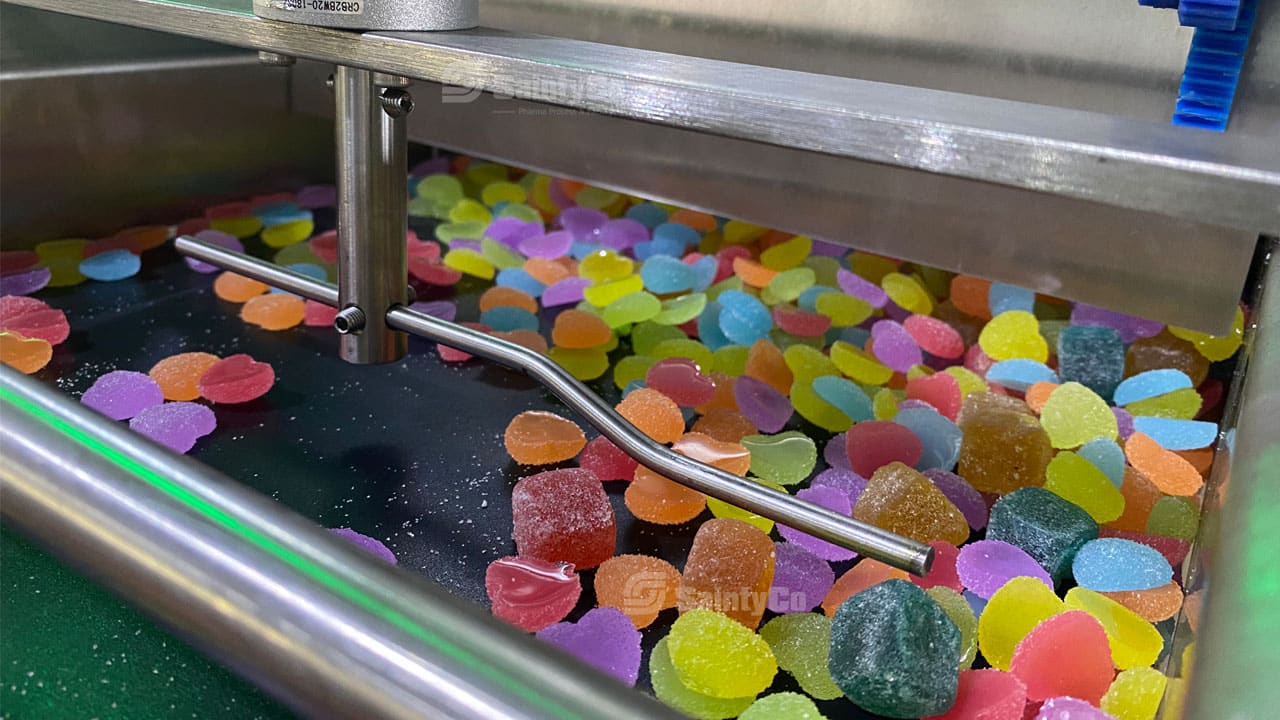
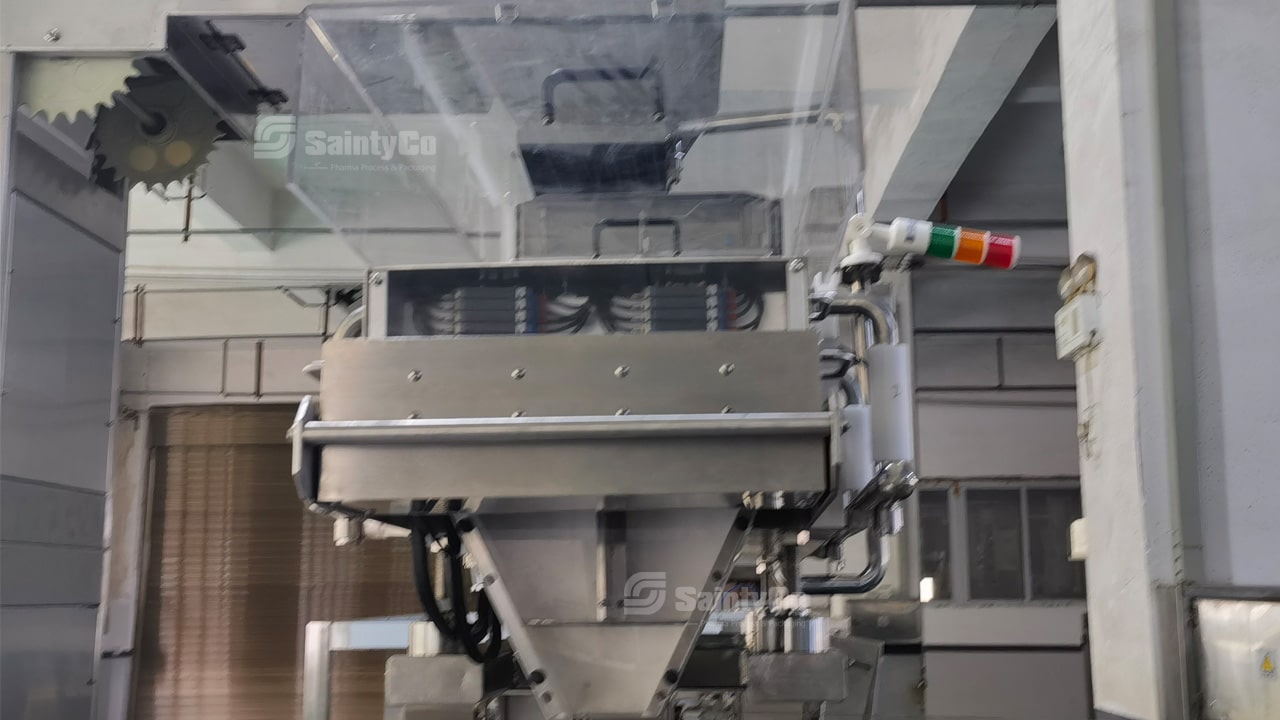
6. Ultra-8 Premade Pouch Filling Machine with Code Printing:
Purpose: Designed to automate the filling process, ensuring precision pouch placement and consistent filling for both solid and liquid products, complemented by accurate code printing.
Key Features:
- Integration: Compatible with multiple fillers like Multi-Head Weigher, Auger Filler, and Liquid & Paste Pump.
- Optimized Performance: With 8 operational stations, the rotary machine processes up to 35 to 60 pouches per minute.
- User-Friendly Operation: PLC with a 7” color HMI touch screen for easy adjustments and fault indications.
- Precision: Indexing gearbox for accuracy and a “Schneider” frequency inverter for stability.
- Safety: Features like ‘No pouch – No fill – No seal’ and heater disconnection alarm. Safety doors with interlocking system.
- Construction & Hygiene: Made of #304 Stainless Steel with an Omron P.I.D. temperature controller.
- Power: 220V 3-phase, 60 Hz.
- Integrated Code Printing: Facilitates real-time date and batch coding, ensuring traceability and compliance.
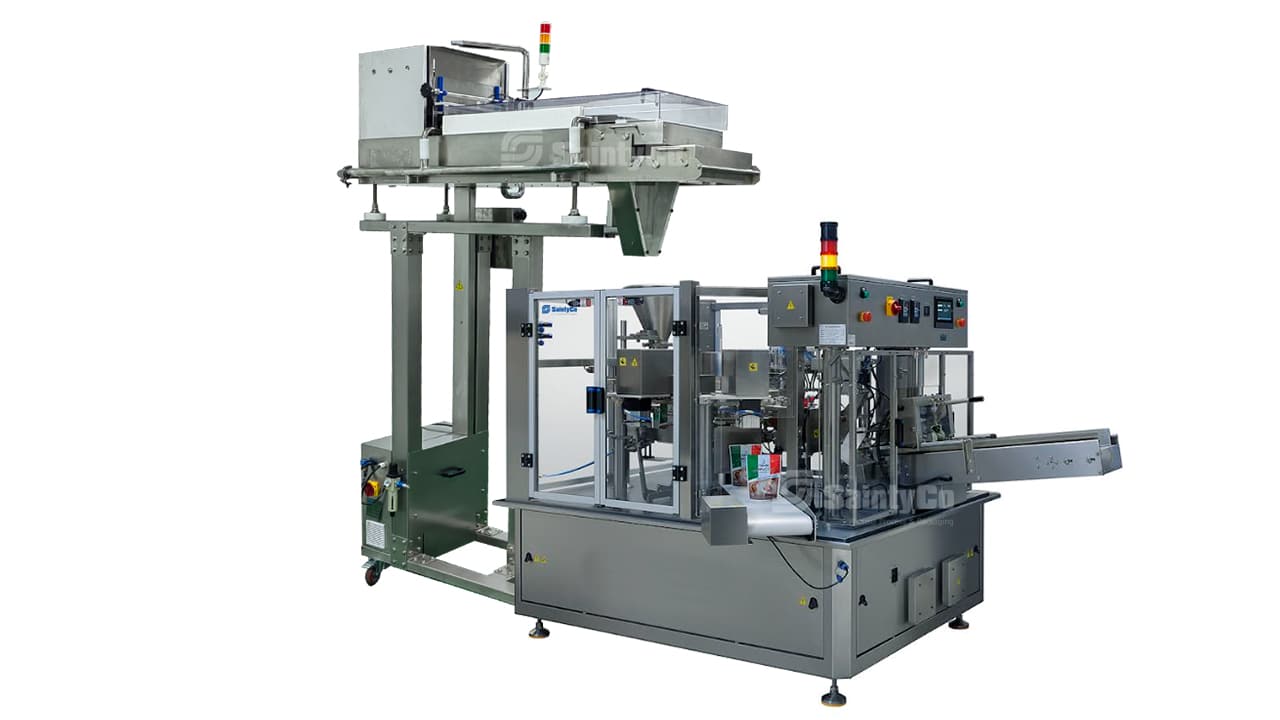
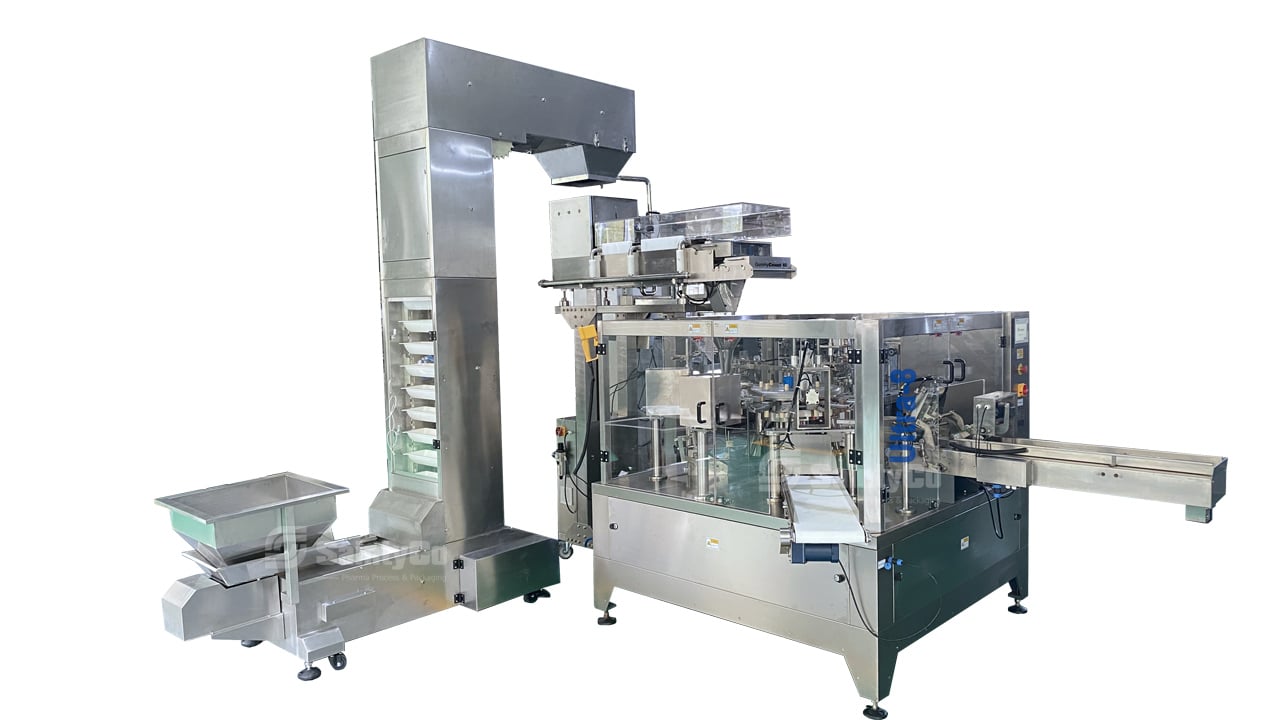
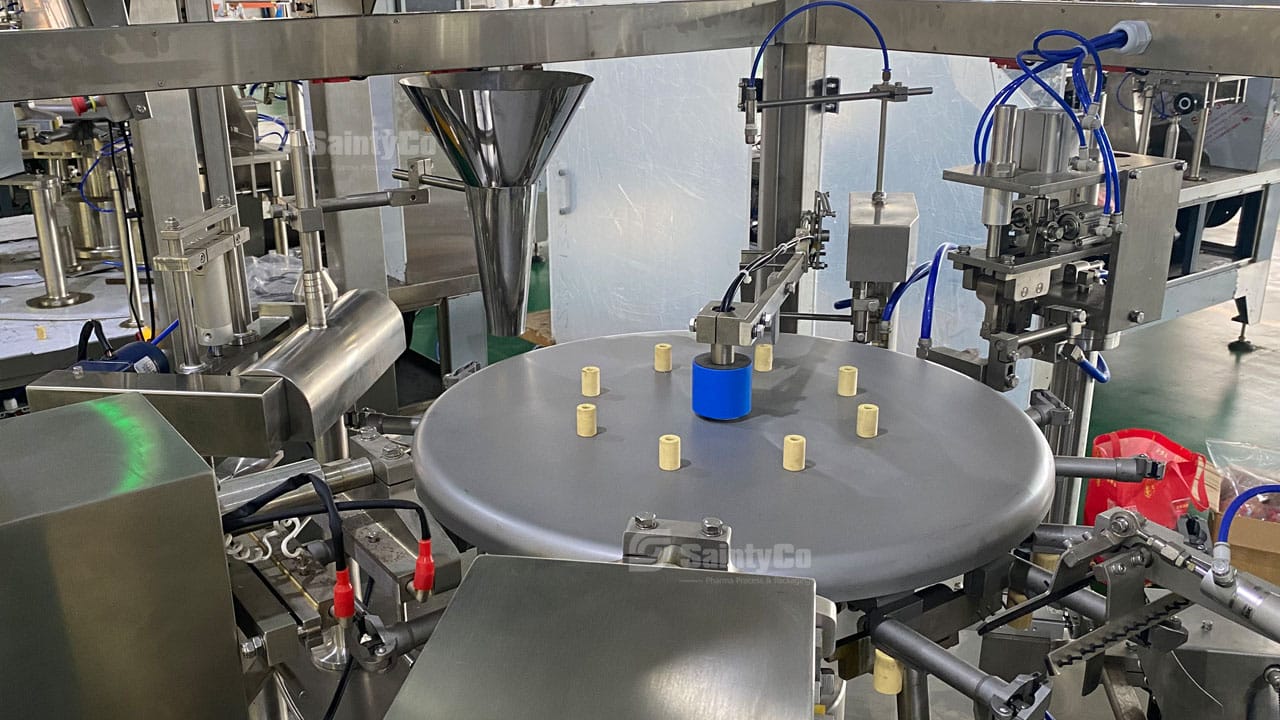
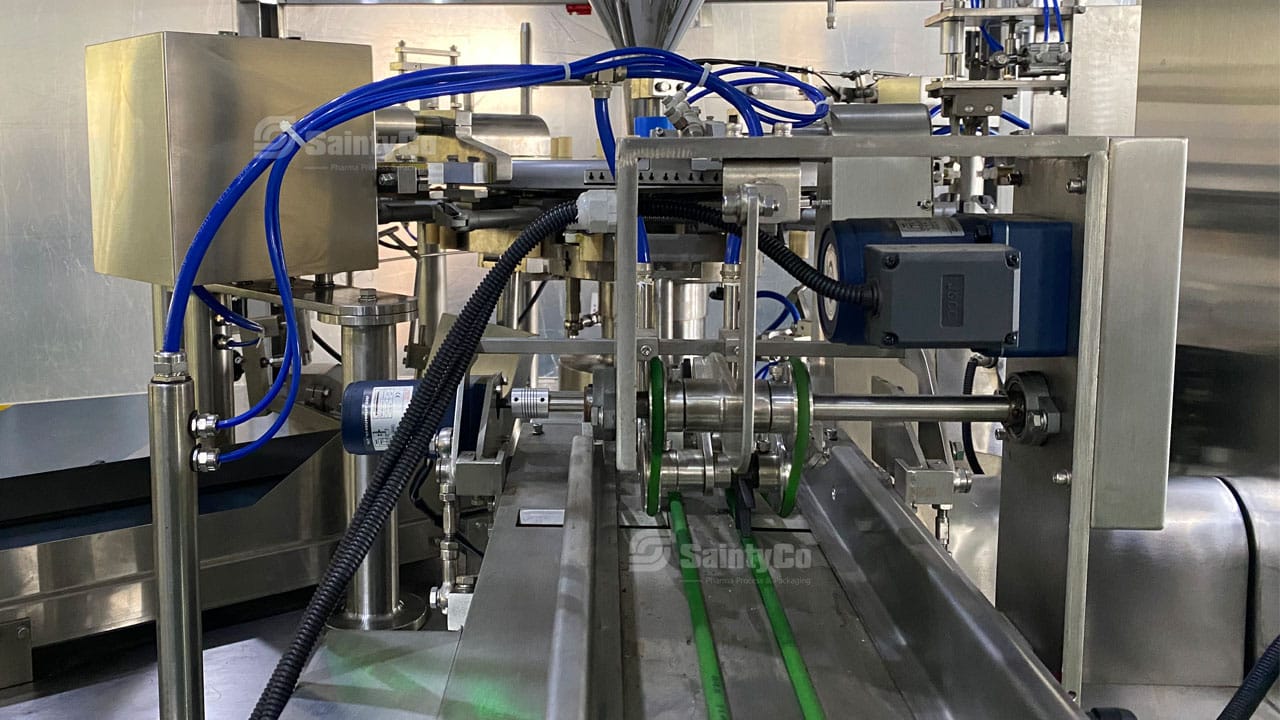
3. Tailored Production Layout
Given Mr. Martin’s facility constraints and the G150 production line’s length of 16 meters, we designed an L-shaped layout. This optimized space, material flow, and staff movement, with the cooking and CFA system on one side and the depositing processes on the other.
We also performed ‘batch testing’ using real ingredients to fine-tune machinery settings and validate gummy quality.
4. Streamlined Installation & Commissioning
On arrival, our US service team evaluated the site for power and air configurations. Once the equipment was unboxed and set up, Mr. Martin’s electronic technician connected the components. We then oversaw comprehensive tests to guarantee optimal functionality.
We also performed ‘batch testing’ using real ingredients to fine-tune machinery settings and validate gummy quality.
5. Comprehensive Training
We dedicated several days to hands-on training for Mr. Martin’s team, emphasizing:
- Startup Preparations: Readying raw materials and initiating operations.
- Active Production: Efficient real-time operations and troubleshooting techniques.
- Shutdown & Maintenance: Thorough post-production cleanup protocols to prolong machine lifespan.
Throughout, we emphasized the importance of adhering to Standard Operating Procedures (SOPs) for consistent output.
6. Responsive Technical Support
Minor glitches can have significant impacts. A case in point: when a rotor pump faced an interruption, we initiated a video session within an hour. Our skilled technician walked Mr. Martin’s team through the cleaning, reassembly of the rotor pump, and the subsequent Variable Frequency Drive (VFD) reprogramming. Our rapid response ensured minimal downtime and maintained a steady production flow.
7. Regulatory Assurance
SaintyCo’s machinery meets international standards, including FDA, cGMP, GMP, and ISO 9001. This ensures that gummy manufacturers in the CBD sector consistently meet high-quality benchmarks.
Results: Amplified Production, Enhanced Profitability, and Strengthened Partnerships
Through strategic collaboration with GummyGenix by SaintyCo, Mr. Martin’s business saw remarkable growth. Production capabilities expanded, reaching an output of 50,000 gummies per hour. This efficiency led to a milestone: a significant order of 2 million gummies for a well-known global retailer.
By the end of the fiscal year, profit margins increased by a notable 25%. Operational processes improved by 15%, and the product range diversified with the introduction of five new lines. Collaborative efforts also bore fruit, resulting in partnerships with over ten leading domestic wholesalers and retailers.
In terms of regulatory compliance, the business achieved excellence, securing top scores in FDA and cGMP evaluations. Feedback post-engagement reflected a renewed trust in our expertise and machinery. These achievements not only validate our initial project goals but also emphasize our commitment to our clients’ success in the gummy manufacturing industry.
What Our Clients Say:
Starting with the DM-20S and transitioning to the G150, our partnership with GummyGenix by SaintyCo has consistently elevated our operations. In the dynamic world of gummy production, the right partner is invaluable. With GummyGenix, we've not only met our immediate objectives but have set our sights on a brighter future. Their expertise and reliable support have been helpful, and we're eager to continue pushing the boundaries together. Beyond just supplying machinery, GummyGenix empowered us with essential knowledge and connected us with key industry contacts. Their total support, clear communication, and expertise have been instrumental in the success of our gummies. With GummyGenix, it wasn't merely a supplier-client relationship; it felt like a genuine partnership, with both parties invested in mutual success.
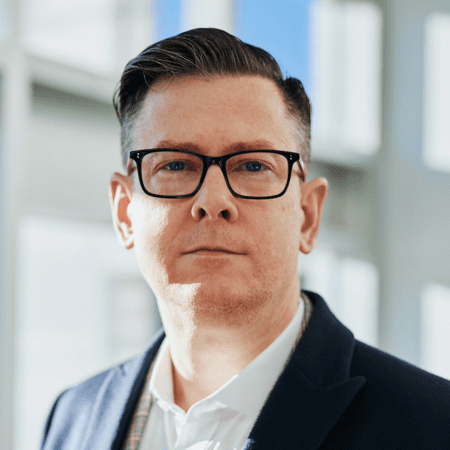
Facing challenges in scaling your gummy production? We understand what you’re going through. Let’s schedule a free consultation today >
GummyGenix, a dynamic arm of SaintyCo International Group, leverages its parent company’s pharmaceutical machinery expertise to provide cutting-edge automated gummy production and packaging solutions worldwide, tailored for the confectionery, cannabis, and nutraceutical industries. Our genuine commitment lies in helping you to be more successful.
From compact R&D gummy depositor units to versatile gummy production lines covering kitchen setups and packaging machinery for finished gummies, our solutions are designed to save time and resources, boosting your profitability.
Our value goes beyond machinery. We offer comprehensive support, including customized gummy formulations, facility layout design, manufacturing operations, and training. With two decades of partnership-building, we are dedicated to bringing innovation, one-stop solutions, and proactive customer service to you. Schedule a call to learn more.
Let's start the conversation
How can we help you succeed?
Partnering with GummyGenix, you will benefit from:
Expertise: Over 20 years in confectionery and pharmaceutical machinery design.
Custom Solutions: Tailored, cost-effective gummy machinery solutions.
Support: Financing, custom gummy formula, facility layout design, SOP optimization, installment, training, and more reliable after-sales service.
Productivity: Seamless operations for peak productivity.