The gummy industry is highly competitive, and staying ahead means keeping up with the latest technology. Are your gummy production machines holding you back? Discover the signs that it's time to upgrade your gummy making equipment to ensure quality and efficiency in your production process.
If your gummy making equipment is leading to slow production speeds, inconsistent product quality, or frequent maintenance issues, it indicates that it’s time for an upgrade. Upgrading modern, efficient machinery can significantly enhance your production capacity and product consistency, helping you stay competitive.
Upgrading your equipment is an investment that can transform your business.
Key Upgrade Signs to Watch for
1. Slow Production Speeds
Struggling to meet production deadlines because your equipment can't keep up? This stresses your team and risks your reputation with clients expecting timely deliveries. Slow production times cause inventory issues and disappoint retail partners. Upgrading to faster, more efficient equipment can drastically improve your output, allowing you to meet demand and keep your customers happy.
Upgrading to high-speed depositing systems can massively cut the time needed to fill gummy molds. For instance, a servo-driven depositor can ramp up throughput while maintaining tight control over gummy weight and shape, ensuring each batch is consistent and high-quality. In addition, modern automated systems integrated with ERP software provide real-time monitoring and control, reducing manual interventions and improving production accuracy.
.
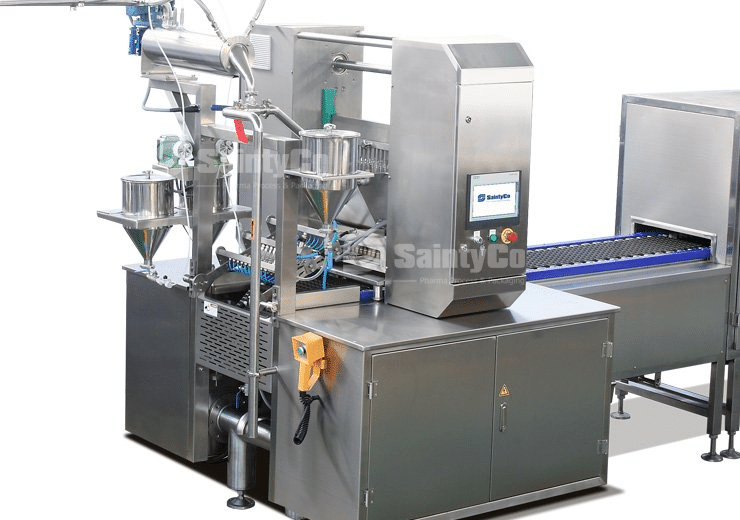
.
2. Inconsistent Product Quality
Consistency is everything in the gummy business. Customers who buy your gummies expect the same texture, taste, and look every time. Variations can lead to disappointment and lost business. If you see product inconsistencies, your machinery isn’t performing as it should. Upgrading to advanced machinery ensures uniformity in every batch, maintaining your brand’s reputation for excellence. Newer tech provides precise control over the entire process, ensuring consistent quality.
Using precision molds and accurate temperature control during cooking and cooling stages can prevent texture variations. Advanced gummy production line with integrated temperature sensors guarantees that the gelatin mixture is cooked and set at the optimal temperatures.
.
3. Limited Batch Sizes
To scale your gummy production, you need the ability to handle larger batch sizes. If your current setup can't produce the desired volume, it's time to upgrade. Modern equipment can handle larger batches efficiently, allowing you to scale up production to meet increasing demand.
Consider upgrading to larger mixing and cooking systems that handle higher volumes of ingredients. These systems, along with high-capacity storage tanks for gelatin and other raw materials, can streamline your production process and reduce downtime between batches.
.
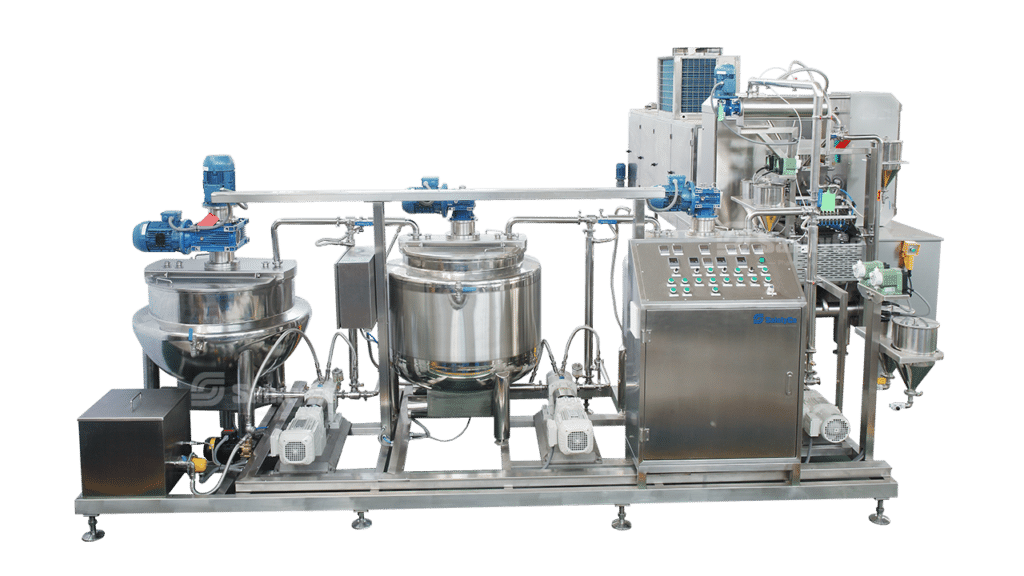
.
4. Frequent Maintenance Issues
Constant machinery breakdowns are a production nightmare, disrupting schedules and hiking up costs. If your team spends more time fixing machines than making gummies, it's a sign you need to upgrade your gummy equipment. Modern gummy processing equipment is more reliable and requires less maintenance, ensuring smoother operations and reducing unexpected downtime. Predictive maintenance features in new equipment help anticipate issues before they cause breakdowns.
Implementing a computerized maintenance management system (CMMS) can track equipment conditions and schedule preventive maintenance, extending your machinery’s lifespan and avoiding unexpected breakdowns.
.
5. Increased Rejection Rates
High rejection rates are a red flag, wasting resources and pointing to deeper issues. If you’re frequently discarding batches, it’s time for an upgrade. Up-to-date machinery offers better precision and control, reducing rejects and ensuring more products meet quality standards. This leads to cost savings and higher customer satisfaction.
Inline quality control systems, like automated vision inspection, can catch defects early, ensuring only high-quality gummies make it to packaging.
.
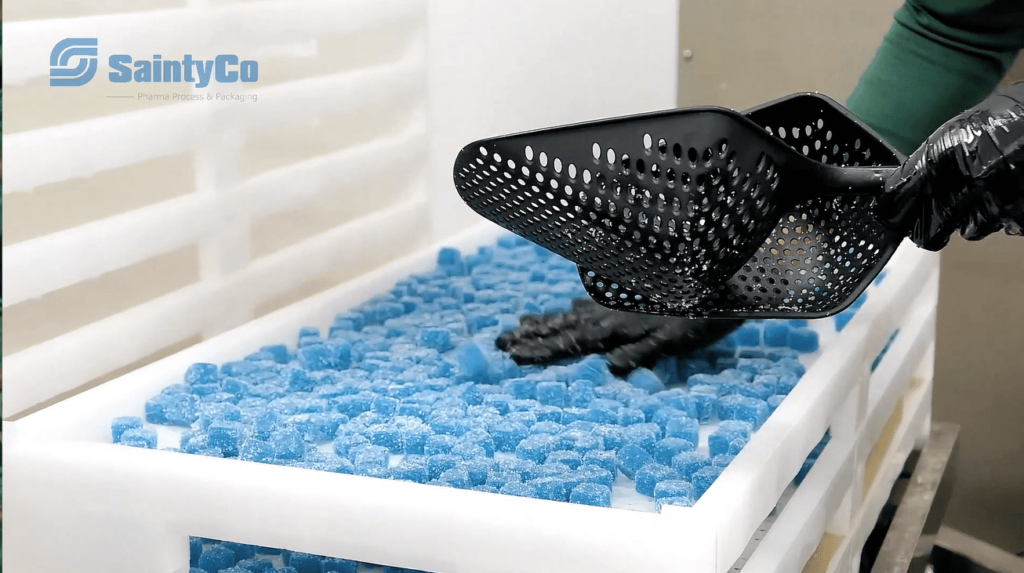
.
6. Outdated Technology
The gummy manufacturing industry continually evolves with new technologies that enhance efficiency and product quality. Sticking with old tech can put you at a competitive disadvantage. Modern gummy machinery includes features like automated controls, improved energy efficiency, and better integration with digital monitoring systems. Upgrading your technology boosts production efficiency and opens up new possibilities for product innovation and market expansion.
Industry 4.0 technologies, such as IoT-enabled sensors, provide real-time performance and production metrics data, allowing better decision-making and process optimization for gummy manufacturing.
.
7. Regulatory Compliance Challenges
Keeping up with industry standards is crucial for credibility and avoiding legal trouble. If your equipment struggles with compliance, it’s time for an upgrade. Newer machinery meets stringent safety and quality standards, ensuring smooth certification processes and reducing non-compliance risks. Compliance with certifications like ISO 9001:2015, CE, and FDA can facilitate market expansion.
Modern gummy equipment for manufacturing often includes built-in compliance features, such as hygienic design elements that meet GMP standards, reducing contamination risks and ensuring product safety.
.
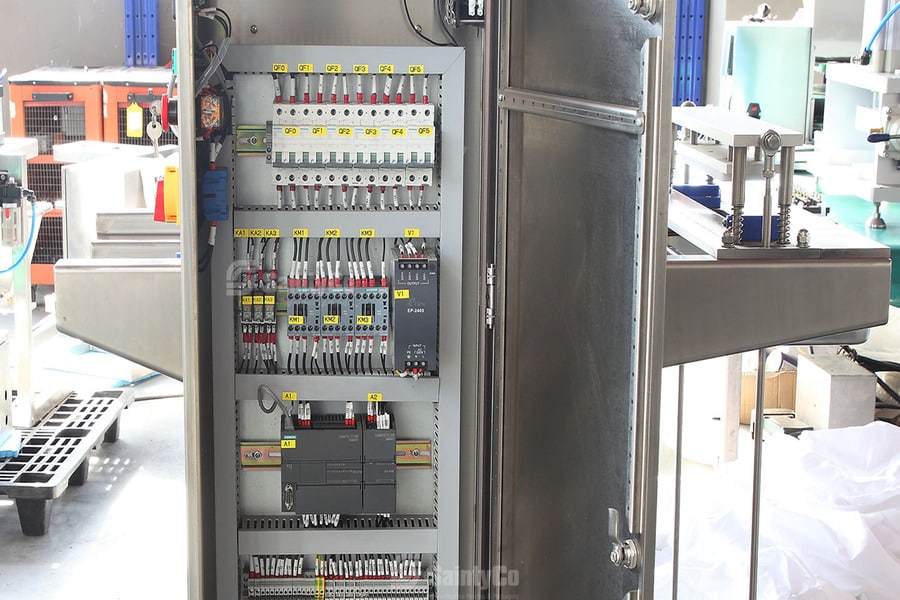
.
8. Hard-to-Source Components
If sourcing parts for your current gummy machines is getting tougher and more expensive, it's a sign your machinery is nearing the end of its lifecycle. Consider a control cabinet upgrade or new gummy processing equipment to avoid these sourcing issues and extend your equipment’s life.
Upgrading to machinery from reputable manufacturers with extensive parts support and after-sales service can prevent production delays due to component shortages.
.
9. Safety Concerns
The safety of your gummy-making equipment is crucial. If your machinery fails safety audits or lacks essential features, it’s time to upgrade. Look for gummy equipment with advanced safety features. The most common areas we see requiring attention (and where upgrades are available) are:
- Light curtain
- Safety Sensors on all doors
- Explosion relief valves
- Explosion prevention measures
- Mechanical guarding
- Automatic shut-off mechanisms
- Emergency stop buttons
.
10. Demand Outstrips Supply
As the gummy market grows, your production must keep pace. If you can’t meet customer demand, consider upgrading. New gummy production lines or servo upgrades can increase your manufacturing output and efficiency, ensuring you meet market demands without compromising on quality. This investment can help you capture more market share and grow sustainably.
Scalable solutions, like modular production lines, allow you to expand capacity incrementally, matching growth with demand without over-investing upfront.
.
11. Draining Resources
Older equipment often needs more human resources to function your gummy processing machinery. Modern gummy-making machinery requires minimal supervision and can run independently, freeing up staff for other tasks. Upgrading reduces labor costs and improves efficiency, allowing better resource allocation and productivity.
.
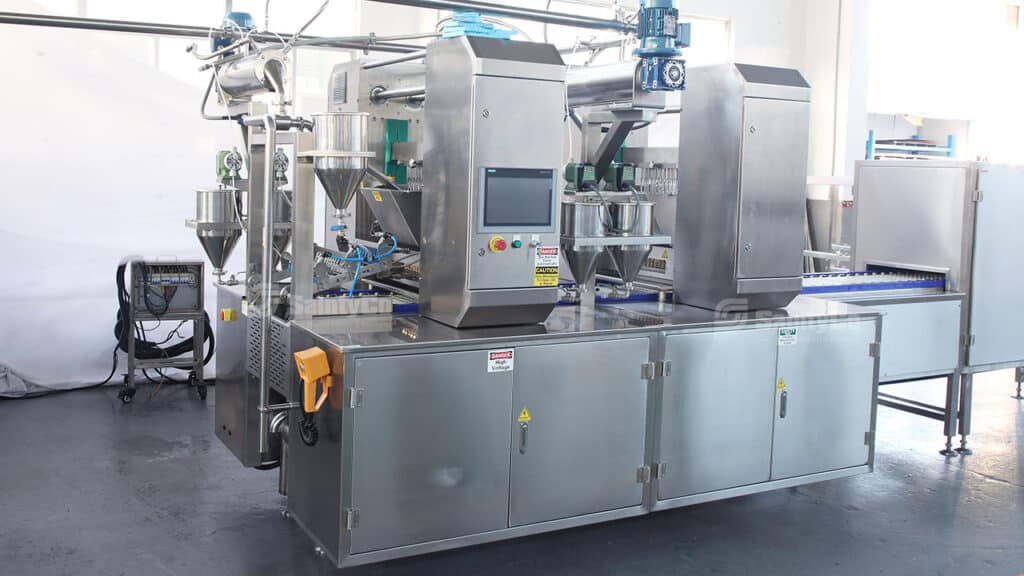
.
12. Production Flexibility
In today’s market, the ability to produce a variety of gummy shapes, sizes, and colors is crucial. With the rising demand for alternatives like vegan gummies, your equipment must be flexible. Plant-based substitutes have different melting and freezing points than gelatin, which can impact quality if your machinery can't adapt. If your current equipment limits your production options, it’s time to upgrade.
Modern starchless molding technology offers the versatility to produce diverse recipes, including center-fill or layered gummies. This adaptability helps you cater to various consumer preferences and stay ahead of trends.
Utilizing multi-head depositor systems adds visual appeal, making your gummies more attractive and expanding your product range.
.
.
Staying competitive in the gummy industry requires continuous improvement and modernization of your production line. Upgrading your gummy making equipment can lead to higher production speeds, better product quality, fewer maintenance issues, and compliance with industry standards. Invest in quality gummy machines to secure your place in the market.
For a top gummy processing equipment manufacturer and supplier, contact GummyGenix by SaintyCo.
.
Why Choose SaintyCo?
SaintyCo specializes in providing expert automated systems for gummy production tailored to startups, retailers, and large manufacturers globally.
.
Our Gummy Machines’ Advantages:
- High Efficiency: Production lines with capacities from 6,000 to 240,000 gummies per hour.
- Advanced Technology: Our machines, featuring servo-driven systems, accurate temperature control, and hygienic designs, ensure reliable and consistent production.
- Versatile Equipment: Our equipment is suitable for producing CBD, THC, vitamin gummies, and more, meeting diverse manufacturing needs.
.
Customer-Centric Approach
We focus on understanding and addressing our clients’ pain points, such as reducing production costs, improving production speed and accuracy, and ensuring high-quality output with minimal waste.
.
Compliance
Our gummy machinery complies with international standards, including cGMP, ISO 9001:2015, CE Electrical Certification, and FDA Quality Standards. It is perfect for pharmaceutical-grade, high-precision production. These features enable you to streamline your production process, save labor, and maintain high hygiene standards.
.
Global Support
SaintyCo provides global sales support and after-sales service to ensure smooth operation and maintenance of your equipment.
.
For more information, reach out to [email protected]