Are you looking to streamline your gummy production process?
To optimize the layout and integration of different gummy making machines, consider configuring your production line in a straight line or L-shape to maximize space efficiency. Focus on modular setups that simplify connections between machines, ultimately enhancing productivity.
This blog delves deeper into the best practices for layout design, machine compatibility, and operational efficiency in gummy manufacturing. Keep reading to uncover strategies that can elevate your production process.
Straight line layouts enhance gummy production efficiency.True
Configuring machines in a straight line maximizes space and workflow, leading to improved productivity in gummy manufacturing.
Modular setups complicate machine connections.False
Modular setups actually simplify connections between machines, making the production process more efficient, not complicated.
What are the key considerations for designing an efficient gummy production line?
Designing an efficient gummy production line involves multiple critical considerations that ensure high-quality output while maintaining productivity. Let's explore these key factors.
Key considerations for designing an efficient gummy production line include selecting appropriate machinery, optimizing workflow layout, ensuring safety compliance, improving energy efficiency, maximizing space utilization, and providing comprehensive staff training.
Equipment Selection
Selecting the right machinery is crucial for a gummy production line. Key equipment includes cookers, depositors, cooling tunnels, and coaters. Each piece must be compatible and efficient.
For example, consider the cooker’s capacity to handle your batch size. A well-sized cooker can significantly reduce cooking time and improve consistency. This can lead to higher quality gummies and reduced waste.
Workflow Optimization
Optimizing the layout is essential to ensure smooth operations. A linear or L-shaped configuration may be ideal depending on your facility’s dimensions. The goal is to minimize movement and streamline the process.
A well-planned workflow can prevent bottlenecks and ensure each stage flows seamlessly into the next. Learn more about optimizing workflows1.
Safety Standards
Compliance with safety regulations is non-negotiable. Ensuring that machinery meets safety standards protects your workers and your business. Regular maintenance checks and employee training can prevent accidents and maintain production efficiency.
Energy Efficiency
Investing in energy-efficient equipment can lower operational costs over time. Look for machines that have energy-saving modes or that utilize less energy during production cycles. Implementing energy management systems can also track usage and identify areas for improvement.
Consideration | Description |
---|---|
Equipment Selection | Choose suitable machinery for efficiency |
Workflow Optimization | Design layout to minimize movement |
Safety Standards | Adhere to regulations for worker safety |
Energy Efficiency | Invest in machines that save energy |
Space Utilization
Maximizing your production area is vital. Utilizing vertical space with stacked machinery or overhead conveyors can free up floor space, allowing for more equipment or easier movement around the facility. Explore more on space optimization techniques2.
Training and Support
Finally, continuous training of staff on equipment usage and safety protocols enhances productivity. Providing resources and support will ensure your team operates efficiently, reducing downtime and errors.
In summary, focusing on equipment selection, workflow optimization, safety compliance, energy efficiency, space utilization, and training will ensure your gummy production line operates at peak efficiency. Proper planning in these areas can lead to significant improvements in productivity and profitability.
Choosing suitable machinery boosts gummy production efficiency.True
Selecting the right equipment is essential for maximizing productivity and ensuring high-quality gummies.
Energy-efficient machines increase operational costs in production.False
Investing in energy-saving equipment can significantly lower long-term operational costs, benefiting production budgets.
How does machine integration impact production speed and quality?
Machine integration significantly influences production speed and quality in manufacturing. By connecting various machinery, manufacturers can streamline processes and enhance output effectiveness.
Machine integration impacts production speed by enabling seamless workflows and reducing manual handling. It also enhances quality through automation, minimizing errors and ensuring consistent product standards.
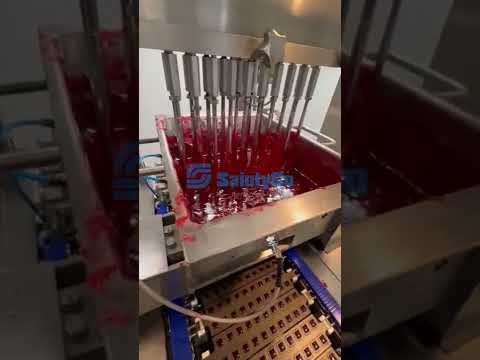
Real production scenario in our client's facility in Denver. SaintyCo G80 gummy production with 30,000 gummy per hr | L type in a limited space! Flexible layout!
The Role of Machine Integration in Enhancing Production Speed
Machine integration refers to the seamless connection of various equipment and technologies within a manufacturing process. By linking machines like depositors, cookers, and cooling tunnels, production lines operate more efficiently.
When machines are integrated, it minimizes manual interventions, reducing the time needed for product transfers. For example, using conveyor systems to connect machines ensures that gummy products move swiftly from one stage to another without delays. This streamlined process significantly boosts overall production speed, allowing businesses to meet demand faster.
Additionally, integrated systems enable real-time monitoring of operations. Data collected from machines can be analyzed to identify bottlenecks, leading to improvements in workflow. Companies that implement these systems often report a notable decrease in cycle times and an increase in throughput. To learn more about optimizing production line layouts, check out optimal layouts3.
Improving Quality Through Automation
The integration of machines not only speeds up production but also enhances product quality. Automated processes reduce human error, which can lead to inconsistencies in gummy production. By employing advanced machinery equipped with precise controls, manufacturers ensure that each batch of gummies meets specific standards.
Moreover, integrated machines often include quality control features that inspect products in real-time. For instance, cooling tunnels can be monitored for temperature consistency, ensuring that gummies set correctly and retain their intended texture. This proactive quality management leads to fewer defects and higher customer satisfaction.
The table below illustrates the impact of machine integration on production speed and quality:
Impact Area | Before Integration | After Integration |
---|---|---|
Production Speed | Slower due to manual handling | Faster with automated transfers |
Quality Consistency | Variability in batches | Higher consistency due to automation |
Error Rate | Higher due to human intervention | Lower with automated checks |
Monitoring Capability | Limited | Real-time analytics available |
For deeper insights on how automation affects manufacturing processes, explore automation benefits4.
Challenges and Considerations
While the advantages are compelling, integrating machines also comes with challenges. Initial setup costs can be significant, and companies must ensure that existing infrastructure supports new technologies. Moreover, staff training is essential to maximize the potential of automated systems.
A well-planned integration strategy can mitigate these challenges. Investing in staff education on new machinery can lead to a smoother transition and enhance overall productivity. It's crucial for decision-makers to weigh the costs against the long-term benefits of improved speed and quality.
In summary, machine integration plays a pivotal role in enhancing both production speed and quality within manufacturing environments. By carefully considering layout designs and training, businesses can harness the full potential of automated systems.
Machine integration reduces production cycle times significantly.True
Integrating machines minimizes manual interventions, leading to faster product transfers and reduced cycle times in manufacturing processes.
Automated systems increase human error in production.False
Contrary to this claim, automation reduces human error by streamlining processes and enhancing consistency in manufacturing operations.
What common challenges do gummy manufacturers face when optimizing layouts?
Gummy manufacturers encounter a variety of challenges when optimizing their production layouts. Understanding these obstacles is crucial for enhancing efficiency and product quality.
Common challenges faced by gummy manufacturers when optimizing layouts include space utilization issues, equipment integration complexities, labor shortages, maintaining quality control, and communication gaps among staff.
Space Utilization Issues
One of the most significant challenges gummy manufacturers face is optimizing space utilization.
Production layouts often require careful planning to ensure that every square foot is used effectively.
For instance, a straight line layout may seem efficient, but it could lead to bottlenecks if not properly designed. Consider using an L-shape layout which can enhance workflow and reduce unnecessary movement.
A good approach is to evaluate your current layout5 regularly to identify potential inefficiencies.
Equipment Integration
Integrating various gummy-making machines like cookers, depositors, and cooling tunnels can be daunting.
Each piece of equipment must be strategically positioned to facilitate seamless operations. For example, ensuring that your cooling tunnel is placed after the depositors minimizes the risk of gummies sticking together.
Utilizing modular machinery can simplify this process, allowing for easy adjustments and modifications.
Investing in a versatile gummy production line will greatly aid in streamlining equipment placement6.
Labor Challenges
Labor shortages and high turnover rates pose additional challenges.
Manufacturers must design layouts that not only maximize efficiency but also make it easy for workers to operate the machinery. This can involve creating ergonomic workstations that enhance comfort and productivity.
Incorporating automation in certain areas of production can also alleviate labor issues, allowing human resources to focus on more critical tasks. Consider reviewing automation options7 for your production line.
Quality Control
Maintaining quality throughout the gummy manufacturing process is vital. The layout must support effective quality control measures.
For instance, positioning inspection stations at various points along the production line can help catch issues early, reducing waste and improving overall product quality.
Implementing a layout that facilitates easy access to quality control checkpoints will enhance compliance with regulatory standards. You might want to explore quality assurance strategies8 tailored for gummy production.
Communication Gaps
Lastly, communication gaps among staff can lead to errors in production.
Designing the layout to promote better communication is essential. For example, placing workstations closer together encourages teamwork and swift problem resolution.
Additionally, incorporating visual aids or digital monitoring systems can keep everyone informed about production status. This ensures that all team members are aligned on objectives and processes, ultimately leading to improved efficiency. To learn more about effective communication in manufacturing, check out best practices9.
Gummy manufacturers often struggle with space utilization.True
Space utilization is a key challenge for gummy manufacturers, impacting efficiency and workflow in production layouts.
Labor shortages do not affect gummy production efficiency.False
Labor shortages significantly impact gummy production, necessitating ergonomic designs and automation to enhance efficiency.
What role does equipment compatibility play in overall production efficiency?
Equipment compatibility is vital for optimizing production efficiency in manufacturing. Discover how it can streamline operations and improve overall effectiveness.
Equipment compatibility plays a crucial role in enhancing production efficiency by ensuring machines work together seamlessly, reducing downtime, and improving output quality.
Understanding Equipment Compatibility
Equipment compatibility is crucial in any production line, particularly in the gummy-making industry. When machines work together seamlessly, the entire process runs smoother, ensuring that production efficiency is maximized.
For instance, consider the integration of gummy cookers, depositors, cooling tunnels, and coaters. If these machines are designed to be compatible, they can be connected easily through pumps and pipelines or conveyors. This not only simplifies the setup but also reduces labor costs by minimizing the need for extensive manual adjustments.
The Impact on Production Efficiency
When all equipment is compatible, it leads to higher Overall Equipment Effectiveness (OEE). OEE is a metric that helps you understand how well your manufacturing operation is performing. It considers availability, performance efficiency, and quality rate. High compatibility can significantly improve these metrics.
Metric | Impact of Compatibility |
---|---|
Availability | Less downtime due to fewer machine breakdowns |
Performance | Machines running at optimal speeds |
Quality | Reduced defects from integrated systems |
By focusing on equipment compatibility, production managers can ensure that each part of the line supports the others. This holistic approach not only enhances efficiency but also contributes to better product quality.
Selecting Compatible Equipment
Choosing the right equipment involves more than just picking the best individual machines. It requires evaluating how well these machines will work together. Factors to consider include:
- Machine Specifications: Ensure that machines have matching capacities and dimensions.
- Technology: Look for machines that utilize similar technology for easier integration.
- Manufacturer Support: Opt for equipment from suppliers who can provide comprehensive support for integration.
Investing in compatible machinery may have an upfront cost but offers long-term savings by improving workflow and reducing delays. For example, integrating automated systems can streamline operations, leading to faster production times and better resource management. Explore more about equipment selection strategies10 to optimize your production line.
In summary, equipment compatibility plays a significant role in enhancing overall production efficiency. By ensuring that all machinery works harmoniously together, businesses can achieve optimal performance, reduce downtime, and improve product quality. Consider learning more about OEE metrics11 to dive deeper into enhancing your operational effectiveness.
Compatible machines reduce production downtime significantly.True
When machines are compatible, they require fewer adjustments, leading to less downtime and smoother operations.
High equipment compatibility guarantees better product quality.True
Seamless integration of compatible machines minimizes defects, ensuring higher quality in the final products.
Conclusion
Learn effective strategies for optimizing gummy production layouts and integrating machines to enhance efficiency, improve quality, and streamline operations in your manufacturing process.
At GummyGenix by SaintyCo, we're here to support your journey with cutting-edge, GMP-compliant gummy manufacturing equipment designed for efficiency, precision, and adaptability. Our machines are fully compatible with regulatory standards, and we offer reliable after-sales support to keep your operations running smoothly.
As a manufacturer and supplier of gummy manufacturing equipment, GummyGenix by SaintyCo brings extensive hands-on experience from working closely with gummy production facilities. This experience enables us to offer practical, tailored recommendations that fit your specific setup. Drawing from insights in both gummy production and machine manufacturing, our team provides layout suggestions that maximize efficiency—optimizing machine placement and streamlining production flow from raw materials to finished products, all within your available space.
We can also guide you in integrating essential utilities, such as power, air, water, and environmental controls, to ensure each machine’s utility requirements are met smoothly. Alongside complete support and consulting, we provide detailed specifications for each machine to help you prepare with precision.
For more information on optimizing your gummy manufacturing facility, feel free to reach out to GummyGenix by SaintyCo today.
Gummy Production Machinery from GummyGenix by SaintyCo | Click to Know More
-
This link offers insights into optimizing gummy production workflows, which can enhance efficiency in your manufacturing process. ↩
-
Explore techniques on utilizing space effectively in production facilities, a must-read for improving operational efficiency. ↩
-
Discover how machine integration can boost your production efficiency and maintain high product quality. ↩
-
Learn about the benefits of automating production lines for better efficiency and quality assurance. ↩
-
This link provides insights into the latest industry trends and solutions for layout optimization challenges. ↩
-
Find innovative strategies that can help improve equipment integration in gummy production lines. ↩
-
Discover how automation can solve labor challenges in gummy manufacturing and enhance productivity. ↩
-
Explore effective quality control measures tailored for gummy production environments. ↩
-
Learn about effective communication strategies to enhance teamwork in gummy manufacturing. ↩
-
Discover insights on equipment compatibility that can significantly boost your production efficiency. ↩
-
Discover insights on equipment compatibility that can significantly boost your production efficiency. ↩