How to Make Sour Gummy Candies?
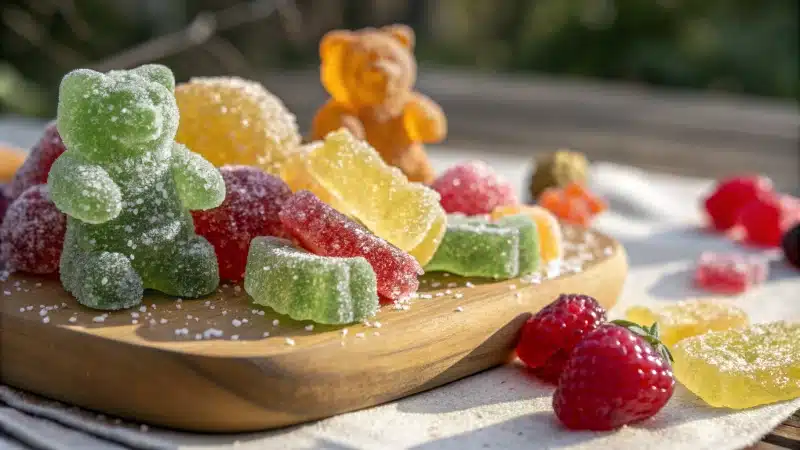
Learn expert tips for making sour gummies, focusing on ingredient balance, timing, and production techniques. Discover how to troubleshoot common issues and create delicious, consistent treats with automation.
How Many Operators for Your Gummy Production Line?
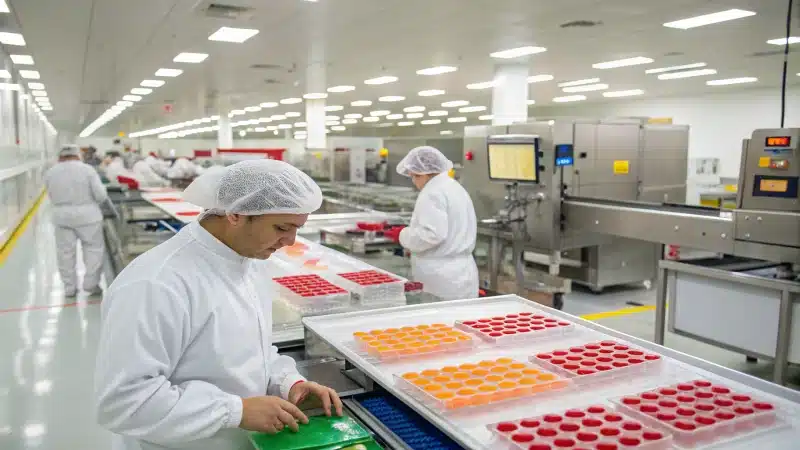
Optimizing gummy production requires understanding the ideal number of operators based on automation levels. Semi-automated lines need 2-3 operators, while fully automated setups require 3-4 for efficiency and quality control.
How Are Sour Gummy Worms Made: Which Production Method Is Best, Starch Mogul or Starchless Depositing?
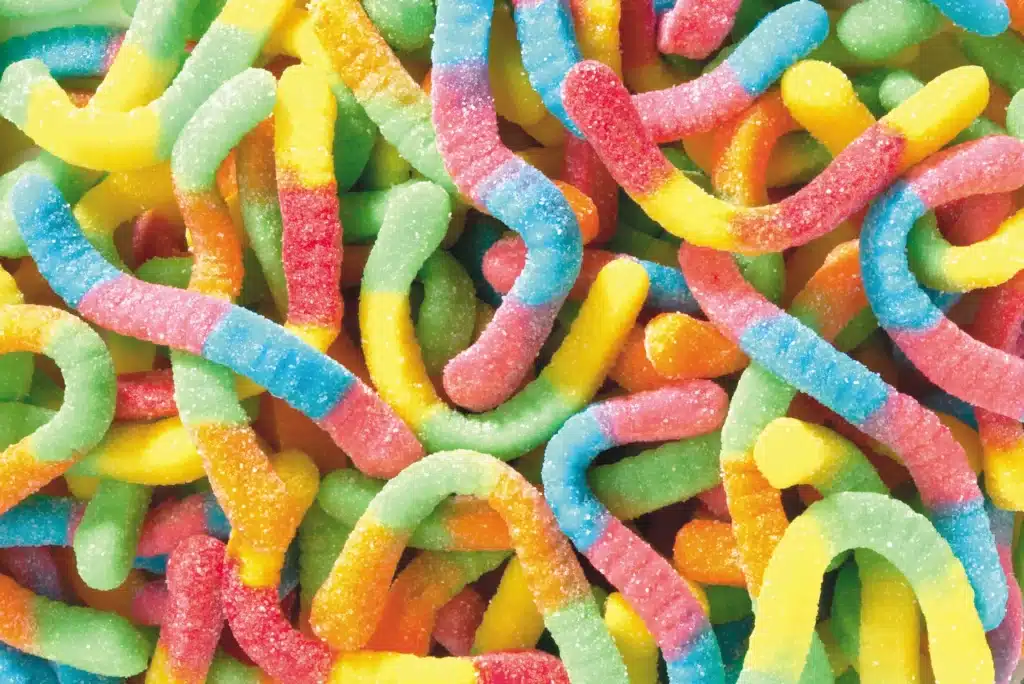
This blog post explores the production methods for sour gummy worms, comparing Mogul lines and starchless depositing. It highlights their advantages, challenges, and key considerations for manufacturers to make informed decisions.
How to Choose Small Gummy-Making Machines for Your Restaurant?
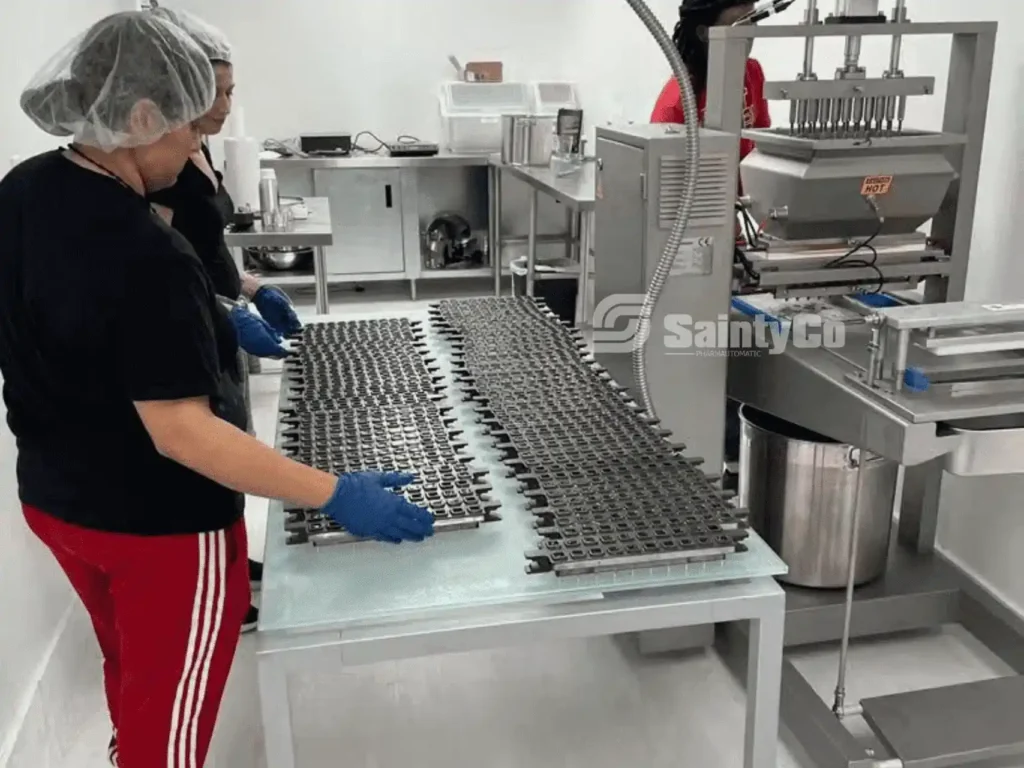
This ultimate guide helps restaurants choose the right small gummy-making machines by considering production volume, space, customization options, ease of use, budget, and after-sales support for optimal operations.
What Are the Steps to Set Up a Supplements & OTC Gummies Factory in Spain?
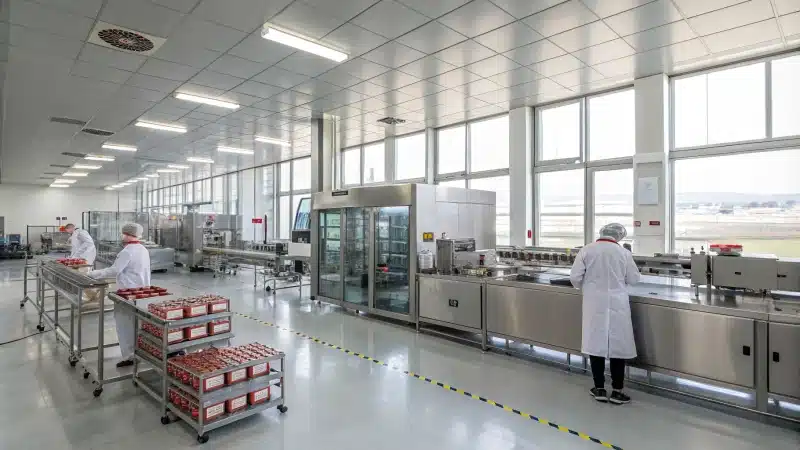
Establishing a supplements and OTC gummies factory in Spain involves navigating EU regulations, designing an efficient facility layout, selecting appropriate production equipment, and ensuring compliant formulations. Key steps include hiring regulatory consultants to ensure adherence to the EU Food Supplements Directive and implementing HACCP systems for food safety. A well-planned facility layout optimizes workflow while minimizing contamination risks. Essential equipment includes cooking vessels, gummy depositors, cooling tunnels, and packaging machines. Streamlining production processes through technology integration and continuous improvement fosters efficiency. Understanding market trends is crucial for product differentiation. Partnering with experienced providers can enhance setup success by offering tailored solutions for machinery selection and operational support.
How Do Gummy Bears and Energy Chews Differ in Their Production Process?
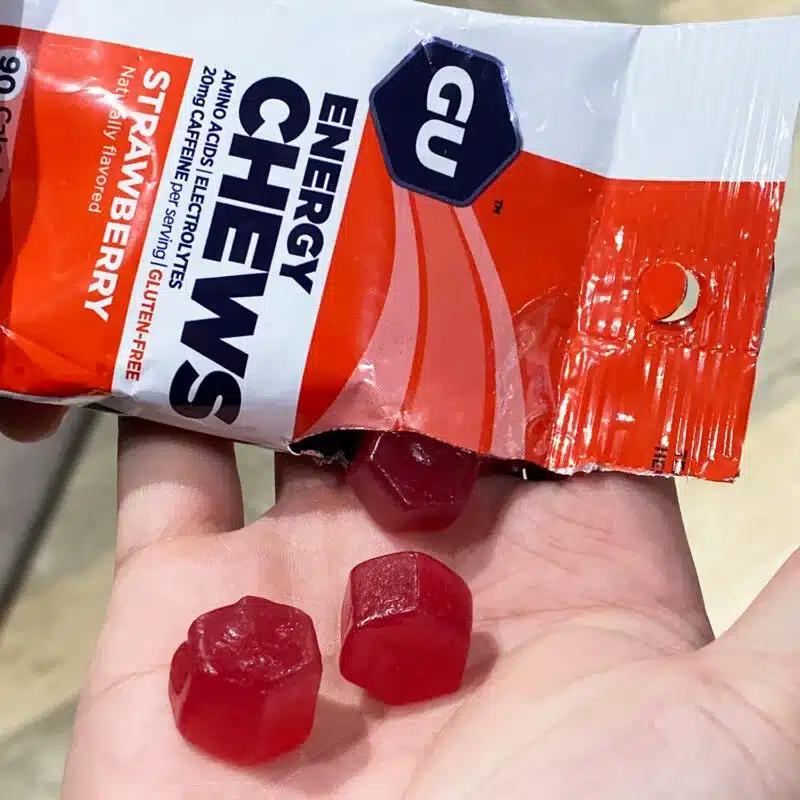
Gummy bears and energy chews are distinct in their manufacturing processes. Gummy bears use gelatin, sugar, and corn syrup, focusing on taste and texture. In contrast, energy chews incorporate active ingredients like caffeine or vitamins for performance enhancement. This leads to variations in cooking temperatures—gummy bears require high heat while energy chews are processed at lower temperatures to preserve sensitive components. Molding techniques also differ; gummy bears are molded using cornstarch molds while energy chews are pressed into shape. Understanding these differences is vital for manufacturers aiming to optimize production efficiency and meet consumer expectations.
What Production Equipment is Essential for Making Energy Gummies for Running?
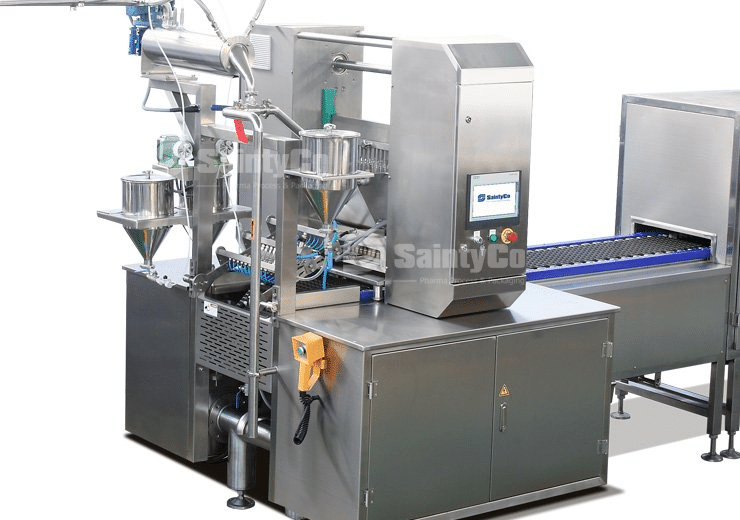
To successfully produce energy gummies for runners, manufacturers need essential equipment such as precision dosing systems for accurate ingredient incorporation, multi-hopper integration for complex formulations, and high-shear mixing to maintain consistent potency. These technologies enhance production efficiency while ensuring that each gummy is packed with performance-enhancing ingredients. Precision dosing minimizes waste and ensures compliance with regulatory standards by maintaining accurate ingredient levels. Multi-hopper systems allow simultaneous addition of various active ingredients, supporting complex formulations tailored to athletes’ needs. High-shear mixing guarantees uniform texture and flavor distribution across batches. Understanding these key components can help manufacturers create high-quality energy gummies that meet the demands of health-conscious consumers.
How Are Creatine Gummies Made and Which Machines Ensure the Best Production?
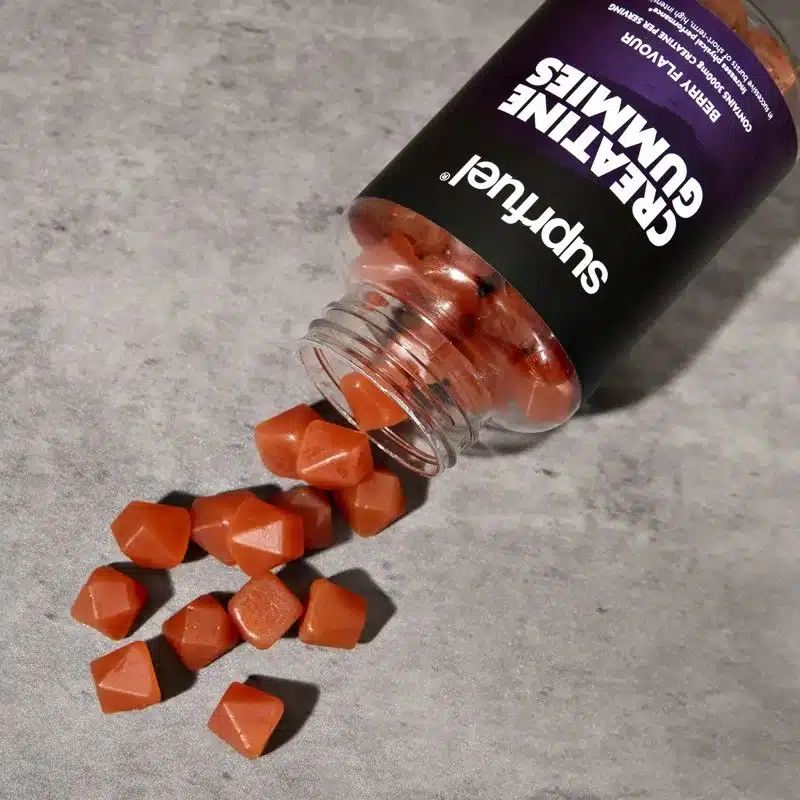
Creatine gummies are transforming the supplement market by offering a convenient, tasty alternative to traditional powders. Made through a meticulous process involving specialized machines like gummy depositors and cooling tunnels, these gummies ensure precise dosing and maintain ingredient efficacy. Their appeal lies in their chewable format, pleasant flavors, and ease of use for athletes and everyday consumers alike. As consumer preferences shift towards more accessible supplement forms, creatine gummies stand out for their ability to deliver essential nutrients without the hassle of mixing or measuring. The production process faces challenges such as managing creatine’s hygroscopic nature and ensuring even distribution of ingredients; however, innovative machinery addresses these issues effectively. Customization options in flavor profiles and dosages further enhance their marketability, making them a popular choice among health-conscious individuals.
Fortified Gummies: Why They Outperform Traditional Vitamins & How Are They Made?
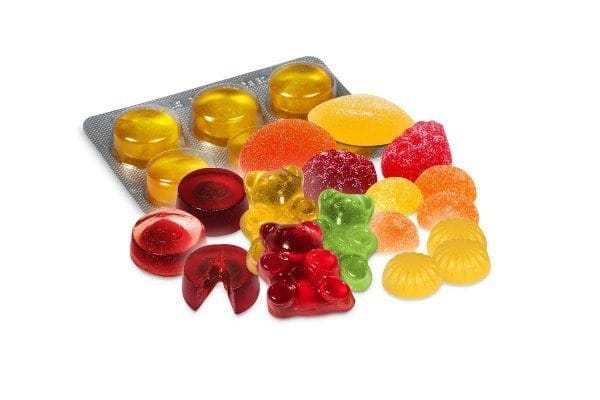
Fortified gummies are increasingly popular due to their taste, convenience, and nutritional benefits. They are easier to consume than traditional pills, making them ideal for children and seniors alike. With flavors that appeal across age groups, these chewable vitamins often contain essential nutrients but may have added sugars. Their manufacturing process ensures quality and efficacy, with advanced techniques for ingredient mixing and hygiene standards. While they offer comparable absorption rates to pills, consumers should be mindful of sugar content and nutrient levels when selecting gummies. Overall, fortified gummies combine practicality with pleasure for a delightful health supplement experience.
What Are the Key Steps to Commercially Manufacturing Mushroom Gummies?
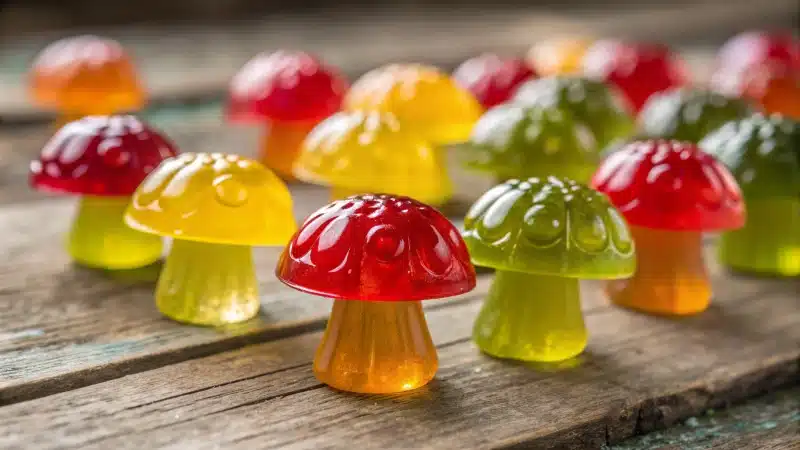
Mushroom gummies are gaining popularity due to their health benefits and ease of consumption. The commercial manufacturing process includes selecting functional mushrooms like Chaga and Reishi, using gelling agents such as gelatin or agar-agar, and employing advanced machinery for precision. Key steps involve grinding mushrooms into powder, mixing ingredients thoroughly, and utilizing automated depositors for uniform gummy shapes. Understanding the specific health benefits of various mushrooms enhances product appeal. Additionally, manufacturers must adhere to strict quality control measures throughout the production process to ensure safety and efficacy. As consumer demand grows for innovative health products, mushroom gummies stand out as a convenient supplement option that combines taste with nutritional value.