Ready to dive into the world of sour gummy worm production?
The choice between statch mogul line and starchless depositing for sour gummy worms hinges on factors like production scale, cost, and desired product shape. Starch mogul production lines are excellent for large volumes and detailed shapes, while starchless depositing for gummies offers flexibility and lower startup costs. Which method aligns with your business goals?
In this post, we'll break down the pros and cons of each production method, explore critical considerations for your gummy business, and guide you toward making an informed decision.
Mogul lines are ideal for producing large volumes of gummy worms.True
Mogul lines excel in high-volume production, making them suitable for businesses needing to produce sour gummy worms at scale.
Starchless depositing is more cost-effective than mogul lines.True
Starchless depositing typically requires lower startup costs, making it a more affordable option for smaller production runs compared to mogul lines.
What Are the Key Differences Between Starch Mogul and Starchless Methods for Manufacturing Sour Gummy Worms?
Understanding the key differences between the Mogul and starchless methods can significantly impact your gummy production strategy. Let's explore these variations to help you make an informed decision.
The starch mogul molding method uses starch molds for consistent long gummy shapes and high-volume production, while starchless depositing for gummies offers cleaner processes and flexibility at lower startup costs.
![]() |
![]() |
---|
Starch Mogul Line vs Non-starch Depositing Line for Gummy Production
Overview of Mogul Line Production for Sour Gummies
The Mogul method is a time-tested technique that involves using starch molds for shaping gummies. This method excels in producing longer, uniform shapes such as sour gummy worms.
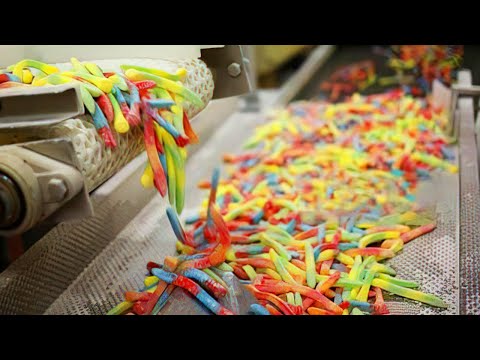
Watch this video showcasing How It's Made: Sour Gummy Worms in a mogul line.
Advantages of Starch Mogul Method for Sour Gummy Bears:
- Consistent Shapes: Starch molds allow for detailed and consistent long shapes.
- High Volume Production: Ideal for large-scale production, ensuring uniformity across batches.
- Efficiency in Bulk Production: Once operational, the system runs for extended periods with minimal labor.
Challenges of Starch Mogul Method:
- Starch Cleanup Requirements: Handling starch leads to extra cleaning, increasing downtime.
- Limited Recipe Flexibility: Changing shapes or recipes can be time-consuming.
- Higher Initial Investment: Upfront costs can be significant, making it less ideal for startups.
Understanding Starchless Depositing for Making Sour Gummies
The starchless depositing method represents a modern approach to gummy production. By utilizing metal or silicone molds, this method eliminates the need for starch, promoting a cleaner production environment.
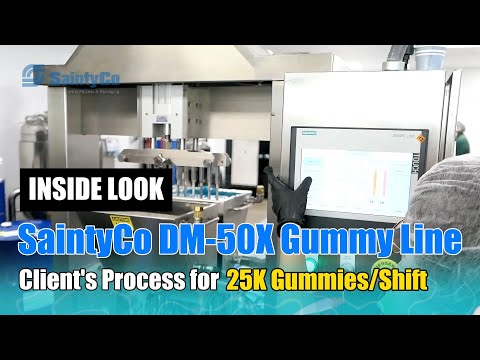
Watch this client video showcasing starchless gummy production with SaintyCo's DM-50X Gummy Depositor in action!
Advantages of Starchless Method:
- Clean Production Process: Reduces the mess associated with starch handling.
- Flexibility and Quick Setup: Easily switch molds and recipes, ideal for shorter runs.
- Lower Startup Costs: More accessible for new businesses wanting to test the market.
Challenges of Starchless Method:
- Shorter Gummy Shapes: Due to mold size limits, the gummies may not achieve the same length as those produced by the Mogul method.
- Lower Throughput Rates: Slower output compared to mogul lines, which could affect larger scale needs.
Key Differences Between the Two Methods for Sour Gummy Worm Production
Feature | Mogul Method | Starchless Method |
---|---|---|
Production Style | Uses starch molds for shaping | Uses metal/silicone molds |
Shape Consistency | High consistency in longer shapes | May produce shorter shapes |
Production Volume | Best for high-volume production | Suitable for small runs |
Cleanup | Requires extensive cleanup | Easier and quicker cleanup |
Investment Cost | Higher initial costs | Lower startup costs |
Recipe Flexibility | Limited flexibility | High flexibility |
Considerations for Choosing a Method for Manufacturing Sour Gummy Candies
When deciding between the Mogul and starchless methods, consider:
- Production Goals: Evaluate the desired volume and product consistency.
- Budget Constraints: Assess your initial investment capability.
- Product Variety Needs: Determine how often you will change recipes or shapes.
For further insights on gummy production methods, check out our resource on gummy production techniques1. Explore how you can enhance your operations by upgrading your equipment.
The Mogul method produces longer gummy shapes than starchless.True
Mogul method excels in creating longer, uniform shapes like sour gummy worms, unlike the starchless method that limits shape length.
Starchless method has higher initial investment costs than Mogul.False
The starchless method is more accessible for startups, featuring lower startup costs compared to the Mogul method's higher initial investment.
How Do Production Costs Compare for Each Method for Sour Gummy Worm Production?
Production costs play a critical role in determining the success of your sour gummy worm manufacturing. How do these costs compare between Mogul and starchless depositing methods?
When comparing production costs for sour gummy worms, Mogul lines require a higher initial investment but are ideal for high-volume production. Starchless depositing offers lower startup costs with flexibility for small batches, impacting overall expenses differently.
Initial Investment Costs
When comparing production methods, the initial investment is crucial.
Mogul Line Production:
- Higher upfront costs due to machinery and starch handling systems.
- Suitable for businesses expecting high volumes.
Starchless Depositing:
- Lower initial costs make it appealing for startups.
- Less machinery complexity allows for faster setup.
Overall, Starch Mogul Lines require a larger investment, while Starchless Depositing Lines offers a more accessible entry point for new manufacturers.
Operating Costs
The ongoing operational costs can greatly influence profitability over time.
Cost Factors | Mogul Line | Starchless Depositing |
---|---|---|
Labor | Higher due to starch cleanup | Lower, easier cleanup |
Maintenance | Regular, more complex | Typically lower maintenance |
Ingredient Handling | More labor-intensive | Easier handling |
Mogul systems may incur higher labor costs due to the need for starch management and cleanup. In contrast, the starchless method reduces labor, leading to potential cost savings in daily operations.
Scalability of Production
Understanding how each method scales is vital for long-term planning.
-
Starch Mogul Lines:
- Ideal for high-volume production with minimal recipe changes.
- Scalable for mass production but may require more significant investment as production increases.
-
Starchless Depositing:
- Flexible and allows quick recipe changes, making it suitable for smaller batches or product variations.
- As demand grows, additional equipment may be necessary, impacting scalability.
This flexibility with starchless depositing allows manufacturers to adapt quickly to market trends, potentially leading to increased profitability.
Cost-Benefit Analysis
Conducting a thorough cost-benefit analysis helps in making informed decisions.
- Mogul Lines offer benefits in terms of consistent quality and higher output, which can justify higher costs when aiming for large-scale production.
- Starchless Depositing provides benefits in flexibility and lower initial investment, making it attractive for businesses experimenting with different gummy products.
For a detailed analysis, consider reviewing various production cost calculators2 that can assist in determining the financial implications of each method.
Final Thoughts on Cost Comparisons
Each production method comes with unique costs and benefits tailored to different business needs and scales. Understanding these aspects can significantly impact your decision-making process. Assess your goals and budget to determine the best fit for your gummy production needs. For further insights into cost management strategies, explore our guide on optimizing production efficiency3.
Mogul Lines have higher initial investment costs than starchless depositing.True
Mogul Lines require more expensive machinery and systems, resulting in a larger upfront cost compared to the simpler starchless depositing method.
Starchless depositing is better for high-volume production.False
Mogul Lines are designed for high-volume output, making them more suitable for large-scale production than starchless depositing methods.
What Impact Do Production Methods Have on Sour Gummy Product Quality?
Exploring the relationship between production methods and product quality is crucial for manufacturers. Different techniques can lead to varied outcomes in texture, consistency, and consumer perception.
Production methods directly impact product quality by influencing factors such as consistency, texture, and flexibility in manufacturing. Starch mogul lines offer high uniformity but less flexibility, while starchless depositing allows for quicker changes but may affect texture. Understanding these trade-offs is essential for quality management.
Understanding Production Methods
The choice of production method can significantly influence product quality. Each method has distinct characteristics that impact the final product's consistency, texture, and overall appeal.
For example, consider the difference between Starch Mogul line production and starchless depositing. The mogul line, with its starch molds, is known for producing long and consistent gummy shapes. This method excels in maintaining a uniform texture across large batches, ensuring that each gummy worm meets consumer expectations.
On the other hand, starchless depositing offers flexibility. It allows manufacturers to quickly switch between different gummy shapes and flavors. However, it may lead to variations in texture due to mold material differences. This variability can affect how consumers perceive quality.
The Role of Shape and Size in Manufacturing Sour Gummy Worms
One crucial factor in product quality is the shape and size of the gummies produced. Here’s a quick comparison:
Production Method | Ideal Shapes | Texture Consistency | Flexibility |
---|---|---|---|
Mogul Line | Long, intricate shapes | High | Low (harder to change) |
Starchless Depositing | Short, compact shapes | Moderate | High (easier to change) |
As shown in the table, the mogul line is best for longer shapes, while starchless depositing is ideal for compact gummies. This distinction plays a vital role in meeting consumer preferences and expectations for quality.
Sour Coating Application
Both production methods can apply a sour coating, but they do so differently:
- Starch Mogul Line: Automated application allows for even coverage across large batches. This automation ensures consistency in flavor and experience.
- Starchless Depositing: Requires additional equipment for coating application. While this method allows for creativity, it may introduce inconsistencies in smaller runs.
Understanding these differences is essential as it directly correlates with how consumers perceive product quality. For more insights on coating processes, check out coating techniques4.
Automation and Efficiency
Automation is another significant factor that influences product quality:
- Mogul Lines: Highly automated systems provide consistency and efficiency in production. With minimal manual intervention, they maintain quality across large production runs.
- Starchless Depositing: Offers flexibility and quick recipe changes but may require more hands-on management. This might lead to variations in quality if not closely monitored.
A comparison of these methods highlights how automation impacts overall product quality. For details on optimizing production efficiency, see production optimization5.
Cost Considerations and Scalability
The choice of production method also ties back to cost and scalability:
- Mogul Lines: High initial investment but ideal for large-scale production with consistent quality.
- Starchless Depositing: Lower startup cost suited for small businesses, but may require additional investment as demand increases.
A careful assessment of cost vs. quality is critical for manufacturers aiming to scale operations without sacrificing product integrity. To explore cost-effective strategies, visit cost management in production6.
Mogul line production ensures high texture consistency in gummies.True
The mogul line method excels in producing gummies with uniform texture across large batches, meeting consumer expectations effectively.
Starchless depositing allows for easier shape changes than mogul lines.True
This method provides flexibility for manufacturers to quickly switch shapes and flavors, unlike the more rigid mogul line approach.
Which Method Is More Suitable for New Gummy Businesses?
Choosing the right method for producing gummies is vital for new businesses. Each production method has unique strengths that can impact your operational efficiency and product quality.
When starting a gummy business, selecting between Mogul lines and starchless depositing is essential. Mogul lines suit high-volume needs, while starchless depositing offers flexibility and lower costs, ideal for startups.
Evaluating Production Methods for New Gummy Businesses
When starting a gummy business, the choice of production method is critical. Two primary options exist: Mogul lines and starchless depositing. Each method has unique advantages and challenges.
Statch Mogul Line Production
This traditional approach involves using starch molds to create gummies. It's best for businesses focusing on high-volume production of longer, detailed shapes like sour gummy worms.
Advantages:
- Long, Consistent Shapes: Ideal for producing intricate designs.
- High Volume Production: Suited for large-scale operations, ensuring uniformity across batches.
- Bulk Production Efficiency: Once set, it runs smoothly for extended periods.
Challenges:
- Starch Cleanup: Increased cleaning time and labor requirements.
- Limited Flexibility: Time-consuming to change recipes or shapes once set up.
- Higher Initial Investment: Requires a significant upfront investment, suitable for established producers.
Starchless Depositing for Gummies
This modern method utilizes metal or silicone molds, eliminating the need for starch and providing a cleaner and more flexible production environment.
Advantages:
- Clean Production: No starch means easier cleanup.
- Flexible and Fast Setup: Quick changes in molds and recipes.
- Lower Startup Cost: Ideal for startups with limited budgets.
Challenges:
- Shorter Gummy Worms: Mold size limitations may affect length.
- Lower Throughput: May not be ideal for high-volume needs.
Key Factors to Consider
Factor | Starch Mogul Line | Starchless Depositing |
---|---|---|
Shape and Size | Best for longer shapes | Good for shorter, varied designs |
Sour Coating Application | Automated coating process | May require additional equipment |
Product Texture | Consistent and firm | Slight variations possible |
Automation | Highly automated | Less automation, more manual effort |
Cost | Higher initial investment | Lower startup cost |
Making the Right Choice Between Starch Mogul Moulding and Non-Starch Depositing
Selecting the right production method depends on your business goals and production needs. If your focus is on high-volume, consistent products, a Mogul line might be the better choice. For those exploring various flavors and shapes with lower initial costs, starchless depositing offers flexibility.
For additional insights on gummy production methods, check out advanced gummy production techniques7.
To dive deeper into the comparison of equipment options, visit equipment selection for gummy manufacturing8.
Mogul lines are ideal for high-volume gummy production.True
Mogul lines support large-scale operations, providing efficiency and consistency in producing gummies, especially for longer and intricate shapes.
Starchless depositing requires higher initial investment than Mogul lines.False
Starchless depositing typically has a lower startup cost, making it more suitable for startups compared to the higher investment needed for Mogul lines.
Conclusion
Explore the pros and cons of Mogul lines versus starchless depositing in sour gummy worm production, focusing on cost, efficiency, and product quality.
At GummyGenix by SaintyCo, we're here to support your journey with cutting-edge, GMP-compliant gummy manufacturing equipment designed for efficiency, precision, and adaptability. Our machines are fully compatible with regulatory standards, and we offer reliable after-sales support to keep your operations running smoothly.
Contact GummyGenix by SaintyCo to explore how our machinery and expertise can enhance your production line. Let’s bring your vision of quality gummy products to life—together.
Gummy Production Machinery from GummyGenix by SaintyCo | Click to Know More
-
This link provides expert insights into gummy production methods, helping you make informed decisions for your business. ↩
-
Discover how different production methods affect your budget and profitability. ↩
-
Find expert insights into optimizing your gummy production costs effectively. ↩
-
Learn how different production methods affect product quality to enhance your understanding and decision-making. ↩
-
Discover techniques to optimize production quality in gummy manufacturing and elevate your business outcomes. ↩
-
Explore cost-effective production strategies that ensure high-quality output without breaking the bank. ↩
-
Explore this link for an in-depth analysis of production methods to find the best fit for your gummy business. ↩
-
Learn more about equipment options that can enhance your gummy production process by clicking this link. ↩