Ever wonder how some gummy production lines run like a well-oiled machine while others struggle?
To optimize a gummy production line, focus on streamlining workflows, investing in reliable equipment, and ensuring precise ingredient control. Embrace continuous flow operations, automation, and regular maintenance to boost efficiency and consistency.
The first time I walked through a gummy factory, the hum of machines and the sweet aroma made it clear how every detail mattered in creating those perfect candies. Shifting to continuous flow operations and investing in automation can transform efficiency, while routine maintenance keeps everything running like a finely tuned instrument. Let’s explore how these strategies can elevate your gummy production line.
Continuous flow reduces gummy production bottlenecks.True
Continuous flow allows simultaneous operations, enhancing efficiency.
How to Streamline Workflow and Optimize Space Utilization in Gummy Production?
Ever felt overwhelmed by clutter in your workspace or production line? Streamlining workflow and space can feel like magic, turning chaos into efficiency.
To streamline workflow and space utilization, start by breaking down tasks into smaller segments, adopt continuous flow processes, and design compact layouts that fit your specific needs.
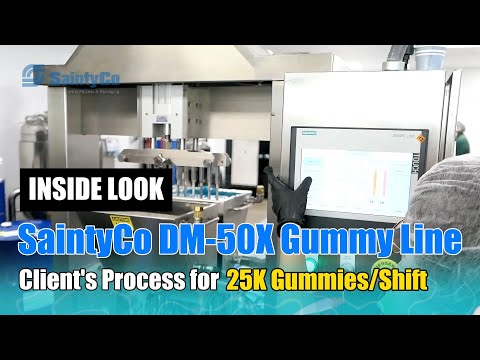
Task Segmentation
Task segmentation involves breaking down the production process1 into distinct stages. For example, in gummy production, tasks can be segmented into weighing, depositing, cooling, and packaging. Each stage is assigned specific operators or teams, enabling simultaneous operations. This segmentation reduces bottlenecks and increases overall efficiency by allowing teams to focus on specialized tasks.
Continuous Flow Implementation
Transitioning from batch production to a continuous flow model can lead to significant improvements in workflow efficiency. In a continuous flow setup, different teams work concurrently on various stages of production. For instance, while one team is responsible for depositing gummies, another might manage the cooling or packaging process. This approach not only maximizes resource utilization but also ensures that every step of the process is continuously in motion, reducing idle time and increasing throughput.
Optimizing Facility Layout
The layout of your workspace plays a crucial role in optimizing both workflow and space utilization. Compact layouts can be achieved by employing self-stacking drying trays and dollies. This method significantly reduces the floor space required compared to traditional racks—up to 80%!
Moreover, by collaborating with us, you can benefit from expert layout planning. Share your facility layout, and we’ll design a production line arrangement tailored to your space and utility requirements. Our designs focus on strategic equipment placement to minimize movement, enhance accessibility, and maximize operational efficiency.
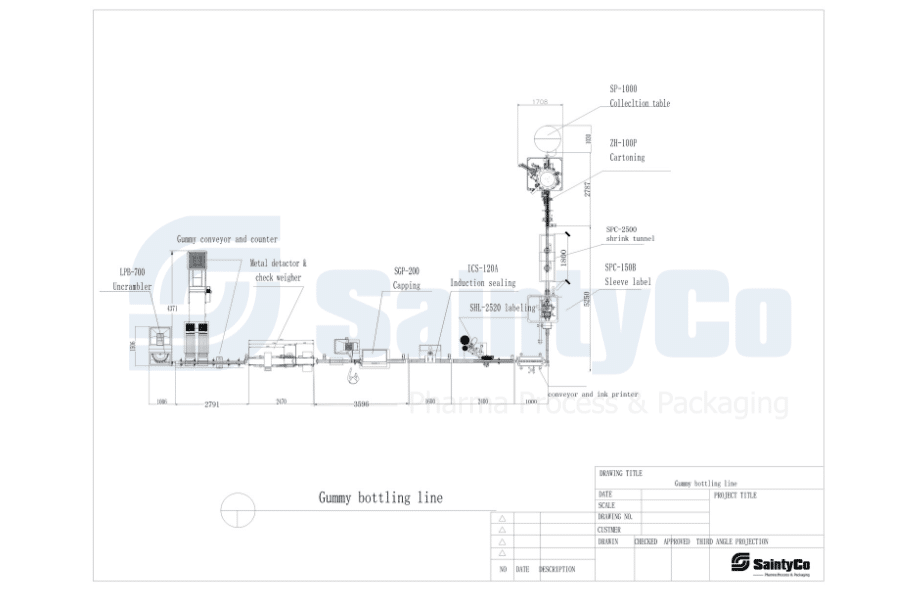
Automation and Equipment Upgrades
Investing in automation—like having an extra pair of hands that never get tired—and reliable manufacturing equipment can dramatically streamline workflow.
Automated systems like the SaintyCo DM-50X depositor provide precise depositing with quick product changeovers, which is essential for maintaining a continuous flow.
Fully automated production lines are particularly beneficial for high-volume outputs or sensitive products like CBD gummies.
While the initial investment may be substantial, it was an investment in peace of mind due to long-term savings and efficiency gains.
Data-Driven Optimization
By recording production rates, quality metrics, and downtime, you can identify areas for improvement and optimize staffing levels accordingly. This data-driven approach not only enhances workflow but also ensures that resources are allocated efficiently without overextending personnel.
Incorporating these strategies transformed the gummy production operation from a chaotic jumble into a seamless system. If you're ready to take the leap towards greater efficiency, consider reaching out for expert advice or tailored equipment suggestions.
Continuous flow model reduces gummy production time.True
Continuous flow allows simultaneous operations, reducing bottlenecks.
Batch production is more efficient than continuous flow.False
Continuous flow maximizes efficiency by allowing simultaneous processes.
How Does Automation Revolutionize Gummy Production?
Ever wonder how those delicious gummy candies are made so perfectly every time? Automation is the secret ingredient behind it all!
Automation in gummy production transforms processes like mixing, molding, and packaging into efficient, consistent operations. This technology boosts productivity, ensures uniform quality, and cuts labor costs, making it a cornerstone of modern gummy manufacturing.
Streamlining Gummy Manufacturing with Automation
Automation significantly enhances the efficiency of gummy production lines2, allowing manufacturers to handle larger volumes with fewer errors. Imagine walking through a candy factory where everything runs like a well-oiled machine—literally! Automated systems can manage tasks like ingredient weighing, mixing, and depositing with precision, ensuring consistent product quality.
Switching from manual labor to automated systems is like moving from driving a stick shift to an automatic car—it makes everything smoother and faster. By transitioning from manual processes to automated systems, companies can achieve a continuous production flow that minimizes bottlenecks. This shift not only accelerates production rates but also optimizes resource allocation. For instance, automated depositors ensure precise dosing of ingredients, reducing waste and enhancing the flavor profile of gummies.
Enhancing Product Consistency and Quality
Consistency is crucial in gummy production, where variations can affect texture and taste. When I was a kid, I always wondered why every gummy in the bag tasted the same. Now I know that consistency is key in gummy production, and automation is the hero here. Automated systems provide uniformity across batches, maintaining standards that manual processes might struggle to achieve.
And those high-tech cooling systems? They're not just for show. Automated cooling systems are pivotal as they ensure gummies cool at the correct rate for ideal texture, giving it that perfect chewiness we all love. Moreover, automation enables the use of advanced mixing technologies3 that guarantee even distribution of flavors and colors. This results in a consistently appealing product that meets consumer expectations.
Reducing Labor Costs and Enhancing Safety
Let's face it; making gummies by hand can be labor-intensive and exhausting. Automation reduces the need for extensive manual labor, which cuts costs and diminishes the risk of human error. This shift allows manufacturers to allocate personnel to more strategic roles, enhancing overall operational efficiency.
Plus, automation enhances safety by keeping people away from potentially dangerous machinery or materials. The introduction of automation in gummy production is also beneficial for meeting stringent compliance standards4. Automated cleaning cycles and oil-coating systems maintain product integrity by preventing cross-contamination or sticky situations.
Driving Innovation in Gummy Production
Automation isn't just about doing the same thing faster; it's about opening doors to new possibilities. With customizable molds and automated settings, manufacturers can experiment with new shapes and flavors without having to reconfigure everything manually. Automation supports innovation by enabling the creation of new gummy varieties without extensive manual reconfiguration.
It's exciting to think about how this technology allows producers to cater to evolving market demands while staying competitive by rapidly adapting to consumer preferences.
Continuous flow maximizes gummy production efficiency.True
Continuous flow reduces downtime by synchronizing production stages.
Batch production is more efficient than continuous flow.False
Batch production often leads to bottlenecks and increased downtime.
Why Is Equipment Calibration Crucial for Optimizing Gummy Manufacturing Performance?
Ever wondered how a small tweak can make a huge difference? That's what calibration does for equipment.
Equipment calibration is crucial because it ensures machines work within set limits, enhancing accuracy and minimizing mistakes. This keeps processes consistent and efficient.
The Importance of Calibration in Gummy Production
Calibration is essential for maintaining precision and avoiding costly disruptions. One client learned this lesson the hard way when an uncalibrated machine caused a shutdown during a critical production run. Since making calibration a priority, they’ve significantly reduced errors and maintained smooth operations, optimizing both performance and product quality.
In precision-driven industries like pharmaceuticals or food production, even minor inaccuracies can result in waste, recalls, or compliance failures. Regular calibration ensures equipment operates at peak accuracy, safeguarding product consistency and quality.
Avoiding Costly Downtime
Uncalibrated equipment is a major risk for unexpected shutdowns, leading to delays and financial losses. By implementing regular calibration schedules, clients have minimized such risks, detecting potential issues before they escalate into full-blown breakdowns. This proactive approach keeps production on track and ensures deadlines are met.
Routine calibration is also a smart investment—it extends equipment lifespan, reduces repair costs, and helps avoid expensive replacements, ultimately saving resources in the long run.
Ensuring Compliance and Meeting Standards
In industries with strict regulatory requirements, calibration plays a critical role in meeting compliance standards. Missed calibration schedules can result in failed audits, fines, or even loss of certifications. Regular calibration not only protects against these risks but also reinforces a commitment to quality and reliability.
Maintaining compliance also builds trust with clients and stakeholders, giving businesses a competitive edge in quality-focused markets.
Optimizing Resource Utilization
Accurate equipment calibration improves resource efficiency, reducing material waste and unnecessary expenses. For example, calibrated machines in manufacturing ensure precise material usage, cutting down on overproduction or excess costs. Clients who invest in consistent calibration often see enhanced operational efficiency and significant cost savings.
Plus, investing in calibration5 frees up our team from fixing errors due to inaccurate measurements. It ups productivity, letting them focus on important tasks instead.
Continuous flow model reduces production bottlenecks.True
Implementing continuous flow allows different teams to work simultaneously, enhancing efficiency.
Automated gummy lines require minimal initial investment.False
Automated systems need significant upfront costs but offer long-term savings through efficiency.
Why Does Ingredient Precision Matter in Gummy Candy Production?
Ever wondered why some gummies are just right while others miss the mark? It all boils down to ingredient precision.
Accurate ingredient measurement ensures gummies have consistent texture, flavor, and appearance. Precise dosing prevents issues like uneven flavors or sticky textures from imbalanced recipes. Sticking to exact ingredient ratios is crucial for maintaining product standards and keeping customers happy.
The Role of Precision in Texture
Texture is a defining characteristic of gummies that directly correlates with ingredient precision. Variations in ingredient measurements can lead to changes in the gummy's chewiness or firmness. For instance, an excess of gelatin might make the gummy too firm, while too little could result in a sticky, unshapely product.
Advanced weighing systems are crucial here, allowing for accurate dosing and consistent product quality. By maintaining precise measurements, manufacturers can achieve the ideal balance of softness and elasticity that defines a high-quality gummy.
Flavor Consistency Through Accurate Measurements
Flavor is another critical element that hinges on ingredient precision. Inconsistent dosing of flavor enhancers or sweeteners can lead to uneven taste profiles, which detract from the consumer experience. Automated mixing systems6 help ensure even distribution of flavors across large batches, preserving the intended taste and aroma.
Precision also plays a role in maintaining the color consistency of gummies, which is important for brand recognition and consumer appeal.
Ingredient Interaction and Quality Control
Beyond individual ingredients, the interactions between them also demand precision. Ingredients like acids and sugars must be balanced to prevent unwanted chemical reactions that could affect the gummy's stability and shelf life. Inline mixing technologies7 are often employed to achieve this balance, providing real-time adjustments to maintain quality standards.
Moreover, regular calibration of machinery ensures that these precise measurements are consistently applied, preventing variations that could compromise the final product.
Importance of Accurate Ingredient Ratios in Specialized Gummies
For specialized gummies such as those containing vitamins or CBD, ingredient precision becomes even more vital. These products require exact dosages to meet regulatory standards and provide the intended benefits. Sophisticated depositor machines8 aid in achieving these precise formulations, ensuring compliance and efficacy.
Maintaining strict control over ingredient ratios not only enhances product quality but also supports transparency and trust with consumers who seek specific health benefits from these gummies.
Task segmentation minimizes production bottlenecks.True
Dividing production into stages ensures simultaneous operations, reducing delays.
Batch production is more efficient than continuous flow.False
Continuous flow maximizes efficiency by allowing simultaneous processing steps.
How Can You Maintain Hygiene Standards in Gummy Bear Manufacturing Effectively?
Maintaining strict hygiene standards in gummy manufacturing is critical to ensuring product safety and quality. From regular cleaning to proper waste management, following structured practices minimizes contamination risks and ensures compliance with industry regulations.
Regular Cleaning and Disinfection
A structured cleaning schedule is essential to maintaining hygiene. One client shared how implementing targeted cleaning of high-contact surfaces, such as equipment panels and conveyor belts, significantly reduced contamination risks. Using industry-approved cleaning agents designed to eliminate bacteria and viruses ensures effective sanitation. A structured cleaning routine9 can provide peace of mind and prevent lapses in cleanliness.
Hand Hygiene
Clients have highlighted the importance of rigorous hand hygiene protocols in preventing contamination. For instance, setting up handwashing stations with clear instructions and providing alcohol-based sanitizers (minimum 60% alcohol) ensures compliance. One manufacturer reported a noticeable reduction in cross-contamination incidents after implementing hand hygiene protocols10 for staff and visitors.
Waste Management
Effective waste management is another cornerstone of hygiene. Separating waste into recyclables, compostables, and non-recyclables not only streamlines disposal but also reduces the risk of pest infestations. One client successfully implemented efficient waste management systems11, resulting in cleaner production areas and improved operational efficiency.
Personal Protective Equipment (PPE)
Proper use of PPE is crucial in environments where contamination risks are high. A gummy producer emphasized the value of comprehensive PPE protocols, including gloves, masks, and protective clothing, to safeguard both staff and products. Adopting a PPE management plan12 helps minimize contamination risks and manage waste effectively.
Education and Training
Hygiene practices are only as effective as the people enforcing them. Regular training sessions and access to educational resources13 ensure that staff are equipped with up-to-date knowledge of best practices. One client reported significant improvements in compliance and overall hygiene standards after conducting periodic workshops for their team.
Continuous flow reduces gummy production bottlenecks.True
Continuous flow allows simultaneous operations, enhancing efficiency.
Batch production is more efficient than continuous flow.False
Continuous flow maximizes efficiency and resource utilization over batch production.
How Can Data Analytics Improve Gummy Candy Production Efficiency?
Remember the last time you found a shortcut that saved you tons of time? That's the magic of data analytics in production—finding those hidden efficiencies that make everything run smoother.
Data analytics boosts production efficiency by spotting bottlenecks, fine-tuning resource use, and predicting maintenance needs. By diving into real-time data, manufacturers can streamline workflows, cut downtime, and ramp up productivity, making operations more cost-effective and nimble in meeting market demands.
Identifying Bottlenecks and Streamlining Processes
Data analytics tools can pinpoint inefficiencies within production lines by tracking metrics such as cycle time, throughput, and defect rates. By visualizing this data, manufacturers can identify stages where delays occur, allowing for targeted interventions to streamline operations. Implementing machine learning algorithms14 can further predict patterns leading to bottlenecks, enabling proactive adjustments.
Optimizing Resource Allocation
Allocating resources efficiently is crucial for maintaining smooth production flows. Data analytics provides insights into optimal staffing levels, machine usage, and material consumption. For instance, predictive analytics can forecast demand fluctuations, allowing companies to adjust resource allocation accordingly. Utilizing real-time dashboards15 helps managers make informed decisions to enhance productivity and reduce waste.
Predictive Maintenance
Data analytics facilitates predictive maintenance by monitoring equipment health through IoT devices and sensors. Analyzing data such as vibration levels and temperature trends helps predict when machinery might fail, preventing unexpected breakdowns. Companies like General Electric16 have adopted these practices, significantly reducing downtime and maintenance costs by scheduling timely interventions based on data insights.
Enhancing Quality Control
Quality control is paramount in maintaining product standards and customer satisfaction. Data analytics enables real-time monitoring of production quality by analyzing data from various checkpoints along the assembly line. By implementing statistical process control17, manufacturers can detect deviations from quality norms early, ensuring consistent product output and reducing rework rates.
Increasing Responsiveness to Market Changes
In a dynamic market environment, being able to swiftly adapt to changes is a competitive advantage. Data analytics equips manufacturers with the capability to respond to market demands efficiently. By analyzing sales trends and consumer preferences, production schedules can be adjusted promptly, ensuring supply aligns with demand without overproduction or shortages.
Continuous flow maximizes gummy production efficiency.True
Continuous flow reduces bottlenecks by allowing simultaneous operations, enhancing efficiency.
Batch production is more efficient than continuous flow.False
Batch production often causes delays and bottlenecks, unlike continuous flow which optimizes efficiency.
Conclusion
Optimize gummy production lines by streamlining workflows, investing in automation, ensuring precise ingredient control, and maintaining hygiene standards to enhance efficiency and product quality.
GummyGenix by SaintyCo is here to support your promising gummy making journey. With over 23 years of experience, we specialize in end-to-end gummy production solutions—from innovative, industry-compliant machinery to expert guidance at every step. Whether you're a new business or expanding production, our customized solutions, efficient equipment, and dedicated after-sales support can help you meet your goals.
Contact GummyGenix by SaintyCo to explore how our machinery and expertise can enhance your production line. Let’s bring your vision of quality gummy products to life—together.
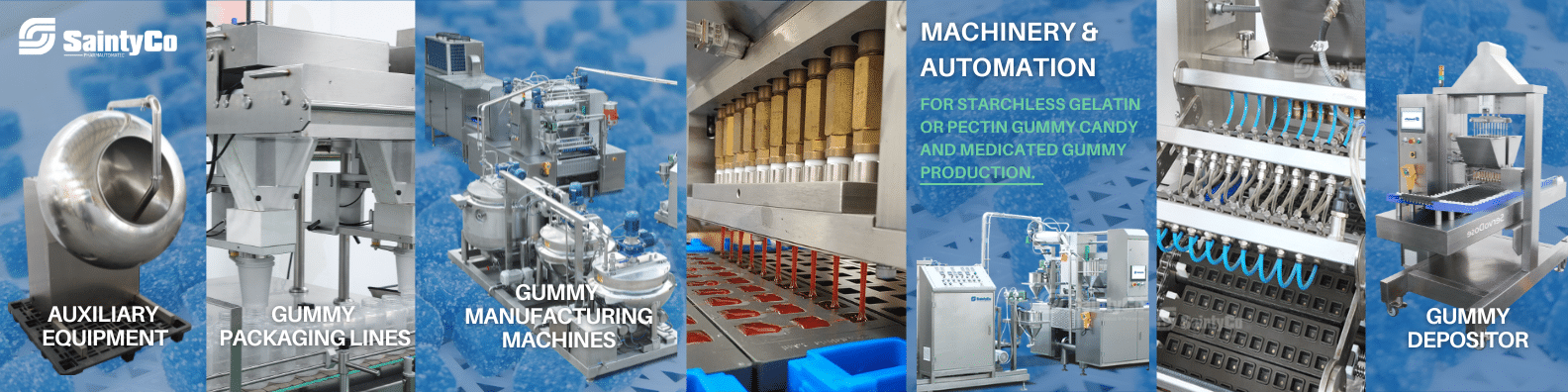
-
Discover detailed insights into task segmentation benefits for production. ↩
-
Discover how automation boosts efficiency and reduces errors in production. ↩
-
Learn about technologies ensuring even flavor distribution in gummies. ↩
-
Explore how automation helps maintain stringent compliance standards in the US. ↩
-
Understand the cost-saving and efficiency benefits of proper equipment calibration. ↩
-
Discover how automated systems ensure consistent flavor distribution in gummies. ↩
-
Explore how inline technologies maintain quality by balancing ingredients. ↩
-
Learn how depositors ensure precise dosages in specialized gummies. ↩
-
Learn how to create an effective cleaning schedule tailored for your needs. ↩
-
Discover the best hand hygiene practices for public safety. ↩
-
Explore strategies for effective waste management to maintain cleanliness. ↩
-
Understand how to implement a PPE plan to enhance safety. ↩
-
Access comprehensive materials on maintaining high hygiene standards. ↩
-
Explore how algorithms predict inefficiencies for proactive adjustments. ↩
-
Learn how dashboards enable informed decisions to boost productivity. ↩
-
Discover GE's success in reducing downtime through data-driven maintenance. ↩
-
Understand how statistical control ensures consistent product quality. ↩