Keeping a gummy depositor in top shape is like nurturing a garden—both require attention and care.
To effectively maintain a gummy depositor, focus on regular cleaning, routine mechanical inspections, precise calibration, and operator training. These practices prevent residue buildup, reduce wear on components, and ensure accurate deposition, thereby minimizing downtime and maintaining consistent product quality.
While these basics are crucial, there’s so much more to explore. Let’s dive deeper into what truly makes a difference in maintaining your gummy depositor.
Regular cleaning prevents gummy depositor breakdowns.True
Regular cleaning removes residues that cause clogging, ensuring smooth operation.
What Are the Key Components of Gummy Depositors to Inspect Regularly?
Regular inspections of key components in a gummy depositor are vital for sustaining production efficiency and preventing unexpected downtimes.
Key components to inspect regularly include pistons, nozzles, O-rings, and seals. These elements are prone to wear and require consistent checks to ensure they function correctly, minimizing the risk of production interruptions.
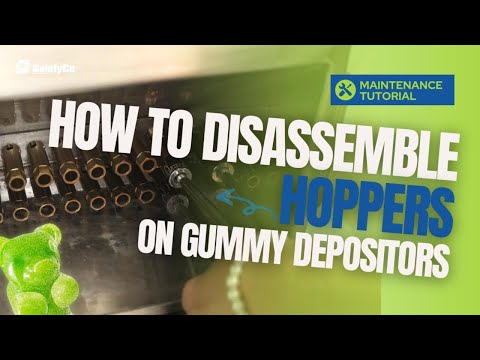
Pistons and Nozzles
Pistons and nozzles are the heart of a gummy depositor1. They drive the deposition process by controlling the flow and volume of the gummy mixture. Regular inspection is crucial:
- Wear and Tear: Check pistons and nozzles for any signs of abrasion or wear, which can affect the accuracy of gummy deposition.
- Cleaning: Ensure these components are free from sticky residues that could lead to clogging. Daily cleaning after each production cycle is recommended.
O-Rings and Seals
O-rings and seals are integral to maintaining airtight connections within the machine:
- Inspection Frequency: Inspect these components weekly to detect any degradation that might compromise sealing.
- Replacement Schedule: Keep a preventive replacement schedule to avoid leaks and maintain consistency in gummy production.
Temperature and Viscosity Monitoring
Fluctuations in temperature can alter the viscosity of the gummy mixture:
- Temperature Control: Regularly monitor and calibrate temperature settings to ensure stable operations.
- Viscosity Sensors: Employ sensors to maintain optimal viscosity, preventing uneven deposits.
Lubrication of Moving Parts
Lubrication minimizes friction between moving parts, prolonging their lifespan:
- Manufacturer's Guidelines: Use lubricants recommended by the manufacturer for specific parts like gears and valves.
- Frequent Application: In high-production environments, lubrication may need to be more frequent than standard intervals.
Component | Inspection Frequency | Replacement Schedule |
---|---|---|
Pistons | Weekly | As Needed |
Nozzles | Weekly | As Needed |
O-Rings | Weekly | Preventive |
Seals | Weekly | Preventive |
Lubrication | Bi-weekly | As per Manufacturer |
By systematically inspecting these components, manufacturers can ensure their gummy depositor operates at peak efficiency. Incorporating modern technologies like smart sensors can further enhance the monitoring process, ensuring timely maintenance interventions. Remember, operator training2 is essential to equip your team with the knowledge needed for thorough inspections.
Pistons should be inspected daily in a gummy depositor.False
Pistons should be inspected weekly, not daily, for wear and tear.
O-rings require preventive replacement to avoid leaks.True
Preventive replacement of O-rings helps maintain airtight connections.
Why Is Operator Training Crucial for Gummy Machine Longevity?
Operator training is fundamental for maximizing machine lifespan, preventing costly downtime, and ensuring consistent production quality.
Operator training is vital because it empowers employees with the skills to handle equipment properly, recognize signs of wear early, and perform routine maintenance. This not only extends the life of the machinery but also enhances operational efficiency and safety.
The Importance of Proper Handling
Training operators to handle machinery correctly is essential. Proper handling minimizes the risk of accidental damage that can occur from incorrect use, such as forcing components or using inappropriate tools. An operator well-versed in the machinery's functionalities can prevent mishaps that could lead to costly repairs.
Early Recognition of Wear and Tear
One of the significant benefits of operator training is the ability to identify signs of wear and tear early. Trained operators can distinguish between normal operating sounds and unusual noises that might indicate a problem. This proactive approach allows for timely interventions before minor issues escalate into major failures.
Routine Maintenance Skills
Operators trained in routine maintenance can significantly contribute to a machine's longevity. Understanding how to perform basic tasks like lubrication, cleaning, and component inspections means that operators can keep machines in optimal condition between scheduled maintenance sessions. Such skills also reduce reliance on external technicians, saving time and resources.
Task | Frequency | Operator Responsibility |
---|---|---|
Lubrication | Weekly | Apply manufacturer-recommended lubricants |
Cleaning | After each shift | Use appropriate cleaning agents |
Component Checks | Monthly | Inspect for wear or damage |
Enhancing Safety and Efficiency
Training not only focuses on machine operation but also emphasizes safety protocols. Well-trained operators are less likely to make mistakes that could compromise safety or production quality. Understanding safety procedures ensures compliance with industry standards, reducing accident risks and enhancing overall efficiency.
Building a Comprehensive Training Program
A successful training program should encompass several key areas:
-
Equipment Familiarization: Operators must be familiar with the specific components and functions of the machinery they manage. This knowledge is fundamental for recognizing and diagnosing potential problems.
-
Maintenance Procedures: Training should include step-by-step guidance on routine maintenance tasks like cleaning, lubrication, and part replacements. Hands-on workshops can reinforce this learning.
-
Troubleshooting Techniques: Equipping operators with problem-solving skills ensures they can respond swiftly to unexpected issues, reducing downtime.
-
Safety Protocols: Comprehensive safety training protects both operators and equipment, emphasizing the importance of following manufacturer guidelines.
Continuous Improvement through Feedback
Encouraging operators to provide feedback on machine performance fosters a culture of continuous improvement. By understanding operators' experiences and challenges, management can make informed decisions about equipment upgrades or process changes. Engaging operators in this way ensures that their insights contribute to sustained machine performance.
For more insights into operator training programs3, consider exploring resources that discuss effective training methodologies and their impact on equipment longevity.
Proper training reduces machine downtime significantly.True
Training equips operators to handle equipment correctly, preventing breakdowns.
What Role Does Gummy Machine Manufacturer Support Play in Maintenance?
Manufacturer support is vital in maintaining complex machinery like gummy depositors, ensuring optimal performance and minimizing downtime.
Manufacturer support provides technical assistance, training resources, and spare parts, crucial for maintaining equipment efficiency and reducing operational disruptions.
Access to Technical Expertise
Manufacturer support often includes access to a team of technical experts who understand the intricacies of your gummy depositor. This can be invaluable when troubleshooting unexpected issues. Having a direct line to experts who can provide solutions based on their extensive knowledge of the machine ensures that any operational hiccups are resolved quickly.
Additionally, they can provide real-time diagnostics4 through remote monitoring systems, allowing for proactive maintenance measures.
Comprehensive Training Resources
Training provided by manufacturers goes beyond basic operational instructions. It encompasses in-depth guidance on maintenance protocols, troubleshooting techniques, and best practices for optimizing machine performance. By investing in comprehensive training sessions, manufacturers help operators understand how to maintain and troubleshoot their equipment effectively. This reduces reliance on external support and enhances overall productivity.
Availability of Spare Parts
Manufacturers often offer a ready supply of spare parts specifically designed for their machines. This ensures compatibility and quality, preventing the risk associated with using generic or substandard components. Maintaining an inventory of critical spare parts, such as O-rings or nozzles, allows for swift replacements during emergencies, minimizing production downtime.
Warranty Coverage and Service Agreements
Understanding warranty terms and service agreements is crucial. Manufacturers typically offer warranties that cover specific parts and repairs for a set period. These agreements can significantly reduce repair costs and provide peace of mind that any defects will be addressed without additional expenses. Service agreements often include scheduled maintenance visits by trained technicians, further enhancing the longevity of the equipment.
Detailed Documentation and Support Materials
Access to detailed documentation is another critical aspect of manufacturer support. Manuals, maintenance guides, and troubleshooting checklists provided by the manufacturer are tailored to the specific model of your gummy depositor. They ensure that maintenance tasks are carried out consistently and accurately, reducing the likelihood of errors that could lead to machine failure.
Leveraging Technology for Enhanced Support
Many manufacturers integrate advanced technologies into their support services. For instance, smart sensors and automated diagnostic tools can be employed to monitor machine performance continuously. This data-driven approach enables manufacturers to offer predictive maintenance solutions, ensuring issues are identified and rectified before they escalate.
Manufacturer support reduces operational disruptions.True
Support includes technical assistance, training, and spare parts.
Generic spare parts are better than manufacturer parts.False
Manufacturer parts ensure compatibility and quality, reducing risks.
How Can Technology Enhance Gummy Depositor Maintenance?
Technology plays a pivotal role in streamlining gummy depositor maintenance, ensuring efficiency and minimizing downtime.
Technology enhances gummy depositor maintenance through smart sensors, automated diagnostics, and data-driven insights. These innovations allow for predictive maintenance, reducing unexpected breakdowns and optimizing production efficiency.
The Role of Smart Sensors in Maintenance
Smart sensors are a technological advancement that can significantly enhance depositor maintenance. By integrating smart sensors5 into your gummy depositor system, you gain real-time insights into critical parameters such as flow rate, temperature, and pressure. This continuous monitoring allows for immediate detection of anomalies, enabling proactive maintenance measures before issues escalate.
For instance, sensors can detect fluctuations in temperature or viscosity, which may indicate potential clogs or misalignments within the system. By addressing these early warnings, manufacturers can prevent production halts and maintain consistent product quality.
Automated Diagnostics for Proactive Maintenance
Automated diagnostic systems are another technological boon for gummy depositors. These systems conduct regular self-checks on the machinery, identifying potential problems such as wear and tear on pistons or valves. For example, automated diagnostics6 in modern machines can alert operators to the need for lubrication or part replacements based on usage patterns.
This proactive approach not only minimizes downtime but also extends the lifespan of equipment by ensuring timely interventions. Automated diagnostics enable operators to focus on optimization rather than troubleshooting, thereby enhancing overall production efficiency.
Data-Driven Insights for Optimizing Maintenance
Data collection and analysis have become integral to efficient depositor maintenance. By leveraging data-driven insights7, operators can track trends in equipment performance over time. This information is crucial for establishing preventive maintenance schedules tailored to the specific demands of the production environment.
For example, analyzing data from past maintenance activities can reveal patterns in wear and tear or common points of failure. This enables more strategic planning of part replacements and maintenance tasks, reducing unexpected failures and optimizing resource allocation.
Furthermore, data analytics can provide insights into operator performance, identifying areas where additional training may be beneficial to prevent human errors that could lead to equipment damage.
Integrating Advanced Technologies for Comprehensive Maintenance
The integration of advanced technologies such as the Internet of Things (IoT) and machine learning can further enhance depositor maintenance practices. IoT connectivity allows for remote monitoring and control of depositor systems, facilitating quick responses to issues even when operators are off-site.
Machine learning algorithms can analyze vast amounts of data to predict equipment failures before they occur. By recognizing patterns that precede malfunctions, these systems can suggest specific maintenance actions to prevent downtime.
In conclusion, technology offers numerous opportunities to enhance gummy depositor maintenance. By embracing innovations like smart sensors, automated diagnostics, and data analytics, manufacturers can achieve greater efficiency, reduce costs, and maintain high product quality.
Smart sensors enable predictive maintenance in depositors.True
Smart sensors provide real-time data, allowing early detection of issues.
Automated diagnostics increase depositor downtime significantly.False
Automated diagnostics reduce downtime by identifying issues early.
Conclusion
Maintaining your gummy depositor with regular cleaning, routine inspections, precise calibration, and proper operator training is crucial for maximizing uptime and ensuring consistent, high-quality production. By proactively monitoring key components and integrating modern technology like smart sensors and automated diagnostics, you can minimize unexpected downtimes and extend the lifespan of your equipment. Following these practices will help keep your production line running smoothly and efficiently.
GummyGenix by SaintyCo: The Ideal Gummy Depositor Solution
SaintyCo’s GummyGenix Depositors are engineered to provide precision, reliability, and ease of operation for high-volume gummy production. With advanced features such as smart sensors, automated diagnostics, and a user-friendly interface, these depositors are designed to streamline your manufacturing process and ensure optimal performance, minimizing interruptions and boosting overall productivity.
Whether you’re producing traditional gummies or specialized formulations, GummyGenix by SaintyCo is the perfect solution for achieving consistent, high-quality results.
If you’re looking to improve your production efficiency and maintain your equipment with ease, get in touch with SaintyCo today. We offer tailored support and expert guidance to help you reach your production goals.
Want to see the GummyGenix Depositor in action?
Contact us now for a personalized consultation or schedule a demo to learn more about how GummyGenix can benefit your business!
-
Learn about pistons and nozzles' role in gummy deposition.: This XL Universal Candy Depositor comes with the extra large hopper with heated panels for gummies and hard candies is designed to work with all the Truffly Made silicone molds and most polycarbonate molds up to 11.5 inches wide, it delivers accurately metered fillings with great flexibility. ↩
-
Discover why operator training is crucial for effective equipment maintenance.: Discover the crucial role of training for equipment maintenance personnel in ensuring optimal performance and longevity of machinery. ↩
-
Learn about successful training strategies to improve machine longevity.: In this blog, we'll explore effective ways to train manufacturing operators that will assist you in building a competent and motivated team. ↩
-
Explore how remote monitoring optimizes maintenance through real-time diagnostics.: By remotely monitoring different machine components, plants can detect excess vibration before it causes unplanned downtime. Typical IIoT-enabled vibration ... ↩
-
Discover how smart sensors provide real-time monitoring benefits.: Most of these sensors on the gummy depositor can automatically stop the operations of the gummy depositor in case of any hitches. Control Panel. ↩
-
Learn about the benefits of automated diagnostics in reducing downtime.: Diagnostic systems are critical to reducing downtime and allowing systems to run “lights out.” Today's manufacturing environment has accelerated ... ↩
-
Explore how data analysis optimizes maintenance schedules.: Reduced Downtime: By predicting when equipment is likely to fail, data-driven maintenance minimizes unplanned downtime, ensuring continuous ... ↩