Choosing the right gummy packaging machine is key to protecting your products and boosting your operational efficiency. If you're running a gummy business, navigating the multitude of available options to find the perfect machine for your needs is essential. With extensive experience assisting hundreds of gummy manufacturers worldwide, including those in the CBD and nutraceutical sectors, with automated gummy processing and packaging solutions, I understand your challenges. This guide will walk you through the necessary steps to make an informed decision, showcasing various packaging technologies and essential factors to consider.
When selecting a gummy packaging machine, consider factors such as packaging type, recommended technology, automation level, key features, and supplier reliability. Grasping these aspects will help you choose a machine that enhances your production efficiency and product quality. Specifically, focus on cost, the technology best suited to your product, and the level of support suppliers can provide.
Key Considerations When Selecting a Gummy Packaging Machine
Types of Gummy Packaging
Gummy packaging comes in various forms, each catering to different needs and preferences. The primary types include:
- PET or HDPE Plastic Bottles: Available in various sizes and shapes, these bottles are ideal for bulk packaging.
- Premade Pouches: Versatile and can be resealed, maintaining product freshness.
- Single-Serve Portion Packs: Convenient for on-the-go consumption, these packs are gaining popularity.
- Stand-Up Pouches: These pouches stand upright, making them perfect for shelf display.
- Gusseted Bags: These bags expand when filled, offering more space.
- Sachets: Ideal for single servings and easy to package.
- Counter Displays and Club Store Trays: Suitable for retail environments, these options help market and display products.
.
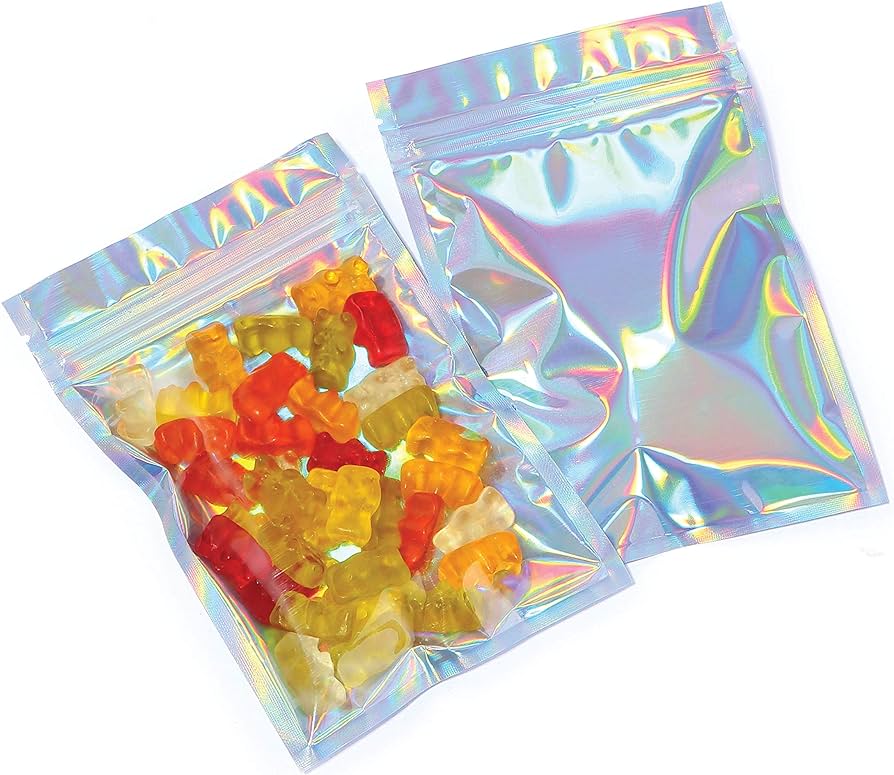
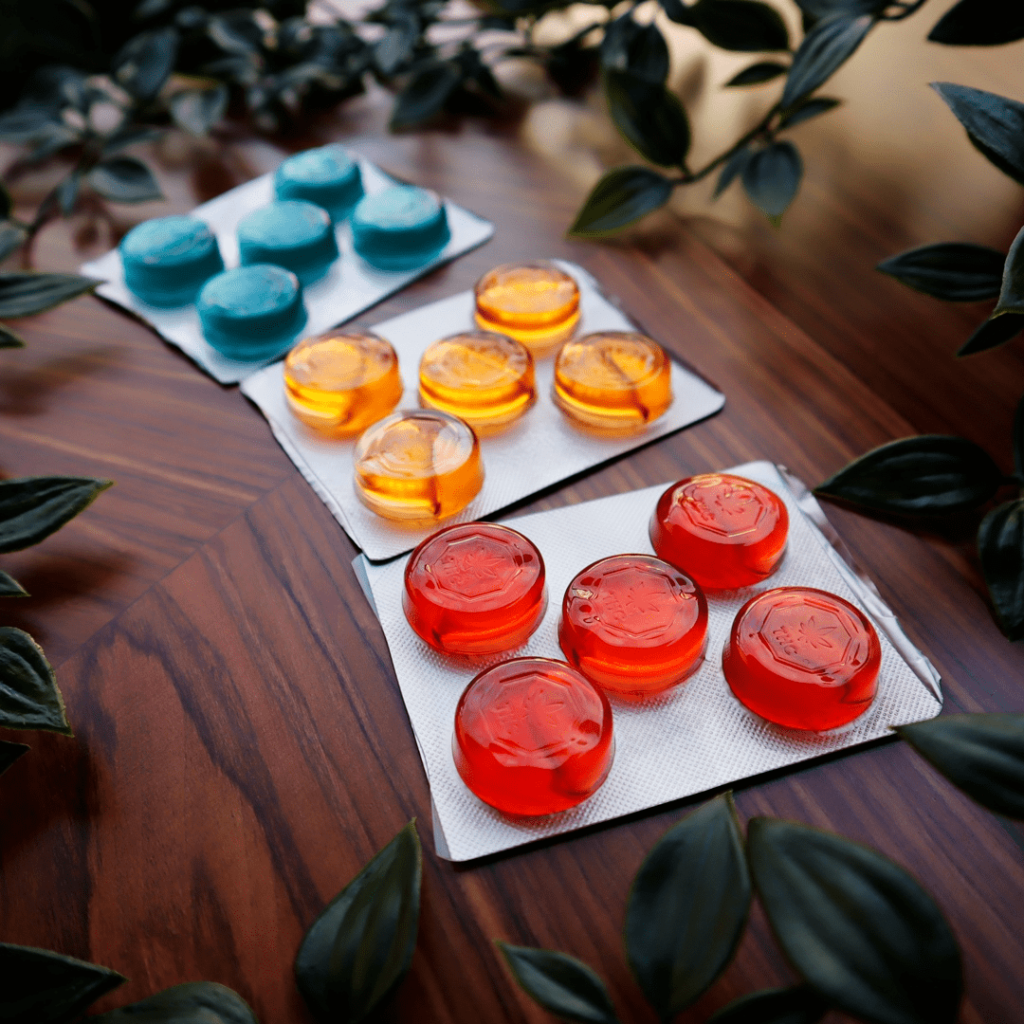
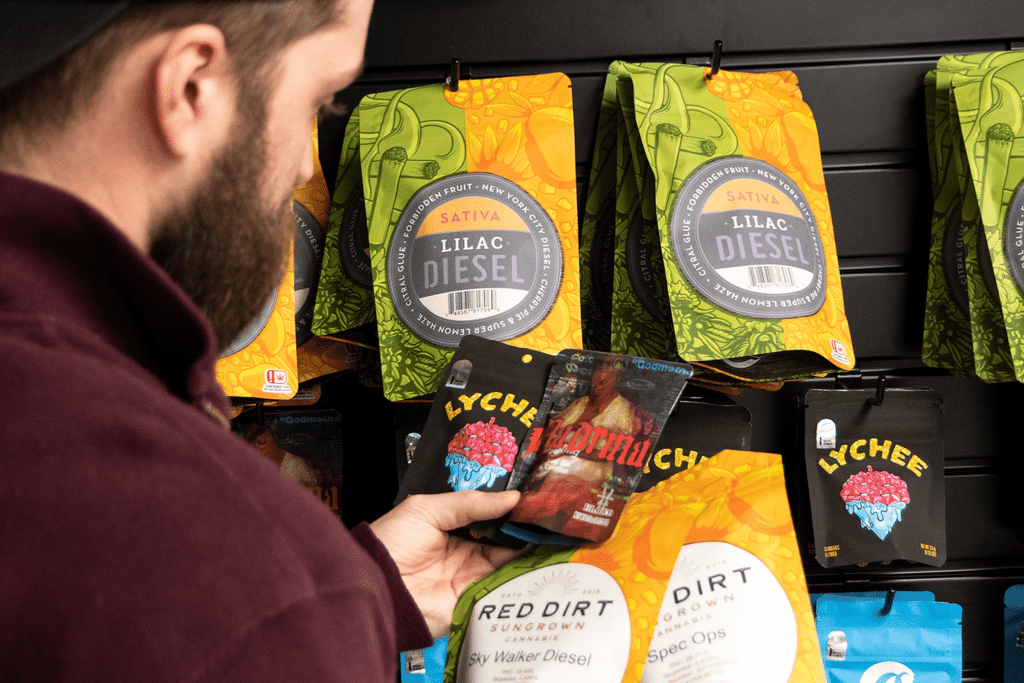
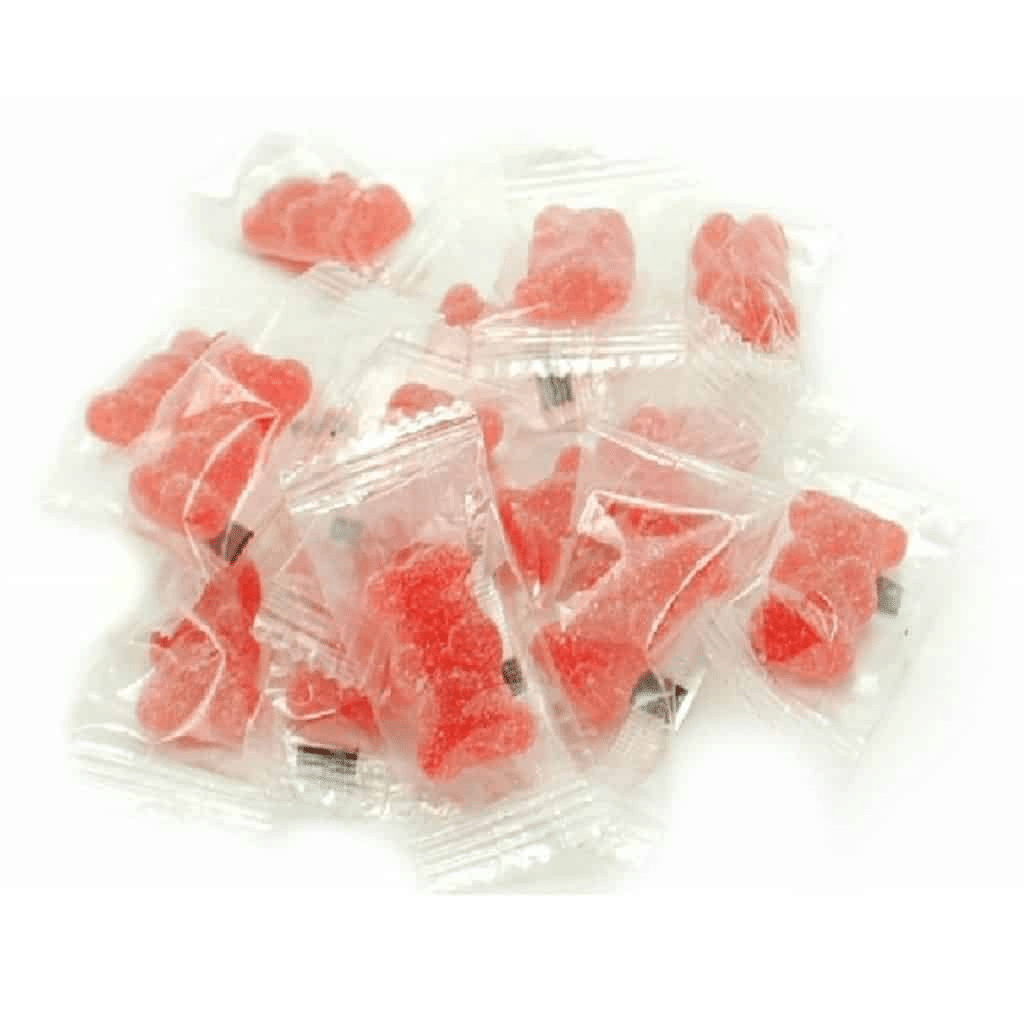
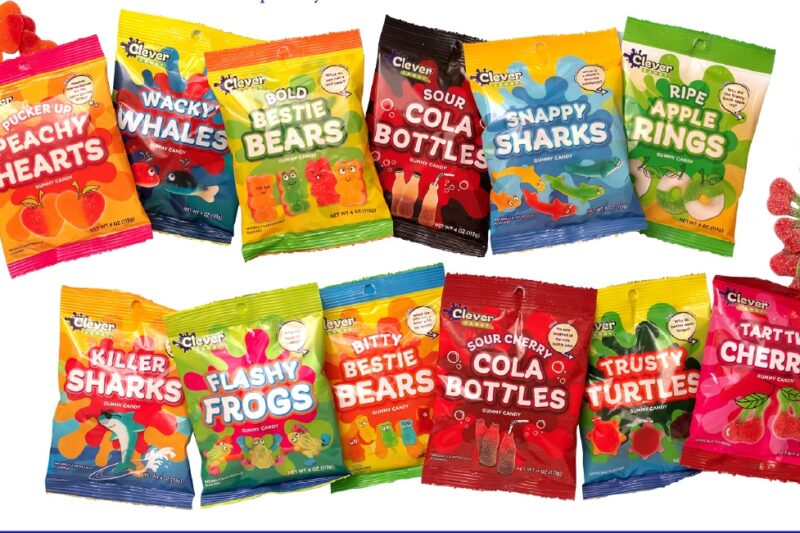
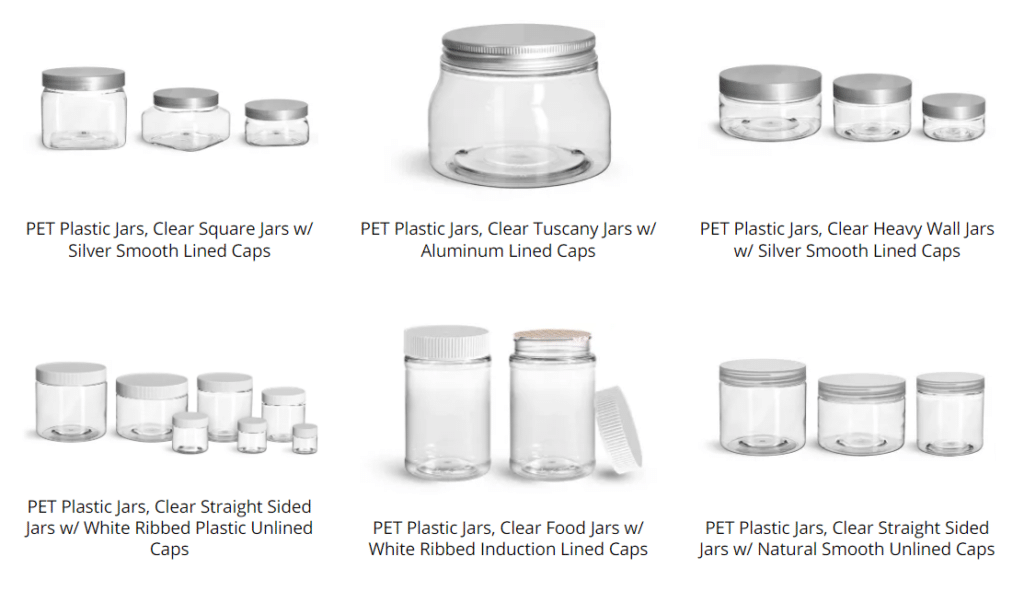
.
Here is a brief cost comparison or typical use cases for each packaging type:
- PET or HDPE Plastic Bottles: Cost-effective for bulk packaging, commonly used for vitamins and supplements.
- Premade Pouches: Mid-range cost, ideal for flexible and resealable options.
- Single-Serve Portion Packs: Higher cost per unit, best for convenience and on-the-go products.
- Stand-Up Pouches: Attractive for retail displays, slightly higher cost but offers excellent shelf presence.
- Gusseted Bags: Cost varies, providing additional space for larger quantities.
- Sachets: Low to mid-range cost, suitable for single servings.
- Counter Displays and Club Store Trays: These have a high initial cost but are effective for marketing and bulk sales.
.
Packaging Type | Cost Range | Typical Use Cases |
PET or HDPE Plastic Bottles | Cost-effective | Bulk packaging, commonly used for vitamins and supplements |
Premade Pouches | Mid-range cost | Ideal for flexible and resealable options |
Single-Serve Portion Packs | Higher cost per unit | Best for convenience and on-the-go products |
Stand-Up Pouches | Slightly higher cost | Attractive for retail displays, offers excellent shelf presence |
Gusseted Bags | Cost varies | Provides additional space for larger quantities |
Sachets | Low to mid-range cost | Suitable for single servings |
Counter Displays and Club Store Trays | High initial cost | Effective for marketing and bulk sales |
.
Recommended Packaging Technology for Gummies and Their Pros and Cons
Accuracy and efficiency are paramount in gummy packaging technology. Here are the main technologies used:
- Optical Counting: This technology uses sensors to count gummies precisely. It ensures each package contains the exact number of gummies, which is crucial for maintaining consistency and customer satisfaction.
- Pros: High accuracy, reduced product giveaway, suitable for high-value products.
- Cons: It can be costly and requires regular calibration and maintenance.
- Applications: Particularly beneficial for the cannabis industry, where precise dosing is crucial.
.
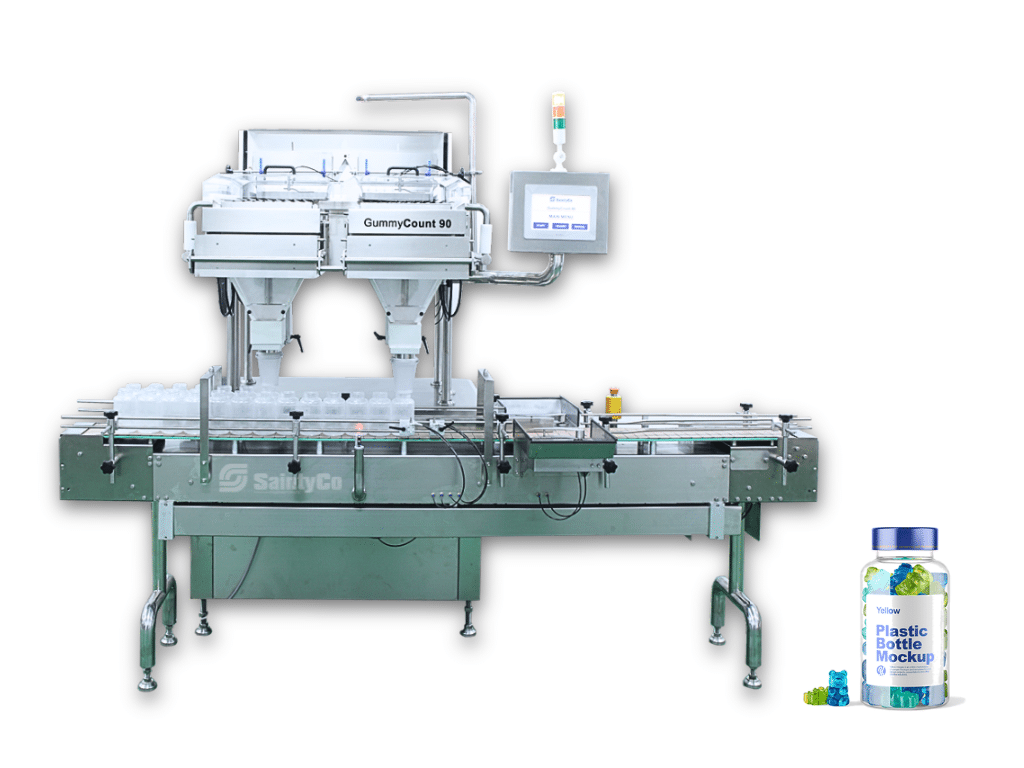
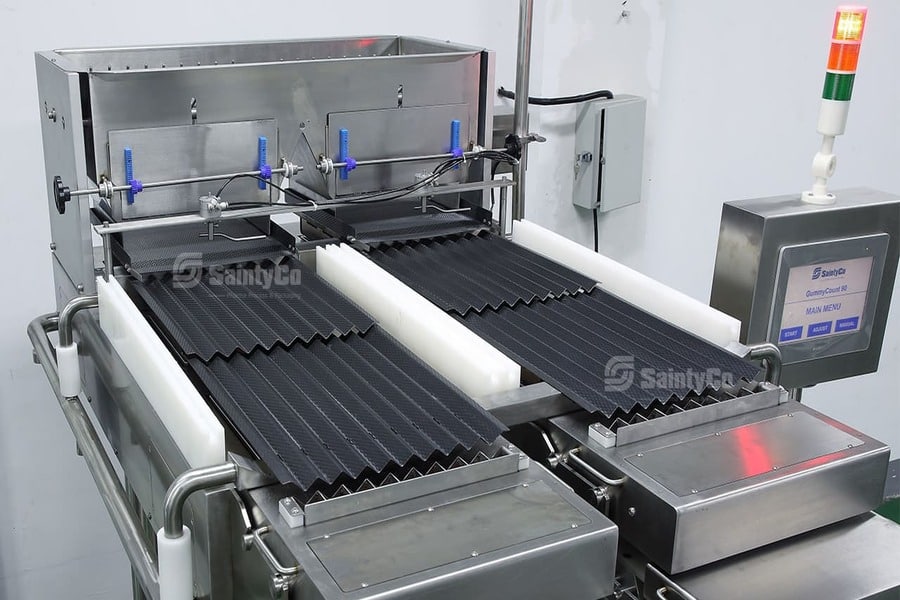
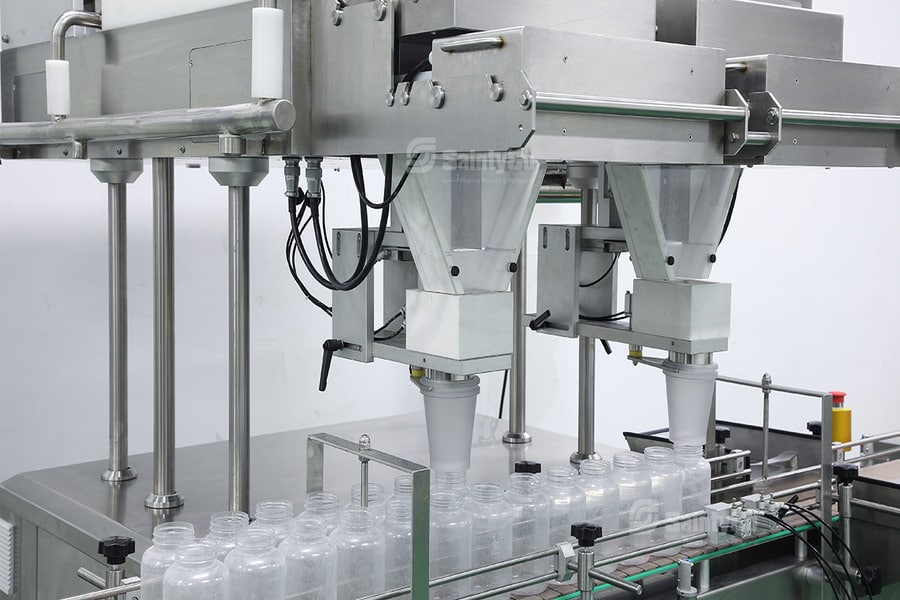
.
- Checkweighers: These machines weigh each package to ensure it meets the specified weight criteria. Any package outside the acceptable range is rejected.
- Pros: Ensures weight consistency, reduces product wastage, and high-speed operation.
- Cons: It may not be as precise as optical counting for small batches and requires regular maintenance.
- Applications: Ideal for the nutraceutical industry where exact dosages are critical.
.
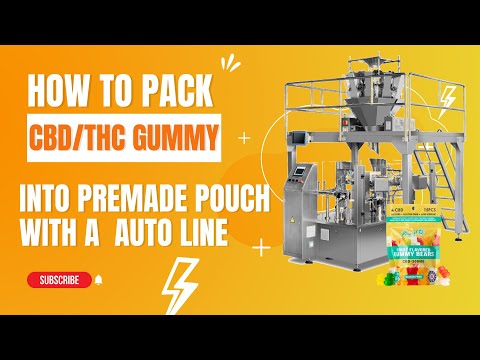
.
- Vibratory Fillers: These machines use vibration to move gummies into packaging containers.
- Pros: Flexible, cost-effective, can handle irregularly shaped and different size gummies.
- Cons: Less precise than optical counting, can be slower for large-scale operations.
- Applications: Suitable for the confectionary industry, where product shapes and sizes can vary widely.
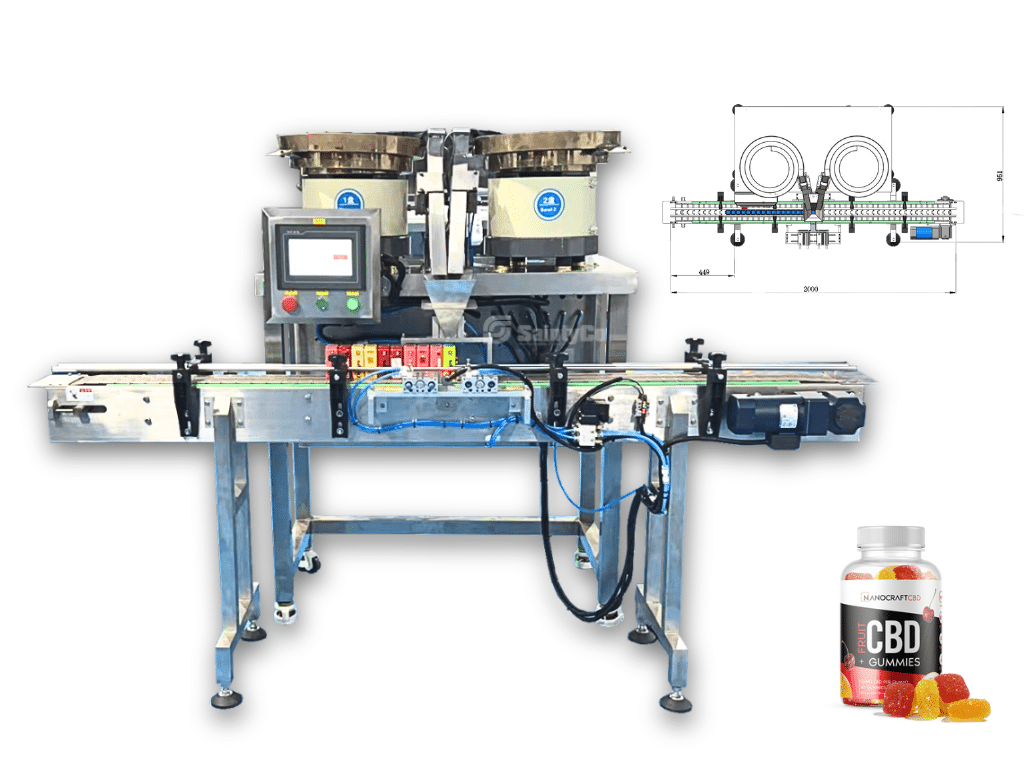
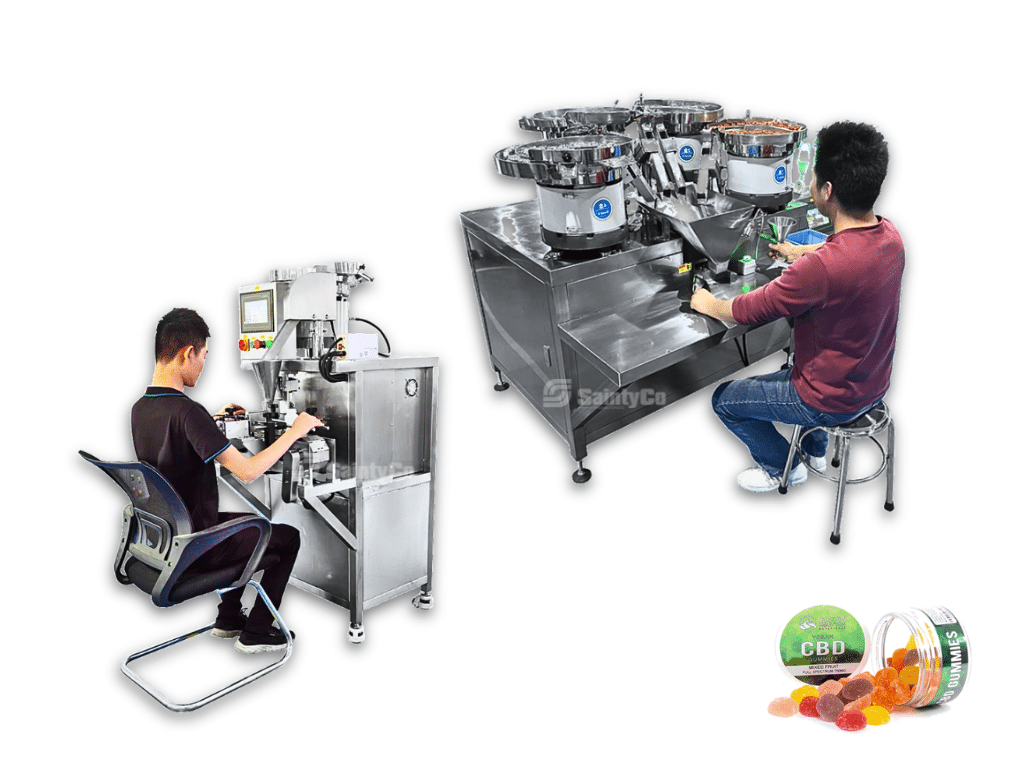
.
- Auger Fillers: These are often used for powdered or granular products, but they can also be packaged in gummies in certain scenarios.
- Pros: Accurate for specific applications, suitable for consistent shapes.
- Cons: Not ideal for irregularly shaped gummies, may require additional equipment for optimal use.
- Applications: Useful in mixed-use production environments.
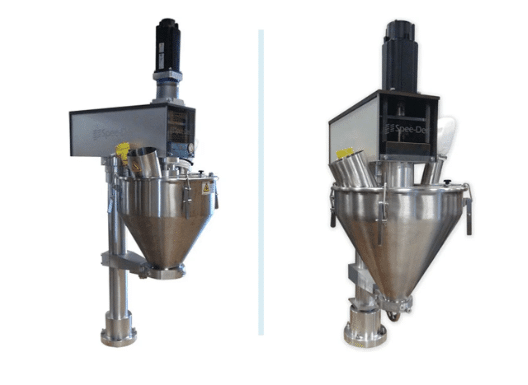
.
Technology | Pros | Cons | Suitable Industries |
Optical Counting | High accuracy, reduces product giveaway | Costly, requires regular maintenance and calibration | Cannabis (precise dosing), high-value products |
Checkweighers | Ensures weight consistency, high-speed operation | Less precise for small batches, requires maintenance | Nutraceutical (exact dosages), high-speed operations |
Vibratory Fillers | Flexible, handles irregularly shaped gummies | Less precise, slower for large-scale operations | Confectionary (varied shapes and sizes) |
Auger Fillers | Accurate for specific shapes and products | Not ideal for irregularly shaped gummies | Mixed-use production environments, granular products |
.
The Advantages of Opting for Fully Automated Gummy Packaging Machines
There are compelling reasons to choose fully automated gummy packaging machines:
- Efficiency: These machines efficiently manage large batches of gummies with minimal human input, increasing production rates.
- Uniformity: They guarantee consistent quality by ensuring each package is evenly filled by weight and quantity.
- Cost Savings: Despite a steeper initial cost, the reduction in labor and decrease in wasted products prove economically beneficial over time.
- Growth Ready: These systems are designed to grow with your business, easily adjusting to higher production needs.
- Cleanliness: They minimize human contact, thus lowering the risk of contamination and keeping hygiene standards top-notch.
Especially in sectors like cannabis and nutraceuticals, where adherence to regulations and maintaining product integrity are crucial, these machines deliver superior control and traceability, setting your business apart in these competitive fields.
.
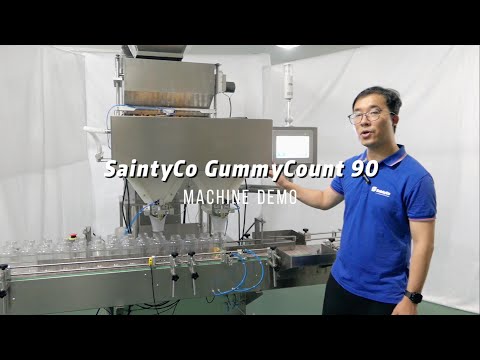
.
Critical Considerations for Choosing a Gummy Packaging Machine
Picking the right gummy packaging machine involves several vital factors:
- Performance: Make sure it can handle your production needs while maintaining quality.
- Versatility: It should support various packaging sizes and types, catering to diverse market demands.
- User-Friendly: An intuitive interface cuts down on training time and reduces chances for errors.
- Support and Upkeep: Local support and accessible spare parts are essential to keep your operations running smoothly.
- Compliance: To fulfill regulatory demands, it should meet relevant standards such as ISO 9001:2015, cGMP/GMP, UL, CE, and FDA.
- Integration: The machine should mesh well with your current production setup, ensuring a smooth workflow.
- Precision: It must feature precise measuring tools to maintain consistency across products.
- Longevity: Designed for durability, the machine should withstand the rigors of continuous use.
- Flexibility: It ought to adjust to different product sizes and packaging styles.
- Safety: Prioritize built-in safety features to safeguard operators and uphold cleanliness.
- Automation: Look for sophisticated control systems that simplify monitoring and operation.
When it comes to automation in gummy packaging, it's not just about what your machine does; it's about setting the stage for growth, quality, and efficiency. Make sure your choice ticks all these boxes to keep your production sweet and streamlined!
.
Sample Checklist for Buyers
To assist further, here’s a sample checklist of questions to ask potential suppliers:
- What is the machine’s production speed and throughput?
- Can the machine handle different types of packaging formats?
- Is the machine easy to operate and has a user-friendly interface?
- What kind of maintenance support is available locally?
- Are spare parts readily available, and what is their average lead time?
- Does the machine have the necessary certifications to comply with industry standards?
- Can the machine integrate with existing production lines?
- What are the critical safety features of the machine?
- How precise is the machine’s weighing or counting mechanism?
- What is the total cost of ownership, including maintenance and energy consumption?
.
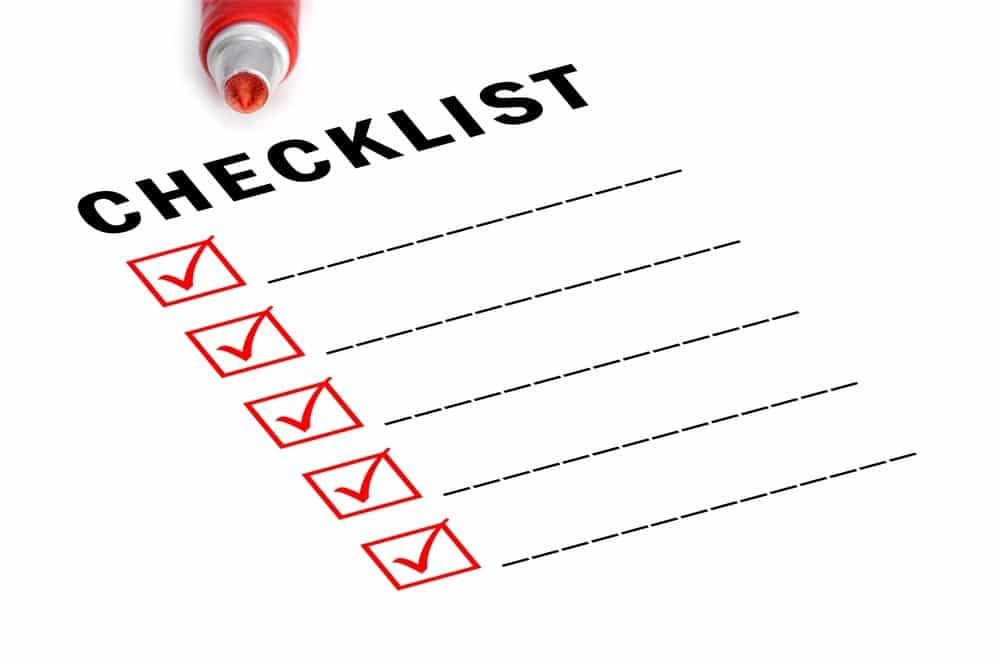
How to Find the Best Gummy Packaging Machine Suppliers
Securing a dependable supplier is key to acquiring a top-notch packaging machine. Here’s how you can ensure you’re choosing the best:
- Dive Into Research and Seek Out Reviews: Scout for suppliers that shine with stellar reviews and a solid reputation. Dive into industry forums or ask peers in the confectionary, cannabis, or nutraceutical fields for their go-to recommendations.
- Search Online and Social Media: Use Google Search, LinkedIn, and YouTube, etc. to find suppliers. High rankings and visibility indicate an active, market-oriented business.
- Attend Trade Shows: Nothing beats seeing the machines firsthand and shaking hands with the suppliers. Make your way to leading trade shows like Pack Expo (USA), Interpack (Germany), ProSweets Cologne (Germany), MJBizCon (USA), SupplySide West (USA), and SupplySide East (USA). These gatherings are gold mines for evaluating various suppliers and spotting cutting-edge technologies.
- Check for Certifications: Confirm that the supplier’s machinery meets stringent industry standards. Request evidence of compliance with ISO, cGMP/GMP, CE, UL, and FDA regulations to ensure quality and safety.
- Ensure Local Support: Choose suppliers offering local maintenance and repair support. Suppliers with local offices or authorized service centers provide quicker and more reliable support.
- Evaluate Transparent Communication: Reliable suppliers should be responsive and transparent about their products and services. Ensure that communication is clear and consistent throughout the purchasing process.
- Communicate via Phone or Video: Engage in phone or video calls to assess the supplier's professionalism and responsiveness. This method is more efficient and genuine than email alone.
- Verify Local References: Utilize local market references and success stories to gauge the supplier's reliability and performance. Ask the supplier for case studies or references from businesses similar to yours.
- Seek Comprehensive Training and Support: Look for suppliers who offer extensive training and after-sales support. This is especially valuable for entry-level buyers who need extra guidance during setup and operation.
- Request Machine Demonstrations: Consider suppliers that provide machine demonstrations. Check if they can test your gummy samples on their packaging machines to ensure the equipment meets your needs.
By following these steps, you can confidently select a supplier that will meet your needs and help ensure the success of your gummy packaging operations.
.
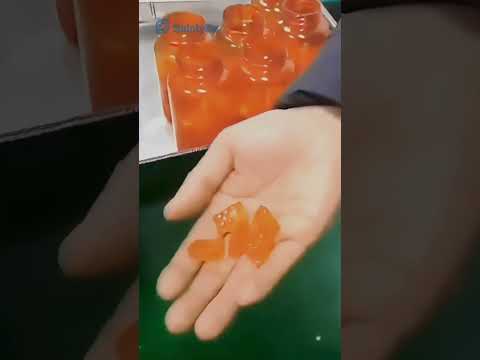
.
Summary
Selecting the ideal gummy packaging machine is pivotal—it directly influences your production speed and the caliber of your product. By familiarizing yourself with different packaging options, cutting-edge technologies, and essential factors, your decision will be well-informed. Opting for fully automated machines is wise due to their effectiveness and uniformity. Additionally, prioritize attributes like speed, adaptability, and available support when choosing your equipment. Partnering with a dependable supplier is key to ensuring ongoing operational success.
This comprehensive guide aims to simplify your journey in choosing the right gummy packaging machine. Should you need additional help, don't hesitate to contact us at GummyGenix by SaintyCo for specialized advice and support designed for your unique requirements. We provide various packaging solutions tailored to diverse sectors, including confectionary, cannabis, and nutraceuticals, helping you discover the ideal fit for your enterprise.
.
.
Contact GummyGenix for Expert Assistance
At GummyGenix by SaintyCo, we understand the complexities of selecting the perfect gummy packaging machine. Our team is ready to assist you with personalized recommendations based on your specific needs. Reach out to us for:
- Expert Advice: Our experienced professionals will guide you through the selection process.
- Customized Solutions: Tailored packaging solutions that align with your production goals.
- After-Sales Support: Comprehensive training and ongoing support to ensure smooth operation.
- Compliance Assurance: Equipment that meets all necessary regulatory standards.
.
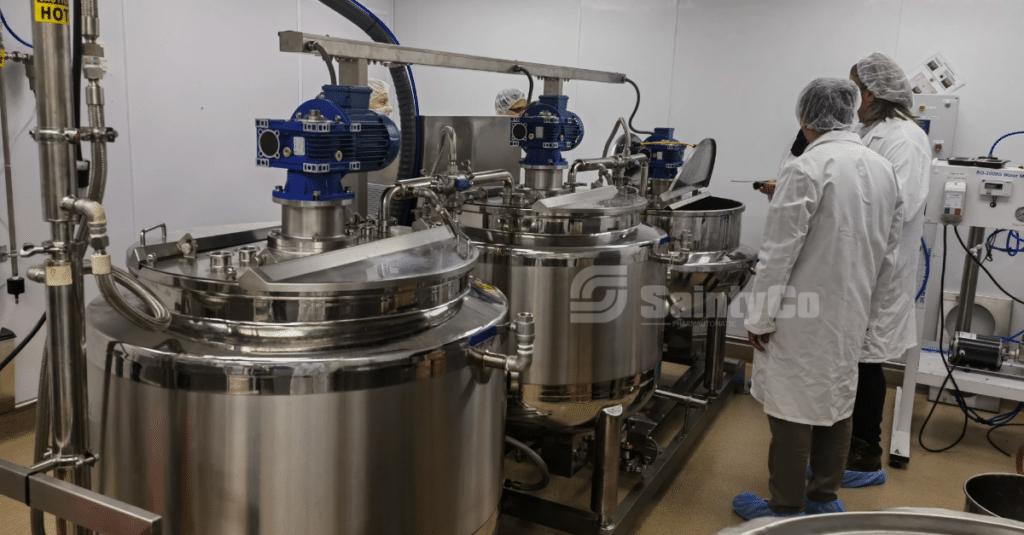
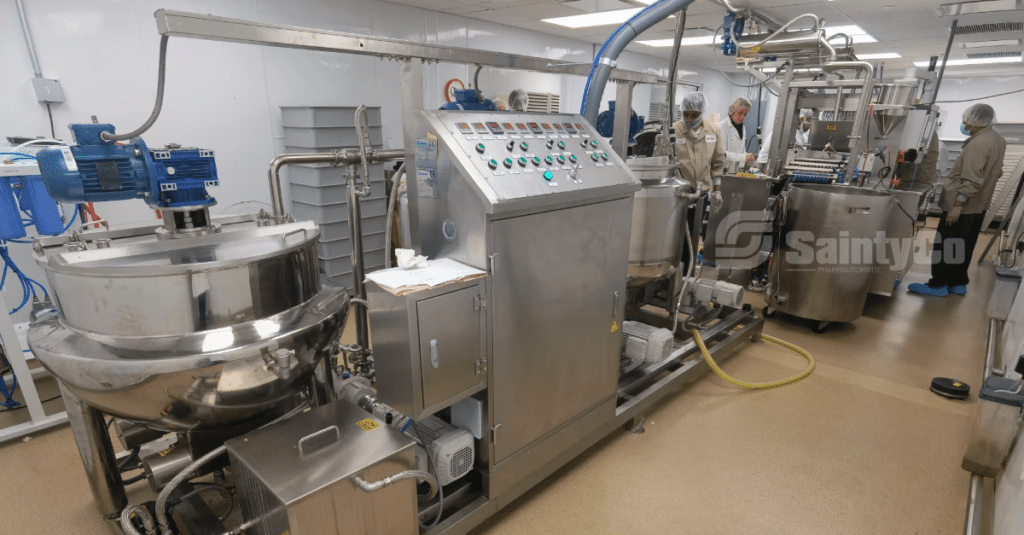
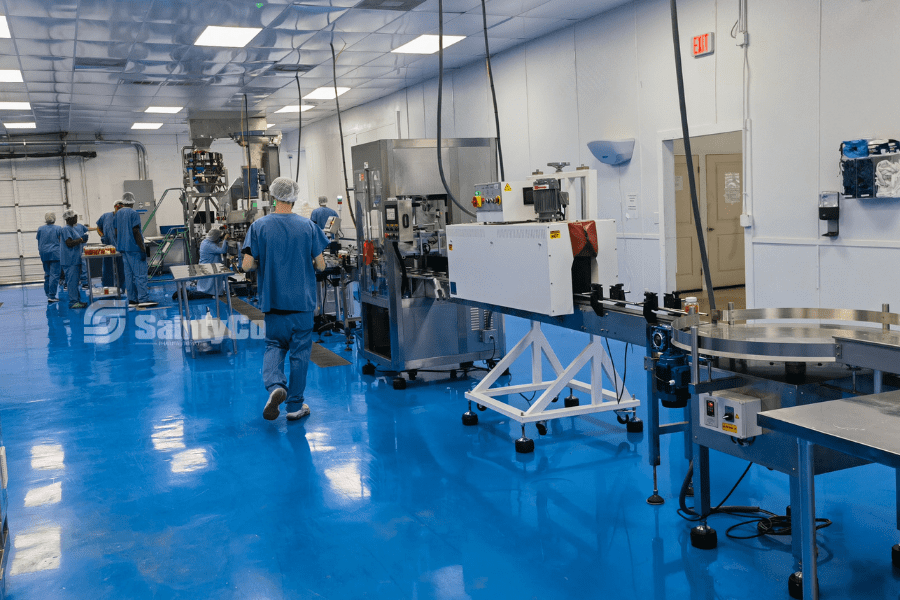
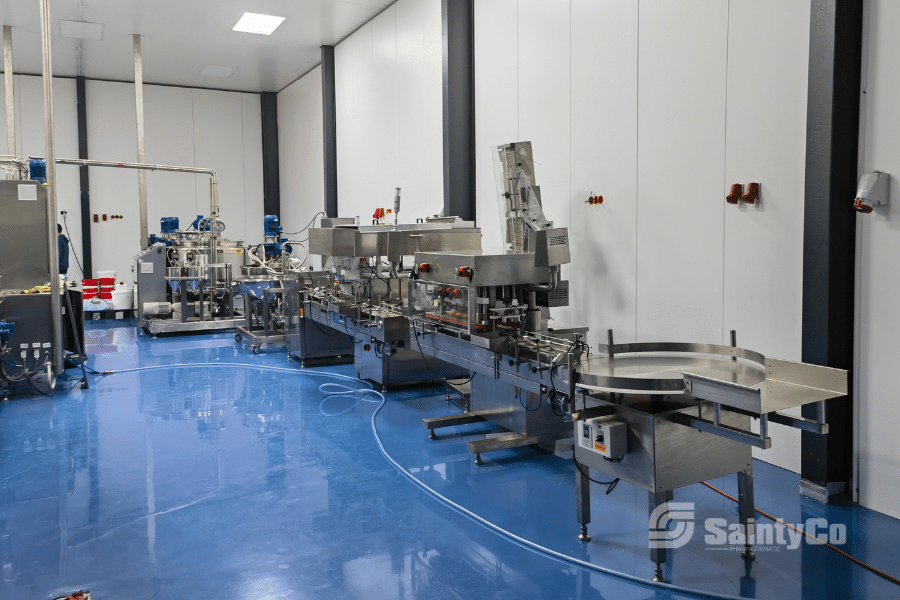
For more information, contact us at GummyGenix by SaintyCo or visit our website.
.
.
Enhance your gummy production with the right packaging machine. Let GummyGenix by SaintyCo be your trusted partner in achieving operational excellence and product quality.