Setting up a gummy manufacturing business in Peru involves more than just great recipes. You need to navigate complex regulatory waters and choose the right machinery to ensure efficiency and compliance.
To start a gummy manufacturing business in Peru, adhere to local health standards set by DIGESA, ensure machines meet food-grade material requirements, and select equipment based on production scale and product type.
While these initial steps provide a solid foundation, delving deeper into each aspect can significantly enhance your production's success and scalability. Let's explore further to ensure every piece fits perfectly into your business puzzle.
DIGESA sets health standards for gummy production in Peru.True
DIGESA is the regulatory body responsible for health standards in Peru.
All machinery must use non-food-grade materials.False
Machines must use food-grade materials to comply with safety standards.
How Does DIGESA Influence Gummy Manufacturing Compliance in Peru?
DIGESA, a Peruvian regulatory body, is pivotal in ensuring that gummy manufacturing aligns with local health and safety standards. Understanding its role can help manufacturers maintain compliance and enhance product quality.
DIGESA oversees gummy manufacturing compliance by enforcing health and safety standards specific to Peru. This includes ensuring the use of food-grade materials, hygienic machine designs, and adherence to environmental regulations.
Understanding DIGESA's Role
DIGESA, or Dirección General de Salud Ambiental e Inocuidad Alimentaria, is responsible for regulating food safety and environmental health in Peru. For gummy manufacturers, this means strict adherence to local health standards1. These regulations ensure that gummies produced are safe for consumption and meet quality expectations.
Key Compliance Areas
-
Material Standards
Gummy Manufacturing Equipment used in production must be constructed from food-grade materials like 304 or 316 stainless steel to prevent contamination. This ensures that machinery aligns with DIGESA's regulations for hygienic design.
-
Validation Protocols
For functional gummies such as those containing CBD or vitamins, IQ/OQ validation protocols may be necessary. This is particularly important for maintaining pharmaceutical-grade standards.
-
Environmental Regulations
Gummy Manufacturers must comply with waste management and emissions controls as dictated by Peru's Ley General del Ambiente. Ensuring minimal environmental impact is crucial for maintaining operational approval by DIGESA.
Importance of International Certifications
While DIGESA focuses on local compliance, international certifications like FDA, CE, and ISO 9001:2015 enhance a company's credibility. These certifications demonstrate a commitment to global quality standards, facilitating smoother market entry and consumer trust.
Certification | Significance |
---|---|
FDA | Ensures compliance with US standards |
CE | Indicates conformity with European safety standards |
ISO 9001:2015 | Demonstrates quality management system standards |
Impact on Import and Machine Selection
Machines imported to Peru must meet specific requirements, including local voltage standards and providing manuals in Spanish. This eases the integration of new machinery into gummy candy production lines and ensures compliance with Peruvian regulations2.
Understanding these factors allows gummy manufacturers to align their processes with DIGESA requirements effectively, ensuring both local and international success.
DIGESA mandates food-grade materials in gummy production.True
DIGESA requires equipment to be made from 304 or 316 stainless steel.
International certifications are irrelevant for Peruvian compliance.False
Certifications like FDA and ISO enhance credibility and market entry.
What Certifications Should Your Gummy Production Machinery Have?
Navigating the certifications required for gummy production machinery is crucial for quality assurance and regulatory compliance. Ensuring your equipment meets these standards can safeguard your investment and facilitate market entry.
Gummy production machinery should ideally have certifications like ISO 9001:2015 for quality management, CE for safety standards, and FDA compliance for food safety. These certifications ensure adherence to both international and local regulations.
G150 Gummy Production Machine | Brand Name: SaintyCo | Click to Learn More
Understanding Key Certifications
When it comes to choosing gummy production machinery, several certifications3 are essential. First, the ISO 9001:2015 certification ensures the machinery aligns with international quality management standards. This certification indicates that your equipment manufacturer follows stringent quality processes, reducing the risk of defects.
CE Marking for Safety
The CE Marking is crucial for machinery safety. This European certification confirms that the equipment meets necessary health, safety, and environmental protection requirements. It’s vital if you’re planning to operate in or export to the European Union.
Certification | Purpose |
---|---|
ISO 9001:2015 | Quality Management |
CE | Safety Standards |
FDA | Food Safety |
FDA Compliance
For those in the food industry, FDA compliance ensures that machinery is safe for food processing. This certification is particularly important if you plan on selling products in the U.S. market.
Other Relevant Certifications
Beyond these primary certifications, there are additional ones like cGMP (Current Good Manufacturing Practices) and UL (Underwriters Laboratories) standards. The cGMP4 certification is crucial for pharmaceutical-grade production, while UL focuses on electrical safety. Ensure your equipment adheres to local voltage requirements, such as 220V/50Hz if operating in Peru.
- ISO 22000 - Specific to food safety management systems.
- UL Certification - Ensures electrical safety of machinery components.
To further explore certification requirements5, consider consulting with regulatory bodies or industry experts. Ensuring that your machinery holds these certifications not only facilitates compliance but also boosts consumer confidence in your brand.
ISO 9001:2015 ensures machinery quality management.True
ISO 9001:2015 certification aligns with international quality standards.
CE Marking is only required in the United States.False
CE Marking is necessary for equipment in the European Union.
Which Machines Suit Different Production Scales for Gummies?
Finding the right machinery for gummy production is crucial for efficiency and quality. But how do you choose the best equipment for different production scales?
Machines vary by production scale: small-scale setups use semi-automatic units, medium operations benefit from fully automated lines, while large-scale facilities require high-capacity machines. Each setup ensures optimized output and cost-efficiency.
Small-Scale Production
For artisanal or startup ventures, semi-automatic machines like the DM-20S or DM-50X servo driven gummy depositors are ideal. They deliver outputs of 6,000 to 18,000 gummies per hour, perfect for limited batches. These machines often feature compact designs, making them easy to fit in smaller spaces. A critical aspect of choosing these machines is their ability to maintain quality without significant financial investment.
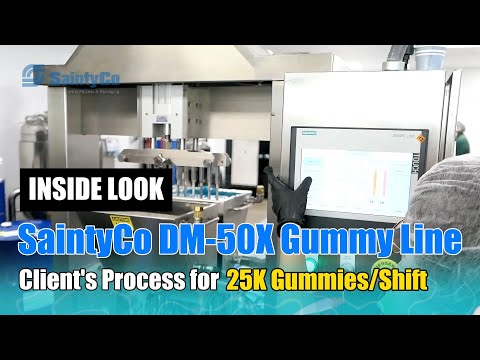
Watch this client video showcasing gummy production with SaintyCo's DM-50X Gummy Depositor in action!
Medium-Scale Production
When scaling up, consider fully automated lines such as the G40 or G80 gummy production line. These machines handle 15,000 to 30,000 gummies per hour, balancing increased capacity with manageable costs. A significant advantage here is the reduced need for manual intervention, which increases consistency and reduces labor costs.
Machine Model | Output (Gummies/Hour) | Features |
---|---|---|
DM-20S | 6,000 | Compact, semi-automatic |
DM-50X | 18,000 | Versatile, semi-automatic |
G40 | 15,000 | Fully automated |
G80 | 30,000 | High efficiency |
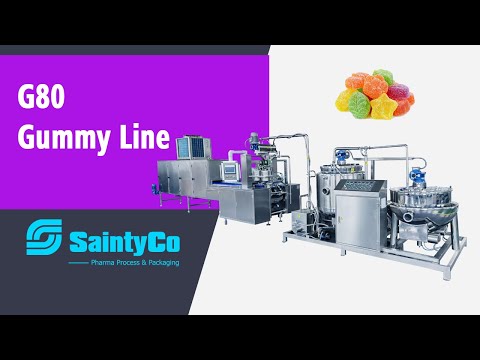
Watch this video showcasing SaintyCo's G80 Gummy Production Line in action!
Large-Scale Production
For enterprises targeting massive distribution, machines like the G300 gummy production line or G800X are necessary. These can produce up to 240,000 gummies per hour. Such machines require substantial initial investment but offer unmatched production rates and reliability. They are essential for meeting large market demands efficiently.
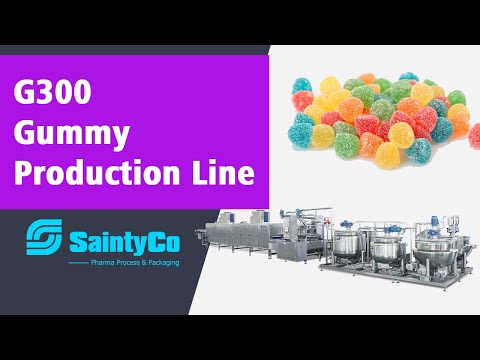
Watch this video showcasing SaintyCo's G300 Gummy Production Line in action!
Machine Capabilities and Product Types
Selecting the right machine also depends on the gummy type. Machines designed for pectin-based gummies6 ensure quality in gelatin-free production. Equipment must handle multi-color, center-filled, or sugar-free variants to meet diverse consumer preferences. A versatile machine can adapt to various recipes without compromising quality.
Auxiliary Equipment and Facility Needs
Supporting equipment like the CW-600 Oil Coating Drum helps apply protective layers to gummies, enhancing shelf life. Efficient drying processes utilize self-stacking trays and dollies. For packaging, choose fully automatic solutions such as flow-pack or bottling machines to complement high-output lines. Ensure your facility has adequate space and controlled environments, essential for maintaining product integrity.
Preparing for Future Expansion
Modular systems like the All-in-One Production Line7 offer scalability without significant additional investments. This approach allows businesses to grow organically while keeping overheads low.
Navigating Compliance and Certifications
Machines should meet international certifications such as FDA and CE, ensuring compliance with safety and quality standards. This is crucial for global market entries and maintaining consumer trust.
By understanding these elements, businesses can select machinery tailored to their specific needs and goals, ensuring efficient and profitable operations in the gummy industry. Implementing these strategies supports not just production goals but also aligns with long-term business growth plans.
DM-20S produces 6,000 gummies per hour.True
The DM-20S is a semi-automatic machine designed for small-scale production.
G800X is ideal for medium-scale production.False
The G800X is suited for large-scale production, not medium-scale.
How Can Facility Layout Affect Gummy Manufacturing Efficiency?
Optimizing your gummy manufacturing facility layout can significantly boost efficiency, streamline production processes, and reduce costs. Discover how strategic design choices influence operations and maximize productivity.
Facility layout affects gummy manufacturing efficiency by optimizing workflow, reducing movement, and improving equipment accessibility. Efficient layouts minimize bottlenecks and enhance production speed, crucial for meeting market demand in gummy production.
The Role of Workflow in Facility Layout
An efficient workflow is pivotal for any manufacturing process, especially in gummy production. By organizing equipment logically, manufacturers can ensure a smooth flow from raw material processing to final packaging. For instance, placing the cooking unit near the depositing machine reduces transport time, thus increasing production speed. Efficient layouts reduce unnecessary movement, thereby minimizing delays.
Equipment Accessibility and Maintenance
A well-planned layout ensures easy access to all machinery, facilitating regular maintenance and reducing downtime.
This approach helps maintain consistent production levels. Additionally, placing machines in an easily accessible configuration enables quick repairs, reducing the risk of extended shutdowns.
Machine Type | Recommended Placement | Benefits |
---|---|---|
Cooking Unit | Close to raw material storage | Reduces transport time |
Depositing Machine | Near cooking unit | Streamlines transition |
Cooling Tunnel | Adjacent to depositing machine | Efficient cooling process |
Packaging Line | End of production line | Smooth final product transition |
Minimizing Bottlenecks with Strategic Layouts
Bottlenecks can severely impact production efficiency. Identifying these areas and designing layouts that alleviate pressure points can dramatically increase throughput. For example, incorporating adequate space for drying trays ensures that gummy bears move smoothly through each phase without interruptions.
Planning for Flexibility and Expansion
Designing with future growth in mind is crucial. Modular layouts allow for easy expansion without significant disruption to ongoing operations. This flexibility is particularly beneficial in rapidly growing markets like CBD gummy production. Modular systems8 offer scalable solutions that accommodate increasing demand without large-scale investment.
Strategically planning facility layout not only enhances current operational efficiency but also positions a business for future growth. By considering factors such as workflow optimization, equipment accessibility, and modular design, gummy manufacturers can stay competitive in a dynamic market.
Facility Layout Optimization9 is essential for maximizing output while maintaining quality standards. This balance ensures that manufacturers meet both market demand and quality expectations effectively.
Efficient layout reduces gummy production delays.True
Organizing equipment logically minimizes unnecessary movement and delays.
Placing machines far apart improves gummy production speed.False
Machines should be placed close to reduce transport time and increase speed.
Conclusion
Starting a gummy manufacturing business in Peru requires compliance with DIGESA health standards, selecting food-grade machinery, and understanding production scales for efficient operations.
At GummyGenix by SaintyCo, we're here to support your journey with cutting-edge, GMP-compliant gummy manufacturing equipment designed for efficiency, precision, and adaptability. Our machines are fully compatible with regulatory standards, and we offer reliable after-sales support to keep your operations running smoothly.
Contact GummyGenix by SaintyCo to explore how our machinery and expertise can enhance your production line. Let’s bring your vision of quality gummy products to life—together.
-
Learn about specific local health regulations enforced by DIGESA to ensure your manufacturing processes align with Peruvian requirements. ↩
-
Discover essential import guidelines to ensure your equipment complies with Peruvian standards, facilitating seamless production operations. ↩
-
Learn about various essential certifications for gummy manufacturing machinery. ↩
-
Understand how cGMP standards affect gummy production quality and compliance. ↩
-
Discover methods to ensure your gummy production equipment's certifications are valid. ↩
-
This link provides insights into why pectin-based gummies are preferred for specific dietary needs and market trends. ↩
-
This link explores how modular systems enable easy scaling of gummy production, saving costs and resources. ↩
-
Explore how modular systems enable scalable production solutions without large-scale investments. ↩
-
Discover effective strategies for optimizing facility layout to enhance manufacturing efficiency. ↩