Are you looking to produce gummy candies in your restaurant?
When selecting a small gummy-making machine for your restaurant, consider factors like production volume, space, customization options, ease of use, budget, and after-sales support. This guide will help you navigate these key considerations and choose the best gummy equipment for your needs.
In this blog post, we will delve deeper into each consideration and explore various machine options that suit different restaurant operations. Let's ensure you find the perfect gummy-making solution!
Small gummy-making machines are ideal for restaurants.True
These machines can efficiently produce gummies, enhancing menu offerings for restaurants.
Production volume is irrelevant when choosing gummy machines.False
Considering production volume is crucial to meet demand and operational efficiency.
What Should You Consider Regarding Production Volume?
Production volume is a critical factor that influences many aspects of gummy manufacturing. Understanding what to consider can significantly impact your operational success.
When considering production volume for gummies, evaluate market demand, operational costs, quality control, and equipment flexibility to align with your business goals.
Understanding Production Volume Needs
Determining the right production volume is crucial for any gummy-making operation. It directly impacts your costs, efficiency, and overall business strategy. Consider the following factors:
-
Market Demand: Assess the demand for your gummies. If you expect high sales volumes, investing in a high-output machine may be necessary. Conversely, if you plan to produce small batches, a lower-output machine will suffice.
-
Operational Costs: Higher production volumes can lead to cost savings per unit. However, this comes with increased initial investment in machinery. Evaluate the balance between fixed and variable costs to find the most cost-effective solution.
-
Quality Control: With increased volume comes the challenge of maintaining consistent quality. Establish processes that ensure quality checks at various stages of production to avoid costly recalls or waste.
-
Flexibility: Your production volume should allow for flexibility in your product offerings. Can your machine adapt to produce different flavors or shapes? This flexibility can help capture diverse market segments.
Evaluating Equipment Based on Volume
When selecting equipment, consider how each machine aligns with your production goals. Here’s a quick comparison of GummyGenix by SaintyCo Automatic Gummy Depositors:
Machine Model | Output (kg/hour) | Ideal For | Key Features |
---|---|---|---|
DP-10S | 10-15 | Small-scale operations | Compact, easy to use, flexible mold options |
DM-20S | 20-30 | Mid-volume production | 2-in-1 functionality, customizable options |
DM-50X | 50 | High-volume production | Automated conveyor system, labor-saving features |
Choosing the right equipment based on production volume can maximize efficiency and align with your operational goals. You want to avoid bottlenecks that can arise from underestimating demand or overcommitting resources.
Long-term Production Strategy
It is important to think long-term. Will your production volume change? As your business grows, can your current gummy manufacturing equipment scale with it? Look for gummy machines that not only meet your current needs but also have the potential for upgrades or expansions in capacity.
- Scalability: Evaluate whether your machinery can handle increased production needs without requiring complete replacement.
- Future Trends: Stay informed about trends in gummy products. For example, CBD gummies are gaining popularity. Your ability to adapt to these trends might depend on your production capacity.
For detailed guidance on scaling production based on market trends, check out market trends for gummies1.
Conclusion
Finding the right production volume for gummy manufacturing involves analyzing various aspects like market demand, operational costs, and flexibility of equipment. By making informed decisions, you can ensure that your operations remain efficient and profitable as you grow.
High production volume reduces unit costs in gummy making.True
Higher production volumes can lead to economies of scale, reducing the cost per unit produced, which is vital for profitability.
Quality control becomes easier with increased production volume.False
As production volume increases, maintaining consistent quality often becomes more challenging due to scale, requiring robust quality checks.
How Does Space and Portability Affect Your Machine Choice?
Choosing the right machine requires careful consideration of space and portability factors. Let us explore how these aspects impact your decision-making process.
Space and portability are crucial when selecting a machine. Compact machines are ideal for limited spaces, while larger machines offer higher outputs but require dedicated areas. Understanding these trade-offs helps you choose the right equipment for your needs.
The Importance of Space in Machine Selection
When selecting a machine, the amount of available space is crucial. Compact machines are beneficial for small kitchens or facilities.
They can fit into tighter areas while still delivering adequate output. For example, a compact gummy depositor2 like the SaintyCo DP-10S tabletop servo-driven universal depositor operates efficiently in limited spaces, making it ideal for startups.
On the other hand, larger machines, such as the DM-50X Servodose Mini Depositor, require dedicated areas but offer higher production capabilities.
Here’s a quick comparison:
Machine Model | Size | Output | Best For |
---|---|---|---|
DP-10S Depositor | Compact | 10-15 kg/h | Small kitchens |
DM-20S Depositor | Medium | 20-30 kg/h | Medium-sized restaurants |
DM-50X Depositor | Large | 50 kg/h | Large-scale operations |
Portability: A Key Factor
Portability influences how easily a machine can be moved or stored.
For restaurants that need flexibility, a portable machine like the SaintyCo DP-10S tabletop depositor allows for quick relocation when necessary. This means you can adjust your setup depending on events or busy periods.
Conversely, large machines are typically less portable but are designed for high-output production.
Consider this:
- Portable Machines: Ideal for variable production needs and limited space.
- Stationary Machines: Better for consistent high-volume production with dedicated setups.
Trade-offs Between Performance and Usability
When assessing machines, there's often a trade-off between performance and usability based on space and portability.
Compact models may not offer the same output as larger machines but excel in ease of use and setup.
For instance, the SaintyCo DM-20S 2-in-1 Lab Scale Depositor provides a balance between size and output, making it suitable for mid-sized operations that need both versatility and efficiency.
Deciding on the right machine involves evaluating your specific needs against these trade-offs:
- Output Requirements: Higher demands may necessitate larger, less portable machines.
- Space Constraints: Limited areas will benefit from compact, portable solutions.
- Operational Flexibility: Consider how often you might need to move the equipment.
Final Thoughts on Space and Portability
Ultimately, understanding how space and portability affect your machine choice is essential in making an informed decision.
Evaluating your production needs, workspace limitations, and the desired flexibility will lead you to the most suitable option for your restaurant or business.
Compact machines are ideal for small kitchens.True
Compact machines fit well in limited spaces, making them suitable for small kitchens or offices where space is a concern.
Larger machines are more portable than compact ones.False
Larger machines typically lack portability, as they require dedicated setups and are harder to move compared to compact models.
Why is Customization Important for Your Gummy Production?
Customization in gummy production is vital for standing out in a crowded marketplace. It enables businesses to create unique products tailored to consumer preferences.
Customization is crucial for gummy production as it differentiates products, engages consumers, and boosts sales. Tailoring flavors and shapes attracts specific markets and enhances brand loyalty.
Understanding Customization in Gummy Production
Customization in gummy production allows businesses to create unique products that stand out in a competitive market. By tailoring flavors, shapes, and nutritional benefits, companies can cater to specific consumer preferences, thus enhancing brand loyalty.
For example, a restaurant might offer gummy vitamins or CBD-infused options, tapping into health trends. This not only attracts health-conscious customers but also diversifies the product range, maximizing profit potential.
Benefits of Customization
Customization provides several advantages:
- Market Differentiation: In a saturated market, having unique products can set you apart. Businesses that offer specialized gummies can draw in customers looking for something different.
- Consumer Engagement: Engaging consumers through customization invites feedback. This can lead to innovative product ideas and greater customer satisfaction.
- Flexibility in Production: Machines that support various molds and ingredient formulations allow for easy adjustments in production, enabling quick shifts to meet market demands.
For instance, a restaurant could quickly pivot from fruit gummies to gourmet flavored options based on seasonal trends, enhancing their menu's appeal. More information on this topic can be found here3.
Factors Influencing Customization Choices
When considering customization, businesses should evaluate:
- Production Capacity: Machines with flexible configurations can adapt to varying batch sizes and specifications.
- Cost Considerations: While investing in versatile equipment may seem high initially, it can yield long-term savings through reduced waste and increased sales from customized offerings.
- Market Trends: Staying updated with consumer preferences allows businesses to create gummies that resonate with current trends, such as vegan or organic products.
Practical Implementation of Customization
To successfully implement customization in gummy production, consider these steps:
- Research Consumer Preferences: Conduct surveys or focus groups to understand what flavors and types of gummies customers want.
- Invest in Versatile Machinery: Equipment like the DM-20S allows for quick changes in molds and formulations, making it easier to test new products.
- Utilize Seasonal Ingredients: Incorporating local or seasonal ingredients not only enhances flavors but also supports local producers. This strategy can attract eco-conscious consumers looking for sustainable options.
Examples of Customized Gummies
Type of Gummy | Customization Options | Market Appeal |
---|---|---|
Fruit Gummies | Varied flavors, organic ingredients | Kids, families |
CBD Gummies | Different dosages, flavors | Health-conscious adults |
Vitamin Gummies | Tailored formulations for specific needs | Health and wellness sector |
Gourmet Gummies | Unique shapes, upscale ingredients | Gourmet food enthusiasts |
By understanding these factors and implementing effective strategies, businesses can harness the power of customization. This approach not only meets diverse consumer demands but also drives innovation in gummy production. For more insights on optimizing your gummy production process, check out this guide.
Customization enhances brand loyalty in gummy production.True
Tailoring products to consumer preferences fosters a deeper connection, leading to increased brand loyalty and repeat purchases.
Unique gummy shapes attract more customers than standard ones.True
Offering distinctive shapes differentiates products in a saturated market, appealing to consumers seeking novelty and uniqueness.
What Makes a Gummy-Making Machine Easy to Use and Clean?
When it comes to gummy-making machines, usability and cleanliness are paramount. Discover what features make these machines user-friendly and easy to maintain.
Gummy-making machines are designed for ease of use and cleaning. Look for features like intuitive interfaces, quick disassembly, hygienic materials, and compact designs to ensure efficient operation in your production process.
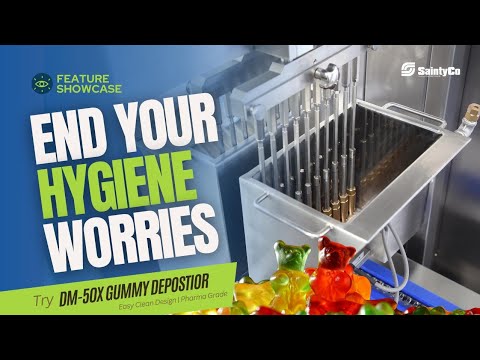
Watch this client video showcasing SaintyCo DM-50X Gummy Depositor: cGMP Compliant, Gummy Production Game-Changer!
User-Friendly Design
The ease of use of gummy-making machines often stems from their user-friendly design. Most modern machines feature intuitive interfaces with clear buttons and displays. This helps operators quickly learn how to operate them. For example, machines with touch screens can provide guided prompts for setup and operation. This reduces the need for extensive training, allowing new staff to get up to speed faster.
Additionally, machines that are designed for simple assembly often come with pre-set programs that can be easily adjusted to fit different production needs. This means less time fiddling with settings and more time focused on production.
Quick Assembly and Disassembly
A significant factor in ease of cleaning is how quickly a machine can be disassembled. Machines designed with user convenience in mind typically allow for rapid assembly and disassembly. Look for models with snap-on or click-in components, which make it easy to remove parts without tools.
For instance, a machine that features detachable molds and hoppers can simplify the cleaning process. Components can be rinsed and sanitized quickly, ensuring hygiene standards are met without wasting time.
Hygienic Materials and Design
The materials used in gummy-making machines play a crucial role in their cleanliness and maintenance. Stainless steel is a preferred choice due to its non-porous nature, which prevents bacteria from harboring on surfaces. Moreover, machines that are designed with smooth surfaces minimize crevices where residues can accumulate.
Maintenance Features
Regular maintenance is essential to keep gummy-making machines running efficiently. Some machines come equipped with features that simplify maintenance tasks. For instance, automatic lubrication systems reduce manual upkeep by providing consistent lubrication to moving parts. This not only prolongs the life of the machine but also ensures smoother operation.
Compact Footprint and Portability
In addition to ease of use and cleaning, the physical size and portability of a gummy-making machine can influence its usability in a busy kitchen environment. Compact models occupy less space, making them easier to maneuver and store when not in use.
Here’s a table summarizing key features that contribute to the ease of use and cleaning of gummy-making machines:
Feature | Benefits |
---|---|
User-Friendly Design | Intuitive interfaces for quick learning |
Quick Assembly/Disassembly | Fast setup and cleaning processes |
Hygienic Materials | Prevents bacteria growth, easy to sanitize |
Maintenance Features | Reduces manual upkeep, enhances longevity |
Compact Footprint | Saves space, improves mobility |
For more insights on selecting the right gummy-making machine, check out this comprehensive guide4.
Gummy-making machines with touch screens require no training.True
Touch screens offer guided prompts, making operation intuitive and reducing the need for extensive training for new users.
Stainless steel is the best material for gummy machines.True
Stainless steel is non-porous, preventing bacteria growth and ensuring easy cleaning, making it ideal for gummy-making machines.
How Do You Balance Budget with Long-Term Benefits?
Balancing a budget with long-term benefits is crucial for sustainable growth. It requires strategic planning that considers both immediate needs and future goals. Here's how to achieve that balance.
To balance a budget with long-term benefits, prioritize strategic investments, evaluate trade-offs, leverage technology for efficiency, and regularly review your financial strategies to ensure sustainable growth.
Understanding the Importance of Budget Balance
Balancing a budget effectively requires a nuanced understanding of both immediate financial needs and future growth potentials. The process is not just about cutting costs; it involves strategic investments that can yield long-term benefits. Consider the following key factors:
-
Identifying Priorities: Prioritize spending that aligns with your business goals. For example, investing in quality machinery can reduce long-term operational costs while enhancing production capacity.
-
Evaluating Investment vs. Expense: Distinguish between essential investments and mere expenses. An investment, such as a new gummy-making machine, may appear costly initially but can lead to higher efficiency and lower labor costs over time.
-
Utilizing Financial Models: Implement financial models that project the impact of various budgetary decisions. For instance, using tools like cost-benefit analysis can help illustrate potential long-term savings from immediate expenditures on quality equipment.
Short-Term vs Long-Term Trade-offs
It's critical to recognize the trade-offs involved in budget decisions. Here are some scenarios:
Scenario | Short-Term Impact | Long-Term Impact |
---|---|---|
Investing in New Machinery | High initial cost | Increased efficiency and reduced waste |
Skimping on Quality | Low immediate expense | Higher maintenance costs and downtime |
Staff Training Investments | Temporary disruptions in workflow | Improved productivity and retention |
-
Cash Flow Management: Ensure that you have a plan for maintaining healthy cash flow while pursuing long-term investments. This might involve staging purchases or considering financing options that align with your cash flow cycles.
-
Setting Realistic Goals: Setting achievable financial goals can help guide your budgeting process. For example, aim to increase your production capacity by a specific percentage over the next year by budgeting for necessary investments now.
Leveraging Technology for Efficiency
Investing in technology can be a game changer when balancing budget with long-term benefits. Here’s how:
- Automation: Automated gummy production lines can drastically reduce labor costs and increase production speed.
- Data Analytics: Implementing data analytics tools allows businesses to track spending and optimize budgets dynamically.
- Energy-Efficient Equipment: Choosing machines that are energy-efficient can significantly lower utility costs, providing long-term savings.
For more insights on maximizing your budget through technology, explore cutting-edge solutions5.
Building a Sustainable Budgeting Framework
Creating a sustainable budgeting framework involves continual assessment and adjustment. Consider these steps:
- Regular Reviews: Regularly review budget performance against goals to identify areas needing adjustment.
- Feedback Loop: Create a feedback loop with stakeholders to ensure that budgetary decisions reflect operational realities and market conditions.
- Future-Proofing Investments: When selecting equipment, ensure that it can adapt to future market demands or production needs, thus safeguarding your investment.
Balancing budget constraints with the pursuit of long-term benefits is crucial for any successful business operation. By focusing on strategic investments and maintaining flexibility, businesses can thrive even in challenging economic climates. For further strategies on optimizing budget balance, check out expert recommendations6.
Investing in quality machinery reduces long-term operational costs.True
Quality machinery may have a high upfront cost but leads to efficiency and lower maintenance costs over time.
Skimping on quality always results in immediate savings.False
While cutting quality may save money now, it often leads to higher long-term maintenance and operational costs.
What Support and Warranty Options Should You Look For?
Choosing the right support and warranty options is essential for ensuring the longevity and efficiency of your gummy-making equipment.
When selecting gummy-making machinery, prioritize suppliers with robust support and warranty options. Look for comprehensive customer service, technical assistance, training programs, and clear warranty terms for optimal long-term benefits.
Understanding Support Options
When purchasing equipment, such as gummy-making machines, it’s crucial to consider the support options available.
Look for suppliers that offer comprehensive customer service. This includes:
- Technical Assistance: Access to knowledgeable support personnel who can help troubleshoot issues.
- Training Programs: Many suppliers provide training for your staff to ensure they can operate the machinery effectively.
- Maintenance Support: Regular check-ups and maintenance options can help prolong the life of your equipment.
- Documentation: Ensure the availability of user manuals and troubleshooting guides, which can be invaluable during operations.
You can explore more about how to choose the right support here7.
Warranty Coverage Details
Warranties vary by manufacturer but typically include:
Type of Coverage | Duration | What’s Covered |
---|---|---|
Limited Warranty | 1-2 years | Parts and labor for manufacturing defects |
Extended Warranty | Up to 5 years | Additional coverage after the limited warranty ends |
Service Contract | Varies | Regular maintenance and repairs, not necessarily tied to defects |
It is important to read the fine print to understand what is included and excluded. For more details on types of warranties available, visit this resource8.
Importance of Warranty Terms
Knowing the terms of a warranty can save you significant costs down the line. Look for:
- Transferability: If you plan to sell the equipment, a transferable warranty can increase its resale value.
- Claim Process: Understand how to file claims, including any required documentation.
- Exclusions: Be aware of what isn’t covered, such as damages due to misuse or accidents.
Read more about warranty terms here9.
Cost Implications of Warranties
When evaluating your options, consider how warranties affect overall costs:
- Initial Costs: Some warranties may increase the upfront cost of machinery.
- Long-term Savings: A good warranty may save on repair costs over time, making it a wise investment.
- Budgeting for Maintenance: Factor in potential maintenance costs not covered by warranties when planning your budget.
Explore budgeting strategies related to warranties here10.
Comprehensive customer service is essential for machinery support.True
Robust customer service ensures effective troubleshooting and assistance, crucial for maintaining equipment functionality.
Extended warranties are always more cost-effective than limited ones.False
While extended warranties offer longer coverage, they may not always be the best financial choice depending on equipment usage and reliability.
Conclusion
Learn how to select the best small gummy-making machines for your restaurant by evaluating production needs, space constraints, customization options, and budget considerations.
At GummyGenix by SaintyCo, we're here to support your journey with cutting-edge, GMP-compliant gummy manufacturing equipment designed for efficiency, precision, and adaptability. Our machines are fully compatible with regulatory standards, and we offer reliable after-sales support to keep your operations running smoothly.
Contact GummyGenix by SaintyCo to explore how our machinery and expertise can enhance your production line. Let’s bring your vision of quality gummy products to life—together.
Gummy Production Machinery from GummyGenix by SaintyCo | Click to Know More
-
Discover insights on optimizing production volume and scaling your gummy manufacturing effectively. ↩
-
This link will provide insights into the best practices for selecting machinery based on space constraints and portability needs. ↩
-
Explore how to make your gummy products and attract more customers. ↩
-
Explore various user-friendly gummy-making machines that simplify the production process, enhancing efficiency in your kitchen. ↩
-
This link offers valuable strategies for effective budgeting that combines immediate financial responsibility with long-term growth considerations. ↩
-
Discover expert insights into creating sustainable budgets that support both current operations and future investments. ↩
-
Understanding support and warranty options can help you make informed decisions and protect your investment. ↩
-
Learning about warranty coverage details can help you choose the right protection for your equipment. ↩
-
Understanding warranty terms can save you money and avoid future headaches. ↩
-
Exploring cost implications will guide your financial planning when investing in machinery. ↩