Ever wonder what makes gummy manufacturing a sticky business? It’s all about the equipment!
The cGMP requirements for gummy manufacturing equipment include hygienic design, precision dosing systems, validated processes, environmental controls, and robust documentation. Adhering to these standards ensures compliance with FDA regulations and maintains product quality and safety.
While we've uncovered the basic cGMP equipment needs, there's a lot more to chew on. Dive into the nitty-gritty details of how each component contributes to a seamless and compliant gummy production process. Get ready to explore the sweet science of staying within the lines!
Hygienic design prevents gummy contamination.True
Hygienic design ensures equipment is easy to clean, reducing contamination risks.
Quick Compliance Checklist for Gummy Manufacturing Equipment
For gummy manufacturers looking to meet cGMP and FDA compliance standards, here’s a quick checklist to ensure your equipment and processes align with industry requirements.
1. Hygienic Design
- ✅ Use FDA-compliant materials: Ensure all equipment is made from FDA-approved materials, like stainless steel (SS304 or SS316), which are corrosion-resistant and easy to clean.
- ✅ Minimize crevices and corners: Equipment should have rounded edges and smooth surfaces to reduce residue build-up and simplify cleaning.
- ✅ Implement starch-free systems: For pectin or gelatin-based gummies, starch-free systems reduce contamination risks and improve overall hygiene.
2. Precision Dosing Systems
- ✅ Calibrate dosing systems regularly: Automated dosing systems should be regularly calibrated to ensure accurate ingredient dosing, particularly for active ingredients like CBD or vitamins.
- ✅ Use PLC-controlled settings: Utilize Programmable Logic Controllers (PLCs) to maintain precise dosing consistency across batches, reducing variability and ensuring product quality.
3. Environmental Control
- ✅ Maintain temperature and humidity control: Implement systems that regulate temperature and humidity within your facility to prevent contamination and ensure product stability.
- ✅ Integrate cooling tunnels: Cooling tunnels with controlled conditions prevent melting and spoilage, preserving the texture and quality of the gummies.
- ✅ Use air filtration and ventilation systems: These systems should reduce airborne particles, dust, and contaminants in the production environment.
4. Regular Cleaning and Maintenance
- ✅ Establish a cleaning schedule: Define regular cleaning intervals for all equipment to prevent contamination. Ensure easy access points for thorough cleaning.
- ✅ Conduct preventive maintenance: Schedule routine maintenance to prevent unexpected breakdowns and maintain compliance with cGMP standards.
- ✅ Document all cleaning and maintenance activities: Keep detailed records of each cleaning and maintenance session to demonstrate compliance during audits.
5. Documentation for Traceability and Compliance
- ✅ Maintain accurate batch records: Record production details for each batch, including ingredients, dates, and operator information for full traceability.
- ✅ Create and follow Standard Operating Procedures (SOPs): Establish SOPs for all key processes (e.g., equipment cleaning, dosing calibration) to standardize operations.
- ✅ Keep quality control records: Document quality checks and testing results to ensure each batch meets the required standards.
- ✅ Integrate ERP systems: Use Enterprise Resource Planning (ERP) software to centralize and automate documentation, making it easier to manage data and track compliance in real-time.
By following these guidelines and maintaining cGMP compliance, you can safeguard product quality, enhance consumer trust, and position your business for long-term success in the competitive gummy industry.
Why is Hygienic Design Crucial for Gummy Equipment?
Ever imagined how gummy bears stay free from germs? It’s all in the design!
Hygienic design in gummy equipment is essential to prevent contamination, ensure easy cleaning, and maintain product quality. By using materials like stainless steel and minimizing crevices, manufacturers can meet stringent health standards, ensuring that your favorite gummies are safe to consume.
The Role of Materials in Hygienic Design
When it comes to crafting gummy equipment, material choice is paramount. Stainless steel, particularly grades SS304 and SS316, is the go-to for its corrosion resistance and ease of cleaning. These materials ensure that equipment can withstand rigorous cleaning protocols without degrading. Think of it as the armor protecting your favorite sweets from the bad guys of contamination.
Design Features That Matter
Rounded edges and minimal gaps aren't just aesthetic choices—they're vital for hygiene. Such designs prevent residue build-up, making cleaning a breeze. Imagine trying to clean peanut butter off a spoon; it’s much easier if the spoon has no nooks and crannies!
Starch-free systems take it a step further by reducing residue in gummy production, particularly useful for pectin and gelatin-based gummies. This not only enhances cleanliness but also boosts efficiency.
Enhanced Cleaning Protocols
With hygienic design, cleaning becomes less of a chore and more of a standard operating procedure. Equipment designed with easy access points allows thorough cleaning, reducing downtime and improving productivity.
Meeting Regulatory Standards
Hygienic design isn’t just about cleanliness; it's about compliance. Adhering to cGMP standards1 is crucial for legal compliance and consumer safety. These standards mandate specific design features that help manufacturers avoid costly recalls and maintain brand trust.
Real-World Applications
Companies using these design principles have seen fewer contamination issues and smoother audits. Imagine running a marathon with shoes that fit perfectly versus ones that are too tight—the right design makes all the difference.
Implementing these features ensures that gummy manufacturing isn't just productive but also safe and compliant. So next time you pop a gummy bear, remember the intricate dance of design and hygiene keeping it squeaky clean.
Stainless steel is crucial for gummy equipment hygiene.True
Stainless steel resists corrosion and is easy to clean, ensuring hygiene.
Rounded edges in equipment design are purely aesthetic.False
Rounded edges prevent residue build-up, enhancing hygiene and cleaning ease.
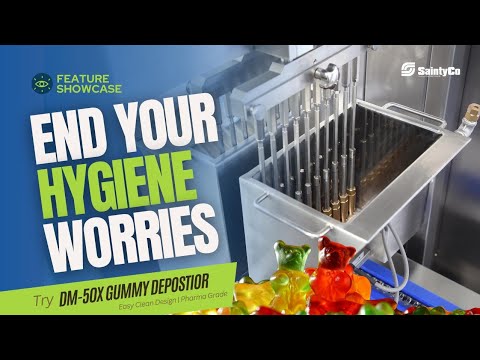
Looking for hygienic equipment that minimizes contamination risks? Schedule a demo to see GummyGenix by SaintyCo’s cGMP-compliant designs in action.
How Does Precision Dosing Impact Product Quality?
Precision dosing in gummy production is like a maestro ensuring every note hits perfectly.
Precision dosing guarantees uniform distribution of active ingredients in gummies, enhancing product quality and efficacy. This method minimizes variability and ensures each batch meets stringent quality standards, critical for consumer safety and satisfaction.
The Importance of Precision Dosing in Gummy Production
Precision dosing is the conductor that ensures each gummy gets the exact amount of active ingredients, whether it's CBD, vitamins, or minerals. This is crucial for maintaining consistent quality2 across batches and ensuring that consumers receive the intended health benefits with each bite.
Mitigating Variability for Quality Assurance
Variability is the enemy of quality. Automated dosing systems reduce variability by ensuring the precise amount of ingredients is consistently added to each batch. This consistency not only meets regulatory requirements but also builds trust with consumers who rely on the efficacy and safety of your product.
Technology Behind Precision Dosing
Advanced machinery equipped with PLC-controlled settings allows manufacturers to maintain strict control over dosing processes. This technology integrates seamlessly with recipe management systems, enabling easy adjustments without compromising product integrity. It’s like having a precise GPS guiding you to the same destination every time.
Real-World Application: A Case Study
Consider a manufacturer of vitamin gummies. By using precision dosing systems, they achieved a reduction in ingredient wastage by 15% and improved batch consistency by 20%. These improvements not only enhanced product quality but also boosted overall production efficiency.
Benefit | Impact on Production |
---|---|
Reduced Wastage | Lower production costs |
Improved Consistency | Enhanced consumer trust |
Compliance Ease | Simplified audits and regulatory checks |
Precision dosing isn't just a technical requirement; it's the secret sauce for maintaining top-notch quality in every gummy produced.
Precision dosing reduces ingredient wastage by 15%.True
A case study showed a 15% reduction in wastage using precision dosing.
Automated dosing systems increase batch variability.False
Automated systems reduce variability, ensuring consistent product quality.
What Role Does Environmental Control Play in Manufacturing?
Have you ever wondered how manufacturers keep products safe and consistent? Enter environmental control!
Environmental control in manufacturing ensures stable production conditions by regulating temperature, humidity, and cleanliness. This minimizes contamination risks, enhances product quality, and aligns with cGMP standards, safeguarding consumer safety.
The Science Behind Environmental Control
Environmental control isn't just about keeping things cool or dry; it's the backbone of consistent manufacturing. By managing temperature and humidity, manufacturers reduce microbial risks and ensure product stability. For example, cooling tunnels in gummy production maintain specific conditions to prevent melting and spoilage.
Why Temperature Matters
Temperature plays a pivotal role in manufacturing processes. It affects chemical reactions, material properties, and product quality. A slight deviation can lead to defects or contamination. In gummy manufacturing, precise temperature control ensures the gelatin or pectin sets correctly without compromising the texture or efficacy of active ingredients.
Humidity: The Silent Operator
Humidity control is equally crucial. Excess moisture can foster mold growth or degrade sensitive materials. Conversely, too little moisture can cause products to dry out or become brittle. By balancing humidity levels, manufacturers maintain optimal product quality and prolong shelf life.
Cleanliness Is Key
Beyond temperature and humidity, cleanliness standards ensure equipment functions smoothly and safely. Controlled environments minimize contamination risks by reducing airborne particles and pollutants. For instance, oil coating drums in gummy production not only apply an even layer but also protect the product from external contaminants.
Integration with Technology
Modern environmental control systems integrate with technology for seamless operations. PLC-controlled settings allow for precise adjustments, ensuring consistent conditions are maintained batch after batch. With advancements like SIEMENS TP1200 or Allen Bradley PLCs, these systems can be easily integrated with ERP solutions for comprehensive process management and data logging3.
Embracing these environmental controls isn't just about meeting regulatory needs. It's about ensuring every product that reaches consumers is safe, effective, and of the highest quality.
Temperature control prevents defects in gummy manufacturing.True
Precise temperature ensures gelatin or pectin sets correctly, preventing defects.
Humidity has no impact on product shelf life in manufacturing.False
Humidity affects shelf life by preventing mold growth and material degradation.
How Important is Documentation for Regulatory Compliance?
Ever tried baking without a recipe? That's what manufacturing without documentation feels like.
Documentation is vital for regulatory compliance as it ensures traceability, supports audits, and maintains quality standards. It involves recording procedures, tracking batch data, and storing records securely, aligning with cGMP and FDA guidelines to prevent errors and safeguard consumer safety.
The Backbone of Compliance
Imagine running a marathon without knowing the route. That's manufacturing without proper documentation4. It's not just paperwork; it's the backbone of regulatory compliance. Every step, every process, and every ingredient needs to be meticulously recorded.
Traceability: The Audit Trail
Without documentation, tracing issues in production would be like finding a needle in a haystack. Detailed logs and records are your roadmap during audits. They provide transparency, demonstrating adherence to cGMP standards. This is especially crucial in the food and pharmaceutical sectors where non-compliance can lead to severe consequences.
Documentation Type | Purpose |
---|---|
Batch Records | Track production details |
SOPs (Standard Operating Procedures) | Standardize processes |
Maintenance Logs | Ensure equipment functionality |
Quality Control Records | Monitor product quality |
Enhancing Consistency and Quality
Consistency is king in manufacturing, and documentation is its queen. By maintaining standardized procedures, manufacturers ensure each batch meets the desired quality levels. This is particularly important in gummy production where dosage accuracy and ingredient consistency are paramount.
The Digital Age: Automation and Integration
Today's manufacturing landscape leverages digital solutions. Automated systems with PLC-controlled settings aid in seamless data integration5 with ERP platforms. This not only streamlines documentation but also enhances real-time monitoring and data accuracy.
Meeting FDA Requirements
For industries under the FDA's watchful eye, like dietary supplements, documentation isn't optional—it's mandatory. Systems must support full traceability and secure data management to comply with regulations such as FDA 21 CFR Part 111.
Conclusion: Your Recipe for Success
Just as you wouldn't bake a cake without following a recipe, manufacturing without documentation is a recipe for disaster. It's your safety net, ensuring compliance, quality, and efficiency in every batch.
Documentation is optional for FDA compliance.False
FDA mandates documentation for traceability and quality assurance.
Batch records help track production details.True
Batch records document each production stage, ensuring traceability.
Best Practices for Maintenance and Compliance in Gummy Manufacturing
In the gummy manufacturing industry, maintaining quality and meeting regulatory standards is essential to producing safe, reliable products. Implementing structured practices for equipment maintenance, hygiene, and regulatory compliance helps reduce contamination risks, ensure consistent product quality, and keep your facility audit-ready. Here are the key practices to keep gummy production equipment running smoothly and in full compliance with cGMP standards.
Regular Cleaning and Maintenance
Due to the sticky and residue-prone nature of gummy production, regular cleaning of equipment like depositors, molds, and conveyors is crucial for preventing contamination and maintaining hygiene.
- Scheduled Cleaning: Develop a routine cleaning schedule for each piece of equipment—daily, weekly, or monthly—based on production needs and equipment type. This routine should include detailed cleaning procedures to remove sticky residues and prevent buildup, ensuring equipment remains compliant with food safety standards.
- Preventive Maintenance: Regular inspections and servicing of critical components such as dosing pumps and cooling systems help prevent unexpected breakdowns. Proactive maintenance extends equipment lifespan, minimizes costly downtime, and supports consistent gummy production.
- Documentation: Record each cleaning and maintenance activity, noting the date, technician, and any repairs. This documentation is vital for audit readiness and demonstrates a commitment to maintaining a sanitary, compliant production environment.
Calibrations and Consistency Checks
In gummy manufacturing, maintaining precise dosing and stable environmental conditions is essential for product quality and safety. Regular calibration ensures that each gummy has the correct dosage of active ingredients and is produced under optimal conditions.
- Dosing Calibration: Periodically calibrate dosing systems to ensure accurate measurement of active ingredients, such as CBD, vitamins, or other nutraceuticals. Accurate dosing reduces batch variability and maintains consistent quality across all gummies.
- Environmental Control Calibration: Temperature and humidity control are critical in gummy production to avoid issues like melting, clumping, or microbial growth. Regular calibration of environmental control systems keeps these factors within optimal ranges, supporting product stability and compliance.
Routine Audits and Inspections
To meet regulatory standards and maintain a compliant gummy production facility, regular audits and inspections are necessary to identify and address potential compliance gaps.
- Internal Audits: Conduct scheduled internal audits to verify that all equipment and processes align with cGMP standards. Use an audit checklist focused on hygiene practices, documentation accuracy, and equipment performance. Internal audits help identify areas for improvement before issues escalate.
- Third-Party Inspections: Periodic third-party inspections offer an external perspective on your facility’s compliance status. These unbiased reviews can uncover hidden issues and demonstrate to regulatory bodies that your facility is proactively maintaining high standards in gummy manufacturing.
By following these maintenance and compliance best practices, gummy manufacturers can create a safe, efficient production environment that meets regulatory requirements and consistently delivers high-quality products. A proactive approach to cleaning, calibration, and auditing not only ensures compliance but also strengthens consumer trust and supports long-term success in the gummy industry.
Conclusion
By adhering to cGMP requirements in your gummy manufacturing process, you’re not only ensuring compliance with FDA regulations but also safeguarding product quality, consistency, and consumer safety. Proper hygienic design, precision dosing, environmental control, routine maintenance, and thorough documentation all play vital roles in meeting these standards and positioning your business for long-term success in the competitive gummy industry.
At GummyGenix by SaintyCo, we specialize in providing high-quality, cGMP-compliant gummy manufacturing equipment designed to streamline production and help you maintain the highest standards. If you’re ready to elevate your gummy production capabilities, our team is here to help.
Contact us for a free consultation and discover how GummyGenix can support your compliance needs and optimize your manufacturing process for maximum efficiency.
-
Understand essential regulatory standards for ensuring product safety.: GMPs describe the methods, equipment, facilities, and controls for producing processed food. As the minimum sanitary and processing requirements for producing ... ↩
-
Discover how precision dosing enhances consistency in gummy production.: To achieve consistent dosages, gummy production lines use specialized dosing equipment. These machines are designed to precisely control the ... ↩
-
Discover how SIEMENS TP1200 enhances process control and data management.: Hi guys,I'm doing a PCS7 system using a Comfort Panel TP1200 and Industry Library. The vesions are the follow:- S7-300 CPU programmed with ... ↩
-
Understand why thorough documentation is crucial for compliance.: Good documentation practices helps to track changes, ensures easy reporting of any defects as well as promote continuous improvements to the ... ↩
-
Learn how ERP integration enhances manufacturing efficiency.: ERP implementation in manufacturing helps producers overcome challenges by providing visibility and oversight into operations. ↩