Ever wondered if you could package those delightful gummies with standard confectionery machines? Let's dive in and find out!
Yes, you can use standard confectionery machines for packaging gummies, but be prepared to make some adjustments. Gummies' sticky nature, higher moisture content, and temperature sensitivity need specific tweaks for efficient packaging. While modifying standard ones can be a practical starting point, specialized gummy packaging machines offer tailored solutions.
One of my clients recently shared his experience with packaging finished gummies:
*"When I first ventured into gummy production, I thought I could get by with the same equipment I used for other candies. Boy, was I wrong! Gummies are quite the divas with their stickiness and moisture. It was like trying to dress a toddler in a raincoat on a sunny day—constant adjustments were needed. That's when I realized the importance of tweaking my standard machines to accommodate these quirks.
I began experimenting with non-stick materials and cooling systems, learning the hard way that while you can make do with what you've got, sometimes investing in specialized machinery is worth every penny. It's about weighing your options—literally! Whether you're aiming for precision in counting or just ensuring they don't all clump together like a glob of overcooked pasta, understanding these factors will help you decide if adapting or upgrading is your best bet."*
Standard machines handle gummy's sticky nature well.False
Standard machines often lack anti-sticking features, causing issues.
Gummies require moisture-proof packaging solutions.True
Moisture-proof films prevent clumping and texture degradation.
How Do Sticky Gummies Affect Standard Packaging Machines?
Remember the first time you tried to package sticky gummies? It felt like wrestling a sugary octopus!
Sticky gummies often cling to machine surfaces, leading to jams and inefficiencies. Standard packaging machines typically lack the anti-stick features needed for gummies, causing production interruptions. Solutions include packaging machines with non-stick materials or external systems like oil sprayers to combat stickiness.
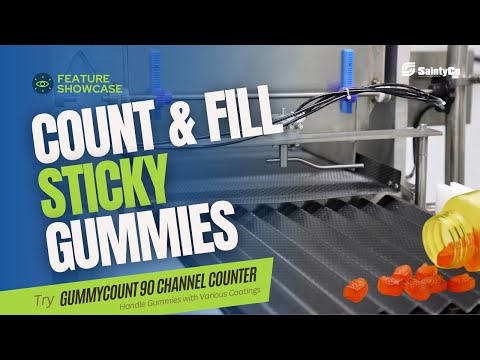
Struggling with Counting Sticky Gummies? Discover How SaintyCo GummyCount 90 Channel Counter Works!
The Sticky Challenge
Gummies and I have a love-hate relationship. On one hand, I adore their chewy texture and fruity flavors, but on the other hand, when it comes to packaging them, they’re like that friend who refuses to leave your side. Their stickiness is thanks to all that sugar and moisture, and it loves to cling to anything it touches—especially machine components1. Once, I watched in horror as a gummy avalanche caused a complete jam in our previous packaging solutions for other solid dose forms - softgel, capsule, and tablet. It was a sticky situation, literally!
Anti-Stick Solutions
To tackle this challenge, I’ve learned that having the right equipment can make all the difference. At SaintyCo, we modified traditional packaging machines so that they come with non-stick coatings or oil-spraying systems designed specifically to handle these clingy candies. It's like giving the machinery a Teflon coating! We manufacturers have gone the extra mile by retrofitting their machines with oil-resistant parts or integrated cleaning systems that keep things running smoothly.
Moisture and Temperature Sensitivity
Gummies are not only sticky but also sensitive to moisture and temperature changes. Had an entire batch clump together because manufacturers didn’t manage the humidity properly—it was a mess! To avoid this, using moisture-proof barrier films and creating controlled environments are key.
Material and Packaging Compatibility
Handling gummies requires packaging machines that can adapt to their unique shapes and sizes without causing jams. We found that using feeders that cater to irregularities really helped. Plus, ensuring compatibility with heat-sealed, moisture-resistant films keeps our gummy treats fresh and delicious.
Precision in Packaging
Accuracy in packaging is everything. Whether it's by weighing or counting, getting it right means quality control and meeting standards. With vision systems, we can detect if gummies are stuck together, affecting count accuracy. Photoelectric sensors are also great for identifying packages where clumping compromises precision, making sure our operations run like a well-oiled machine.
Modifying Standard Machines
Optimizing standard machines is all about tweaking parameters like speed and sealing techniques to handle the unique textures of gummies. Regular maintenance is easier when machines have easy-to-disassemble parts or integrated cleaning modes. Investing in specialized gummy packaging equipment with built-in anti-stick features can really boost efficiency for anyone dealing with these sweet but stubborn products.
Standard packaging machines often lack anti-sticking features.True
Standard confectionery machines aren't typically equipped to handle sticky gummies effectively.
Gummies require less moisture-resistant packaging than chocolates.False
Gummies need more moisture-resistant packaging due to their higher moisture content.
What Are the Material and Packaging Requirements for Gummies?
Have you ever wondered how your favorite gummies stay fresh and chewy?
To keep gummies fresh, use moisture-resistant, heat-sealable films for packaging. These films must fit the gummy's shape, size, and stickiness, utilizing advanced sealing technologies for optimal preservation.
Moisture-Resistant Packaging Materials
I remember my first venture into gummy making—it was an exciting mess! As I experimented with flavors, I quickly learned that moisture was my biggest enemy. Gummies can turn into a sticky clump if not packaged properly. That's why moisture-resistant materials like polyethylene terephthalate (PET) or metalized films are lifesavers. They act as a barrier against moisture, ensuring my gummies stay fresh and delightful. Using heat-sealable films2 ensures everything is snugly sealed away, just like I want to wrap up all those precious memories of my first gummy success!
Shape and Size Considerations
With gummies, it's like dealing with a bunch of tiny, squishy artworks. Each batch I create has its own personality—some are shaped like bears, others are whimsical stars or hearts. I needed packaging that could handle these variations without squishing them. Molds and feeders designed for irregular shapes became my go-to tools. They helped me maintain the unique integrity of each gummy, allowing me to share my creations without worry.
Additionally, some packaging machines include adjustable settings to handle various gummy sizes3, enhancing versatility in production lines.
Stickiness and Anti-Adhesion Solutions
Anyone who's tried making gummies knows that they can be as sticky as a toddler with a popsicle. I found that using non-stick coatings on packaging equipment or incorporating oil-resistant parts was crucial. It reminded me of how my mom always taught me to lightly oil the pasta pot to prevent sticking—same concept! Some advanced machines even spray a light coat of oil over the gummies to keep them from adhering to each other or to the machinery.
Advanced Sealing Technologies
When it comes to sealing, it's like locking in the secret recipe of happiness. I discovered that using techniques like vacuum sealing or nitrogen flushing could extend shelf life by reducing oxygen levels inside the package. It was a bit like those moments when I sealed a letter with a kiss—only this time, it’s with high-tech sealing machines that keep my gummies fresh and appealing4.
Quality Assurance Through Detection Systems
In my journey, ensuring that every gummy gets its moment of glory in the spotlight was important. That's where detection systems like vision cameras or photoelectric sensors came in handy. They work like little guards, making sure each gummy is counted and weighed correctly, just like how I ensure every slice of birthday cake is perfectly fair.
These systems caught any mishaps before final sealing, enhancing both efficiency and product quality control5 in my gummy-making adventure.
Standard machines lack anti-sticking features for gummies.True
Standard confectionery machines often don't have non-stick materials or oil-resistant parts, essential for handling sticky gummies.
Gummy packaging doesn't require moisture-resistant films.False
Gummies need moisture-proof barrier films to prevent clumping and maintain texture during packaging.
Why Does Accuracy in Gummy Packaging Matter So Much?
Have you ever wondered how a seemingly small detail like gummy packaging accuracy can make or break a brand's reputation?
Accuracy in gummy packaging is vital because it ensures consistent product quality, minimizes wastage, and enhances customer satisfaction. Precise weighing and counting align with industry standards, preventing issues that could harm brand reputation.
Ensuring Consistent Product Quality
Imagine the excitement of opening a bag of your favorite gummies, only to find fewer than expected. That's a surefire way to ruin a sweet moment! Accuracy in gummy packaging isn't just about meeting regulatory requirements; it's about delivering joy with every package. It ensures each pack meets quality standards, maintaining customer satisfaction and reducing the risk of complaints or returns due to incorrect quantities. Using a precision weighing system6 helps keep things consistent, ensuring everyone gets their fair share.
![]() |
![]() |
---|
Multihead Combination Weigher efficiently portioning gummy candies with precision for seamless packaging in pouches and containers | Gummy Packaging Machine Brand: SaintyCo
Minimizing Product Wastage
I once heard from a friend who worked in confectionery about the sheer amount of waste they saw daily because of imprecise packaging. It's not just about the gummies; it's about resources and costs, too. Accurate packaging minimizes wastage by ensuring only the required amount of gummies is packaged. This precision prevents overfilling, saving on production costs. Investing in automated counting systems7 ensures each package has the exact number of items, optimizing resource usage and keeping costs in check.
![]() |
![]() |
---|
Optical Detection Gummy Counter precisely counting and sorting gummies with high-speed sensors for accurate bottle filling and pouch packaging | Gummy Packaging Machine Brand: SaintyCo
Enhancing Consumer Trust
In our household, trust is a big deal. We expect what we buy to be what it says on the tin—or package, in this case. Maintaining accurate packaging builds consumer trust by consistently delivering what’s promised on the label. Customers expect to receive the quantity stated, and any discrepancies can damage a brand's reputation. Using vision systems8 allows manufacturers to detect and rectify errors before products reach consumers, maintaining that all-important trust.
Compliance with Industry Standards
The food industry is no stranger to regulations—something I learned the hard way when I once tried to bake for a local fair and got overwhelmed by guidelines! In the food industry, adhering to regulatory standards is non-negotiable. Accurate packaging aligns with these standards, ensuring legal compliance and avoiding potential fines or recalls. Systems like multi-head weighers9 are designed to meet stringent industry requirements, offering precision that fulfills both local and international guidelines.
Technology Solutions for Accuracy
We've come a long way from manual processes—thank goodness for tech! Technological advancements offer solutions that enhance packaging accuracy. From photoelectric sensors to advanced camera technologies, integrating these tools into the packaging process reduces human error and increases throughput efficiency. Exploring options such as sensor-based monitoring10 can significantly improve the overall packaging operation.
Understanding the importance of accuracy in gummy packaging isn't just about efficiency; it's about integrity and loyalty. It's ensuring that every bag of gummies brings the joy it promises—a sweet responsibility for any gummy manufacturer.
Gummies are less sticky than other confectioneries.False
Gummies are known for their sticky nature, which can cause processing issues.
Moisture-proof films prevent gummy clumping.True
Moisture-proof barrier films help maintain texture and prevent clumping.
Is It Worth Investing in Specialized Gummy Packaging Equipment?
Thinking about taking the plunge into specialized gummy packaging? Let me share why it could be a game-changer for your business.
Investing in specialized gummy packaging equipment is a smart move if you want to boost efficiency, cut down on waste, and enhance product quality. These machines are tailored to meet gummies' specific needs, like stickiness and moisture sensitivity, offering potential for higher profits and happier customers.
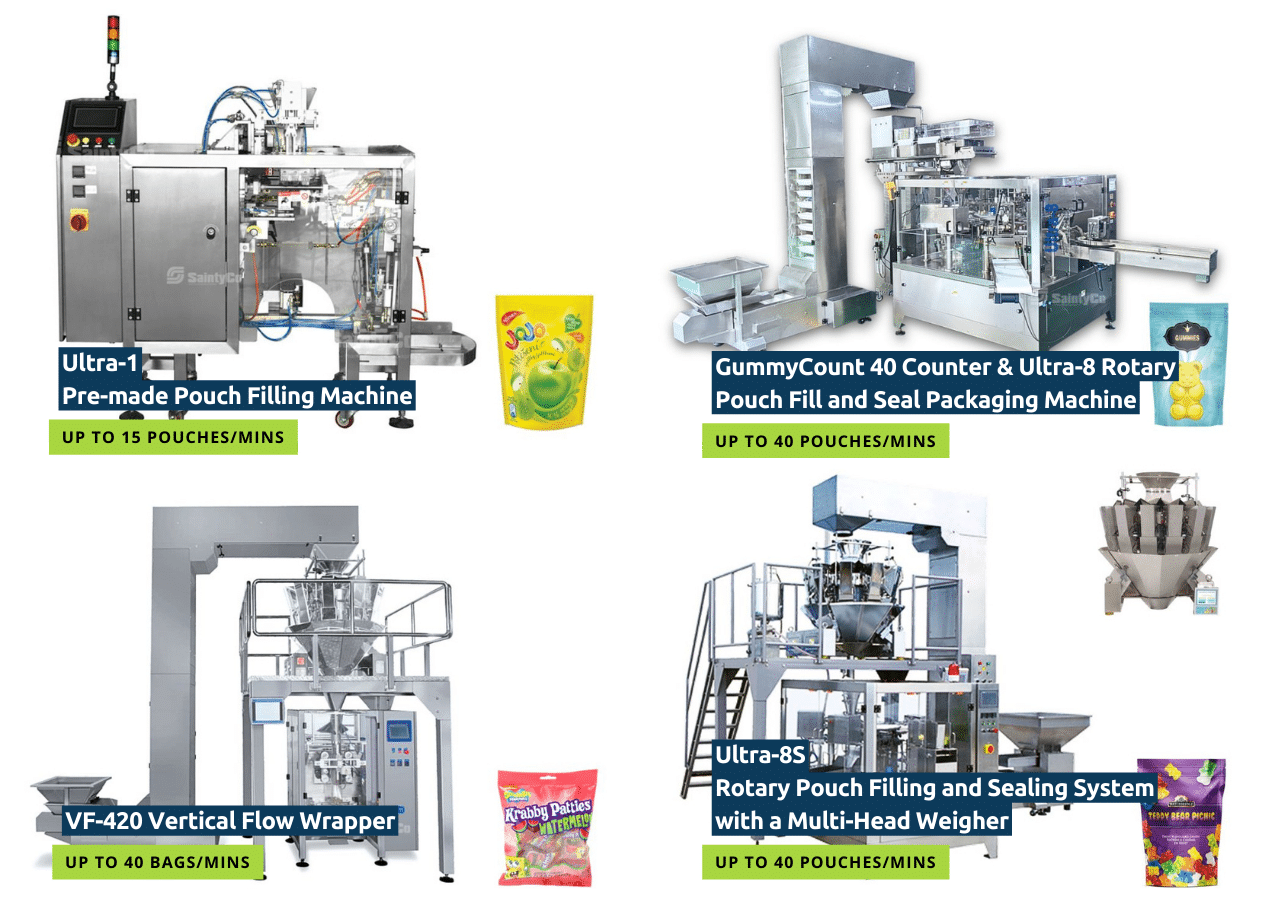
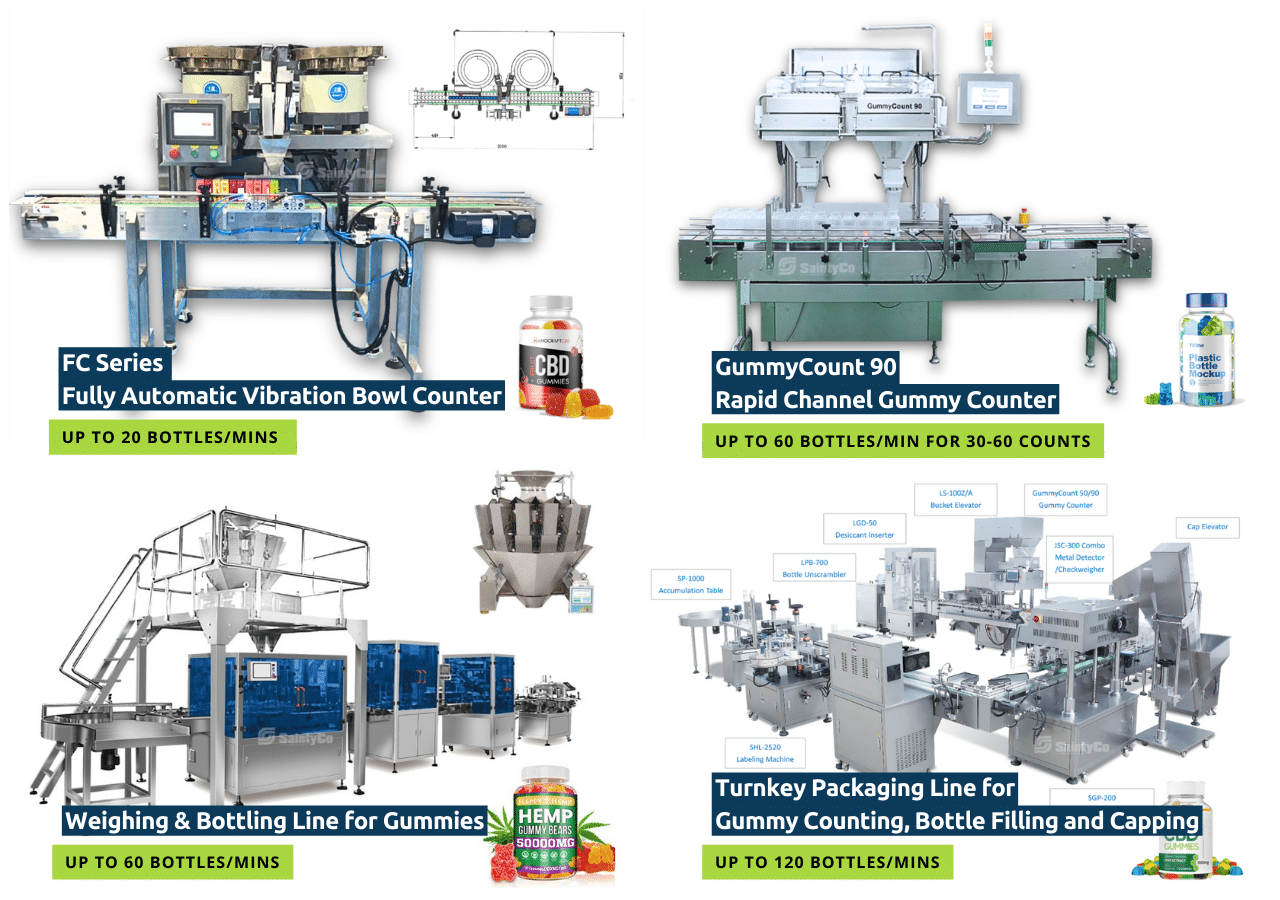
Understanding the Need for Specialized Equipment
Gummy candies present unique challenges due to their sticky nature and varying moisture content. Standard confectionery machines often struggle with these characteristics, leading to frequent interruptions and increased wastage. Specialized equipment is designed with features like non-stick materials and integrated oil-spraying systems to address these issues efficiently.
Efficiency and Cost-Effectiveness
Specialized gummy packaging machines are engineered to handle the intricacies of gummy production. These machines often feature advanced detection systems11 that prevent clumping and ensure accurate weighing or counting, minimizing errors. The initial investment may seem significant, but the long-term savings in reduced wastage and increased production speed can justify the cost.
Enhancing Product Quality and Consistency
Maintaining the quality of gummies during packaging is crucial. Specialized machines help maintain the texture and shape of gummies by managing temperature and humidity levels effectively. By investing in this equipment, you ensure that your products reach consumers in optimal condition, enhancing brand reputation and customer loyalty.
Regulatory Compliance and Hygiene Standards
Food safety is a paramount concern in the confectionery industry. Machines tailored for gummy packaging are built with food-grade materials and comply with stringent hygiene standards12. This compliance not only ensures consumer safety but also safeguards your business from potential legal issues.
Versatility and Flexibility
The adaptability of specialized equipment allows producers to experiment with various gummy shapes and sizes without compromising on efficiency. Features such as mold adaptability and adjustable settings make it easier to diversify product lines, catering to evolving consumer preferences and market trends.
Exploring Market Opportunities
The global gummy market continues to expand, driven by increasing consumer demand for confectionery items with health benefits. Investing in specialized equipment positions your business to capitalize on this trend by enabling the efficient production of high-quality, innovative gummy products.
In summary, while deciding to invest requires careful consideration of your business needs, the benefits of specialized gummy packaging equipment make it a compelling option for anyone serious about thriving in the gummy production world.
Standard machines lack anti-sticking features for gummies.True
Standard confectionery machines often do not have the necessary anti-sticking features required for gummy processing.
Gummies require low-moisture packaging to prevent clumping.True
Gummies have high moisture content, needing moisture-proof packaging to prevent clumping and maintain texture.
Conclusion
Standard confectionery machines can package gummies with adjustments for stickiness and moisture, but specialized equipment offers better efficiency, accuracy, and compliance for optimal gummy production.
At GummyGenix by SaintyCo, we don’t just provide equipment—we empower your gummy business with solutions tailored to your success. Here’s what makes us the ideal partner for your venture:
- Competitive Pricing: Top-tier machinery at affordable rates, ensuring a strong return on investment.
- High-Quality Machinery: GMP-compliant, precision-engineered equipment designed to meet evolving industry standards.
- Equipment Financing & Referral Support: Access flexible payment options and financing resources through our trusted partners, helping you secure affordable payments and potential tax advantages.
- Quick Startup SOPs: Basic recipes and production workflows for a fast, hassle-free start. Additionally, we can connect you with leading formulation consultants and global ingredient suppliers for more advanced product development.
- Custom Molds & Recipes: Stand out in the market with bespoke gummy shapes and innovative recipes tailored to your brand.
- Comprehensive After-Sales Support: From setup and training to troubleshooting, we provide the guidance needed to ensure smooth operations and sustained success.
Contact GummyGenix by SaintyCo, you’ll gain the expertise, resources, and support to build a thriving gummy production business. Let’s succeed together.
Gummy Production Machinery from GummyGenix by SaintyCo | Click to Know More
-
Learn about how gummy stickiness causes machine jams. ↩
-
Learn how heat-sealable films ensure secure and reliable packaging. ↩
-
Understand machine adaptability to diverse gummy shapes and sizes. ↩
-
Discover techniques that prolong freshness in packaged gummies. ↩
-
Explore technologies ensuring accuracy in gummy package counts. ↩
-
Learn how precision weighing enhances product consistency and reduces waste. ↩
-
Discover how automation ensures accuracy and reduces production costs. ↩
-
Explore how vision systems detect and correct packaging errors. ↩
-
Understand how multi-head weighers meet industry standards. ↩
-
See how sensor technology enhances accuracy and efficiency. ↩
-
Learn how detection systems enhance packaging accuracy and efficiency. ↩
-
Explore the importance of using compliant materials in food production. ↩