Have you ever faced a hiccup while trying to produce the perfect gummy? You're not alone! Let’s dive into the common issues with gummy depositors that can turn your sweet dreams into sticky situations.
When using a gummy depositor, common issues include inconsistent filling, clogging, temperature sensitivity, equipment calibration, material compatibility, cleaning challenges, mechanical failures, and operator training. Each of these can affect production efficiency and product quality, but understanding and addressing them is key to smooth operations.
But don't worry! Solutions are at hand. By identifying root causes and implementing effective strategies, we can navigate these challenges together.
Regular cleaning prevents clogging in gummy depositors.True
Frequent cleaning of nozzles and channels reduces ingredient build-up, preventing clogs.
How Can You Ensure Consistent Filling in Gummy Depositors?
Achieving uniform gummy fillings is essential for maintaining quality and efficiency in production.
Consistent filling in gummy depositors requires regular calibration, careful viscosity management, and proper maintenance to prevent nozzle wear and clogging.
Calibration and Maintenance
Regular calibration is fundamental to ensuring that gummy depositors fill molds consistently. Begin by setting a strict schedule for calibrating your equipment. Advanced machines, like those from specific manufacturers, offer automated calibration systems that reduce human error and enhance precision. This regularity helps maintain accurate filling volumes and minimizes volume variation.
Equally crucial is the maintenance of the depositor's components. Pay attention to the nozzles as they are prone to wear, which can lead to uneven filling. Implementing a routine maintenance check can prevent such issues, ensuring that the nozzles are functioning optimally. Consider investing in systems with built-in maintenance alerts that can notify operators when components need attention.
Managing Mixture Viscosity
The viscosity of the gummy mixture plays a pivotal role in achieving consistent filling. If the mixture is too thick or thin, it can lead to variations in fill volume. To maintain the ideal viscosity, continuously monitor and adjust the mixture's temperature and composition.
Using precise temperature control systems can help maintain an optimal consistency. For instance, modern depositors provide detailed temperature settings that allow you to keep the mixture within a specific range, ensuring a smooth flow through the depositor.
Operator Training and Involvement
Well-trained operators are essential for maintaining consistent filling. Training should cover not only basic machine operations but also the intricacies of handling different gummy formulations. Operators who understand how to adjust machine settings according to changes in mixture viscosity or production volume can significantly impact the quality of the final product.
Moreover, empowering operators with knowledge about basic troubleshooting techniques can prevent minor issues from escalating into significant problems. Regular training sessions can keep operators updated on new equipment features and best practices.
Addressing Common Mechanical Issues
Mechanical failures such as misaligned nozzles or worn-out seals can lead to inconsistent fills. Establishing a preventive maintenance routine that includes regular inspections for leaks or unusual noises can help mitigate these issues.
Utilizing advanced diagnostic tools provided by some depositor manufacturers can aid in early detection of potential mechanical failures, allowing for timely interventions and ensuring uninterrupted production cycles.
By focusing on these key areas—calibration, viscosity management, operator training, and mechanical reliability—you can enhance the consistency of your gummy depositor's filling process. Such proactive measures lead to improved efficiency and higher-quality products.
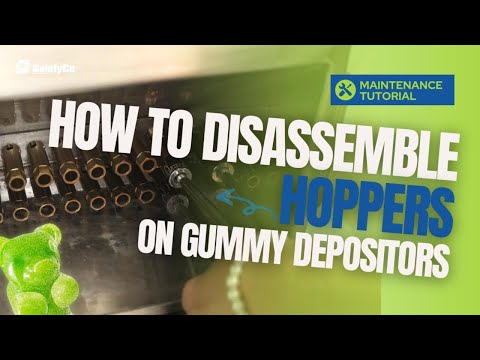
Regular calibration prevents volume variation in gummy depositors.True
Calibration ensures accurate filling volumes, minimizing inconsistencies.
Ignoring nozzle maintenance leads to consistent gummy filling.False
Neglecting nozzles causes uneven filling due to wear and clogging.
What Are Effective Solutions for Clogging Issues?
Clogging in gummy depositors can severely hinder production, leading to costly delays and inconsistent product quality.
To effectively address clogging issues, regular cleaning and maintenance are essential, along with ensuring the correct consistency and temperature of the gummy mixture.
Understanding Clogging Causes
Clogging occurs when gummy ingredients, especially those high in sugar or containing pectin, accumulate in the depositor's dispensing channels. This build-up can obstruct flow and lead to machine downtime. Recognizing the root causes of clogging helps in devising strategies to prevent it.
1. Ingredient Build-Up
- High Sugar Content: Sugars can crystallize over time, forming deposits that clog nozzles.
- Pectin Accumulation: Used as a gelling agent, pectin can thicken and cause blockages if not managed properly.
2. Inconsistent Mixture Consistency
- A mixture that's too thick or too thin affects flow and can lead to clogging. Regular monitoring of viscosity is crucial.
Implementing Effective Solutions
Regular Cleaning Protocols
- Establish a cleaning routine that focuses on critical areas prone to clogging, such as nozzles and channels.
- Consider equipment with self-cleaning features or easy-to-disassemble parts for efficient maintenance. Automated cleaning systems1 can significantly reduce downtime and labor costs.
Optimizing Mixture Consistency
- Ensure a consistent mixture by closely monitoring ingredient ratios and mixing times. Adjust formulations as necessary to maintain optimal flow.
- Use temperature control systems to keep the mixture within the desired viscosity range, preventing thickening or thinning that leads to clogs.
Investing in Advanced Equipment
- Modern gummy depositors come equipped with features designed to minimize clogging. Look for machines with automated calibration and integrated cleaning systems.
- Consult with manufacturers to select equipment compatible with your specific gummy formulations, ensuring seamless operation and fewer interruptions.
Importance of Operator Training
Operators play a critical role in preventing clogging. Comprehensive training ensures they understand machine functions and recognize early signs of potential blockages. Regular training sessions can also cover troubleshooting techniques, enabling swift resolution of minor issues before they escalate.
High sugar content leads to nozzle clogging.True
Sugars crystallize, forming deposits that obstruct flow.
Inconsistent mixture viscosity prevents clogging.False
Inconsistency affects flow, increasing clogging risks.
Why Is Temperature Control Crucial for Gummy Production?
Temperature control is pivotal in gummy production, affecting everything from texture to consistency.
Proper temperature control during the gummy depositing process is crucial for maintaining consistent viscosity and preventing issues like uneven filling or clogging. Regulating the temperature in the gummy depositor hoppers ensures a smooth, continuous flow of the gummy mixture, which helps maintain both quality and production efficiency.
The Science Behind Temperature and Viscosity
In gummy production, temperature plays a critical role in maintaining the right viscosity of the mixture. Viscosity determines how easily the mixture flows into molds and sets. If the mixture is too hot, it becomes too fluid, risking overfilling or spillage. Conversely, a cooler mixture may thicken excessively, leading to incomplete fills or clogging.
Temperature Control in Modern Depositors
Modern gummy depositors, such as those from SaintyCo, incorporate precise temperature control systems. These systems ensure that both the mixture's initial temperature and the depositor's operational temperature are kept within an optimal range.
Maintaining a stable temperature prevents fluctuations that could lead to quality inconsistencies. For example, if the depositor heats the mixture too much during operation, it may thin out unexpectedly. This is why constant monitoring is essential.
Addressing Temperature-Related Issues
-
Monitoring Incoming Mixture: Ensuring the gummy mix starts at the right temperature is the first step. Regular checks and adjustments can preempt many issues.
-
Internal Temperature Management: Modern equipment often includes sensors and alarms that alert operators to any deviations from set parameters.
-
Calibration and Maintenance: Regular calibration and maintenance of temperature controls ensure ongoing precision and reliability.
Benefits of Proper Temperature Regulation
Implementing robust temperature control systems leads to smoother operations by reducing waste and increasing the quality of each batch. Consistency in product texture and taste is vital for brand reputation and customer satisfaction.
In conclusion, while several factors influence gummy production, effective temperature control stands out as a key component in optimizing both efficiency and quality. With advanced technology and a proactive approach, manufacturers can overcome many challenges associated with temperature sensitivity.
For more insights on how temperature affects other aspects of confectionery production, explore this detailed guide2.
Temperature control prevents gummy clogging issues.True
Proper temperature ensures the mixture flows smoothly, avoiding clogs.
Ignoring temperature control enhances gummy texture.False
Neglecting temperature leads to inconsistent texture and quality.
How Important Is Operator Training for Efficient Gummy Production?
Training operators effectively is key to reducing errors and boosting gummy production efficiency.
Operator training is crucial for efficient gummy production as it minimizes errors, enhances equipment handling, and ensures consistent product quality. Properly trained operators can troubleshoot issues quickly, leading to less downtime and more reliable production processes.
The Role of Operator Training in Gummy Production
Operators are the backbone of any manufacturing process, including gummy production. A well-trained operator can identify potential issues before they become significant problems, ensuring that production runs smoothly. They are adept at managing the machinery, understanding the nuances of different gummy formulations, and maintaining optimal production conditions.
Common Errors Due to Lack of Training
Without adequate training, operators might struggle with machine setup or maintenance, leading to common problems such as inconsistent filling3 or clogging. Mismanagement of machine settings or unawareness of calibration needs can result in product defects and increased waste, directly affecting profitability.
Error Type | Impact on Production |
---|---|
Inconsistent Filling | Variations in size/weight of gummies |
Clogging | Production delays |
Miscalibration | Irregular fillings and waste |
Enhancing Operator Skills
Comprehensive training programs should cover both technical aspects of the machinery and practical troubleshooting techniques. Operators should be familiar with all components of the depositor, including how to adjust settings for different gummy formulations and how to perform routine maintenance.
Benefits of Ongoing Training
Investing in continuous training for operators pays off by keeping them updated on the latest technology and methods. This ongoing education reduces the likelihood of errors, keeps the equipment in peak condition, and ensures the production of high-quality gummies consistently.
In summary, while initial operator training sets the foundation for effective gummy production, continuous education and hands-on practice are essential for maintaining and improving efficiency in manufacturing environments. Understanding the importance of this aspect can lead to more reliable and cost-effective production operations.
Operator training reduces gummy production errors.True
Training minimizes errors by improving equipment handling and troubleshooting.
Untrained operators ensure consistent gummy quality.False
Lack of training leads to errors like miscalibration, affecting product quality.
Conclusion
Addressing common issues with gummy depositors—such as inconsistent filling, clogging, and temperature fluctuations—ensures smoother production, higher quality products, and more efficient operations. By focusing on key areas like calibration, maintenance, viscosity management, and operator training, manufacturers can avoid costly mistakes and improve their production flow.
At GummyGenix by SaintyCo, we offer top-of-the-line GummyGenix Depositors designed to eliminate these issues and streamline your production process. With features like automated calibration, smart temperature control, and easy maintenance systems, our machines ensure your gummy production runs without a hitch.
Whether you’re producing traditional gummies or specialized formulations, GummyGenix by SaintyCo is the perfect solution for achieving consistent, high-quality results.
Want to see the GummyGenix Depositor in action?
Contact us now for a personalized consultation or schedule a demo to learn more about how GummyGenix can benefit your business!
-
Discover how these systems enhance cleaning efficiency and reduce machine downtime. ↩
-
Explore how temperature influences other confectionery processes.: As a sugar syrup is cooked, water boils away, the sugar concentration increases, and the temperature rises. The highest temperature that the sugar syrup ... ↩
-
Discover strategies to minimize filling inconsistencies in gummy production.: Always go for a gummy depositor with minimal temperature variations. This is to minimize any damages to the machine or the end product of the ... ↩