In the growing gummy market, especially for CBD, THC, hemp, and essential vitamin-infused gummies, it’s important to maintain quality during production. One problem many manufacturers face is gummies sticking together. This affects how they look, but it also affects how people feel about them and how they use them. In this article, I’ll show you some things you can do and some technology you can use to keep your gummies from sticking together. That way, they’ll look as good in the package as in your ads.
To prevent gummies from sticking together during manufacturing, apply anti-sticking agents like cornstarch or specialized waxes after the gummies have cooled and dried. Ensuring proper storage conditions, such as maintaining a cool and dry environment, also plays a vital role in keeping gummies separate and ready for packaging.
Now let’s look at some things you can do and some equipment you can use to make your gummy manufacturing process better.
Why Do Gummies Stick Together in Manufacturing?
Gummies stick together because of how their ingredients interact with the manufacturing environment. Gelatin and pectin, used to make gummies gel, are hydrophilic. This means they absorb moisture, which makes them sticky. To prevent this, you need to manage the gelation and drying processes.
To understand how gelatin and pectin interact with moisture, you need to know that these polymers absorb water. They also affect the texture and integrity of the gummy during different stages of the manufacturing process. You can use a hygrometer or other moisture analysis equipment to test your gummies' moisture content periodically. You don’t need to use advanced spectroscopy or rheology equipment, which is expensive and impractical for most manufacturers.
.
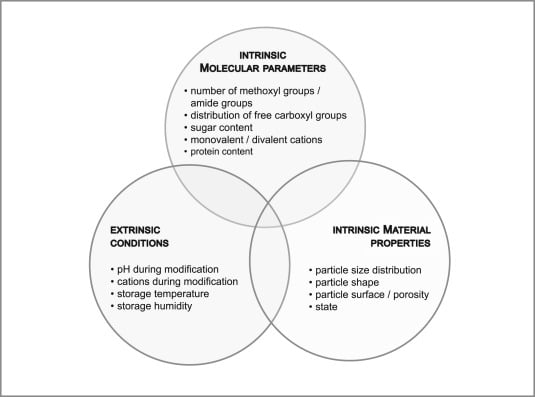
.
Proper cooling is important. You need to cool your gummies in a controlled environment where the temperature and humidity are within certain limits. This prevents the gummies from retaining excess heat or moisture. Ideally, you want to cool your gummies in an area that’s between 18-22°C (64-72°F) and has a relative humidity of less than 50%. This controlled environment helps you get the texture and firmness you want and prevents stickiness. By doing these things, you can reduce the number of gummies that stick together and ensure you’re producing high-quality confections.
Key Points:
- Gelatin and pectin are hydrophilic.
- You need to cool your gummies in a controlled environment after you mold them.
.
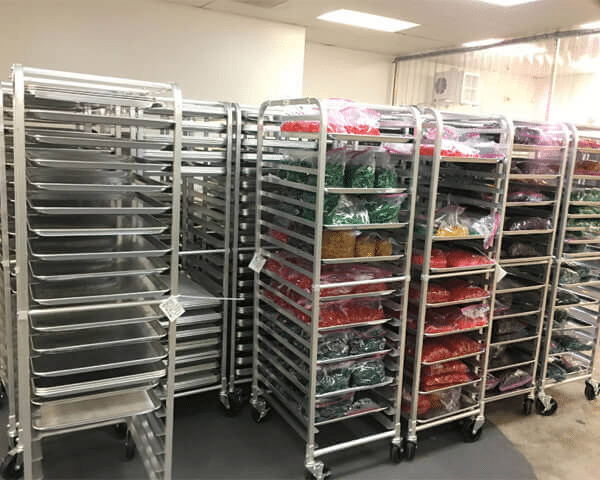
.
What Are the Best Anti-Sticking Agents for Gummies?
To prevent gummies from sticking together, you can use different anti-sticking agents. Each one has its benefits and considerations.
.
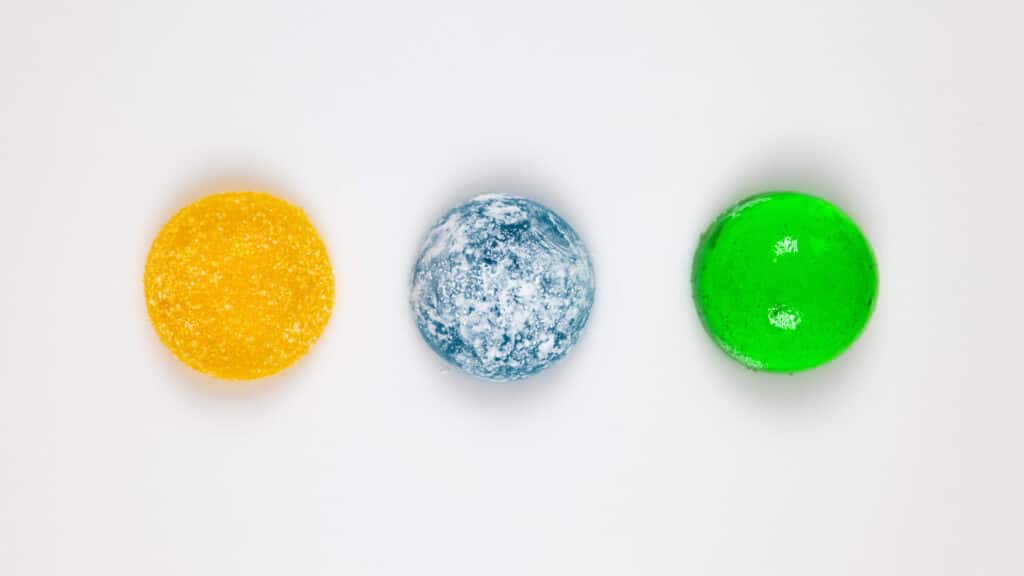
.
Cornstarch is a common anti-sticking agent. It absorbs moisture well, creating a dry layer around each gummy, which keeps them from sticking together. The downside is that cornstarch can leave a matte finish. It can also affect the flavor or clarity of your gummies.
If you want a shinier finish, you can use wax coatings. Beeswax and carnauba wax are two examples. These waxes give your gummies a glossy exterior. The downside is that they can change the texture of your gummies. This may or may not be a problem, depending on the type of gummies you’re making.
Another option is silicone oils. These are non-toxic, tasteless, and odorless. They’re good at preventing sticking without affecting the texture or taste of your gummies. You need to make sure you can use silicone oils in your gummies. They’re not approved for use in all countries.
To apply these anti-sticking agents, you need a precision dispensing system. We have an Auto Oil Spraying System with a Stainless Cover for our gummy production line. This system sprays oil onto the tooling molds to help you release the molded product. It has an oil tank with a level sight glass and spray nozzles. This system is designed to apply the oil evenly and minimize waste. It’s an example of how you can use advanced equipment in your gummy production line to make things better.
.
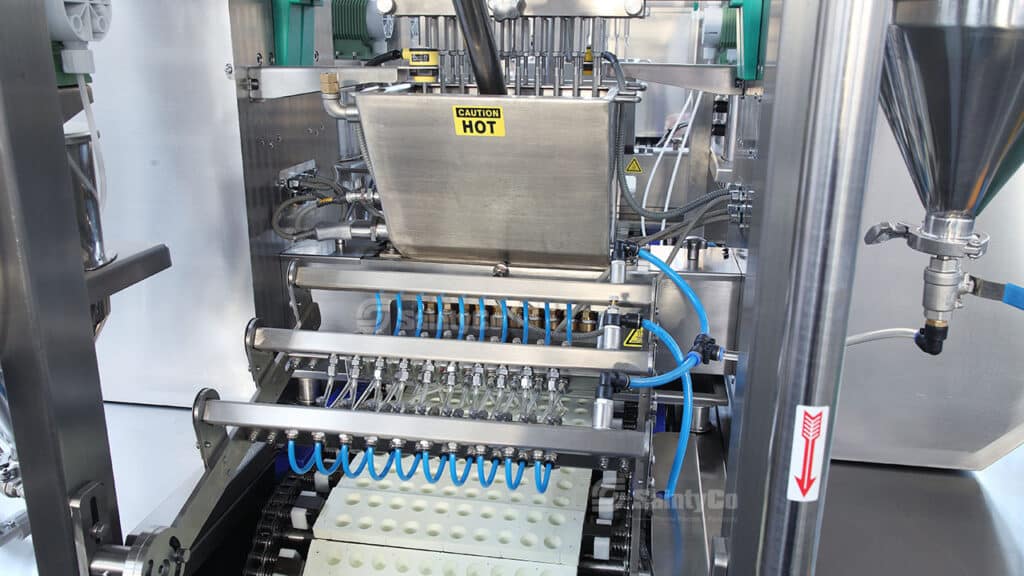
.
By understanding the chemistry and using the right dispensing systems, you can choose the best anti-sticking agent for your gummies. This helps you make better gummies that people want to buy.
Key Points:
- Cornstarch is good for absorbing moisture.
- Wax coatings give you a shiny finish.
- Silicone oils are a modern, efficient solution.
- You need a precision dispensing system to apply these agents evenly.
.
What Equipment Helps Prevent Gummies from Sticking?
In gummy manufacturing, you need the right equipment to help you make gummies that don’t stick together. You need equipment to mix your ingredients, mold your gummies, set them, and coat them. Each of these steps requires specialized equipment to handle the viscous mixtures you work with when you make gummy candy.
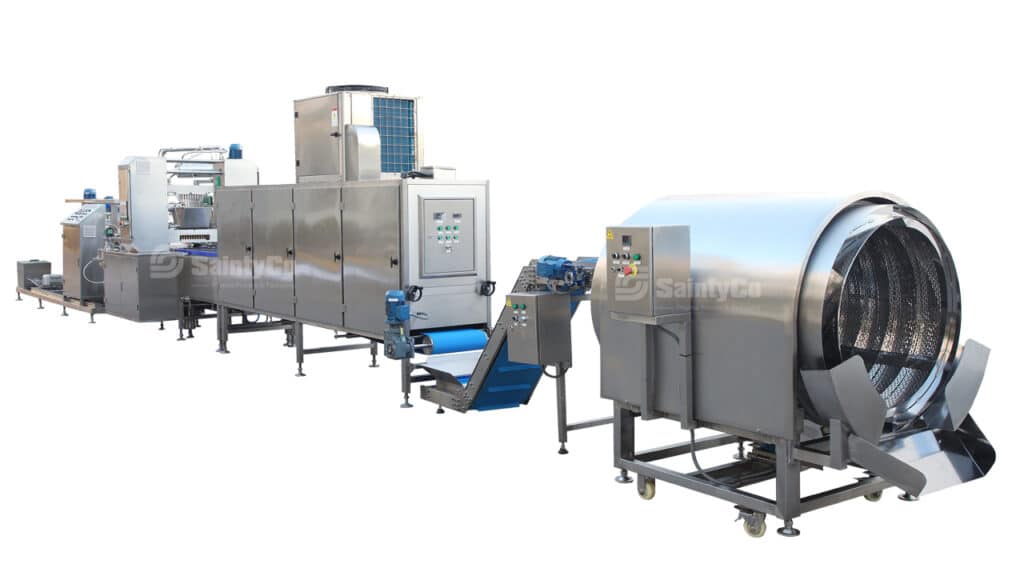
Automated Gummy Production Line – Cooling and Conveyor Systems: The SaintyCo G-series Gummy Production Line is a great example of how we use advanced technology to keep gummies from sticking. We have automated cooling tunnels with advanced chilling systems and desiccant fans that keep the temperature between 0-20℃ so the gummies are set properly and don’t stick. In addition, we have a state-of-the-art conveyor system that includes a polyurethane cooling belt specifically designed for food-grade applications. This system allows the gummies to flow through each production stage, moving smoothly and hygienically, reducing the risk of sticking and deformation.
.
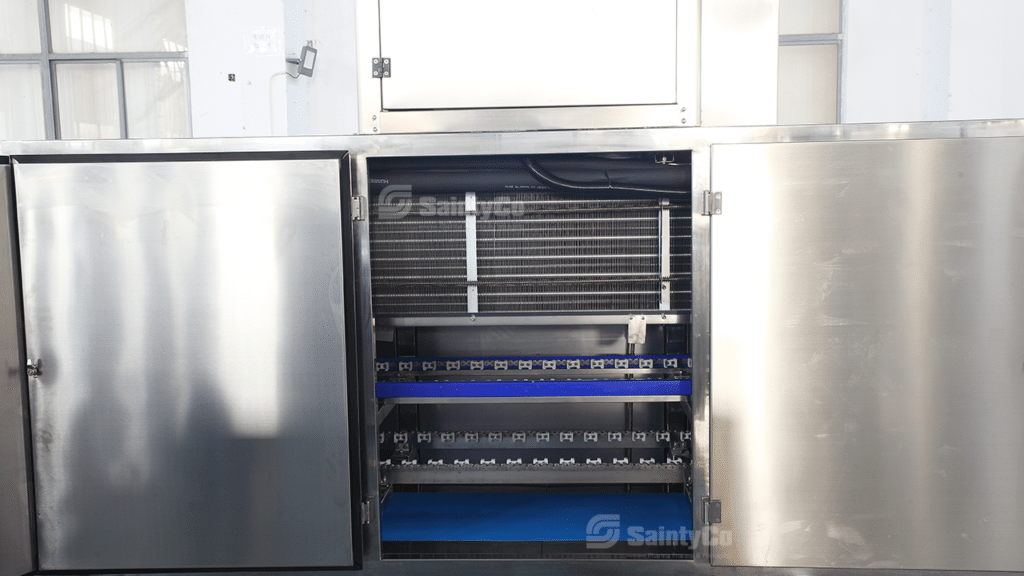
.
Oil Coating System: An Oil Coating Drum is a great solution for applying non-stick coatings. This drum consistently sprays oil on the gummies, making them shiny and providing a protective barrier from the environment. You can adjust the amount of oil and the dwell time to meet your product needs for a consistent and efficient coating application.
.
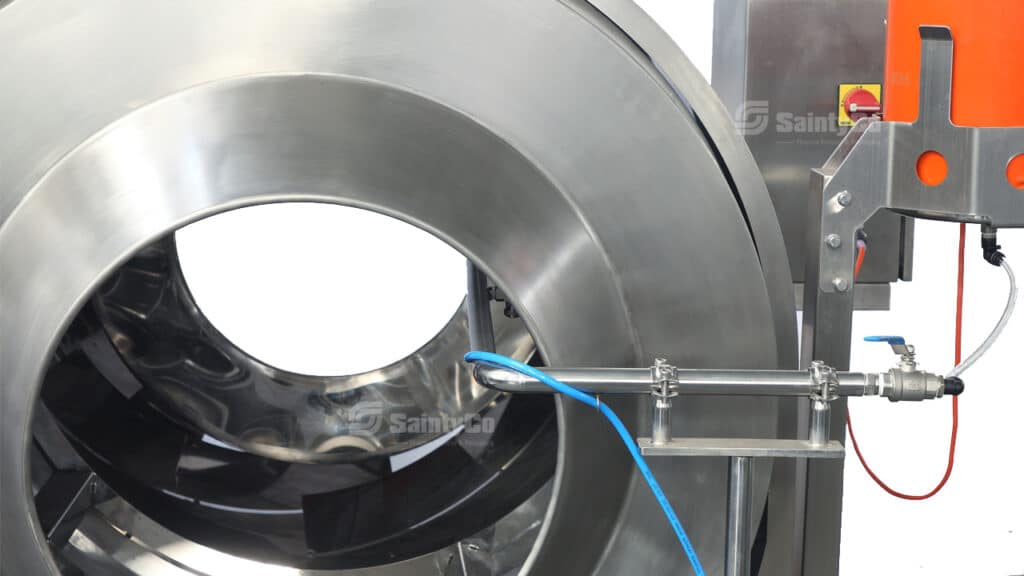
.
Sugar Sanding and Polishing Equipment: If you want a sugared finish, consider our Sugar Sanding Drum, which automates the sugar coating process and has a capacity of up to 600 kg/hr. It works perfectly with modern gummy production lines, so you get a consistent and durable sugared coating. Choose a sugar polishing pan that has adjustable angles and can be fitted with hot or cold air blowers so you can optimize the sugar coating for different types of confections.
.
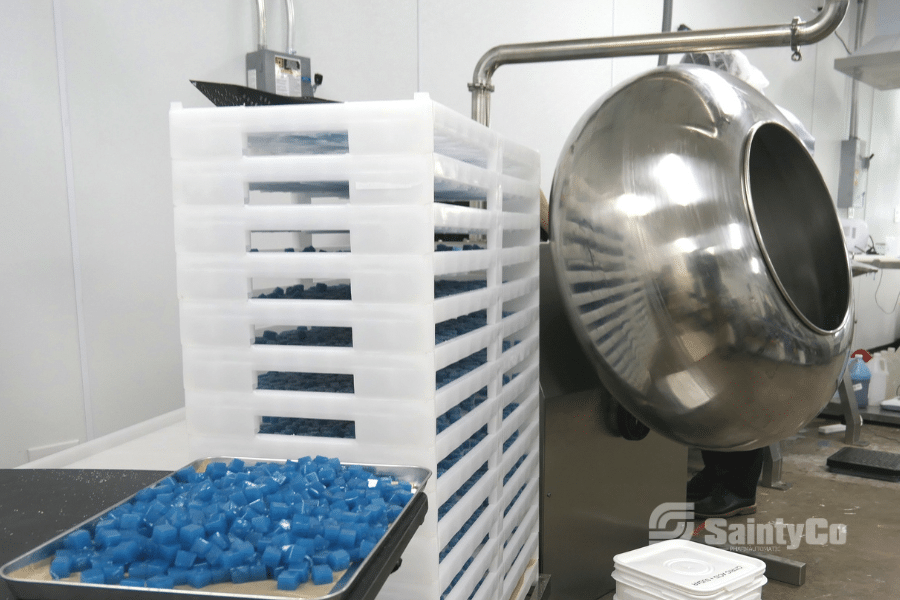
.
These machines not only improve the quality of the final product but also improve the efficiency of the production line. By having systems that manage every production phase, from molding to packaging, you can significantly reduce the number of times gummies stick during production.
These advanced machines are an investment that will pay for themselves by streamlining your operations, reducing waste, and improving the consistency of your product from batch to batch. You need to consider these technologies to stay competitive and maintain high standards in gummy production.
Key Points:
- Advanced Cooling Systems: Maintain precise temperature and humidity control to ensure proper gummies are set.
- Oil Coating Drums: Apply a consistent layer of oil to gummies to enhance appearance and prevent sticking.
- Sugar Sanding Drums: Provide uniform sugar coating to improve texture and prevent gummy candies from clumping.
- Conveyor Belts with Cooling Belts: Transport gummies smoothly through production stages while minimizing handling issues.
- Automated Coating and Polishing Equipment: This equipment ensures even distribution of coatings, such as sugar or oil, for consistent product quality.
.
How Should Gummies Be Packaged to Avoid Sticking?
Proper packaging is critical to ensure that gummies stay non-sticky and maintain quality during storage and transport. Here are some technical details about how to package gummies properly:
Use Advanced Packaging Materials: Use air-tight, moisture-resistant materials like Mylar bags to protect gummies from moisture and air, which can cause them to stick together. Mylar bags can be vacuum-sealed to help preserve the texture and integrity of the gummies.
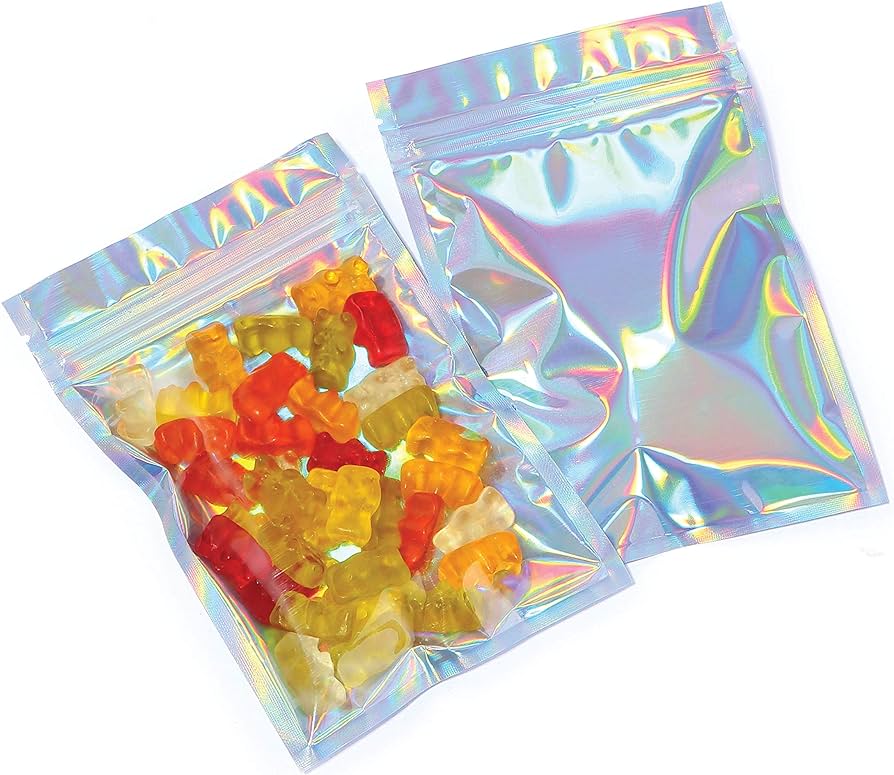
Include Moisture Absorbers: Put silica gel packets in the packaging to absorb any residual moisture that could cause sticking. This is especially important in high-humidity climates or during sea freight, when atmospheric conditions can change significantly.
Nitrogen Flushing: Flush the packaging with nitrogen to remove oxygen, which reduces oxidation and moisture that can cause sticking. This process extends the shelf life of the gummies and helps maintain the color and flavor consistency.
Automated Packaging Solutions: Use automated packaging systems like the Ultra-8 Rotary Automatic Fill and Seal Machine to package your gummies precisely and hygienically. This machine can handle different pouch formats, so you can package your gummies securely without exposing them to the elements that could cause them to degrade or stick.
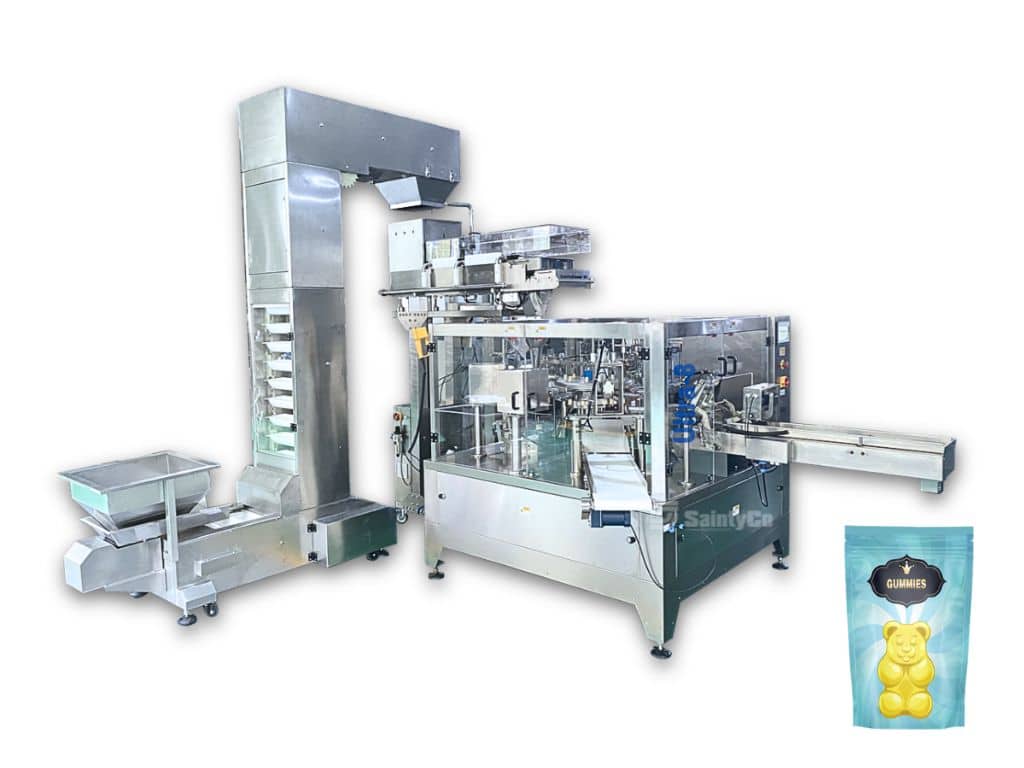
Gummy Counting and Filling Systems: The SaintyCo GummyCount-90 is a specialized machine for counting and packaging gummies without sticking issues. It has Teflon-coated dimpled channels that prevent the gummies from sticking during the counting process.
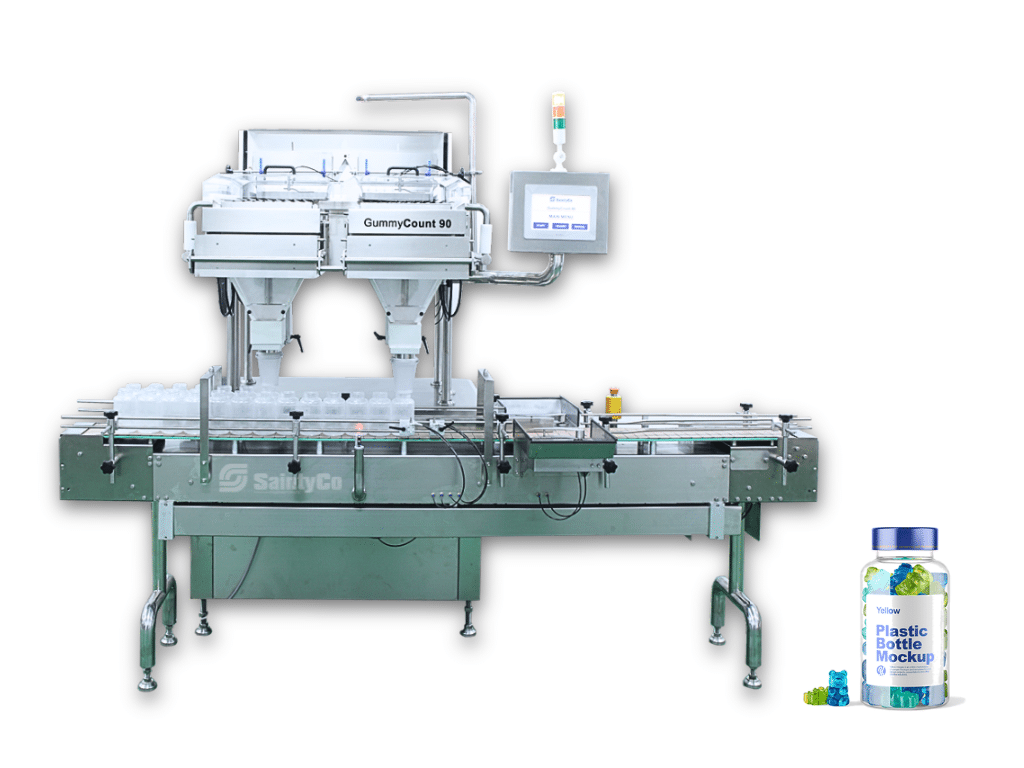
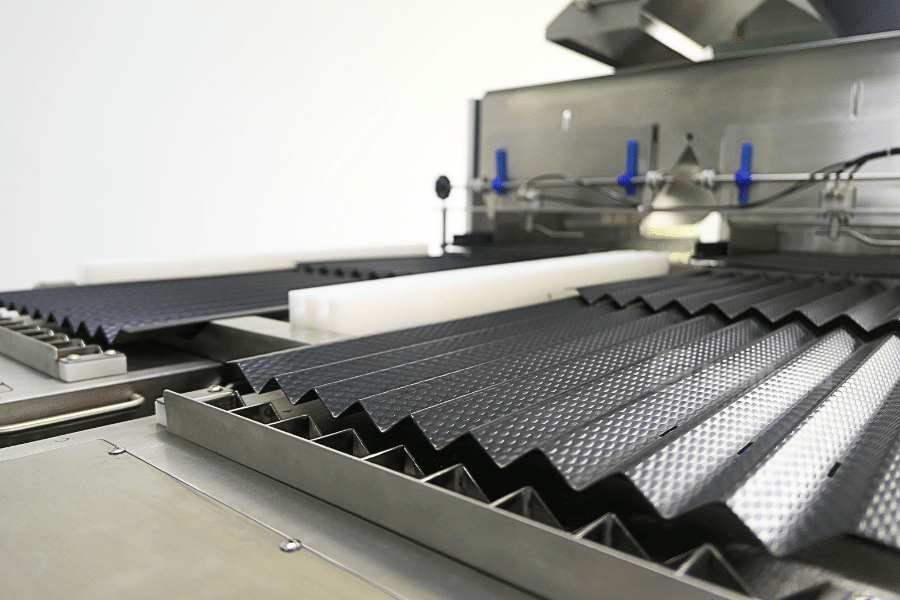
.
By using these advanced packaging methods, you can improve your gummy products' quality and shelf life. These techniques not only prevent sticking but also make your gummies look good and keep them fresh from production to consumption.
Key Points:
- Use vacuum-sealable Mylar bags to protect gummies from moisture and air.
- Include silica gel packets in the packaging to absorb moisture and prevent sticking.
- Flush the packaging with nitrogen to reduce oxygen exposure, minimizing oxidation and moisture that can cause sticking.
- Automated sealing systems are used to ensure airtight packaging, which improves product consistency and quality.
- Use advanced counting machines to package gummies precisely and hygienically, reducing manual handling and potential sticking.
.
What Conditions Should Be Maintained in Gummy Manufacturing Facilities?
You need to control the temperature and humidity in your manufacturing environment. You don’t want it to be too humid or hot because that will make your gummies sticky. You need to check and balance this regularly because if you don’t, your gummies will get sticky over time. You can use high-tech environmental monitoring systems that give you real-time data and allow you to adjust your settings quickly and efficiently. You can also invest in high-quality HVAC systems and dehumidifiers to help stabilize your production environment.
Key Points:
- HVAC systems to control air quality
- Stable temperature and low humidity
- Regular monitoring of the environment
.
Conclusion
By doing these things, you can make sure your gummies don’t get sticky and look good. This will make your customers happy, help you build your brand, and make you more competitive in the marketplace. You also need to use automation and good equipment for manufacturing and packaging to maintain high standards in your gummy production.
To make great gummies, you need to understand how the ingredients, the environment, and the mechanical processes all work together. This is what you need to know to be a great confectionery consultant and help people make great gummies that meet consumer expectations and regulatory standards.
.
GETTING STARTED WITH GUMMY MANUFACTURING
When you’re ready to start making gummies at your facility, GummyGenix by SaintyCo can help you with the best machinery and equipment in the industry.
Contact our team anytime to discuss your gummy production goals with one of our expert team members.